When REACH (Registration, Evaluation and Authorisation of Chemical substances) regulation EC 1907/2006, first came into force in June 2007, it is fair to say that largely went unnoticed by the conveyor belt industry. After all, the possibly hazardous chemicals used to make thick, heavy rubber industrial conveyor belts could surely not pose a risk compared, say, to rubber products handled and used by the general public. Thanks largely to the benefit of 15-years of hindsight, most of us are now far more aware of the seriousness of such issues and the much greater duty of care we owe not only to our families and our work colleagues but also to those who work with handle conveyor belts for a living.
Since its inception, the various component parts of REACH regulations have continued to develop in line with ongoing scientific research. Here, one of the industry’s leading conveyor belt application engineer’s, Rob van Oijen, brings us up to date with the regulations and issues a stark warning to those who continue to turn a blind eye to the very genuine safety aspects involved.
Why worry?
The reason why the hazardous chemicals that conveyor belts contain are such a cause for concern is twofold. Firstly, there are the proven harmful effects that ‘substances of very high concern’ (SVHC’s) can have on humans and the environment. Secondly, and equally important, there is an ever-growing list of substances still under research that are suspected by scientists to have potential harmful effects.
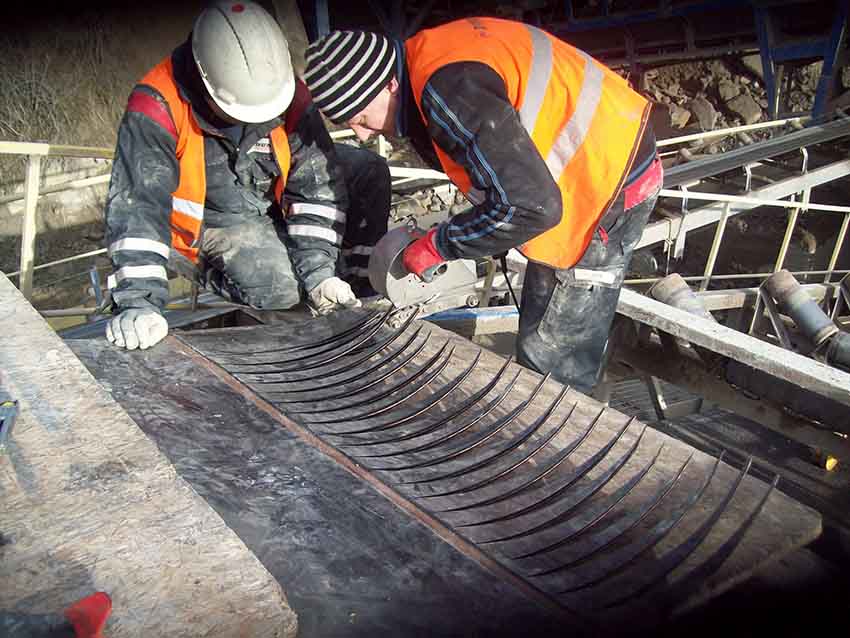
Those physically working with conveyor belts need to be safeguarded
Sadly, history is littered with examples of substances (asbestos example) that were thought to be safe at the time but ultimately proved to have seriously damaging effects. As far as conveyor belts are concerned, those who regularly work with them as part of their job role, such as conveyor maintenance staff and belt splicers for example, are potentially at greatest risk and therefore most in need of safeguards.
The use of chemicals in conveyor belt manufacturing
The vast majority of the rubber used to make modern-day conveyor belts is actually synthetic or, at most, contains only a relatively small element of natural rubber. In basic scientific terms, the creation of rubber compounds (rubber compounding) is the process where a range of ‘specific task’ chemicals, reinforcements and anti-degradants are mixed together with rubber polymers. The most common polymers used in conveyor belts are Styrene- Butadiene rubber (SBR) and Nitrile rubber (NBR). The chemical agents form chains of polymers to form rubber compounds that will ultimately be vulcanised to create the finished product.
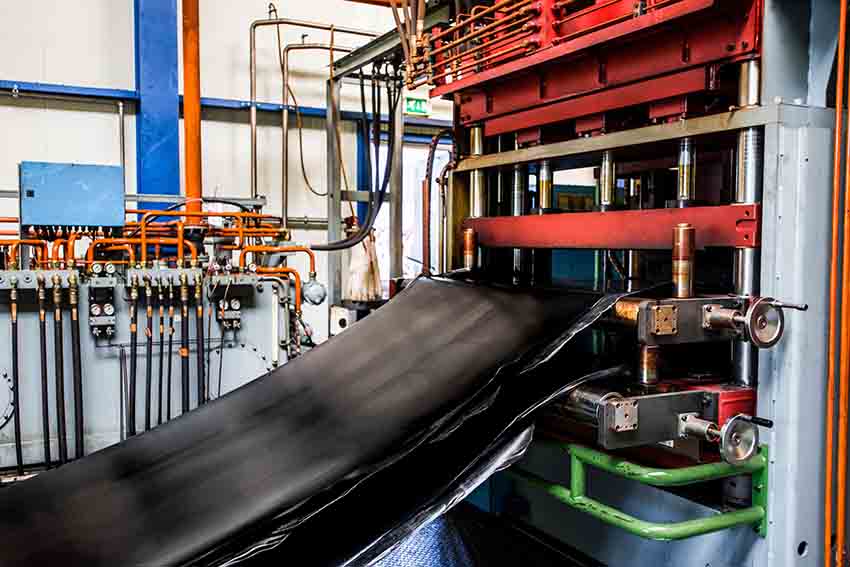
Dozens of different chemical components are used to create rubber compounds
There are literally dozens of different components that are used to create the various rubber compounds, such as anti-degradants, anti-ozonants and also as accelerators (essential for the vulcanisation process for example). These components include primary amine–based sulfenamides, such as N-cyclohexyl-2-benzothiazole sulfenamide, and thiazoles, such as 2-mercaptobenzothiazole. It is an inescapable fact that to make some rubber compounds it is necessary to use chemicals that are extremely dangerous in their own right.
What are the biggest concerns?
One of the biggest concerns involves short-chain chlorinated paraffin’s (SCCP’s). These are commonly used, especially in Asia, to artificially speed up the vulcanizing process. European regulations (which I will explain later) clearly stipulate that SCCP’s should either not be used at all or at least only used on a very restricted basis. This is because SCCPs are identified as persistent organic pollutants because they are bioaccumulative* in human and wildlife and toxic to aquatic organisms at low concentration. These chemicals pose hazards to human health and the environment because they have category 2 carcinogenic classifications and are what is scientifically termed as ‘persistent’. The clue to their presence is the strong, pungent aroma whereas good quality rubber usually has very little smell at all.
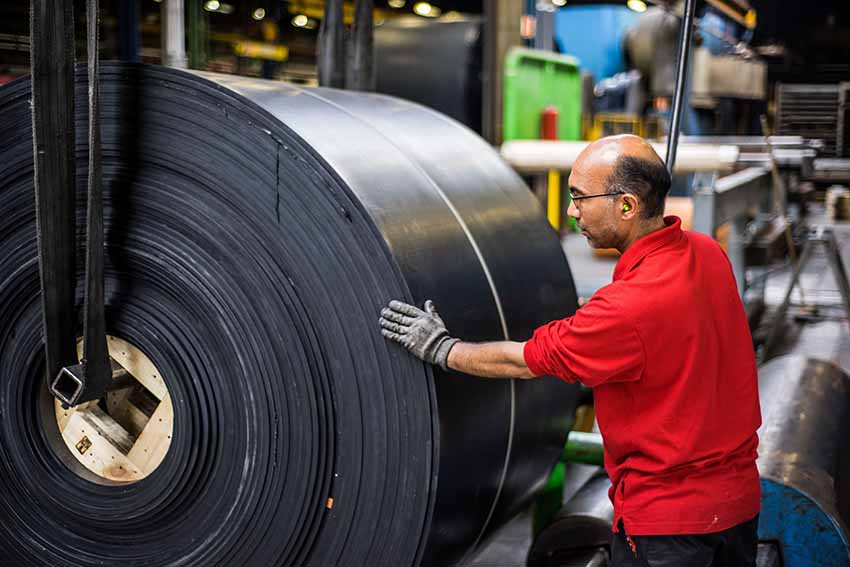
Good quality rubber usually has very little smell at all
The formation of nitrosamine gasses is also a concern and known to occur when certain types of vulcanisation accelerators are used. Nitrosamine gasses gradually release themselves from rubber belts, which could be a problem when the belts are stored indoors. Nitrosamines are chemical compounds classified as probable human carcinogens based on animal studies. Investigative research is still ongoing but publicly available information from the rubber industry (primarily from within Germany and The Netherlands) indicates that nitrosamine formation can be avoided if the accelerators are replaced by others that do not contain nitrosatable substances. Fortunately, at least as far as Europe is concerned, very strong regulations are in place to protect humans and the environment in the form of REACH.
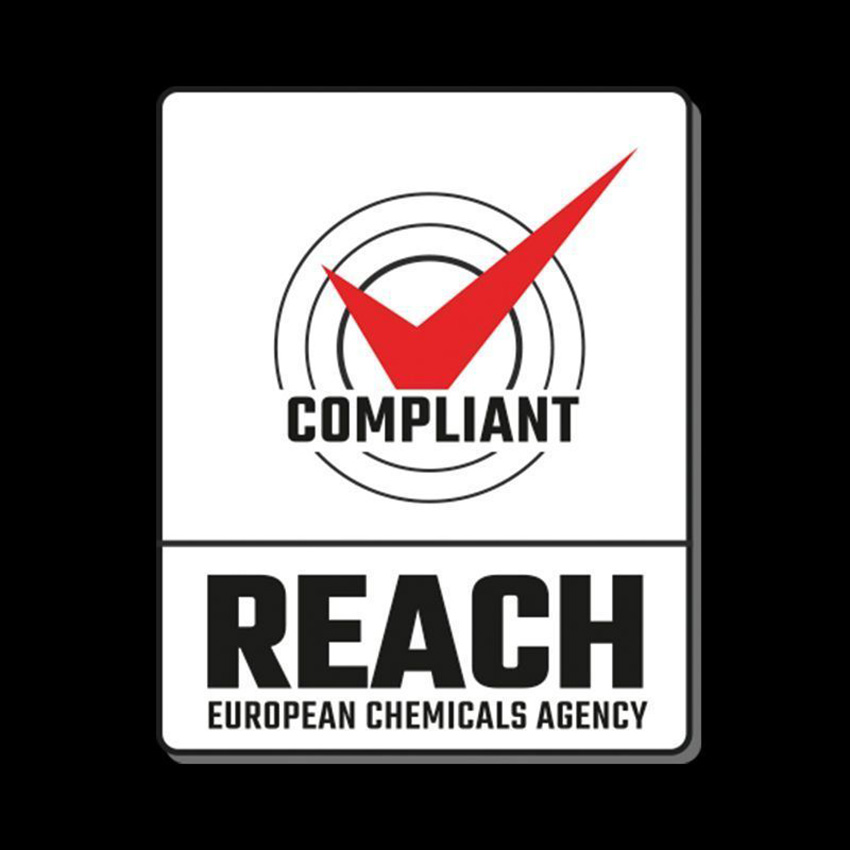
What is REACH?
REACH was established by members of the EU with the specific aim to improve the protection of human health and the environment through the better and earlier identification of the intrinsic properties of chemical substances. This is achieved by the four processes of REACH regulation, which is the registration, evaluation, authorisation and restriction of chemicals. This places direct responsibility on industry to manage the risks from chemicals and to provide safety information on the substances. REACH imposes strict limits on the amounts of certain chemicals that used in each product. The regulation also calls for the progressive substitution of the most dangerous chemicals (referred to as “substances of very high concern”) when suitable alternatives have been identified and, in some extreme cases, bans them altogether.
Manufacturers and importers are required to gather information on the properties of their chemical substances, which will allow their safe handling, and to register the information in a central database in the European Chemicals Agency (ECHA) based in Helsinki. The Agency is the central point in the REACH system. It manages the databases necessary to operate the system, co-ordinates the in-depth evaluation of suspicious chemicals and is building up a public database in which consumers and professionals can find hazard information.
Accountability and responsibility
Although we (Dunlop Conveyor Belting) were one of the first to comply with REACH, most European conveyor belt manufacturers have chosen to ignore this legal requirement, either completely or at least partially because of the impact on production costs. As the volume of cheap, unbranded belting being imported into Europe continues to increase dramatically, the situation is made much worse because manufacturers located outside of EU member states and the UK are not subject to the regulations**. Neither are they subject to EU regulation concerning Persistent Organic Pollutants (POPs). This provides them with an open goal because they are free to use unregulated raw materials that cost appreciably less on the global market compared to their regulated counterparts, even though they may be entirely prohibited or at least have strict usage limitations within the European community.
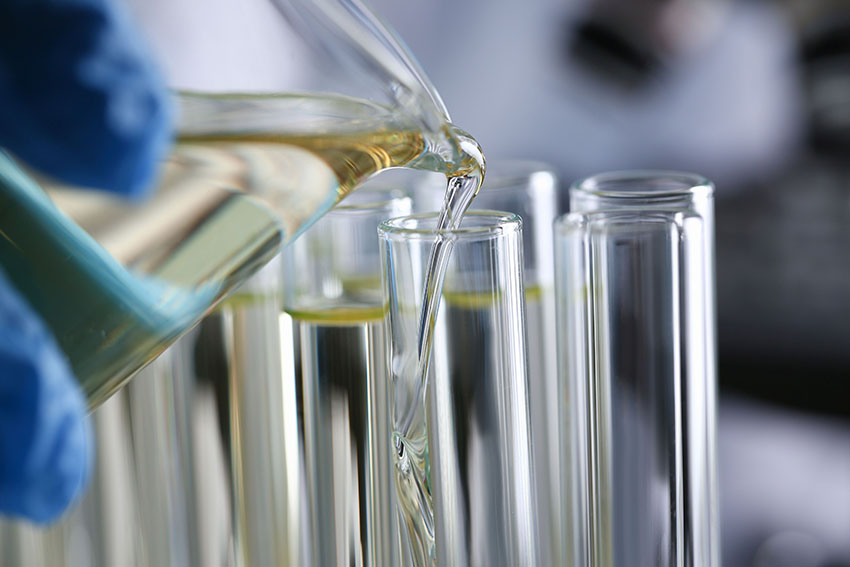
Non-EU and UK based manufacturers are not, subject to REACH regulation or EU regulations concerning Persistent Organic Pollutants
REACH and the UK following Brexit.
REACH, and other chemicals regulations, were retained in UK domestic legislation at the end of the Brexit transition period via the European Union (Withdrawal) Act 2018. Secondary legislation was also passed that amended REACH to make it work in a UK-only context from that point onwards. The UK Government put in place a separate UK REACH regime that applies to businesses that import, make, sell or distribute chemicals in Great Britain, whether as raw materials or in their finished state. The UK REACH regime is designed to replicate the EU system as closely as possible, maintaining the fundamental aims and purposes of REACH including high standards of health and environmental protection.
Progressively tougher
Particularly since 2018, REACH regulation regarding SVHC (substances of very high concern) has become increasingly stringent and demanding. Previous REACH compliance was largely based on declaring (registering) the use of listed chemical substances and staying within specific limits applicable to each substance. Now, Article 31 of REACH (requirements for safety datasheets) demands that if a product contains SVHC that is more than 0.1% of the total weight of the finished product then the manufacturer is compelled to both register its use with the European Chemicals Agency and provide their customer with a safety datasheet.
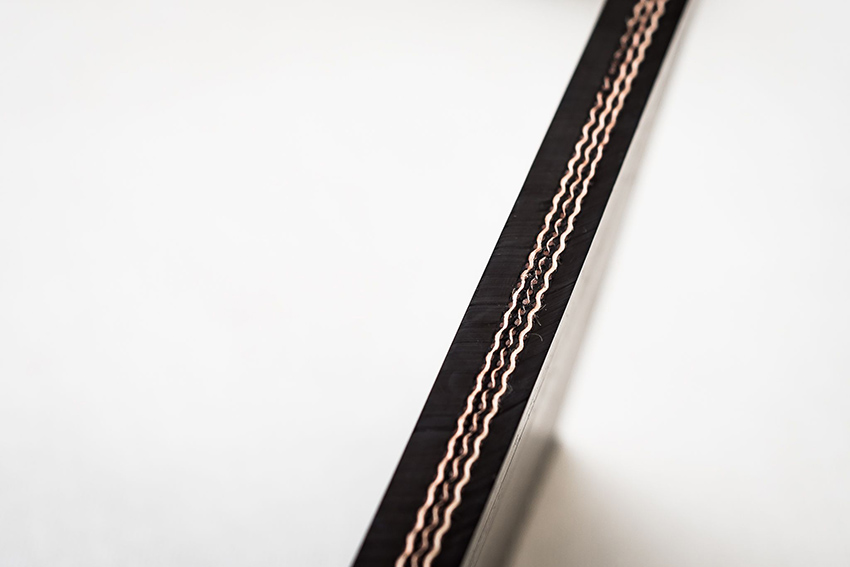
The combined weight of SVHC should not exceed 0.1% of the actual product weight
Calculating the total proportion of weight relating to SVHC for an individual product is a painstaking task. However, there is no doubt that it is entirely necessary. At Dunlop, we review and calculate the weight of SVHC in all of the materials that we use in each individual product. This includes materials that we buy from outside sources such as resin for example. The combined weight of SVHC is calculated as a proportion of the gross weight of the product. Not only do the proportions differ depending on the composition of each product type, they also differ depending on the thickness of the rubber covers. The proportion in terms of weight is naturally higher in thinner, lighter products.
Out of control
Apart from ourselves, only a limited number of genuine conveyor belt companies who actually manufacture belts themselves still exist in Europe and again, apart from ourselves, virtually all European manufacturers import belting from outside of Europe in order to supplement their own production. Many manufacturers also outsource the manufacturing of their rubber to large-scale rubber compound manufacturers rather than produce it in-house. Again, this mostly outside of Europe. Although it is cheaper, the downside is that it is impossible to ensure compliance with European safety and environmental regulations and equally impossible to ensure the consistency of the rubber’s physical properties.
Working safe
Although Brussels is often accused of over-zealous regulation, the use of potentially harmful chemicals and materials should never be compared with regulations concerning the straightness of bananas or the size of eggs. Although it certainly is not my intention to scaremonger, it is nevertheless important that users of rubber conveyor belts make themselves aware of potential hazards. Always ask for written confirmation from the belt manufacturer or supplier that the product you are buying has been produced in compliance with REACH EC 1907/2006 regulations.
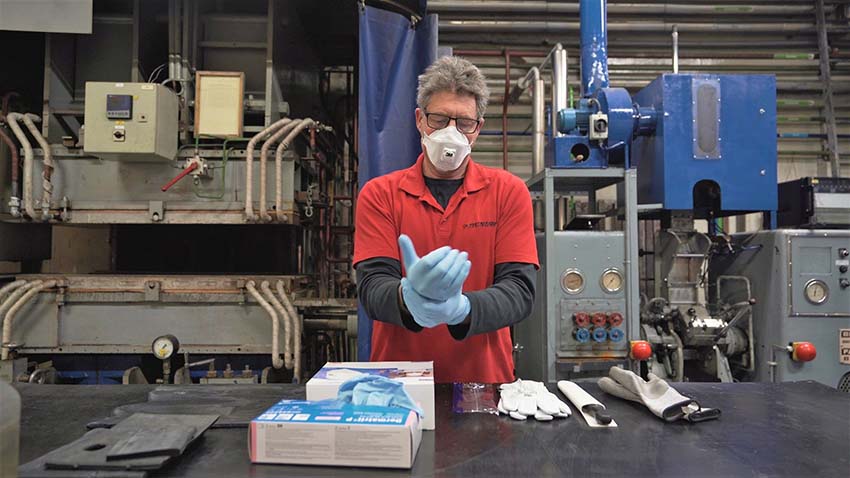
Wear a mask to avoid inhaling rubber dust
At the same time, basic safety precautions for those working with conveyor belts should be applied. Firstly, wear gloves (if practical) when handling belts. Secondly, it is advisable to wash your hands before drinking, eating or smoking. Lastly, those involved in actions that may cause rubber dust to be produced, such as grinding for example, should wear a mask to prevent inhalation of dust particles.
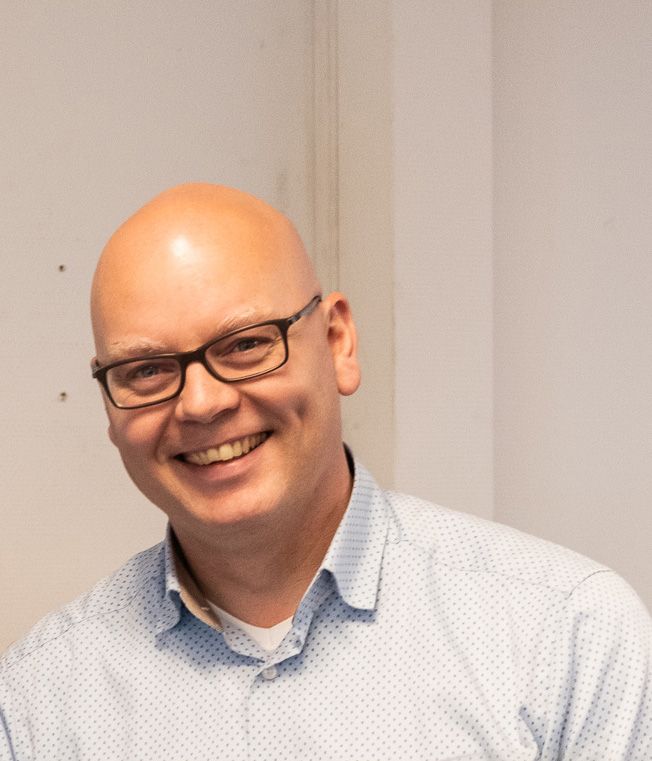
About the author – Rob van Oijen
Rob van Oijen is Manager Application Engineering for Dunlop Conveyor Belting in The Netherlands. Rob has specialised in conveyors for some 14 years, supporting businesses throughout Europe, Africa, the Middle East and South America.