UBOT 3D is a Polish 3D printer manufacturer, building 3D printers since 2015. The company specializes in the development of new and advanced printing technologies for the industrial market and aims to deliver the best, most comprehensive technology for Polish businesses to more effectively utilize traditional manufacturing methods, increase productivity and reduce manufacturing costs.
UBOT 3D also prioritizes R&D efforts, focused on the development and manufacturing of new products, as well as testing their safety and effectiveness.
Interview with Filip Ludwikowski, Chief Technology Officer at UBOT 3D.
Easy Engineering: What are the main areas of activity of the company?
Filip Ludwikowski: Our products are used in prototyping, short manufacturing runs, support and maintenance services for the automotive, aerospace, medical industries, as well as many others, including construction, electronics and metallurgy. Our production line dedicated for industrial clients is outfitted with P440 and P800 machines, with particular specifications depending on the needs of each customer.
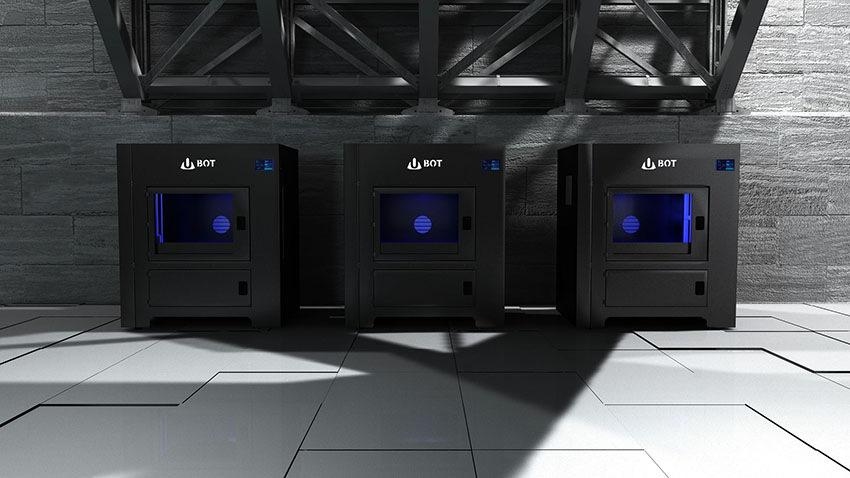
E.E: What’s the news about new products?
F.L: We are currently working on a new printer model, combining speed and precision with large-scale printing capabilities. Thanks to our revolutionary FPD (Fast Plastic Deposit) technology, it will be able to achieve up to 10 times faster printing speeds, far exceeding the capabilities of existing solutions. Thanks to these advances, our clients will be able to print large objects in a relatively short time, greatly optimizing their production lines.
E.E: What are the ranges of products?
F.L: Our flagship printers are the S320 desktop model and the two industrial models: the P440 and the P800. Beyond that, we are capable of building printers of other sizes – according to client specifications. This is what sets us apart from the competition – we create our printers from the ground up: we develop the technology and build machines that serve our clients for many years into the future.
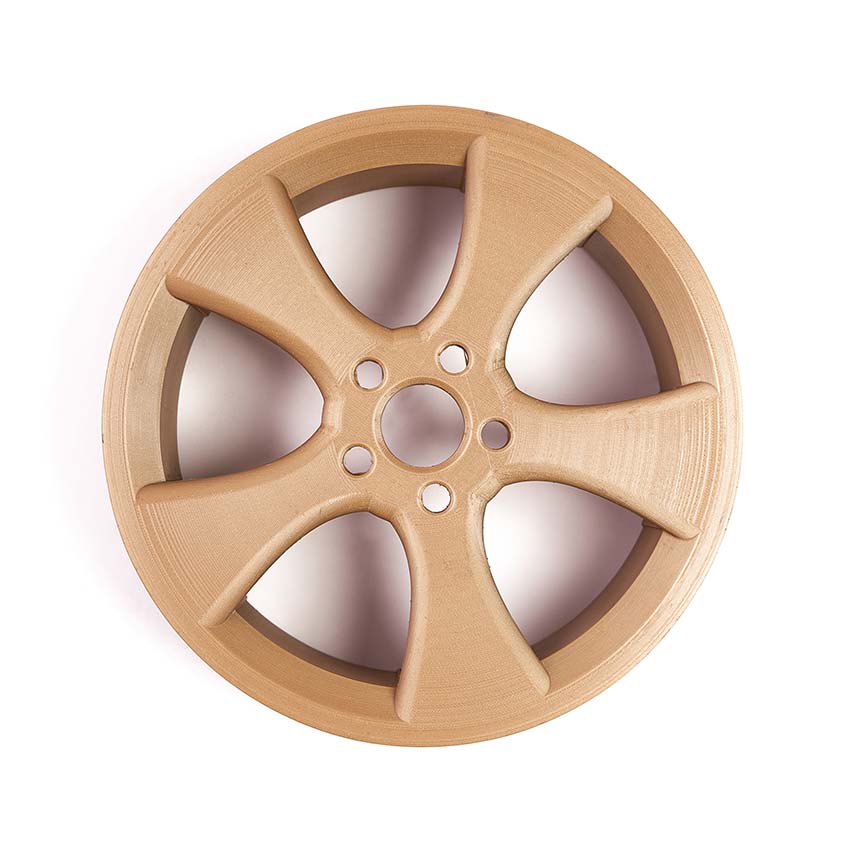
E.E: At what stage is the market where you are currently active?
F.L: Even though 3D printing may seem like a novelty, it has already matured since it first hit the market a few years ago. The advantages of 3D printing were first utilized in the military and medical industries, mainly in the creation of prostheses. Afterwards, 3D printing began to be utilized by the manufacturing industry and soon afterwards, a range of smaller printers appeared, capable of being utilized in education, culture, business or by individual customers in their own homes. Thanks to ever developing technologies, we can now print items from a wide range of materials, such as heat-shrinking or temperature-resistant polymers. Building on years of experience, we’re rapidly and constantly evolving and improving.
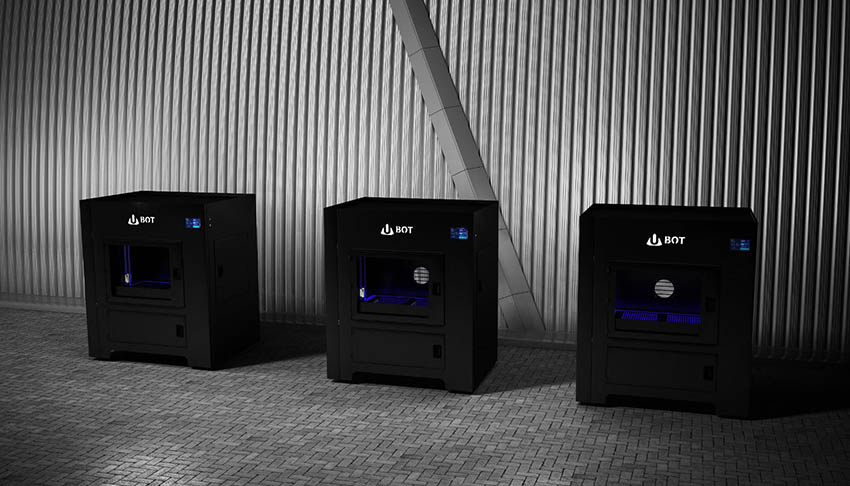
E.E: What can you tell us about market trends?
F.L: We’re following the trend of high-quality 3D printers designed with the manufacturing industry in mind. We use the FFF (Fused Filament Fabrication) technology, using thermoplastic polymers. We want to ensure that our printers can use a wide variety of materials that can be used as alternatives to metal alloys, such as nylon mixed with carbon fiber. Producing printers such as ours is a lot of work, but ensures that they can handle the expectations of the manufacturing industry, which is our main target.
E.E: What are the most innovative products marketed?
F.L: There are various 3D printing technologies, differentiated by the utilized materials. Currently, the three most popular methods are: epoxy resin printing, a precise, but relatively fragile method, usually employed in modelcraft. Powdered steel printing and polymer printing (FFF), the latter method being used in our products. Currently, the most innovation happens in printing technology and methods, rather than the printing devices themselves. In 3D printing, precision, speed and low costs are paramount and we believe to be the industry leaders in these areas.
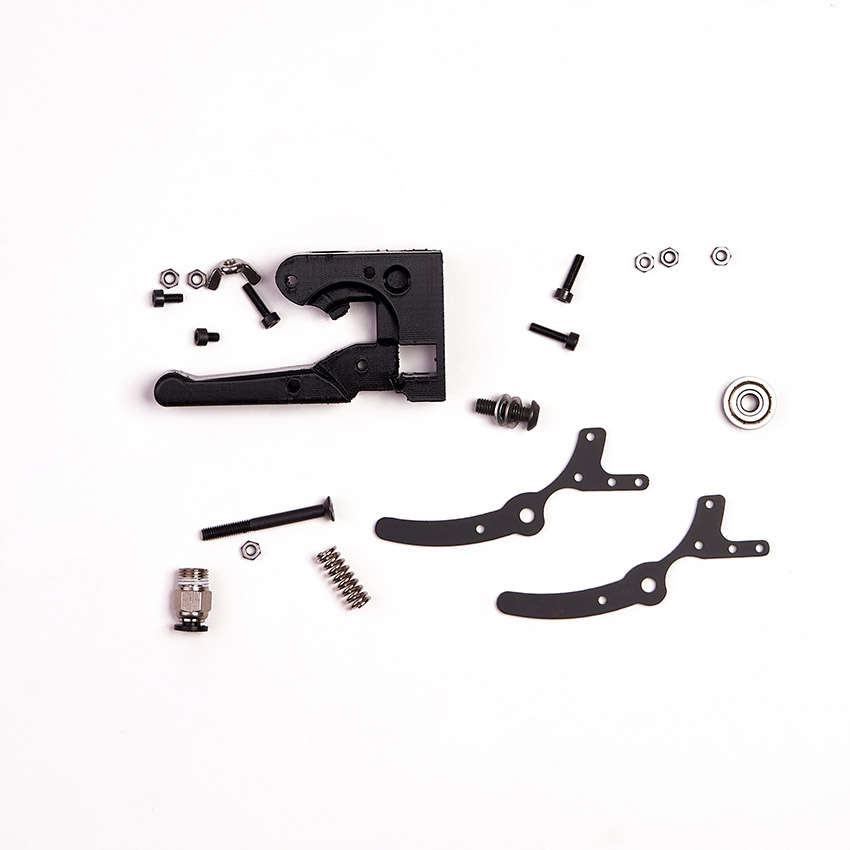
E.E: What estimations do you have for the rest of 2022?
F.L: 2022 is coming to a close, but we’re not slowing down. In Q1 2023, we’ll be taking part in a Polish education program that aims to give schoolchildren the access to the new technologies to study, learn and work with. Hopefully, we’ll help educate the future generations of engineers, sparking interest in future technologies from the earliest stages of education. Beyond that, we aim to expand to foreign markets, such as Romania and Italy. We’re currently working on a very innovative printer model. It’s currently top secret, but we’ll be dropping hints very soon on our social media, so remember to follow us!