3D Spark is a Hamburg-based B2B manufacturing decision support software company. The company offers a web platform that analyzes 3D CAD files, 2D drawings and metadata and suggests the lowest cost, fastest and most sustainable manufacturing process in a transparent way. Their focus is industrial 3D printing but they also evaluate the cost of common conventional manufacturing methods such as milling and casting.
Interview with Ruben Meuth, Co-founder & Co-CEO & Cagri Üzüm, PhD | Business Development at 3D Spark.
Easy Engineering: What are the main areas of activity of the company?
Ruben Meuth & Cagri Üzüm: 3D printing service providers spend a lot of time responding to requests for quotations, particularly with regards to printability analyses and cost calculations. This ties up sales staff and technology experts who could otherwise be generating revenue.
Large OEMs face the challenge of making 3D printing accessible to many of their tens of thousands of employees in order to realize the full potential of the technology in terms of cost-, lead time- and CO2-savings.
Global leaders from industries like rail (Alstom, Deutsche Bahn) and model railroading (Miniatur Wunderland), Automotive (ZF Friedrichshafen), and manufacturing service providers (MetShape) use the 3D Spark platform to quickly identify the most efficient manufacturing technology for each part and keep track of their savings via a detailed dashboard. Alstom for example saved a validated €1.8M in 2022 and is targeting €5M in manufacturing cost savings alone in 2023 with the help of 3D Spark.
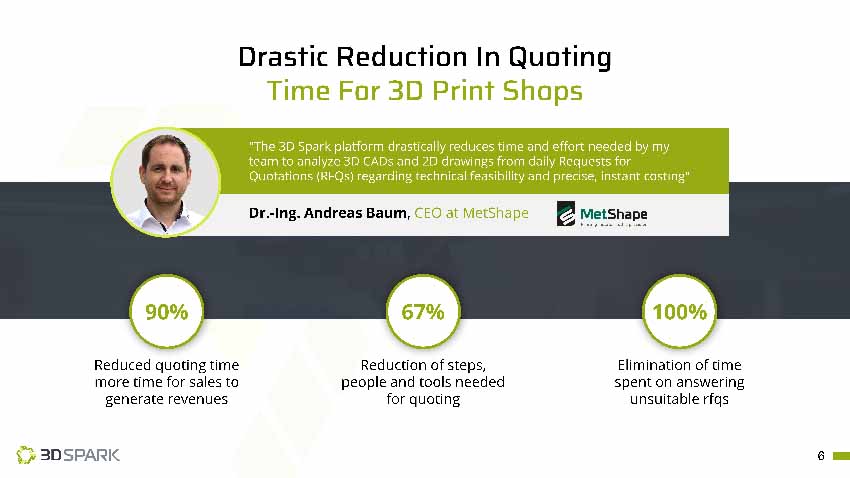
Typical users at manufacturing service providers are sales representatives.
Sales reps reduce their quoting time by 90% through automatic manufacturability checks and instant costing for 12 different 3D printing technologies as well as milling and casting.
Unsuitable requests are answered 100% automatically and thus no longer burden employees.
Therefore, the sales team has more time to generate revenue.
Fewer software tools are needed, thus saving licenses and avoiding media breaks.
Technology experts are not bothered anymore by sales with technical inquiries to answer RFQs and thus can concentrate on value-adding activities such as design engineering for ordered projects.
Typical users at OEMs are 3D printing department/program managers, all of their team members like 3D printing experts, as well as purchasing-, spare parts-, and obsolescence managers.
Added values are 86% reduction in RFQs written – less effort spent by purchasing writing unnecessary RFQs that will lead to unattractive offers and therefore no orders
Data security is increased as fewer quotation requests with sensitive CADs and drawings are sent to fewer service providers.
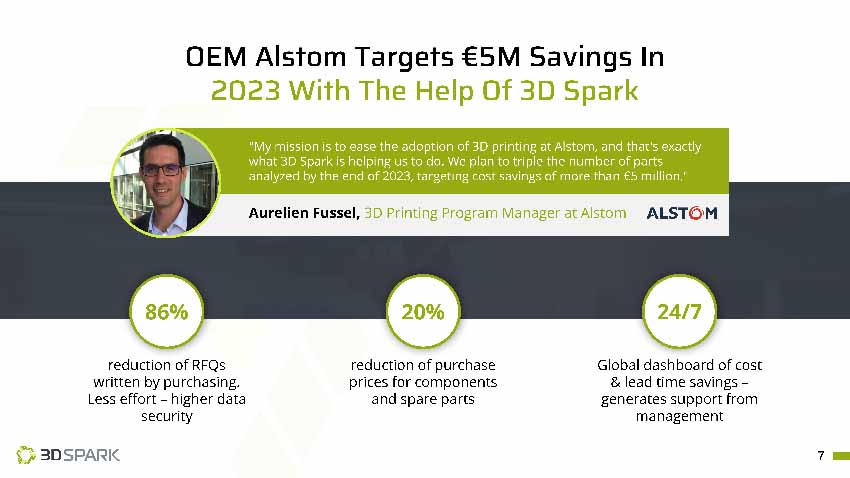
Measurable learning effects for employees due to 24/7 available software for comprehensible answers to their requests
Live dashboard of total cost, lead time and CO2 savings helps management generate support and funding.
E.E: What’s the news about new products?
R.M & C.Ü: Based on customer feedback, several new features have been deployed during the last weeks. This includes fully customizable machine, material and process chain configurations so that each production reality in any company can be modeled, reaching time and cost accuracies of +/- 5%. This by far exceeds any accuracy previously reached, typically using proprietary excel tools, whilst cutting time spent by factor 10.
Carbon footprint calculation of 12 additive manufacturing (AM) technologies is another brand new feature helping users to make sustainable decisions.
Full ERP integration is another recent and major feature. This enables customers to get instant costing & manufacturability feedback from 3D Spark directly from within their ERP system. They can then generate quotes and work plans in their ERP system based on the process steps and times required supplied by the 3D Spark API.
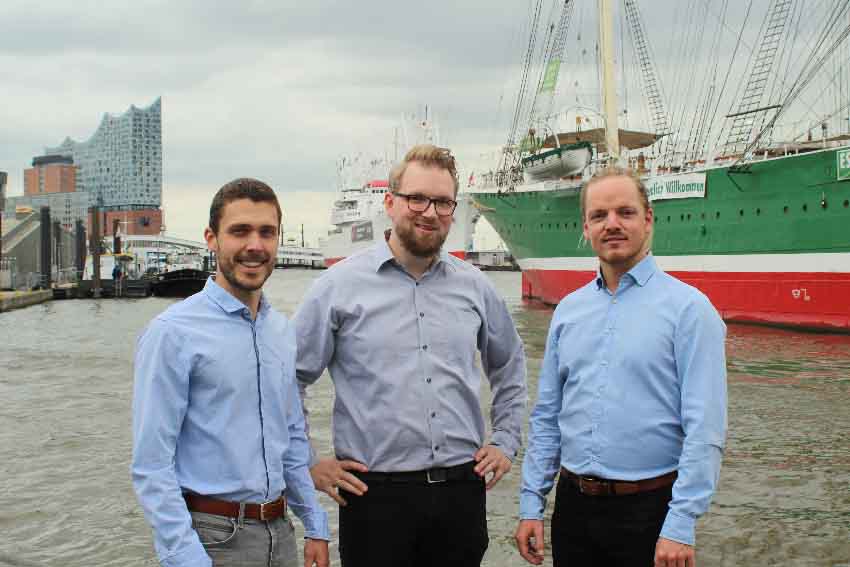
E.E: What are the ranges of products?
R.M & C.Ü: We have a single web-based, all-in-one software product. We add even major and distinct new tools to this single web platform so that technical users can get more from 3D Spark day by day. We also noticed that keeping all analysis tools under one platform is advantageous for manufacturing managers and executives, who can reach cost, time and sustainability related data at once via the 3D Spark dashboard.
E.E: At what stage is the market where you are currently active?
R.M & C.Ü: 3D Spark’s customer base is active in the global rail, automotive and industries, which are well-established but are continuously adapting to new technologies such as AM. And AM itself, which is our focus, is experiencing high growth in adaptation and revenues. We believe the market has overcome its first hype and is now maturing into wide spread industrial adoption with new innovative machines, materials and software being developed, such as our instant printability-check, technology-comparison and resource-calculating tool.
E.E: What can you tell us about market trends?
R.M & C.Ü: Additive manufacturing enables on-demand, custom and function-focused manufacturing as no other technology has ever done. Given that, it is amazing but not surprising that AM industry has grown with a CAGR of 21.6% between 2010 – 2021, and it is expected to keep this pace in the coming years. Major trends in AM enabled manufacturing are in accord with the needs of the industry: wider use of additively manufactured (especially metal) end-parts; a focus on cost-efficient and high-performance materials; more efficient quality assurance practices; sustainability enabled by green materials, recycling and energy-efficient machines; and finally user-friendly but strong software solutions to enable what the industry calls the “digital thread”.
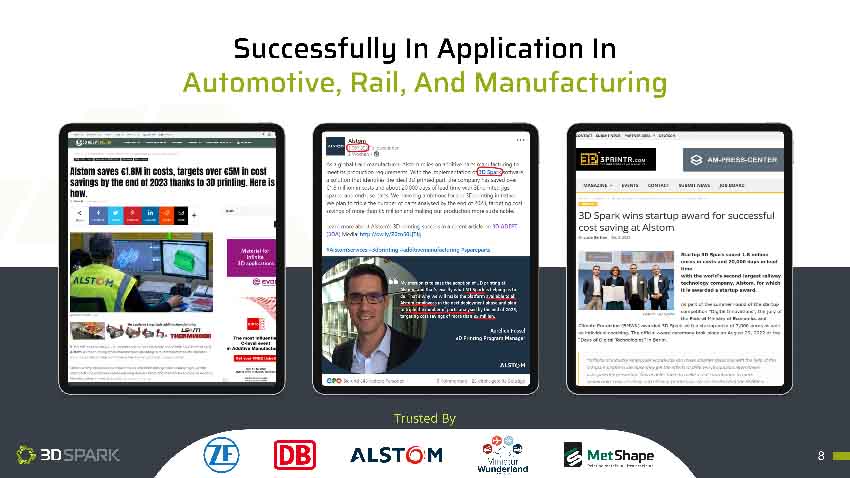
E.E: What are the most innovative products marketed?
R.M & C.Ü: Additive Manufacturing is a vibrant and innovative industry. We can categorize the suppliers as 3D printer / machine makers, materials producers and software developers. Recent industrial 3D printers and periphery are larger, faster and more reliable. On the materials front, both established materials companies and startups have introduced high performance feedstock for the printers such as new alloys and engineering grade polymers. Software offerings are increasing as well. We see a trend towards digital inventories, where digital copies of parts are stored in a cloud and can be produced on-demand with a previously confirmed network of printers so that reproducibility and quality are ensured. This is a big step towards industrialization of AM. Data preparation, build simulation, MES and ERP software are also getting better and more interconnected. Innovative tools for part identification, technology suggestion and instant calculation have been offered as well. For me personally, one of the most exciting features is the ability to analyze 2D technical drawings as if they are modern 3D CAD files.