C&J Industries, an employee-owned, custom injection molder located in Meadville Pennsylvania, recently acquired a 220-ton Nissei two-shot press; this is an incredible piece of machinery that will allow them to accommodate jobs which they may have had to previously turn down. This is a strategic move that will strengthen the company in the wake of a growing demand for products that require two-shot capabilities. With this new machine, C&J will save on costs, lead time to market, and improve overall product quality, all while maintaining military specifications.
By using a two-shot process, it is both cost-effective and sustainable. Instead of paying for two separate injection molding processes running sequentially, you pay for two injection molding processes that run in parallel. Each time the mold cycles you get a complete part, cutting the manufacturing process time nearly in half. At the end of the day, you are saving both man and machine hours.
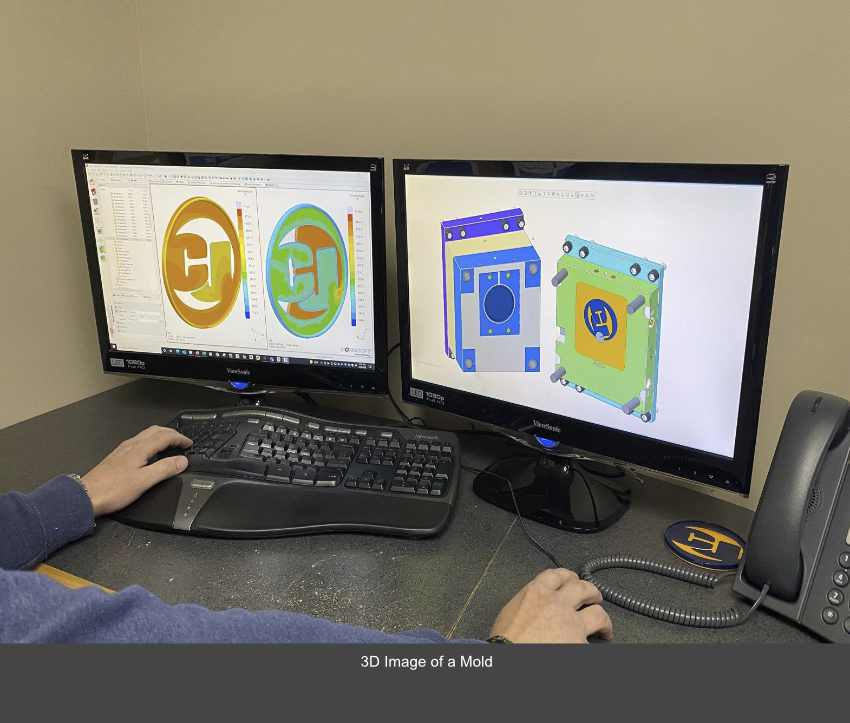
Though the primary advantage to a two-shot process is cost savings, you will also find that you’ll get better product quality. Since it stays in the mold, the results are better fastening between the two resins and better matching of the second core or cavity to the first part. By eliminating secondary assembly and bonding the parts together, overall part quality is greatly improved. The end product is aesthetically pleasing, and provides the capability to choose between a variety of different colors. Another benefit of two-shot molding is that it has a more hermetically sealed part when compared to overmolding; this ensures that no air can leave or enter. While the final quality of a two-shot part compared to an overmolded part can be similar, you will find that its benefit comes from scrap rates and machine capacity. You are likely to run through more parts in the overmolding process to get the same amount of quality parts that you would get with two-shot molding.
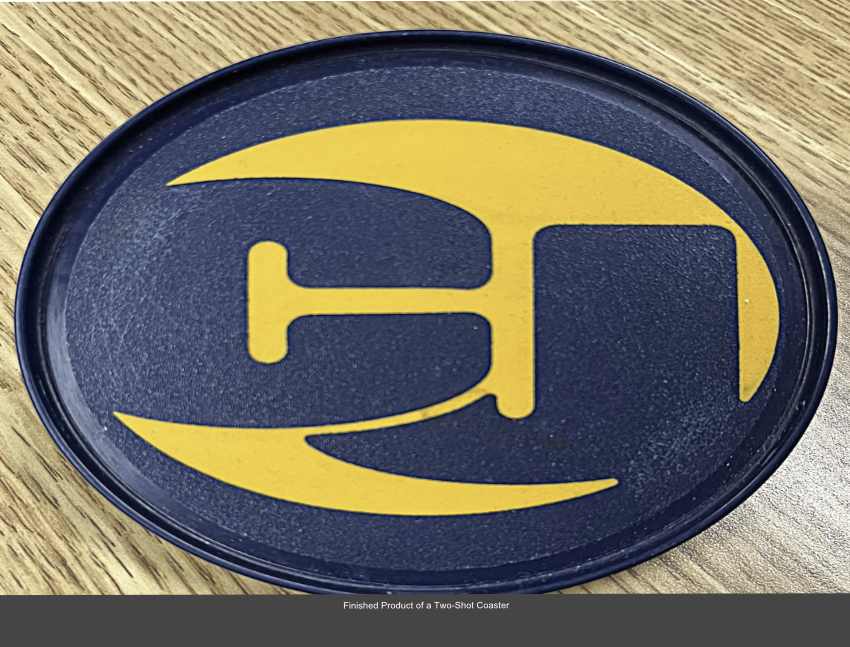
In addition to saved costs and improved quality, the two-shot process reduces lead time to market. Secondary assembly operations, separate over-molding, and insert molding of the first part are eliminated. By decreasing the frequency in which the parts are handled, the risk of damage or contamination is greatly minimized. “It has helped with part consolidation resulting in reduced cost and lead time to market,” says John Hanninen, senior engineer of new business development at C&J Industries.
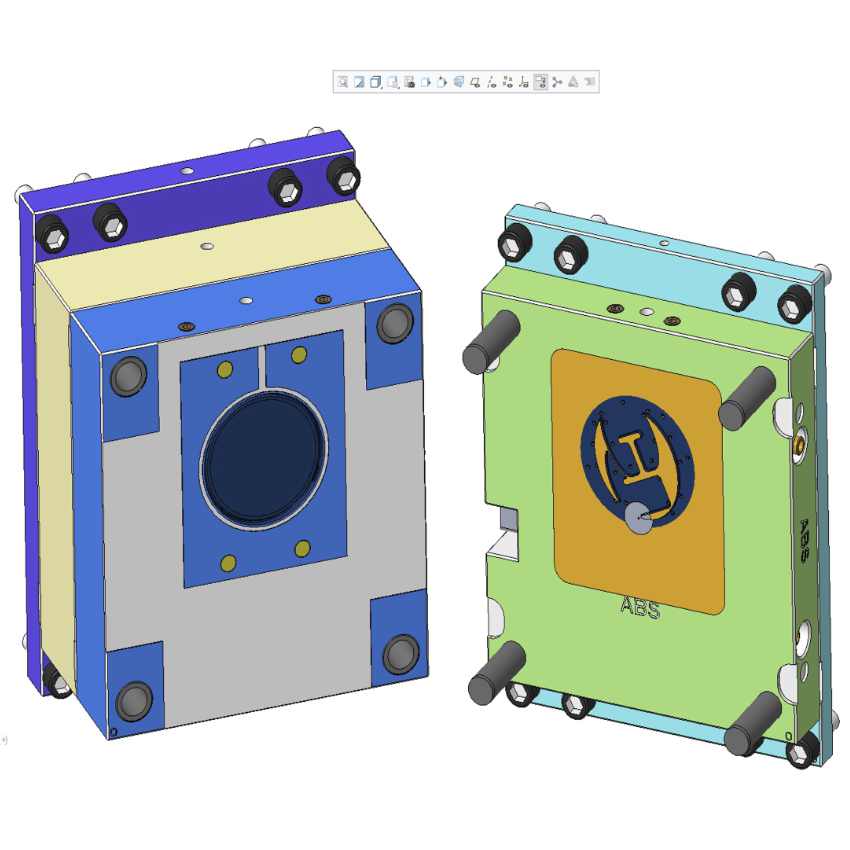
About C & J Industries
C & J Industries was founded in 1962 as a privately held custom injection molder and medical device manufacturer. C & J supplies plastic injection molded components, assemblies, and complete devices to a wide variety of market segments, including Medical Device, Pharmaceutical, Industrial, Consumer Products and Telecom.
(814) 724-4950.