Tiger-Vac has led the charge in explosion-proof recovery systems innovation for over 43 years, with an aim to create safe workplaces for companies around the world.
They are a leading global manufacturer that specializes in the design and manufacture of legally certified portable industrial vacuum and dust collection systems for contamination-controlled environments and hazardous locations. All Tiger-Vac products are third-party certified to ensure compliance with legal safety standards and provide ample protection to the user.
Certifications of compliance include CE, IECEx, ATEX, CSA and ISO.
Interview with James Orsini, Marketing Manager at Tiger-Vac Inc.
Easy Engineering: What are the main areas of activity of the company?
James Orsini: Our number one priority is to find ways of improving workplace safety by designing innovative industrial vacuum and dust collection systems that meet certification standards. We have an extensive selection that cater to the challenges faced by many industries including Metalworking, Food, Pharmaceutical, Additive Manufacturing and Firearms.
For unique applications, our incredible team of designers, engineers and quality control specialists are committed to creating the perfect recovery system while possessing an explosion-proof build for safe operation. We can even tailor our designs to fit a customer’s unique needs!
E.E: Can you share some news about new products?
J.O: Certainly! We recently released the AVSD-2 ORDLOC 652, which can be found on our website. It is a powerful pneumatic (air-powered) vacuum system that produces strong suction without using electricity or possessing moving parts. This ensures that the system can run for extended periods of time without requiring maintenance.
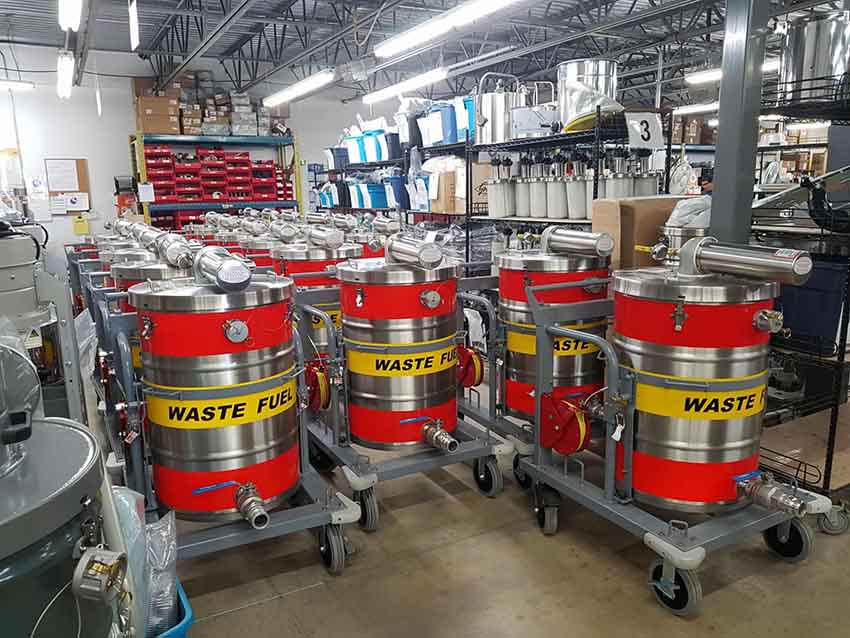
E.E: What are your product ranges?
J.O: We provide over 220 solutions for dust recovery needs. As such, our products can be broken down into some general categories including substance, electric/pneumatic, environment and dust collector/vacuum.
Substance: The substance being recovered will influence what type of system is required. For example, liquid chemical samples such as mercury require a system that utilizes an active carbon filtration system to capture harmful vapors, while metal powders are best suited to a wet mix system which dilutes the metal’s combustible properties.
Electric/pneumatic: Electric-powered systems require an electrical outlet to operate, whereas pneumatic systems require a compressor. The availability of either will influence what type of recovery system is required.
Environment: Each hazardous work environment can be classified by European and International certification standards as zone 20, zone 0, zone 21, zone 1, zone 22, and zone 2. Preventing an accidental explosion is paramount to worker safety, therefore necessitating different levels of ignition protection for recovery systems within these zones.
Zone 20 environments always contain airborne dust particles and zone 0 environments always contain vapors, necessitating that the recovery system possesses a very high level of ignition protection.
Zone 21 environments often contain airborne particles, but not always, while zone 1 environments often contain vapors. This necessitates a high level of protection.
Lastly, zone 22 environments carry little risk of airborne dust and zone 2 environments contain little risk of hazardous vapors, but both still require a certified vacuum system that provide a normal level of protection.
Dust collector/vacuum: Simply put, for the strict collection of airborne substances, dust collectors are required, whereas vacuums are ideal for substances that have settled on surfaces.
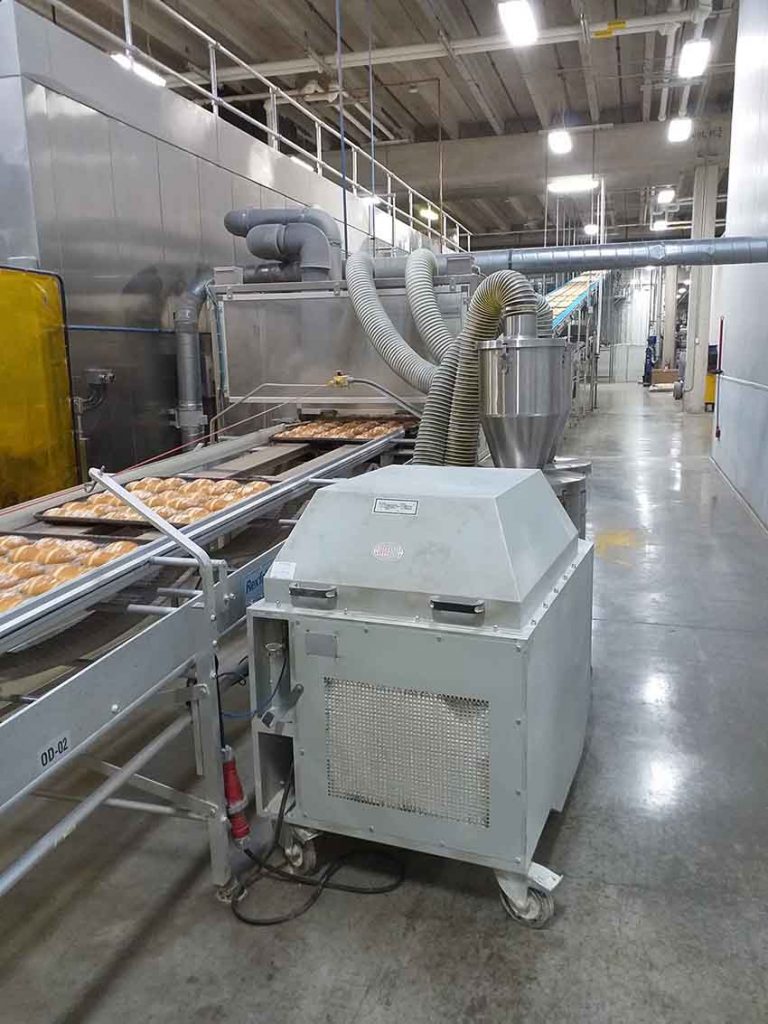
E.E: What can you tell us about market trends?
J.O: It’s no secret that material costs are on the rise. It is becoming increasingly expensive to manufacture product, and so companies are looking for ways to reduce costs. Tiger-Vac does not call their machines “recovery systems” for nothing – many of our models can preserve the collected substances, allowing them to be saved and reused.
For example, powder bed fusion methods of 3D printing make use of powders that are heated into solid forms. Normally, much of the excess powder is wasted due to inefficient recovery, a problem which can be avoided with the right vacuum system. Saving raw materials means reducing environmental waste and costs!
E.E: What are the most innovative products marketed?
J.O: Good question! Technically speaking, all our recovery systems are innovative, as we are the only company whose products are completely third-party certified. It’s not uncommon to see companies claiming to sell explosion-proof certified products, but really, they are only certified in-house and lack official testing. This can be extremely dangerous to the customer.