VITO was founded in 2001 by Andreas Schmidt and has grown to a company with 50 employees. VITO AG is based in Tuttlingen, Germany and has subsidiaries in Hürth (Germany), Orlando (USA), Dubai (UAE) and Santa Lucia di Piave (Italy).
With more than 22 years of experience in production and sales of filtration systems, VITO frying oil filters became a standard in 150 countries and over 50.000 professional kitchens and bakeries.
As a global player in the sector of portable filtration systems, the company took up a long-standing idea and decided to expand the range of customers to the industrial sector. VITO has an enormous potential in this field and creates indispensable advantages with its effect.
For the filtration of cutting fluids, oils and coolants, the VITO gets placed in the industrial basin to remove all chips and solids. The whirl effect causes a strong suction, whereby the particles get sucked directly inside the machine. Additionally, the coolant lubricant gets ventilated during the process.
Interview with Sina Maier, International Key Account Manager at VITO AG.
Easy Engineering: What are the main areas of activity of the company?
Sina Maier: The VITO filter is used in the industrial area. The target businesses are those which turn, grind, or mill any material, basically every business that works with coolant lubricant, emulsions, oils, watery solutions and washing baths. By regularly filtering with VITO, our customers can decrease tool wear and the forming of bacteria and germs. Additionally, they extend the service life of the coolant through better cleaning and ventilation.
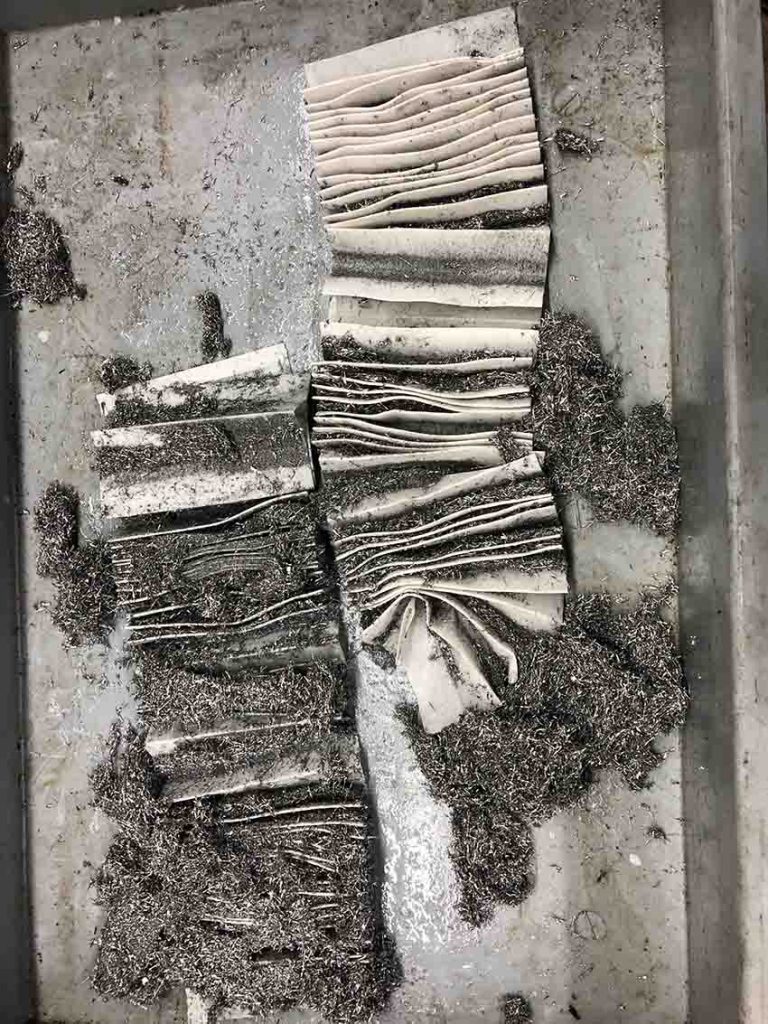
E.E: What’s the news about new products?
S.M: Our products meet all the needs of our target group and offer the perfect solution for any type and quantity of cooling lubricant. Nevertheless, we are always trying to improve our products continuously. At the moment we are further developing our VITOconnect function which allows customers to access the important information of the machine remotely. They can also adjust the filtration cycle time from their smartphone or tablet.
E.E: What are the ranges of products?
S.M: The VITO coolant filter product line consists of a portable and a mobile device. The VITO 90 is a small portable filter that can be put directly into the basin. It filters the lubricant in just a couple of minutes using pressure filtration and a fine cellulose filter paper inside. The VITO XM is a larger device on wheels. It works with vacuum filtration and can store and transport up to 75 liters of coolant lubricant.
E.E: At what stage is the market where you are currently active?
S.M: The market of our target group is already established for many years. Our customers are all industrial companies that operate metal or plastic processing and use any type of cooling lubricant on a daily basis.
E.E: What can you tell us about market trends?
S.M: A trend that has always played a significant role in industrial companies is safety at work. This is also our top priority when it comes to the needs of our customers, and VITO can increase safety at work. By filtering the coolant, we reduce bacteria and fungus that may cause illnesses for the employees working near it. Furthermore, the VITO unit ensures the highest safety at work due to avoiding direct contact with the lubricant during the filtration.
Another ongoing trend in the companies is active environmental protection. In addition to the sustainable production of the VITO with components from regional suppliers, our customers reduce their co2 emissions from their operations. This is mainly due to the reduction in waste. Firstly, because of less cooling lubricant replacement. Secondly, the pump does not get clogged because VITO removes all chips in the lubricant; therefore, the pump needs to be replaced less.
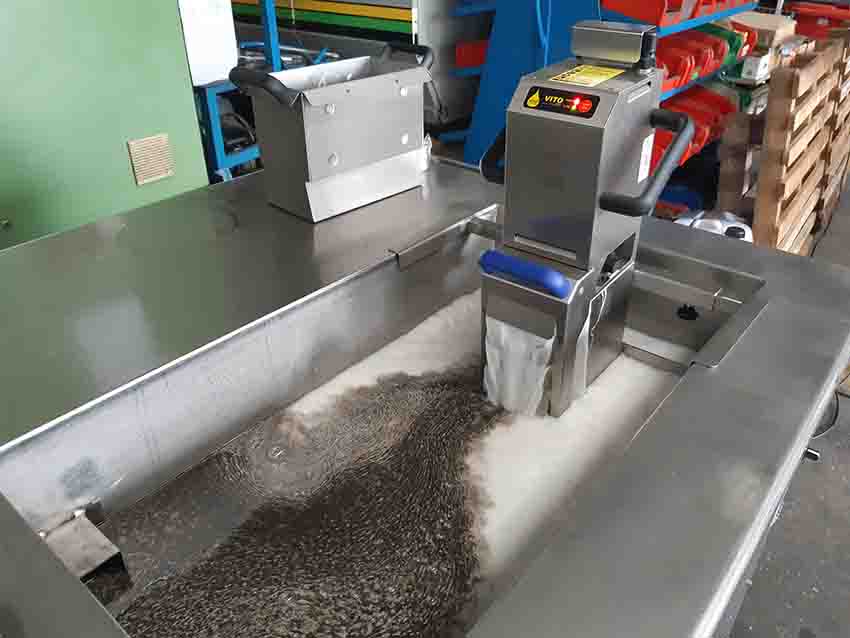
E.E: What are the most innovative products marketed?
S.M: The VITO coolant filter is the most innovative in-tank filtration system. Due to its pressure filtration creating a vortex effect, it can suck up all the chips and other impurities from the very bottom of the tank. With the help of the cellulose filter, the removed particles are very fine, up to 5 microns.
Our biggest customer, one of the world’s leading medical technology companies, achieves, with this innovative technology, savings of 100%, what does this mean exactly? Well, their pump is no longer clogged by the many metal shavings. This means they never have to change their pump again, which they used to change every two weeks.
E.E: What estimations do you have for 2023?
S.M: For the future, we hope for more market presence. We want to be known for our VITO cooling lubricant filter in different regions. Additionally, we want to further expand this business area in the form of new employees exclusively for the industrial sector as well as increased visits to trade shows.