AmeraLabs specializes in developing and producing high-quality resins for 3D printing. Founded in 2017 as a passion project, AmeraLabs has worked tirelessly to elevate industry standards for 3D printing resins. Today, the company is proud to have their own market share, serving over 65 countries and becoming a trusted choice for 3D printing enthusiasts worldwide.
Interview with Andrius Darulis, Co-founder at AmeraLabs.
A brief description of the company and its activities.
Andrius Darulis: At AmeraLabs, we take pride in formulating materials designed to inspire and empower the creativity of the global 3D printing community. Our resins are engineered to provide exceptional physical properties, making them accessible to hobbyists and professionals. We specialize in resins tailored for engineering, dental applications, and miniature enthusiasts, ensuring that our products meet the diverse needs of our customers.
What are the main areas of activity of the company?
A.D: While our factory produces resins for a global market, our professional chemists’ team is dedicated to developing new materials. Our primary focus is on researching and creating innovative products to expand our range, meeting the diverse needs of professionals across various fields.
The AmeraLabs team is committed to sharing our knowledge about 3D printing, supporting creators, and fostering community engagement through impactful collaborations and giveaways. In 2023, we delivered over 100 liters of premium resin, underscoring our commitment to supporting community projects and competitions. We believe in the importance of providing access to high-quality materials for 3D printing. This belief drives our active participation in contests hosted by esteemed partners, including Archvillain Games, Dragon Trappers Lodge, and Mammoth Factory.
Our journey goes beyond material distribution; it is a collaborative and vibrant exploration of possibilities enriched by the diverse talents and innovative visions of creators worldwide.
What’s the news about new products/services?
A.D: This year, AmeraLabs proudly achieved ISO certification, conforming to the ISO 13485:2016 quality management system standard. This certification means we are now qualified to produce products for medical use, further demonstrating our commitment to quality and innovation.
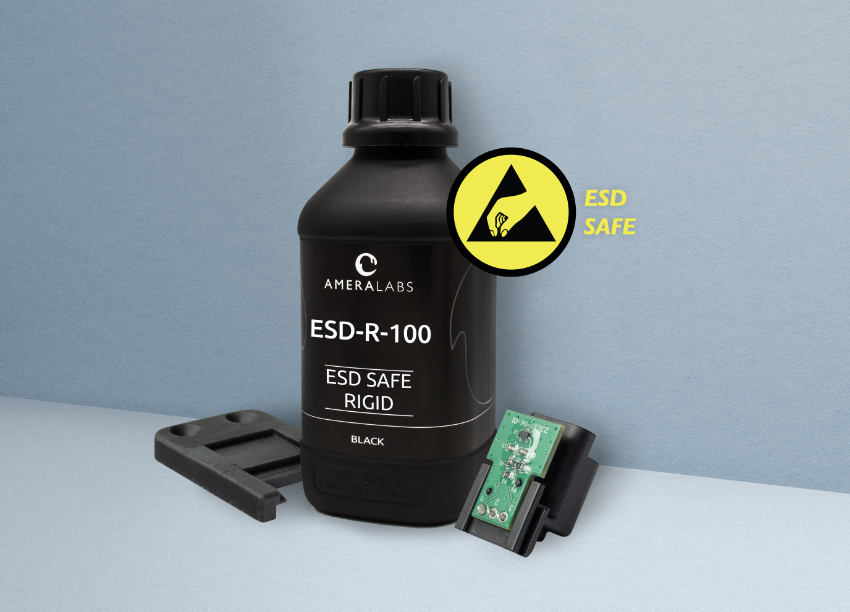
We are also excited to introduce our new versatile engineering product, XVN-50, which has quickly found its place in a wide range of applications. What’s the secret to its versatility? XVN-50 is a tough material with slight flexibility, enabling it to produce precise and accurate models. Our clients have found it perfect for various uses, including various parts, film industry props, and end-use items.
Additionally, our most popular product, TGM-7, is now available in new colors. Previously offered only in grey, clear, and white, TGM-7 can now be enjoyed in red, blue, and yellow. This expansion is a fantastic opportunity for board game and wargame producers to access premium quality material that is easy to work with and visually appealing.
What are the ranges of products/services?
A.D: We work in three main product categories: resins for miniatures, engineering applications, and dental professionals. The range of products includes resins for miniatures hobbyists and boardgames manufacturers. The main product for this purpose is TGM-7 resin with exceptional mechanical properties that enable the production of tough miniatures that withstand bending forces and capture the smallest details. We also have a unique product, SiOmaster, dedicated to 3D-printed masters for high-temperature vulcanization silicone rubber mold making. Masters made of this material can withstand several high-temperature silicone vulcanizations without breaking and are resistant up to 180 °C temperature. AMD-3was the first resin that AmeraLabs released, and during this time, it found its place among miniatures, engineering, and dental applications. It provides extremely high details and accuracy, a hard surface, and very low shrinkage, and is temperature and humidity resistant. This material is appropriate for applications like room temperature vulcanization silicone mold making, dental models for clear aligners, prototyping, figurines, metal electroplating, and many more.
We offer the versatile XVN-50 material for engineering applications, enabling the production of high-accuracy parts with a hard surface that can withstand bending. This material is easily post-processed, allowing for drilling, cutting, machining, or tapping. We also cater to the electronics industry, where electrostatic discharge (ESD) protection is crucial. Our ESD-R-100 3D printing resin is perfect for tools, casings, connectors, soldering jigs, conveying, metering, and sensing applications. This material surprises with its high resolution, accuracy, stability, and chemical and temperature resistance, expanding the possibilities of use.
While we are working on new dental ISO-certified materials for intraoral use, our customers reliably use DMD-21 and DMD-31 dental model 3D printing materials suitable for most dental models. Those materials meet all dentistry professionals’ needs and are adaptable to a wide range of uses.
While we already cater to a wide range of needs, we are continuously expanding our product range. Our aim is to ensure that as many users as possible can find premium quality 3D printing materials that perfectly meet their unique requirements. We value your needs and provide the best solutions for your 3D printing projects.
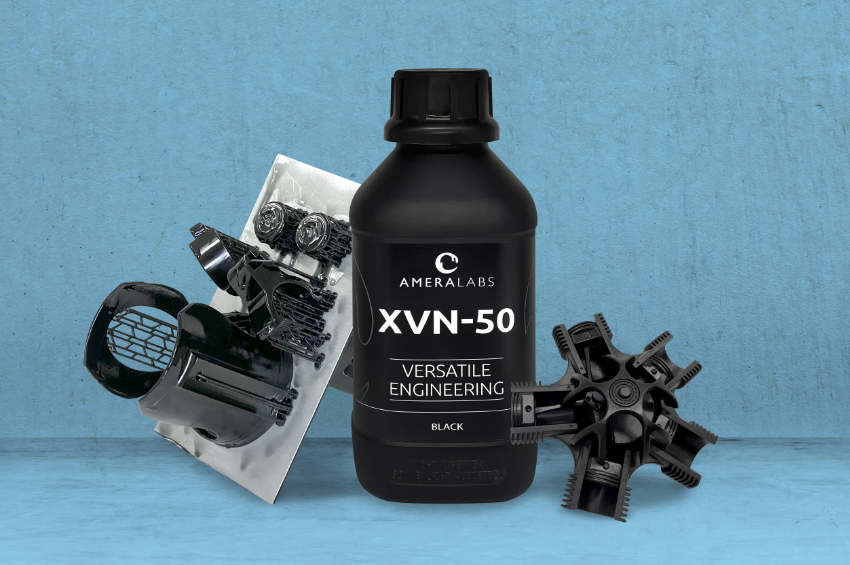
What is the state of the market where you are currently active?
A.D: The market is growing rapidly. More and more people are discovering the benefits of resin 3D printing. We are happy to see the growing number of customers who choose high-quality products to ensure instant successful printing and models that are made to last.
What can you tell us about market trends?
A.D: An increasing number of industries are incorporating 3D printing. The TGM-7 revolutionizes the production of miniatures. Previously, 3D printed miniatures were quite fragile, thus they were printed only by hobbyists. Our materials are very close to injection-molded plastics. This allows game manufacturers to do small series of rapid production on demand locally, instead of investing a lot of money in manufacturing in China.
Although the expansion into new branches/applications is still slow, but as more designers and designers are educated in universities about SLA 3D printing, that development will only accelerate.
The 3D printing market has been experiencing rapid growth and innovation, driven by advancements in technology and increasing adoption across various industries. Industries such as aerospace, automotive, and healthcare are increasingly adopting 3D printing for mass customization, allowing them to produce tailor-made parts and products on a large scale. Combining 3D printing with traditional manufacturing techniques to leverage the strengths of both methods for more efficient and cost-effective production. 3D printing is being integrated into supply chains to reduce lead times, minimize waste, and enable localized production. The decreasing costs of 3D printers and materials make the technology more accessible to hobbyists, small businesses, and educational institutions. Overall, the 3D printing market is poised for continued growth, driven by technological advancements and broader industry adoption.
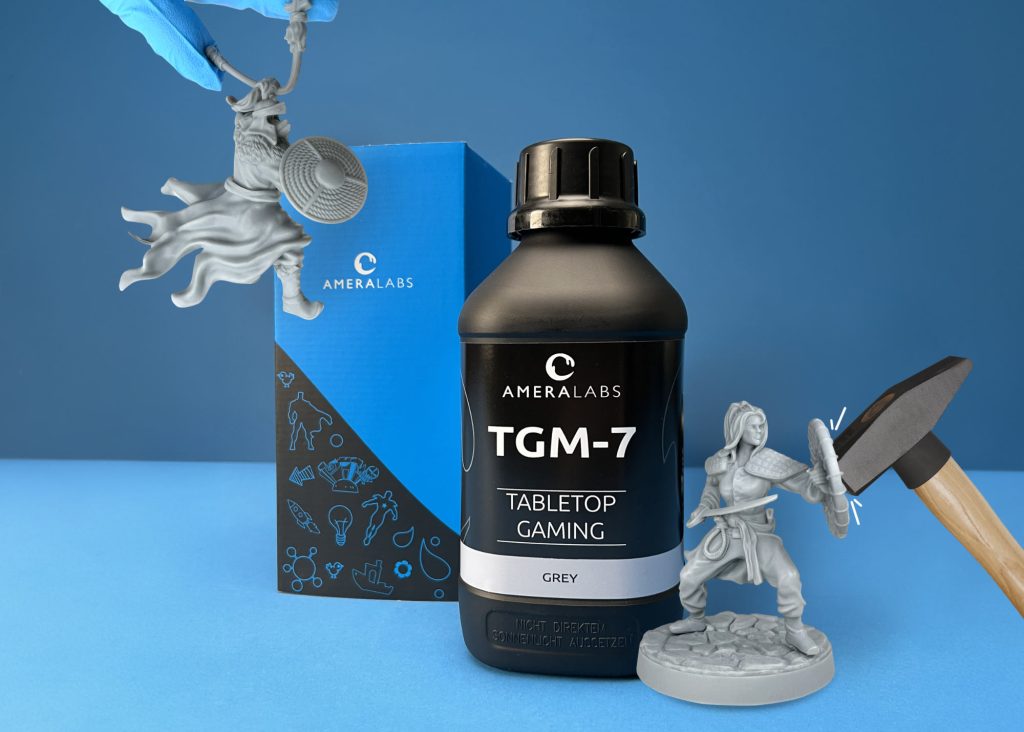
What are the most innovative products/services marketed?
A.D: In the rapidly evolving world of industrial production, the demand for materials that combine advanced functionality with safety is paramount. One such innovation is the development of electrostatic discharge (ESD) safe 3D printing resins. Due to their unique properties and versatility, these specialized materials are becoming indispensable across various sectors, including robotics, electronics manufacturing, and automated production lines. By protecting sensitive electronic components from electrostatic damage and enabling the rapid production of custom tools and parts, these resins are revolutionizing industrial production processes, ensuring both high performance and safety.
What estimations do you have for 2024?
A.D: The hype about 3D printing replacing all traditional manufacturing processes is over; now, people understand the limitations and capabilities of resin 3D printing and are looking realistically at where to apply this technology. Resin printers are improving yearly with added sensors, automatic features, etc. 3D printing becomes easier to adapt. So, more and more people and companies will adopt this technology in the upcoming years. Thus, we will see new exciting applications and areas where resin 3D printing will revolutionize the whole production process.