Schlötter’s electrochemical laboratory was established in 1912. Over a century of robust R&D experience provides firm foundations for the company’s ongoing and sustainable success.
Through their chemistry, customer service and production plants, Schlötter provides integrated coating solutions for general metal finishing, decorative applications, anodizing, electronics and the PCB industry.
A brief description of the company and its activities.
We are committed to constantly improving and developing products – including pioneering tailormade products for specific customer needs. By working alongside our customers to fully understand their requirements we can deliver high satisfaction with processes developed for bespoke applications.
We are driven by two complementary approaches: constantly improving our existing technologies; and developing future technologies for tomorrow’s demands: 25% of our employees are engaged in research.
Schlötter is an international company with products available worldwide.
What are the main areas of activity of the company?
In conventional electroplating, Schlötter has been a leading supplier for zinc and zinc alloy processes for decades. Our extensive portfolio includes pretreatment (incl. pickling), electroplating, and post-treatment (passivation & sealing).
Schlötter’s strong PCB industry reputation is built on our market-leading wet chemical processes (particularly copper and tin plating), which are critical for ensuring reliable electrical connections and durable circuit boards. Our expertise also extends to pre-plate cleaners that help prepare surfaces for optimal adhesion and plating quality.
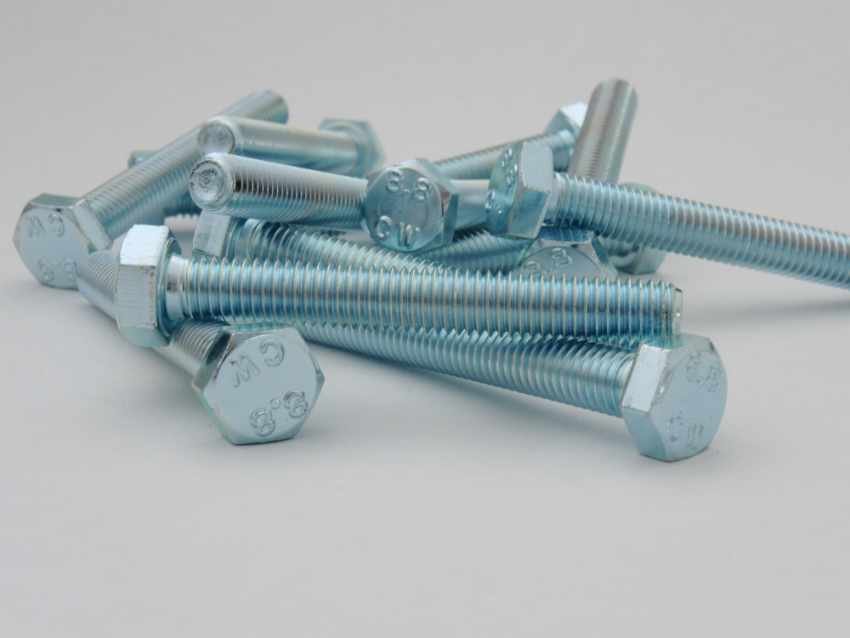
Our recent expansion into final finish applications with the new electroless nickel immersion gold process further complements our range by providing a robust and corrosion-resistant surface finish which is ideal for high-performance electronics. Our continued innovation in these areas makes us a key player in delivering high-quality and durable PCB solutions.
Schlötter’s extensive range of electronics industry products and surfaces is continually evolving to meet ever-higher expectations for electric components: solderability, press in technology, and reduced whisker-formation. We provide innovative solutions and high-performance chemistry. To characterize the physical properties of electroplated surfaces, we’ve partnered with iChemAnlytics to pioneer unique test equipment: the WECO-X test stand.
The bench can be used to perform tribological tests to measure and document electrical resistance and force, where testing is carried out under set conditions (temperature, oxygen content, etc.). Tests on whisker formation and ‘pull off’ tests also help to optimize and monitor R&D on a process- and customer-specific basis.
In recent years, the higher requirements for base materials have resulted in materials with higher strengths and increasing demands on coating processes. As the influence of reaction hydrogen on base material plays an increasingly important role, its influence must be taken into account both in process development and process monitoring during production. Schlötter uses the WSMRE test bench (developed jointly with iChemAnalytics) to achieve this objective.
This also applies to the decorative area of functional nickel-chrome coatings where reaction hydrogen plays an important role in safety parts. Schlötter’s development department has extensive expertise in this area and with the deposition of numerous nickel-, bright- and hard chrome electrolytes (chromium VI-free).
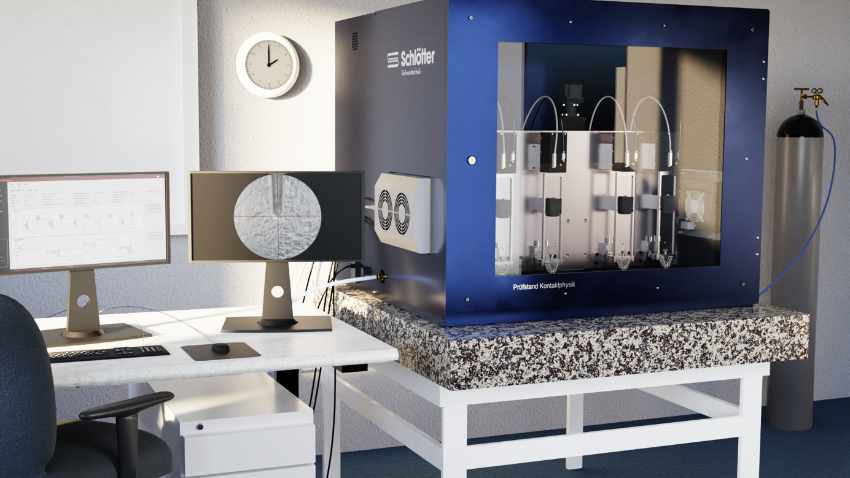
What’s the news about new products/services?
Our award-winning SLOTOCOUP SF 50 copper plating solution has truly set a benchmark in the copper plating industry. Known for its exceptional versatility and performance, it has quickly become the go-to solution for manufacturers in the IC substrate market and advanced HDI PCB production. This success is a testament to its ability to meet the demanding requirements of modern electronics by delivering consistent results with superior plating performance, excellent process controllability, and enhanced precision. The SLOTOCOUP SF 50 has earnt recognition as a market leader by continuing to drive innovation and efficiency in critical applications.
We have developed numerous new and attractive processes in recent years. For the connector industry, we attended this year’s Würzburg connector congress – where we presented the SLOTOCONNECT HT 4200 coating system for a high number of plug cycles and high temperatures. Other exciting new developments include a new hard chrome electrolyte based on trivalent chrome (SLOTOCHROM HC 4300), and various further developments in cathodic corrosion protection for new automotive requirements. For example, our new Sealer SLOTOFIN GM 2450 meets the highest requirements for corrosion protection and OEM requirements for multiple friction and heat-release behaviour.
SLOTOSON MI 1930 is the approved Indium coating process for press in connectors, as requested by several EV-car producers. Approved as Whisker-free by a worldwide active producer for electric components plated in Reel-to-Reel application.
Our SLOTOCHROM BC 4130 bright chrome bath and SLOTOCHROM DR 2430 post-treatment deliver a hex-chrome free bright chrome surface, which meets requested colour tone requirements (negative b-value) and corrosion resistance standards.
After re-entering the anodising sector a few years back, our SLOTOXAL range provides pre-treatment, anodising and sealing products.
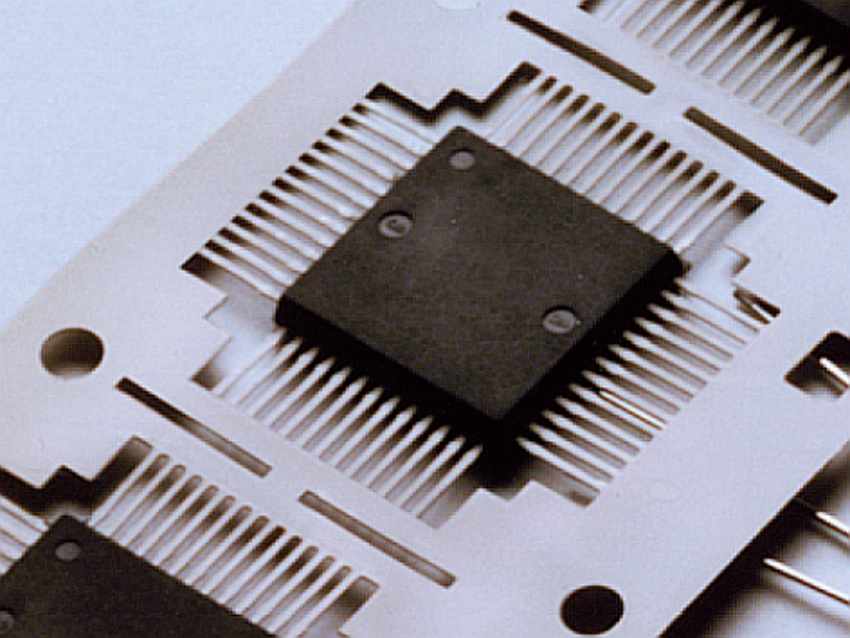
What are the ranges of products/services?
Schlötter is committed to constantly improving and developing products – even pioneering tailormade products for specific customer needs.
In addition to the development and sales of processes for galvanic coatings, we offer customers a comprehensive on-site service, analyses of their electrolytes in our service laboratory, and assessments of defectively coated components when required.
To qualify the properties of layers deposited from our processes we have developed various test benches with our partner iChem Analytics, including the Testbench for Contact physic WECO-X.
What is the state of the market where you are currently active?
As galvanic surfaces are used in many diverse everyday areas we serve a wide market range. Our main market is the automotive industry, where the change to electromobility has had a major impact on the plating industry: fewer component surfaces for combustion engines, and higher demand for fasteners and contact surfaces.
Asia is the main market for our processes – such as Copper SLOTOCOUP SF 50 and Matt Tin SAT 20-1 – for the production of printed circuit boards, hence a large proportion of our PCB processes is based in that continent.
Our Matt Tin SLOTOTIN 40 is used by the biggest PV-system producer in Asia, while local Schlötter companies in Singapore, Taiwan and China enable the efficient selling and servicing of customers.
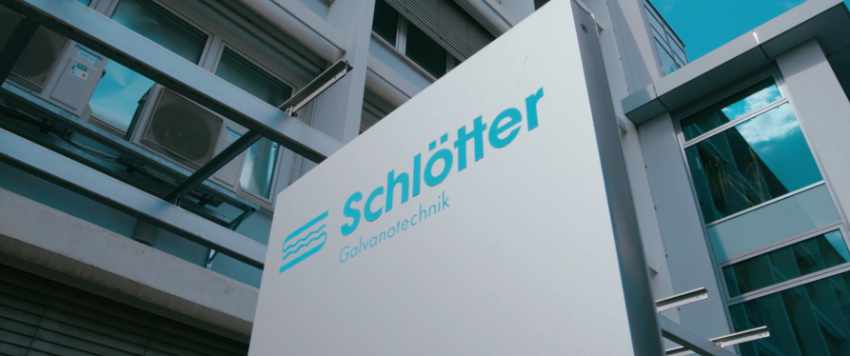
What can you tell us about market trends?
One of the main trends in surface technology (and other sectors) is decarbonisation. In addition to reducing the company’s own carbon footprint to zero, Schlötter is developing processes and coating systems that help customers to reduce their carbon footprint by using less energy and raw materials.
We can already give our customers datasheets about our additives’ carbon footprint.
What are the most innovative products/services marketed?
Our new SLOTOCONNECT HT 4200 and new hard chrome bath SLOTOCHROM HC 4300 are innovative coating systems with unique properties. The production of green hydrogen is also a new field in which new galvanic surfaces for electrodes are required and on which we are working intensively.
What estimations do you have for 2024?
We expect to see a recovery in Q1 2025 from the currently weaker economy. With the market launch of our new procedures and processes, we have a positive outlook for 2025.