The right belt is a key factor in the efficiency and reliability of the entire conveyor system. That’s why it’s so important to choose one appropriately and carefully.
In most conveyor systems, the belt conveyor is the only element that actually comes into contact with the parts, products, or packaging. That’s why it’s crucial to select the appropriate belt to ensure smooth and efficient operation. These eight questions will help you make the best decision.
1. What coefficient of friction is required?
Belt conveyor surfaces range from a very low to a high coefficient of friction. Low-friction belts are ideal for applications where products need to accumulate or come in or out of the side of the belt. The product must be able to slide while the belt conveyor continues to move. Belts with a high coefficient of friction are often used in inclined applications up to 15 degrees. They ensure that the product remains stable due to friction.
2. What temperatures does the belt have to withstand?
There are two important temperature ranges to consider: The ambient temperature and the temporary product temperature. While low ambient temperatures can cause the belt conveyor to become brittle and crack, ambient temperatures that are too high can stretch the belt or loosen the layers at the joints. With regard to temporary product temperatures, you must ensure that these do not damage the surface of the belt conveyor, for example, due to products that are too hot.
3. What color should the belt conveyor be?
The color of the belt conveyor is particularly important in inspection applications, whether inspection is done by automated camera systems or visual inspection. The correct color contrast between the product and belt can be critical to detecting defects or contaminants. In the food industry, for example, blue is often used, as it is rarely found in foods. Residues are thus easy to recognize after cleaning.
4. Is the belt cut-resistant?
If your product has sharp edges, a cut-resistant belt conveyor may be required to prevent damage to the belt surface. Such belts are usually equipped with a hardened urethane or PVC surface that reduces abrasion from sharp parts.
5. Is a belt conveyor with sealed edges necessary?
In cleanroom environments, a belt with sealed edges is often recommended to reduce particles. Such belt conveyors seal the cut edges to protect the fibers inside the belt. Without sealed edges, these fibers could be released when the belt runs around the rollers, which could affect the cleanliness of the environment.
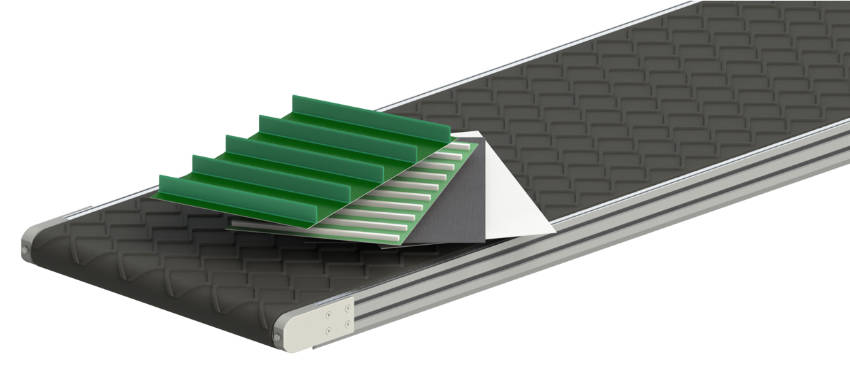
6. Does the belt have non-stick properties?
In certain applications, products may stick to the belt conveyor, whether due to sticky substances such as confectionery or adhesives from packaging processes. Use a silicone belt to ensure that the product is released cleanly and does not leave any residue on the belt.
7. Is a studded belt required?
Studded belts are often used when products need to be transported up a slope or be prevented from slipping or rolling on a gradient. They are also used to maintain the distance between products, especially when products are fed manually. The studs can be adjusted individually at different distances and heights depending on the product and application.
8. Is the belt conveyor available in stock?
Many manufacturers have only a limited selection of belts in their warehouses. They rely on suppliers to meet specific requirements. Therefore, if delivery time is critical, you should check which belt conveyors the manufacturer has in stock to find an alternative that is available quickly if necessary. At Montech, you will find a comprehensive range of belt conveyors as well as custom-tailored and flexible solutions that are perfectly suited to your needs. Thanks to our modular system and our fast delivery times, you can be sure that your production will run on time and efficiently. Our team of experts will be happy to help you find the right belt conveyor for your specific requirements.