Sustainability and Innovation in Perfect Harmony: Pioneering the Future of Recycling
In a world where environmental responsibility is no longer optional but essential, the RCO Recycling Center in Eastern Switzerland is setting a bold new standard. With its advanced wet-mechanical processing plant, the facility efficiently reclaims mineral construction waste, giving materials a second life while reducing the environmental impact of construction. At the heart of this innovation lies a breakthrough piece of engineering: the membrane chamber filter press from MSE Filterpressen GmbH – a technological marvel that redefines what’s possible when sustainability meets precision.
Engineering Excellence: The MSE Membrane Filter Press
Every year, the RCO plant processes approximately 200,000 tons of contaminated excavation and demolition material. The task is monumental – but thanks to the exceptional capabilities of the MSE membrane chamber filter press, it’s achieved with remarkable efficiency. Weighing 85 tons and stretching 16 meters in length, this powerhouse performs the critical task of sludge dewatering with unparalleled precision.
The secret to its success? Advanced membrane technology that extracts water from sludge and produces a filter cake with a remarkably high dry solids content. But this isn’t just about drying sludge – it’s about transforming waste into valuable resources. The filter cake, composed of ultra-fine particles unfit for concrete production, serves a higher purpose: pollutants are securely bound within, removed from the material cycle, and permanently neutralized.
A significant portion of this filter cake is subsequently repurposed as a raw material in cement production – safeguarding primary resources that would otherwise be extracted from the earth. The rest is used in landfill construction, playing a vital role in sealing and compartmentalizing waste. The result? A circular, environmentally-friendly process that exemplifies the potential of modern recycling technology.
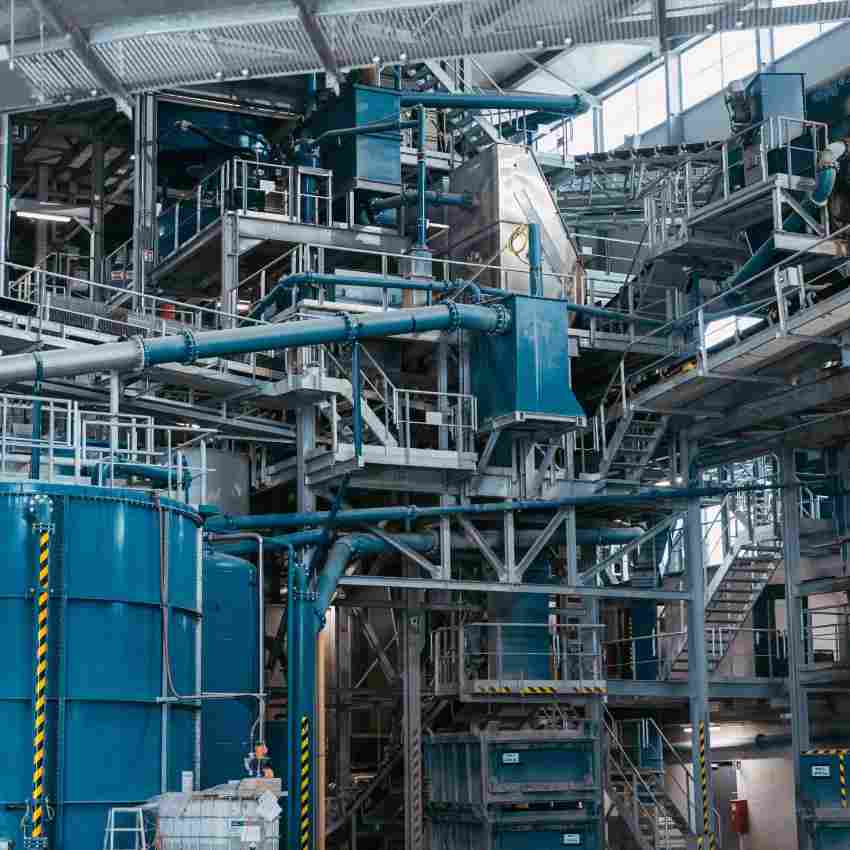
Technical Specifications – Precision Engineered for Performance:
- Dimensions: 16 m length, 4 m, width, 3 m height
- Number of Plates: 130
- Plate Size: 2 x 2 meters
- Operating Pressure: 15 bar
- Weight: 85 tons
- Capacity: approx. 12,000 L chamber volume, approx. 850 m² filter area
- Automatic Filter Cake Release Assistance (Shaker)
- Automatic Swing Drip Plate
- Automatic Filter Cloth Cleaning
- MSE 2FAST Discharge Technology
- Industrial Router for Remote Maintenance
- Membrane Break Detectors
- Real-Time Residual Moisture Measurement
This tailor-made system has been meticulously designed to integrate seamlessly into RCO’s fully automated processes. The dual-sided feed system ensures uniform sludge distribution, dramatically optimizing cycle times and boosting productivity.
The i-Plate Revolution: Smart Filtration for a Smarter Future
Innovation isn’t just about building bigger, faster machines – it’s about rethinking processes from the ground up. In collaboration with LENSER Filtration, MSE Filterpressen GmbH has introduced the groundbreaking i-Plate technology: an intelligent filtration system equipped with embedded sensors that measure filter cake moisture in real-time.
By continuously analyzing these readings, the system dynamically adjusts the dewatering process to maximize efficiency while minimizing water consumption. This adaptive capability enables RCO to handle fluctuations in material composition effortlessly, ensuring consistent quality regardless of input variability. It’s a leap into the future of process optimization, with sustainability as the guiding principle.
Sustainability at Its Core: Turning Waste into Opportunity
The membrane chamber filter press isn’t just a technological triumph – it’s a testament to the power of sustainable thinking. Throughout the entire recycling process, the facility relies on rainwater, which is repeatedly treated and reused, eliminating the need for freshwater consumption. By conserving water, reducing emissions, and recovering valuable materials, MSE Filterpressen GmbH is helping RCO redefine environmentally-conscious construction practices.
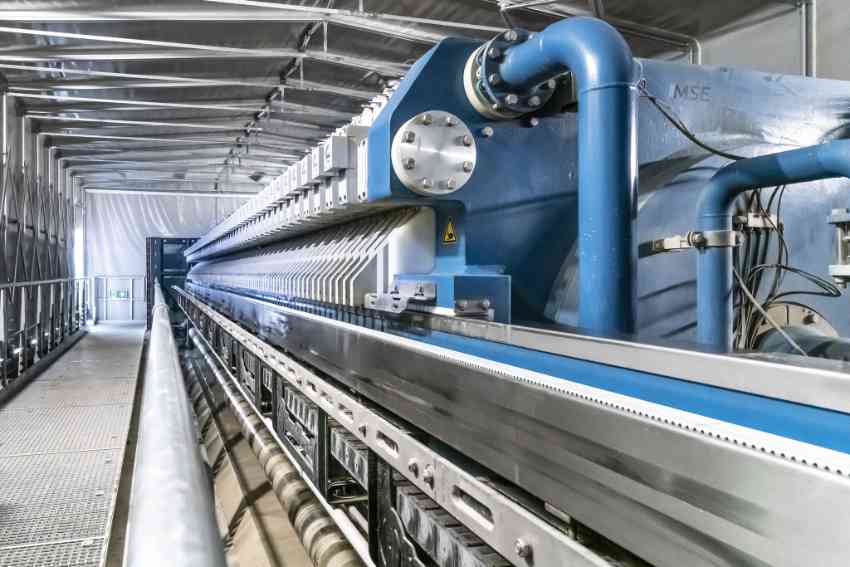
Key Sustainability Achievements:
- Water Recycling: Rainwater is captured, treated, and reused multiple times.
- Resource Preservation: Reclaimed materials are reintroduced into the production cycle.
- Emission Reduction: Avoiding primary material extraction significantly cuts CO₂ emissions.
The filter cake, once an unwanted byproduct of sludge processing, now serves as a valuable raw material in cement production and landfill construction. Contaminants are safely neutralized during the cement production process, ensuring that the recycling cycle remains uncontaminated and environmentally safe.
Precision Under Pressure: A Logistical Masterstroke
Engineering innovation often goes hand-in-hand with logistical challenges – and the installation of the MSE filter press was no exception. Transporting an 85-ton machine is one thing; precisely positioning it six and a half meters above ground is another. Suspended from two colossal mobile cranes, the press was delicately maneuvered into its designated location with millimeter-perfect accuracy – a striking display of collaboration, planning, and engineering prowess.
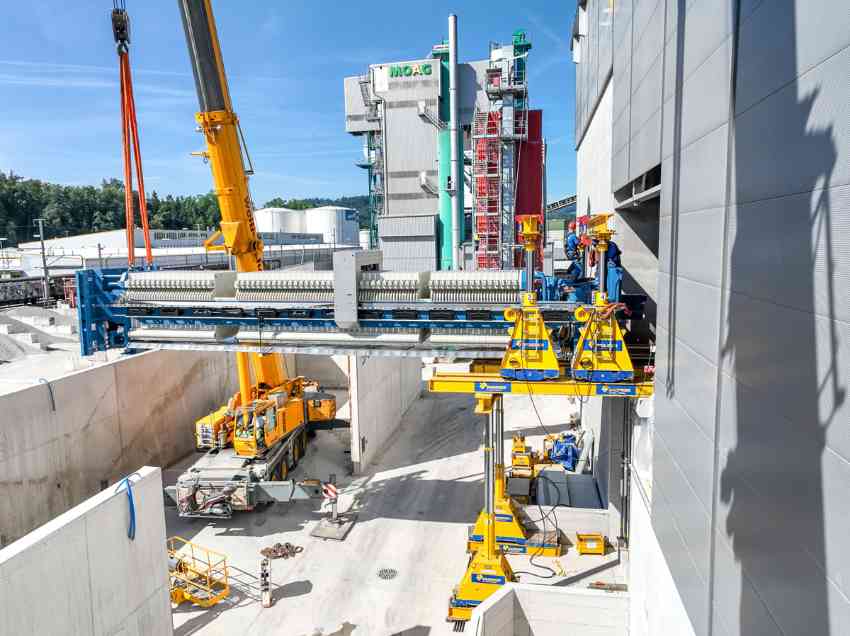
Beyond Innovation: A Vision for a Greener Tomorrow
The success of this project is the result of a dynamic partnership between RCO, Frei Fördertechnik AG, LENSER Filtration GmbH, and MSE Filterpressen GmbH. It proves what can be achieved when expertise, ingenuity, and a shared commitment to sustainability converge. The advanced filter press technology at RCO demonstrates that economic efficiency and environmental stewardship are not mutually exclusive, but rather two sides of the same coin.
MSE Filterpressen GmbH is honoured to have contributed to this pioneering facility – a beacon for the future of recycling in the construction industry. As we look ahead, our mission remains clear: to provide cutting-edge solutions that close material cycles, reduce environmental footprints, and inspire industries to build more responsibly.
Curious to learn more about our innovative technologies?
Visit our website or subscribe to our Techletter for exclusive insights into groundbreaking filtration solutions.
MSE Filterpressen GmbH – Engineering Innovation for a Sustainable Tomorrow.