Hug Engineering is a leading provider of exhaust gas aftertreatment solutions for marine, power generation, rail, and industrial applications. With more than 40 years of expertise, the company specializes in designing, manufacturing, and servicing advanced emission control systems that ensure compliance with the strictest environmental regulations. Hug Engineering’s goal is to help industries reduce their environmental footprint while maintaining operational efficiency and reliability.
What are the main areas of activity of the company?
Our core expertise lies in engineering and delivering high-performance Selective Catalytic Reduction (SCR) and Diesel Particulate Filter (DPF) systems. We serve industries that require robust, reliable, and regulatory-compliant emission control solutions, including:
- Marine – Enabling de-fossilization while guaranteeing compliance to the most stringent emission limits for yachts, commercial vessels, and offshore applications.
- Mission Critical – Reducing emissions from stationary engines in critical infrastructure such as data centers, hospitals and utilities.
- Power Generation – Providing emission reduction solutions for engines in energy production, including backup generators, grid stabilization units, and renewable hybrid systems.
- Rail – Helping locomotive operators meet stringent emission standards while improving fuel efficiency.
What’s the news about new products/services?
We continuously refine our technologies to meet evolving regulatory requirements and customer demands. Recently, we’ve been enhancing our SCR and DPF systems with smart monitoring and predictive maintenance capabilities, integrating digital solutions to maximize uptime and efficiency.
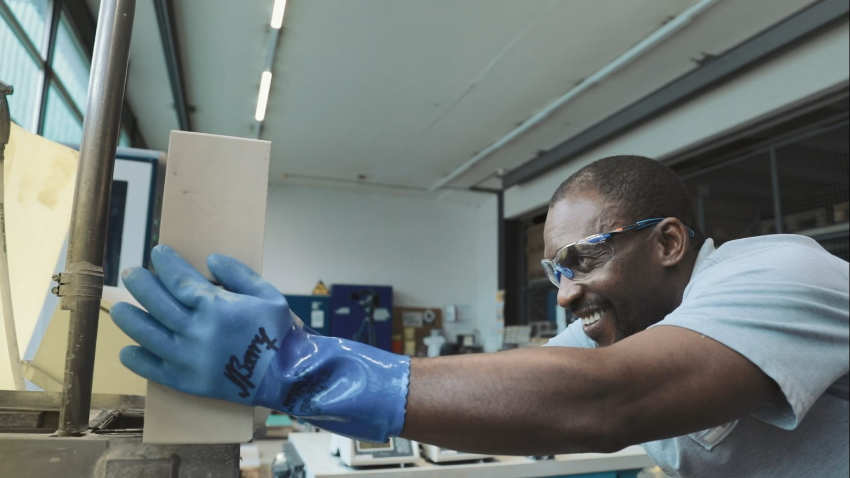
The smart integration of functions is a very interesting area of activity. By adding sound abatement capabilities to the urea mixing section, the overall exhaust system becomes more compact while maintaining an advantageous back pressure level.
What are the ranges of products/services?
Hug Engineering is a full range exhaust gas aftertreatment solutions provider. A true one stop shop. We develop, design, manufacture, commission and service highly customized aftertreatment systems including:
- Ceramics – The core of all of our aftertreatment systems. No matter if DPF, SCR or a combined solution.
- Catalysts – Tailor made catalytic coatings to match any functional demand.
- Stealwork – Maximum of functionality in the smallest, yet durable and robust housing.
- Apparatus – Certified dosing and regeneration systems, meeting the industry’s needs in a competitive heavy duty environment.
- Controls – Extremely versatile software solutions to make the operator’s life as easy as possible
- Service & Maintenance – From installation support to periodic inspections and spare parts supply, ensuring long-term reliability and performance.
What is the state of the market where you are currently active?
Depending on the field of application, market drivers can vary significantly. In the work vessel segment, for example, drivers include voluntary environmental notations aimed at ensuring a fully green supply chain—an important factor for offshore wind park investors. In contrast, the data center market prioritizes speed, ease of installation, and above all, product availability.
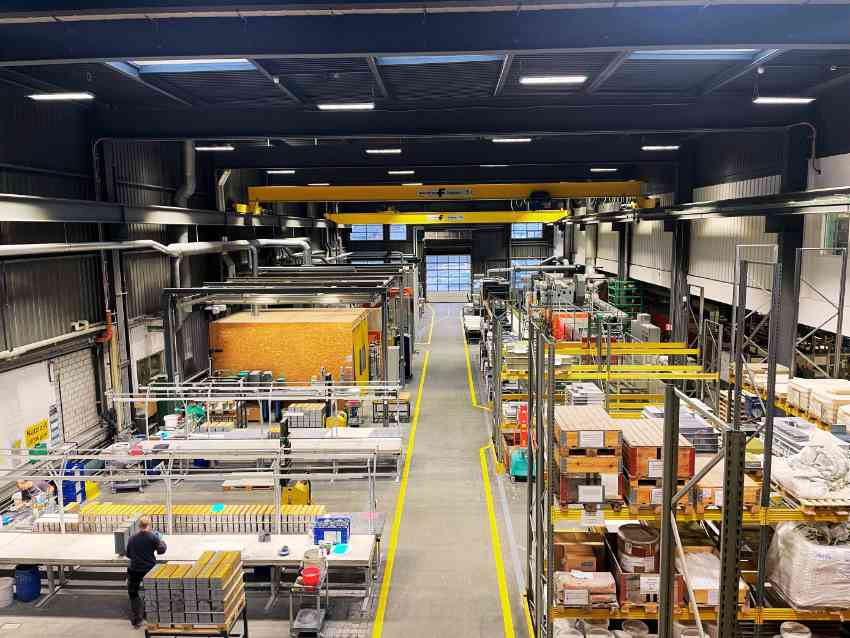
In general, it’s safe to say that the share of large engines equipped with exhaust aftertreatment systems is growing rapidly. Future fuels and increasingly stringent emission requirements add further complexity when it comes to delivering the optimal solution. At Hug Engineering, we see this as a significant opportunity.
What can you tell us about market trends?
Key trends shaping the industry include:
- Stricter Regulations – Governments worldwide continue to tighten emissions standards, making compliance a top priority.
- Voluntary environmental labels – Being green has become an advantage in many markets, leading to increasing demands on emission reduction and flexibility.
- Decarbonization Efforts – The transition to alternative fuels and hybrid power solutions is pushing manufacturers to integrate flexible emission control systems.
- Digitalization & Smart Monitoring – Predictive maintenance and real-time emissions monitoring are becoming industry standards, improving operational efficiency.
- Lifecycle Sustainability – Companies are focusing on long-term environmental impact, leading to demand for more durable, efficient, and serviceable aftertreatment solutions.
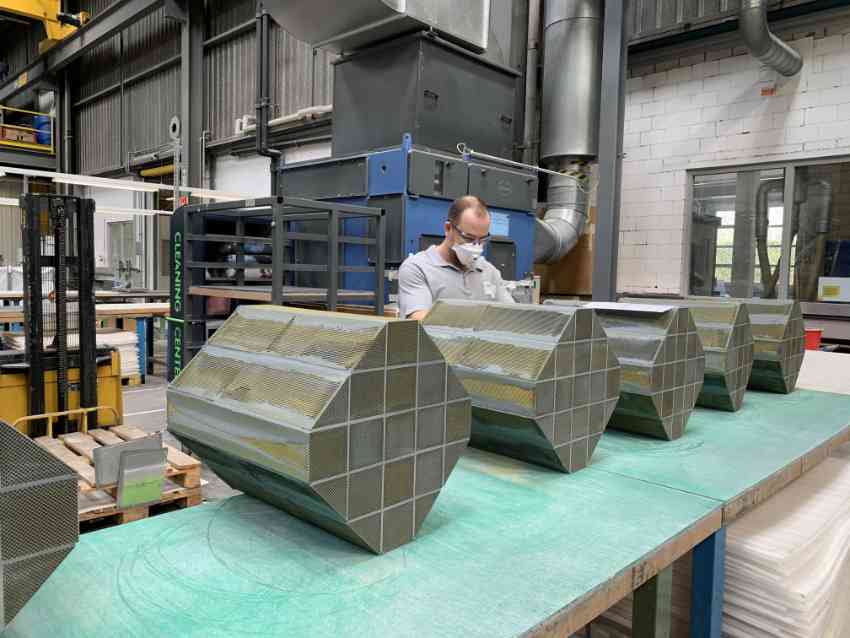
What are the most innovative products/services marketed?
The world’s first-ever medium-speed diesel engine certified under the stringent Euro Stage V emission standard is equipped with a Hug Engineering aftertreatment solution. Building on this success, we are now developing the next-generation work vessel—capable of operating with fuel flexibility, including methanol, while reducing emissions even further to meet Euro Stage VI NOx levels.
With our digital solution, HugConnect, we offer attractive long-term service contracts that provide our customers with maximum uptime, as well as operational and financial planning security. Our latest SCR systems feature advanced urea dosing and optimized catalyst configurations, delivering higher NOx reduction efficiencies while minimizing ammonia slip. Additionally, our intelligent monitoring solutions provide real-time data analytics, allowing operators to proactively manage emissions and optimize performance. These innovations ensure that customers not only meet regulations but also improve fuel economy and operational reliability.