In today’s rapidly evolving advanced composites industry, flexibility has become a critical asset for delivering value and sustaining innovation. At Addyx, we define flexibility as our capacity to actively listen, quickly adapt, and seamlessly tailor our technologies and processes to meet the precise needs of each client, regardless of the sector or application complexity. Flexibility is not merely a feature of our service – it is an integral part of our DNA and a strategic pillar in our mission to empower our clients with high-performance, cost-effective composite solutions.
Flexibility Through Proprietary Technology
At the heart of our approach are two proprietary mandrel technologies: WSM-170 and the Carbon Exoskeleton. These patented, water-soluble expanding mandrels allow the production of hollow, high-performance components with complex geometries. The WSM-170 offers high rigidity at room temperature, making it ideal for male lamination on intricate parts. Once polymerization is complete, the mandrel dissolves in water, eliminating the need for solvents and reducing waste and cost.
Building on that, the Carbon Exoskeleton incorporates internal, topologically optimized ribs to create a structural skeleton that reinforces the final part. This design enables lightweight yet mechanically robust components. Its ribbed structure distributes loads efficiently while minimizing material usage. The mandrel’s architecture allows for compacting forces during lamination, eliminating air pockets and ensuring optimal resin distribution. The result is a monolithic component that outperforms traditional sandwich structures in reliability, thermal stability, and manufacturing simplicity.
Agility Through Vertical Integration
Addyx combines proprietary technology with in-house capabilities – including additive manufacturing, rotational molding, and design/testing services. This integration allows rapid iteration: we can prototype, modify, and validate in real time. Our R&D-driven workflow reduces development cycles and empowers clients to reach the market faster, with better-aligned products.
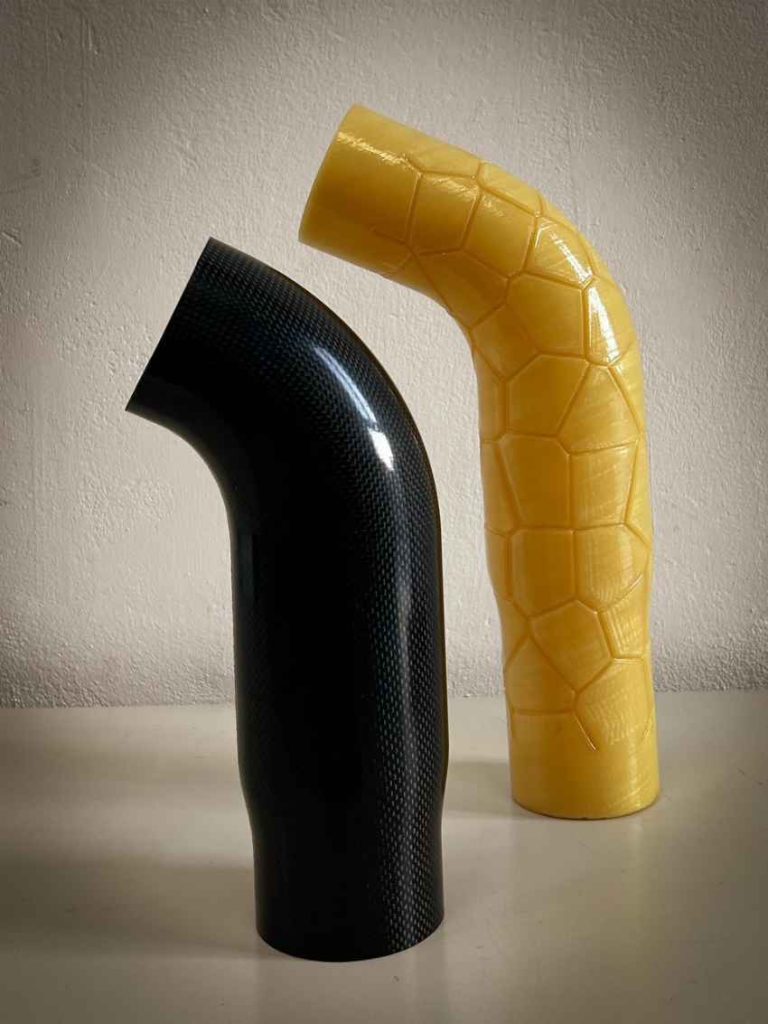
Efficiency Without Compromise
Flexibility at Addyx is built into every phase of production. Our hybrid manufacturing model is cost-efficient and performance-driven. We use 3D printing for prototyping and short runs, rotational molding for medium series, and are expanding toward injection molding for high volumes. This modular approach ensures scalability and cost control without compromising on performance or precision.
Cross-Sector Adaptability
Our technologies serve demanding sectors such as aerospace, motorsport, automotive, and defense – each with unique challenges. The same core technologies can be adapted to meet strict weight-performance ratios, temperature tolerances, or regulatory standards. The Carbon Exoskeleton, in particular, is tailored through FEM-based topological optimization to match each application’s structural requirements – ensuring stiffness and lightness, while enabling design freedom.
One Core Technology, Infinite Applications
Our WSM-170 and Carbon Exoskeleton platforms are not static solutions – they are highly configurable systems. From wall thickness to internal rib geometry, every detail can be adjusted to meet specific project requirements. This level of customization allows a single mandrel technology to serve entirely different performance objectives: from aerospace fluid ducts to impact-resistant automotive parts. It’s the kind of scalable flexibility that adds long-term value across industries.
Design Freedom Meets Manufacturing Reality
One of the most tangible forms of flexibility we offer is design freedom. Our technologies make it possible to manufacture complex hollow shapes with variable cross-sections, closed contours, or multi-branch layouts – geometries that traditional tooling or bladder systems can’t handle. More than just enabling shapes, we help engineers bring ambitious ideas to life without being limited by manufacturing constraints. We align digital design with physical reality.
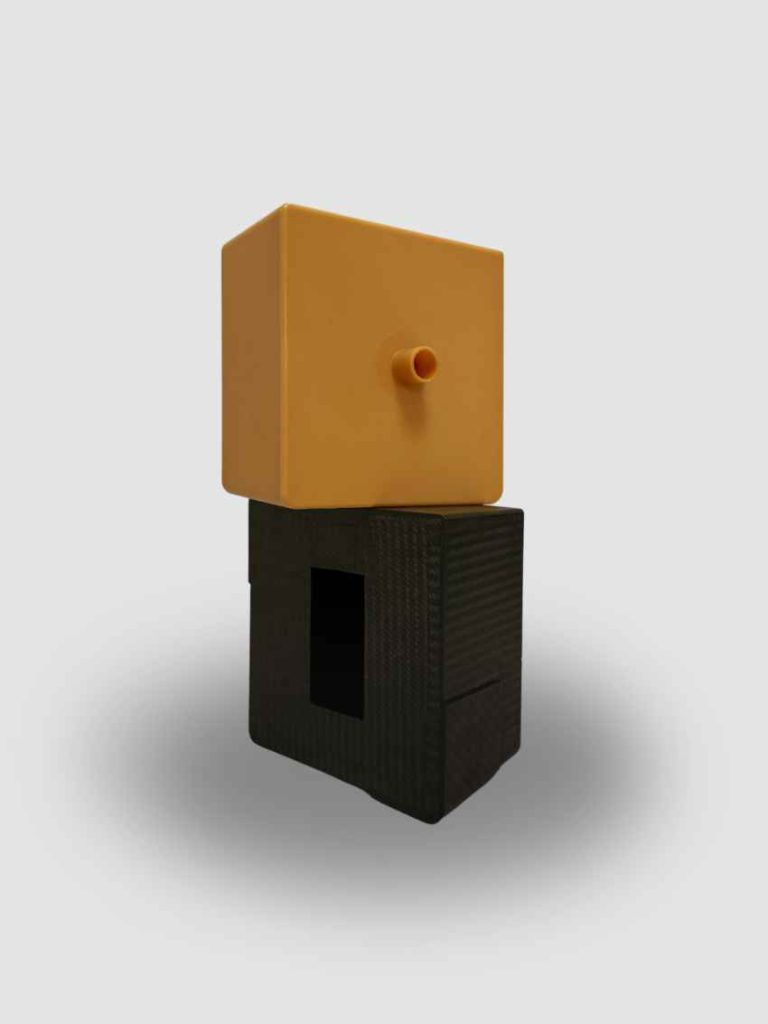
Flexibility as a Partner, Not Just a Supplier
Being flexible means more than adapting processes – it means adapting relationships. At Addyx, we act as a development partner, working closely with clients from early feasibility to final production. Our agile team structure allows us to accommodate design changes, accelerate iterations, and align to shifting priorities. Whether it’s certification, functional validation, or integration into existing assemblies, we stay responsive. This proximity and responsiveness are core to our way of working.
Deep Collaboration as a Driver of Innovation
We believe innovation happens when listening meets execution. Each new project starts with a comprehensive dialogue: understanding the functional constraints, performance targets, regulatory standards, and production environment of our clients. From there, we co-develop the solution, involving clients at every critical step – from design to production, prototyping to validation. This open and iterative collaboration ensures our solutions are not just flexible, but truly client-driven.
Technology as an Enabler of Flexibility
Our design process leverages advanced CAD/CAM tools, structural simulation, and automated quality control. These technologies integrate seamlessly with real-world feedback, enabling us to close the loop between concept and performance. For the Carbon Exoskeleton, we’re also pioneering automated lamination of the internal ribs through AFP in partnership with COMEC Innovative Srl. This step will further reduce production time, increase precision, and enhance repeatability.
Commitment to Sustainability
On the sustainability front, we are developing a closed-loop system to recover and reuse the water used in mandrel dissolution – lowering environmental impact and increasing process circularity.
Our water-soluble polymer is non-hazardous and biocompatible, ensuring a safe and environmentally responsible process.
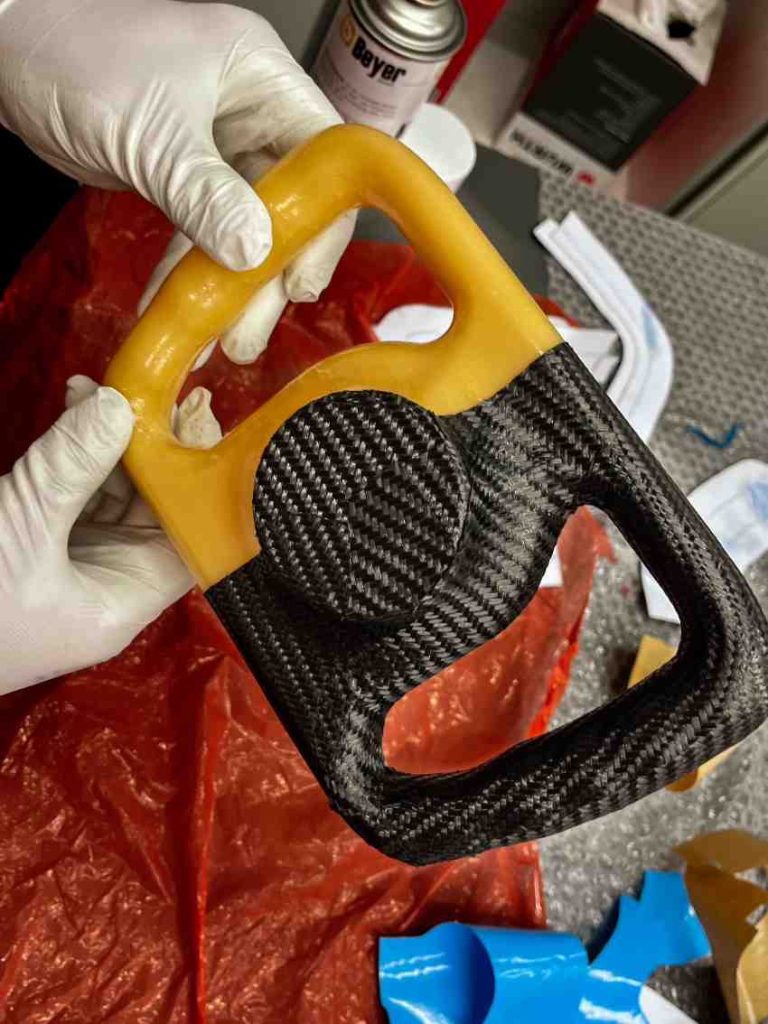
Flexibility as a Strategic Compass
Looking ahead, flexibility will remain our guiding principle. We aim to expand our licensing model, deepen our aeronatutics and space collaborations, and continue developing advanced materials and automated production processes. With a client-centric mindset and a commitment to constant innovation, Addyx is shaping the future of hollow composite manufacturing.
In conclusion, flexibility at Addyx is more than a process – it’s a philosophy. It empowers us to respond to technical complexity with speed and creativity, to reduce environmental impact without sacrificing performance, and to help our partners succeed in a rapidly changing world.