Fortis3D is a Canadian start-up focused on bringing innovative 3DP materials to the market. With a background in polymer chemistry and engineering, the company develops their own proprietary materials that push the limits of what 3DP materials can do. Fortis3D’s production facility follows Good Manufacturing Practices (GMP) and is ISO9001 certified so many of their products are FDA and EU food contact compliant.
Easy Engineering: What are the main areas of activity of the company?
Fortis3D: Currently, our main focus is on filaments, but we are also starting to look at developing pellet materials for FGF. Our products are aimed at the mid-tier segment and are printable with regular desktop printers. We are continuing to develop more products in this segment and plan to expand into both the ultra high performance segment in the near future.
E.E: What’s the news about new products?
Fortis3D: We plan to bring fiber reinforced products to market in about 6 months time. There are some very highly reinforced (30%) carbon and glass fiber materials in the market and while they might be stiffer than the unreinforced counterpart, they aren’t necessarily much stronger. Highly reinforced materials work great in injection molding because there’s a lot of pressure to pack the material into the mold. In 3D printing, the material is flowing through a small nozzle in most cases and the fibers can cause under-extrusion which leads to more void in the part making it weaker. We are optimizing the amount of carbon and glass fiber that will give the best balance of strength, stiffness and toughness so our customer can print truly robust and functional parts.
E.E: What are the ranges of products?
Fortis3D: We currently have two product lines with a third one coming soon. Starting with our Essentials product line, we have a variety of innovative PLA based products. These are not just easy to print but also showcases our ability to modify materials. We have a super toughened PLA we call BioDuro PLA and a metallic version of that which features iridescent pigments that give a brilliant surface finish. Pilates PLA is our flexible PLA that’s like TPU but doesn’t have any stringing issues and is a bit stiffer so it’s easier to print. Last product in that line up is our Lignum PLA which has 25% real wood fibers which gives it not only a nice wood like finish but also a nice wood smell during and after printing.
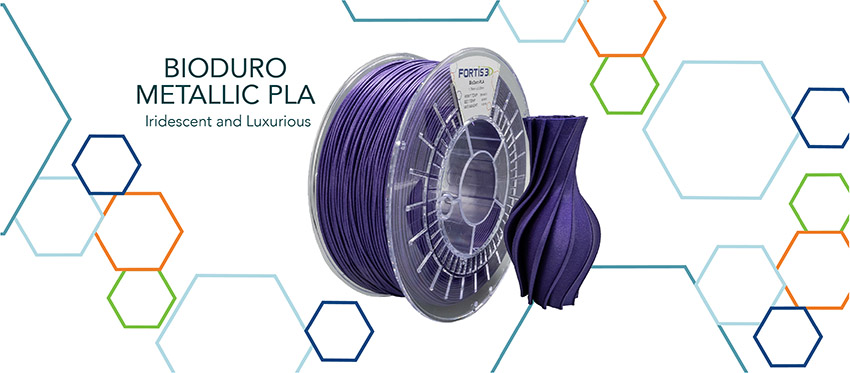
For our Advanced line, we have a trio of engineering grade filaments. Our Ignis PLA is a high heat resistance material that doesn’t require any annealing to reach an HDT of around 95-100°C but it can be further annealed for even higher heat resistance. SnapPrint PP is our take on a low warp polypropylene (PP) filament that can be printed even on open air printers with a thin layer of adhesive and a small brim. Last but not least, our SnapPrint PA is a low-warp and moisture resistant nylon co-polymer that can be easily printed on an open air printer with a thin layer of adhesive and remains quite stiff even after conditioning compared to most other unfilled nylon filaments on the market.
Our last product line is the Industrial line which we are working on products for. These are designed to be as close to the traditional injection molding materials as possible and are meant for serial production of functional parts.
E.E: At what stage is the market where you are currently active?
Fortis3D: I would say that the filament market is maturing. There’s a good variety of traditional injection molding materials in the market but we see a gap in the specialty materials (i.e ESD, FR) and materials tailored for 3DP.
E.E: What can you tell us about market trends?
Fortis3D: The market is trending towards more sustainable materials. PLA was a great start but the only way it can actually biodegrade in a reasonable amount of time is in an industrial compost facility. There are starting to be more PHA/PHB filaments on the market but the cost and availability of these materials are limiting factors. Filaments made with recycled materials are getting more attention as well but there are limited color options and the material properties will vary more batch to batch. Nonetheless, the industry is moving to be greener and participate in the circular economy so expect to see more bio-based and recycled materials in the coming year.
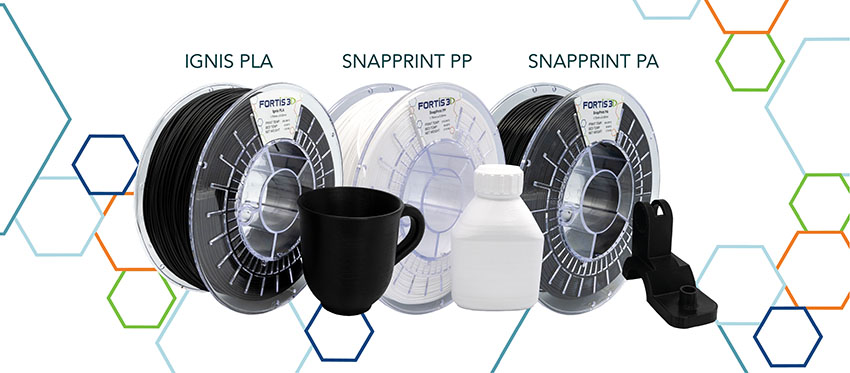
E.E: What are the most innovative products marketed?
Fortis3D: On the fused deposition side of the market, pellet 3D printing is potentially the next big thing. Generally speaking, the price of plastic pellets is lower than filaments as it doesn’t require that extra step of turning those pellets into filaments. You can also combine multiple toolheads to post process the print and machine it to the desired dimensions with a smooth surface. There are a few major hurdles though. Firstly, pellet extruders right now are very large and typically fitted on large expensive printers so until they get small and cost effective enough, we won’t be seeing wide adoption as we’ve seen with FDM printers. The second hurdle is the size of the pellets. Typical plastic pellets might be too big for any pellet extruder small enough to mount on a desktop machine. Lastly, there simply aren’t many materials tailored for pellet extruders. For it to perform well, it must have certain melt and crystallization properties so parts can be printed well and without warpage.
E.E: What estimations do you have for the rest of 2022?
Fortis3D: With the world economy on the brink of recession, filament sales are almost definitely going to slow down a bit at least in the consumer space. The low-cost market most likely won’t be affected too much and the high-performance engineering materials won’t be affected as companies are unlikely to reduce their budgets over the short term. The mid-tier market will most likely be affected the most because it will be harder to justify the premium over the low-cost materials for consumers and SMBs.