MaCh3D is a smart material testing platform expressly designed for those who produce finished products starting from raw materials. Continuous control of mechanical properties and correlation to production parameters is a fundamental aspect in manufacturing. MaCh3D allows to measure the mechanical quality of produced goods by means of (i) a miniaturized tensile testing machine, (ii) a simplified test procedure aimed at speeding up tests and reduce operator errors and (iii) and a cloud for remote machine control, storage and analysis of test data and time-history of production results. MaCh3D can be interfaced to exchange data between production machines to correlate mechanical properties to manufacturing parameters enabling to real-time quality control of industrial productions. The company’s hardware enables prompt verification of both raw material or transformed material batches directly in production departments, without the need of dedicated rooms nor particular materials testing skills, thus enabling a cost-effective material quality check.
Interview with Ing. Lorenzo Bergonzi, PhD, CTO at MaCh3D.
Easy Engineering: What are the main areas of activity of the company?
Lorenzo Bergonzi: MaCh3D is mainly active in the material characterization and product development area. The reference sector of MaCh3D is Material Testing, whose value on a global scale is US$ 529.2 million in 2020. MaCh3D can be extremely useful for all those SMEs which can’t afford the costs of traditional material characterization systems but also for the bigger companies, where material characterization is an activity already integrated in the productive process, MaCh3D can be used to cut down the number of tests to be done by the laboratory. Moreover, MaCh3D can be used to monitor production parameters continuously directly in production, thanks to its reduced dimensions and easiness of use. MaCh3D potentially addresses all sectors of the manufacturing supply chain, macro-category that in Italy 99% is formed by small and medium enterprises. In the first period, for market introduction we will focus on two reference markets selected for their strategic importance with respect to the innovations brought by our product: (a) the Plastic market and (b) the Additive Manufacturing market. In the plastic market, the leading segment is production through injection molding, a market worth 350 B $ in the world with a CAGR of 6% per year. About 75% of turnover comes from Europe, a region that has 62,200 companies (11,000 in Italy). The Additive Manufacturing market is a rapidly growing market: in 2017 it reached a value of 6.1 B $ with CAGR of 17.1%.
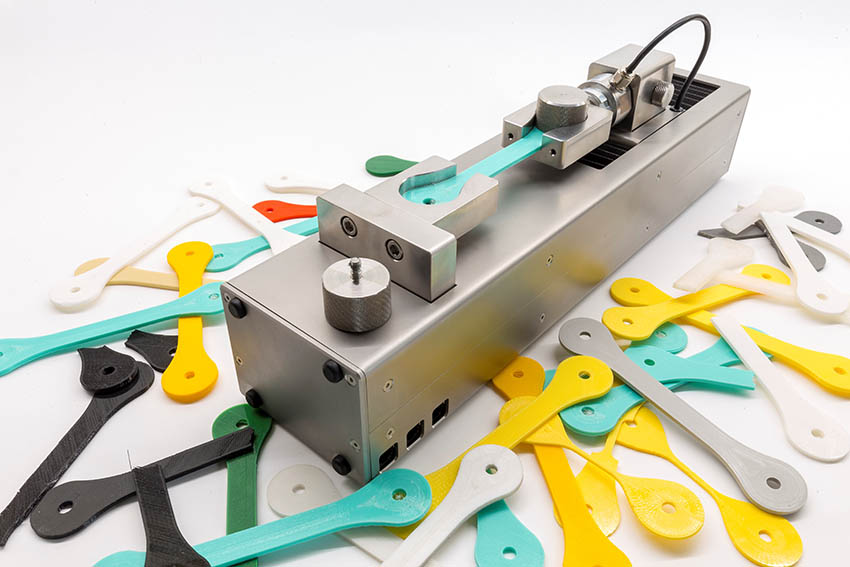
E.E: What’s the news about new products?
L.B: At the end of 2021 we obtained the CE certification, allowing us to start commercializing our solutions in Europe. During 2022 we are strongly focused in developing the cloud platform that will allow to use MaCh3D machines wirelessly with different devices such as tablets and computers (nowadays you can use MaCh3D connected to a PC through USB cable).
E.E: What are the ranges of products?
L.B: Today MaCh3D produces one single model of tensile testing machine with a maximum exercisable force of 5000 N (500 kgf). On request, we can modify it to have different crosshead travels and testing speeds. We do develop interchangeable fixtures to perform different kind of tests, such as three and four points bending, testing of thin films and rubbers, shear tests, compression tests and more. Depending on the project application, we can design specific fixtures according to customers’ requests.
E.E: At what stage is the market where you are currently active?
L.B: The reference sector of MaCh3D is Material Testing, a quite consolidated market, whose value, on a global scale in 2017, was around 700 M$. In this market there are different players: (i) large companies with a worldwide scale, operating with a wide and diversified catalog of products (test machines and accessories), characterized by high quality and high costs, they occupy a prominent position in the market. (ii) medium-sized companies, active on medium-scale territories (national or geographical area) often specialized on needs of specific sectors (construction, packaging, textiles, …). (iii) small companies operating on national or regional basis, specialized in design and construction of customized systems. Some of the main players are Instron, MTS, Tinius-Olsen and Zwick-Roell.
E.E: What can you tell us about market trends?
L.B: The global Material Testing market is expected to reach US$ 676 million by the end of 2026, growing at a CAGR of 3.5% during 2021-2026. The diffusion of new and decentralized production methods, such as additive manufacturing, require a different approach to material testing. Whilst in the past there were few big companies which produced semi-finished products, nowadays we have a lot of small companies that, starting from raw materials, obtain the final object in one single passage (additive manufacturing and injection molding). They are also responsible for the safety and the quality of their final products: hence the need to have a capillary distributed material testing capability to enable all those SMEs to assess the quality of their products, which is hard to develop due to high costs and complexity of traditional material testing systems.
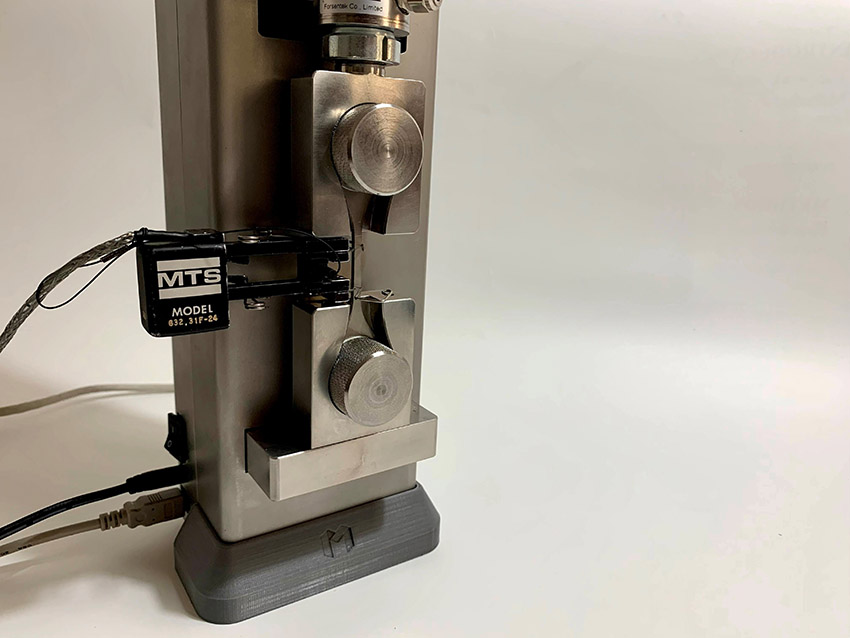
E.E: What are the most innovative products marketed?
L.B: MaCh3D is a miniaturized universal testing machine that enables material certification directly in production, without needs of dedicated laboratories or specific skills in material testing. The hardware is a custom designed machine roughly 400mm long, capable of exerting a 5000 N force (500 kg). During the test, force applied to the specimen is recorded, as well as specimen elongation. The machine can be connected to existing sensors and add-ons, such as external extensometers, strain gauges and thermocouples. On the same machine, different kind of tests can be performed simply changing specimen fixtures. An innovative tensile test specimen has been developed: the shape of the material sample and grips allows to dramatically simplify test set-up operations, the most time consuming and critical phase from the results correctness point of view.
E.E: What estimations do you have for 2022?
L.B: For 2022 we plan to start selling our solutions, starting from the Italian market, and possibly spreading through Europe.