Stanova is a young company from Berlin, specialized in punching machines for the processing of plastics. Their machines are used for daily life-products: roller blinds in the kitchen, price labeling in shops, lighting, medical products and even parts of rotor blades in wind farms.
They entered the market to show that punching, cutting and sawing of plastic profiles can be done easier, faster and more sustainable than before.
Easy Engineering: What are the main areas of activity of the company?
STANOVA: We develop, design and mount machines for the processing of plastics. If the customer needs a prove for the quality of the produced workpiece, we offer punching tests on our test stand. This helps the customer to explore his or her material, as well as the punching force and cutting speed required for optimal results.
E.E: What’s the news for 2021 about new products?
STANOVA: The 2021´generation of Stanova machines is able to drill plastic profiles. This gives us high precision openings with no burr and lint – especially in the medical technology this is highly important. So this is a new processing additionally to the previous cutting, sawing and punching.
Furthermore, we have programmed a smart user interface which enables the operator to individually choose the distance between the openings as well as the kind of tool, the length of the pieces etc. The operator can do all these settings in the office while drinking a cup of coffee instead of standing in the loud factory hall. By the way, I think it is the first user interface fully gendered. We have seen so many female operators in the factories, so why should they not be addressed equally to the male operators? Sounds logic, but the reality in the mechanical engineering is different.
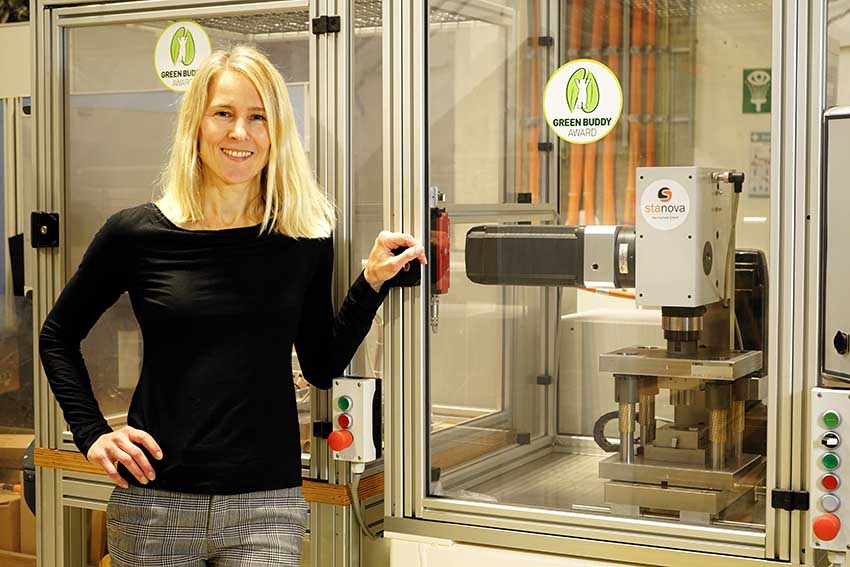
E.E: What are the ranges of products?
STANOVA: Our systems work according to the building block principle: It’s not the finished, unchangeable product that we give to the customer, but the individual assembly and reconstruction, the feel of the parts and the sustainability of the material that excites them.
Modularity is realized via mechanical click systems, rollers for moving the system and easily exchangeable tool holders.
Individuality: a die carriage adapts to the speed of the material coming out of the extruder and returns to the starting position. The principle of the flying saw enables us to achieve high dimensional accuracy of the die-cut products.
Usability: Despite its complexity, the machine is lean and easy to operate. All control elements – from strip feed to engagement protection – are easy to reach.
Sustainability: All systems are equipped with servo motors and low-wear components. The braking energy of a drive is not converted into heat, as was previously the case, but can be used to accelerate another drive. This makes the machine durable and energy-efficient.
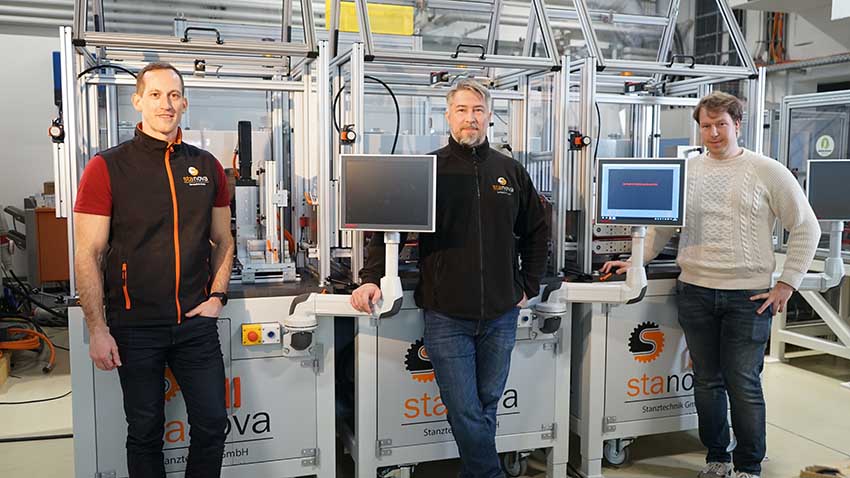
E.E: At what stage is the market where you are currently active?
STANOVA: The plastics industry is highly contested. A company can only survive if it continuously offers innovative products with higher production speed, better quality and lower costs. But this is what spurs an on.
E.E: What can you tell us about market trends?
STANOVA: Circular economy and sustainability: We cannot continue to produce in a linear way where products end up in the landfill. We have to standardize products and compounding so that they can be easily classified for reusage and recycling. At present, the prices for raw material are continuously climbing while the profits decrease.
Also, especially the plastics industry with its enormous hunger for power must use it from renewable sources.
E.E: What are the most innovative products marketed?
STANOVA: Of course, our universal Processing machine FlexSpee. There is no such machine on the market at present. Customers very often prefer the standard machines which they know including its weaknesses.
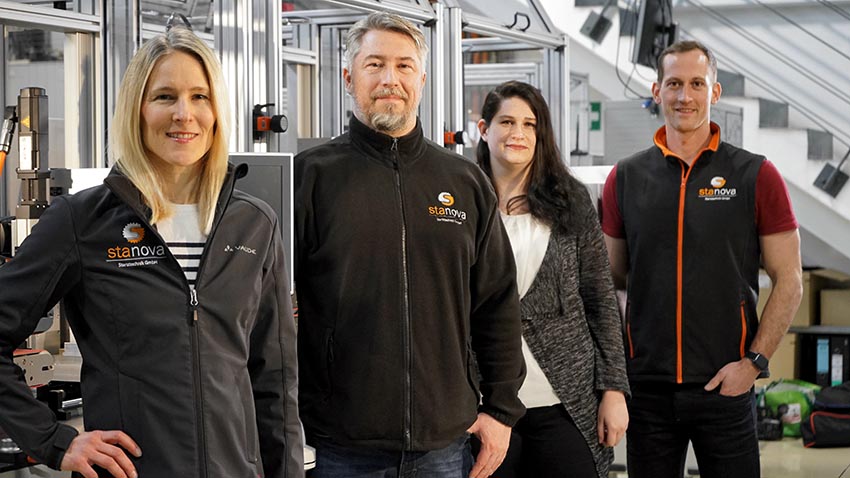
E.E: What estimations do you have for 2021?
STANOVA: First, we have to compensate the declining demand from the automotive by turning to the medical.
Secondly, if we do not manage to reduce the primary resources of our products there will not be enough raw material left for all and companies will have to close their doors.