VauQuadrat (literally “vee squared” v²) was founded in 2009. Continuously, application knowhow around “Penetration Depth Induction” was built up. Since 2015, their inductors were designed and produced, while otherwise being a sales and service company. In 2019, VauQuadrat started to manufacture also the penetration depth induction units in-house.
Nowadays, there are 23 people working in the company situated in Offenburg / Germany, at the edge of the Black Forest.
Interview with Thomas Vauderwange, Managing Director at VauQuadrat.
Easy Engineering: What are the main areas of activity of the company?
Thomas Vauderwange: Since the beginning, the application of “Penetration Depth Induction” defined the core activities. This started in the field of demounting, where we destroy rust thermally without glowing, or dissolve thread glue (like Loctite) extremely fast and without any collateral damage – courtesy of our penetration depth!
Delaminating and paint removal with penetration depth induction, even on work pieces like high voltage towers, are a super efficient way of getting the job done without the need for an “Easter Bunny Suit” or hearing protectors.
Then started the field of welding-associated activities. First, it was only heat straightening – in many cases without visible glowing, on stainless steel with only a minimum of annealing colors. We call that “minimum invasive thermal straightening”.
This was complemented by preheating applications for welding. But so much different from what is normally required!! With penetration depth induction, “preheating isn’t a pain anymore”. Can be automated, can happen directly in-line with the welding arc or laser. The concept of “Energy Displacement in Welding” is a real winner. As crazy as it sounds: You preheat (much) more than you have to – and in return you take energy out of your welding process. Which, in the end, leads to a COLDER welding. Increased welding quality, greatly reduced distortion, faster welding possible…
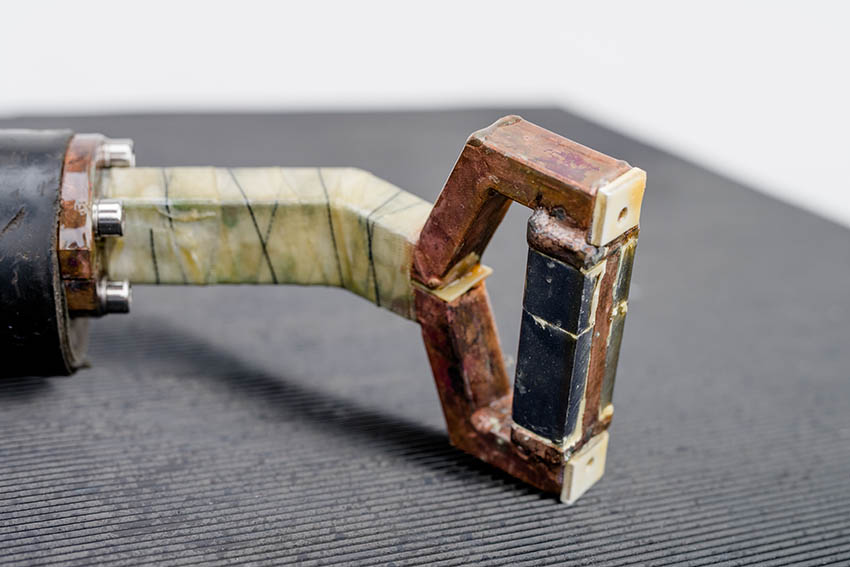
E.E: What’s the news about new products?
T.V: More or less when we did set up our own production, it was a key demand from my side to get a highly repeatable brazing process, to get rid of the risk of leaks in the refrigeration circuit. We succeeded 100% there – not a single refrigeration leak in the first four years. That tells us something. Well, and to our own surprise, especially the refrigeration market has a huge demand for process reliable brazing. As our success on the recent CHILLVENTA exhibition showed.
E.E: What are the ranges of products?
T.V: V2 – For car garages and car body repair shops, but also for loosening Loctite
V3 – Medium sized unit for truck / farming / construction equipment workshops or small heat straightening applications up to 5mm
V4 – Our standard “Workhorse” for all series production in black steel, as well heat straightening, preheating, dehardening of plasma/laser cutting edges,…
V5 – Like V3, but without compressor cooling, for smaller workshops with less applications
V6 – More or less a V4 with boosted compressor system. Very nice on large automations, also for frequent use on stainless steel and aluminum
V7 – That would be a V4 as a split unit! The larger part of the unit (the water cooler) can be placed 25m (or 50m) away from the inverter. Absolute silence at the working place.
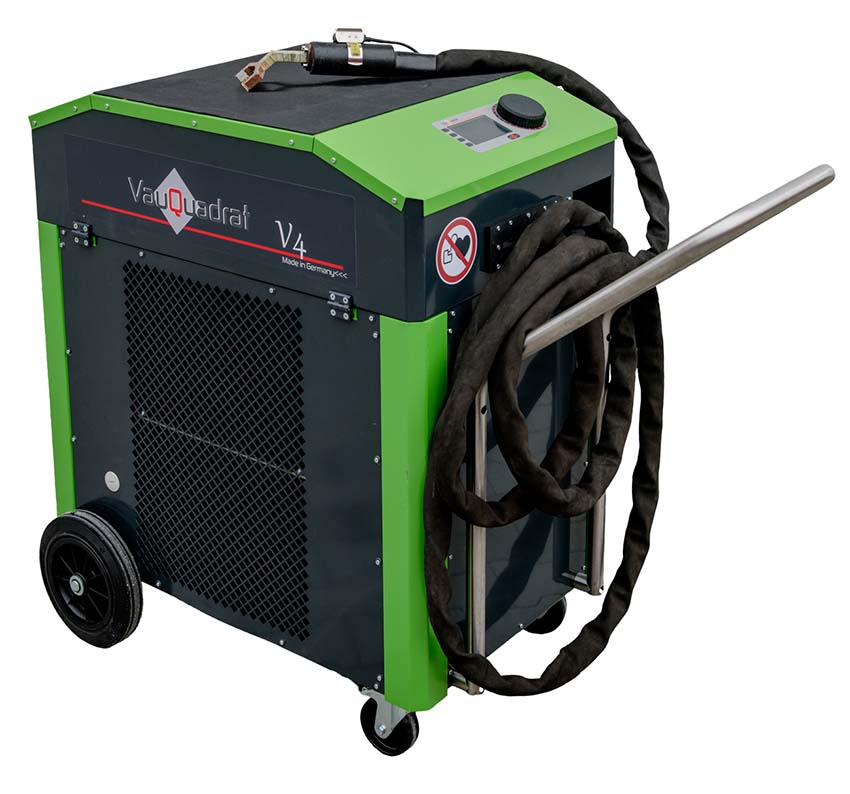
E.E: At what stage is the market where you are currently active?
T.V: Generally speaking, we are actively selling in Germany, Austria and Switzerland – but our units already found their way e.g. to Brazil, the U.S., Poland, Hungary, France, only to name a few. Whereas there is a certain awareness of the differences “Penetration Depth Induction vs Induction”, in many cases we have to fight with the fact that we have to try and explain (and show!) why we typically not just “replace the open flame”. So, one could conclude that we mainly have to deal with a First Mover situation. Or. Of course, with some Fast Followers, in case where enthusiastic users tell their colleagues in other companies…
E.E: What can you tell us about market trends?
T.V: The workpieces constantly get bigger, as the users in the steel construction business (EN 1090) get aware of the possibilities – and more important the compatibility of our technology to a highly regulated environment.
For example, when building bridges, with 50mm material strength, to weld the big beams is no easy task. And normally, the energy demand for preheating the welding process (like Under Powder Welding, or a strong, mechanized MAG welding process) is HUGE. All of a sudden, with penetration depth induction as a heat source that is mechanically coupled 5cm in front of the arc, you get ultra-efficient. And first of all, you have outstanding repeatability!
Naturally, with the workpieces getting bigger, mechanization and automation are the name of the game.
For us, the units used are exactly the same as for manual operation.
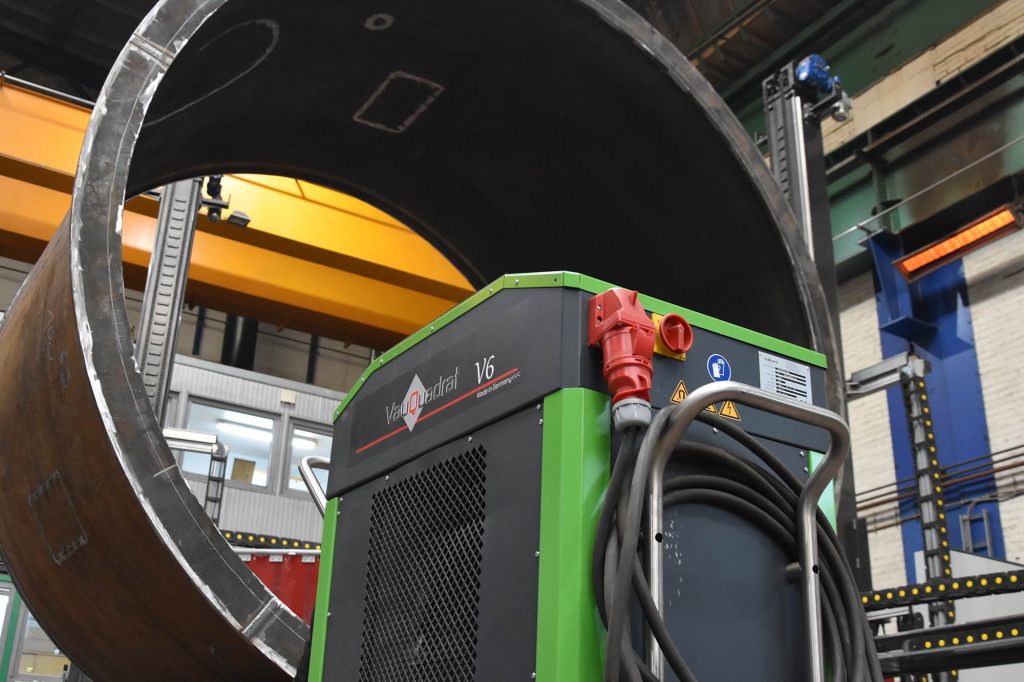
E.E: What are the most innovative products marketed?
T.V: As a derivative of our V7 split unit, we have a “Delamination Unit”. The water cooler together with a generator rest on a truck, while the inverter is in an extremely robust steel cabinet that gets craned up a high voltage tower. There, the operator uses it to remove paint. Real fast and real efficient. The qualification level of the operator is measured in centimeters. You can tell from the size of the paint patches that fall to the ground whether they know what they do or not. In the first half hour, the paint falls off in small pieces of maybe 2cm, after that you find huge chunks of 30cm and more. The clue: If there is the orange lead primer below the paint, it comes off in easily collectable chunks, rather than converting it into air pollution like it happens with conventional compressed-air-nailing machines…
E.E: What estimations do you have for the rest of 2022?
T.V: On one hand, brazing applications are more and more in demand. And with the events in the world in 2022, and the energy prices going way up, customers all of a sudden start to listen when being shown that energy cost can go down to below 10% in many cases when replacing an oxyfuel flame in the right way. Before, nobody really seemed to be interested in that, neither from a CO2 reduction, nor from an energy cost reduction point of view…