Soenen Group, established in 1946, is internationally known as producer of automatic lines and machinery for the production of PVC & alu windows. The company is also specialized in fully aluminium profile processing solutions.
Interview with Pepijn Carlier, Sales Representative at Soenen Group.
Easy Engineering: A brief description of the company and its activities.
Pepijn Carlier: For decades, the Soenen group has stood for creative solutions, great engineering and manufacturing expertise and a strong customer focus.
As partner, Soenen offers a full range of integrated products, innovation, continuity and transparency. Our know-how allows efficient, customized solutions, higher productivity and faster growth.
Thinking outside the box, that is, taking new paths to develop solutions and think beyond barriers.
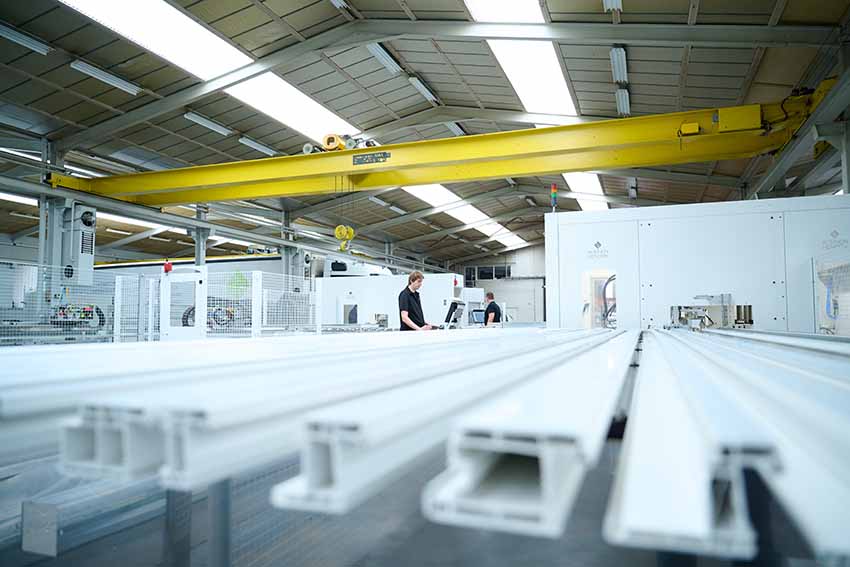
E.E: What are the main areas of activity of the company?
P.C: Soenen Europe is a one-stop-shop. All produced ‘in’ and ‘by’ Soenen. Everything for uPVC and ALU processing made by one machine manufacturer = direct contact, direct service, a one-stop-shop. We sell our machines and fully automatic lines in PVC mainly to manufacturers of windows and doors. Our fully automatic aluminium centres are bought by anyone who wants to process aluminium profiles fully automatically and without the intervention of an operator. This means feeding, milling, drilling, tapping, flow drilling, sawing, counter-profiling, stickering and then fully automatic output on a conveyor belt.
E.E: What’s the news about new products?
P.C: Our machining centres are always new as we work on a bespoke basis for our customers. We are on the eve of a number of new developments and this for both PVC and ALU.
E.E: What are the ranges of products?
P.C: We develop, manufacture and sell fully automated lines for PVC window and door products. For alu, we have fully automatic machining centres for all kinds of actions needed.
E.E: At what stage is the market where you are currently active?
P.C: Our customers are people who think ahead (sometimes 10 to 20 years) and work with us to see how they can organize production as optimally as possible and do so by means of machines, in other words: automation, automation, automation.
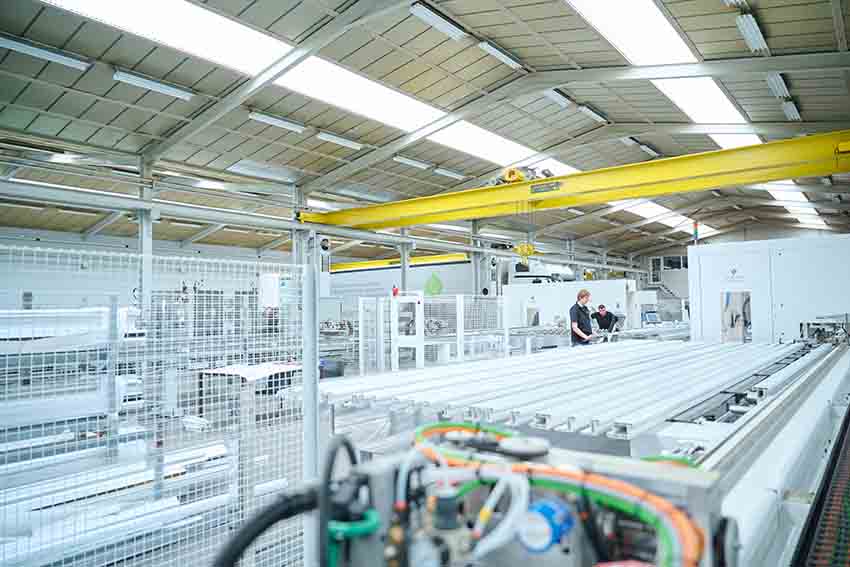
E.E: What can you tell us about market trends?
P.C: The main focus of the PVC world is to produce efficiently at the lowest possible price. Unfortunately, some evolutions stand in the way of this goal. These include increased raw material prices, expensive wages and the lack of technically trained personnel. The situation where employee A saws the profiles, then takes the profiles to employee B for milling, who then passes on the welding to employee C is therefore increasingly under pressure. Not only is this approach time-consuming, the lack of manpower is and remains a bottle neck. Moreover, technical knowledge is also disappearing from companies, as experienced workers are hard to replace.
Window manufacturers are logically constantly looking for ways to address these obstacles. In other sectors, automation is often the answer to such challenges, and this is no different in PVC window production. It is just not that simple because of the many operations required.
Driving up speed
Boosting speed happens in various ways among many manufacturers. Today, for example, there are fully automated production lines for those who want to process large volumes. Profiles are loaded at the beginning of the machine, and a complete window comes out at the end of the line. Sawing, milling, screwing and welding are done autonomously. The number of operators still required for this approach? One or max 2. They only have to ensure that the profiles arrive on time and the windows are removed. In other words, the reduction in production costs is not only due to fast production, but also to lower labour costs. And then we forget that today’s machines have a very high repeat accuracy: the variation between the pieces is virtually zero, moreover with a very low error rate. That is a lot harder to approach with human operation.
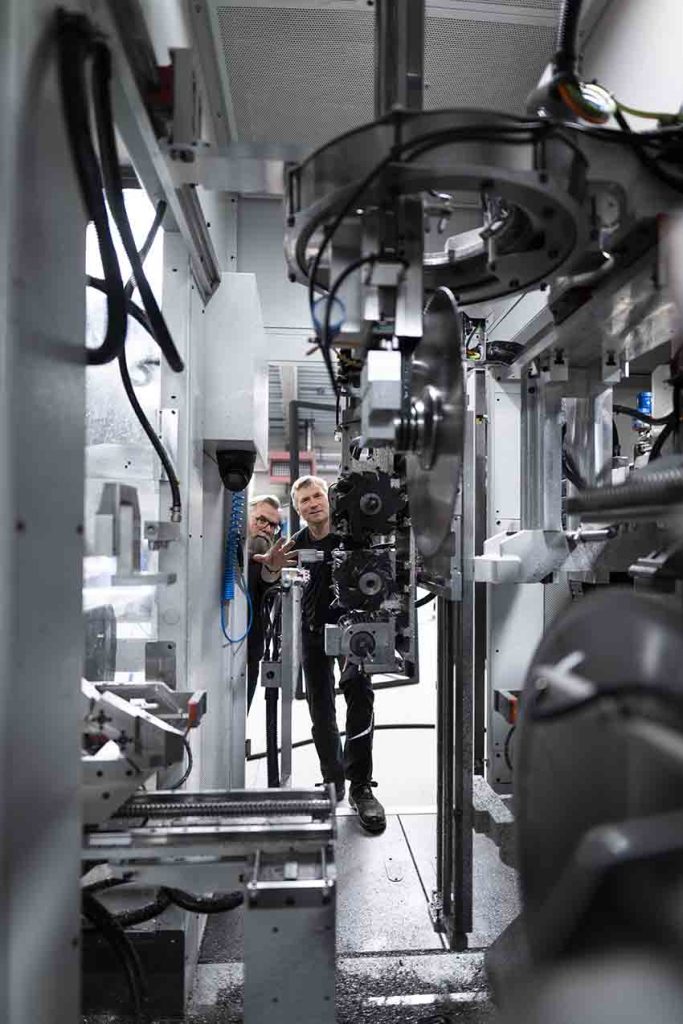
These machines are already on the market today, so it is definitely worth looking a bit further into the future. For example, it seems logical to also further automate the delivery and disposal of documents. A future vision in which an incoming order is automatically forwarded to production, after which the fully automated controlled warehouse selects the correct profile and places it on an automatic forklift that finally feeds the machine, is certainly no longer a distant science fiction. In fact, if unloading and preparation for further processing is also automatic on the outfeed side, there will no longer be any human intervention at all. It remains to be seen when -and at what price- we will effectively see this kind of system appear on the market. The same applies to robots. Cost is often still an obstacle here, but it is to be expected that they too will gain more and more ground in feeding and unloading in the coming years.
E.E: What are the most innovative products marketed?
P.C: Our fully-automated alu centre where people can work at night, without the supervision of an operator is currently the cream of the crop. Also, via camera.
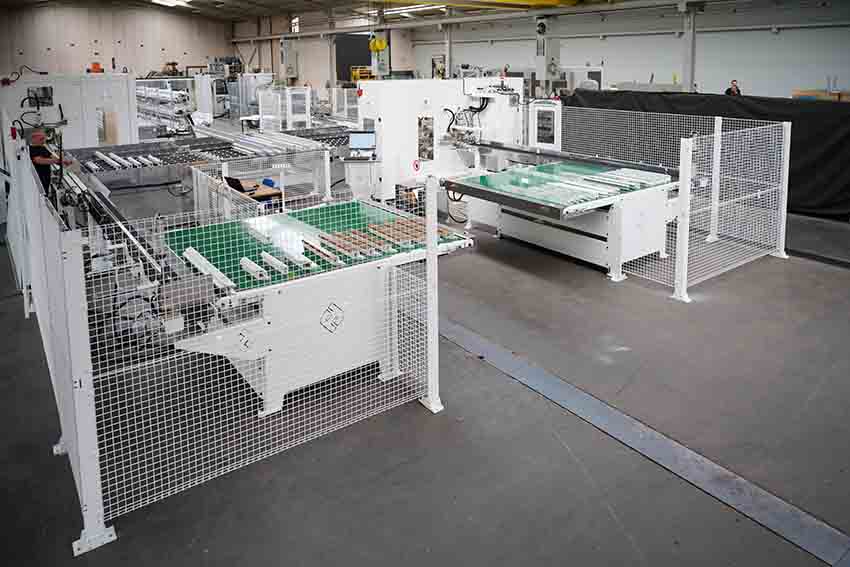
The lack of personnel also leads to less supervision within the machine. In itself, this is not a problem due to the limited error rate, but something can always go wrong. To address that, you can have cameras installed in the machine. This is useful, for example, for looking back at certain events to find out the exact cause of the error. The images can also be viewed remotely via an app. The loss of technically trained staff also leads to another kind of risk: machine maintenance and repair can come under pressure. When a downtime occurs, everyone obviously wants to be helped back on track as soon as possible, but it is not always obvious to get technicians from the manufacturer or supplier on site quickly. Today, mixed reality allows remote monitoring of the machine. The customer puts on mixed reality glasses and looks at his machine, at the machine manufacturer they see the error message appear directly. They in turn can then provide the necessary instructions for repair, which are immediately displayed on the glasses. Thus, in many cases, the fault can be fixed very quickly.
E.E: What estimations do you have for 2023?
P.C: We have delivery times of 14 months and more. So we are always looking 2 to 5 years ahead. We are already looking at 2025. We are currently developing a revolutionary machine centre to allow our customers to produce even more and faster and this through new technologies and developments.