Ad Rem (short for „Advanced Design of Recycling Machines”) is a company that is specialized in the research, design, engineering and construction of machinery for the recycling-, mineral- and food-processing industries. These machines rely on a wide range of different technologies.
Ad Rem is a joint venture between Group Galloo and the Valtech Group, both strong companies in their field of expertise, with Group Galloo being one of the largest and most renowned recycling companies in Europe. The Valtech Group is a holding containing 15 niche market engineering and construction companies that are mainly active in, or closely connected to the recycling industry.
The recycling expertise of Group Galloo together with the engineering ingenuity of the Valtech Group makes for a strong foundation. The ambitious staff of Ad Rem is putting in all possible effort to maintain Ad Rem’s position as a front runner in the industry. During its existence Ad Rem has been optimizing and developing new ways for separating diverse waste streams and materials. Ad Rem is continuously upgrading, modifying and researching new solutions for their customers.
Easy Engineering: What are the main areas of activity of the company?
AD REM: Having sprouted from Group Galloo, Ad Rem’s main area of activity still lies in the recycling industry, specifically in the recycling of ELV’s (End of Life Vehicles), WEEE (Waste of Electric and Electronic Equipment) and IBA (Incinerated Bottom Ash).
The core technology Ad Rem provides for this is flotation: mixed shredder waste is brought into a liquid on a certain density called a „medium”, wherein the lighter material floats and the heavier material sinks. This way, a separation is obtained between different types of metals and plastics.
Many components are required to operate such a process, for example in water treatment, material pre-treatment such as sieving and air separation, or material transport. Hence, Ad Rem can boast a broad portfolio of process components which are also relevant for other industries. For example, a carrot washing system was provided for a food processing company in West-Flanders.
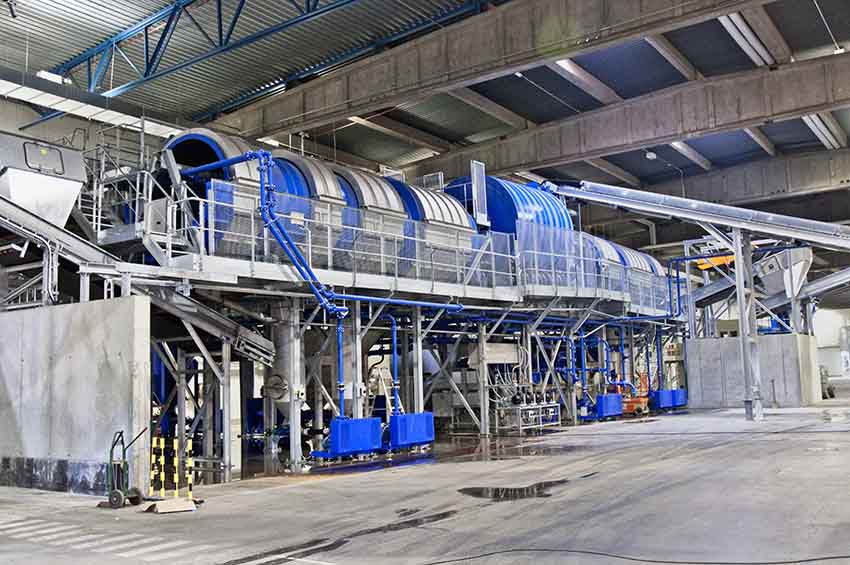
E.E: What are the ranges of products?
AD REM: Ad Rem focuses on the development of two main production lines: metal separation plants and plastic separation plants. Both products use the same physical principle of flotation in a density liquid to obtain the separation of the input material, but the process is rather different.
For metal separation, Magnetite and Ferro Silicon are used to raise the density up to 3.2 kg/l. This means one liter of this liquid is 3.2x heavier than water. At these densities, a highly turbulent process is required to keep the liquid in suspension. With this process, plastics can be separated from metals, but also different types of metals such as magnesium and aluminium can be floated from the rest of the heavier metals. The clean output fractions are then sent to a smelter to be made into new metal products.
In the case of plastic separation, densities only go up to 1.25 kg/l, but the density range of the materials to be separated is a lot narrower. This means that a less turbulent process is required to give the heavier plastics the opportunity to sink to the bottom. The substance we add to increase the water density is unique in our process, the use of which is patented. It creates numerous advantages compared to the more traditional use of salt, since it remains a suspension and not a solution. This not only prevents corrosion of the plant, it’s also a lot cheaper, and it can be recovered and re-used in a closed loop system.
E.E: At what stage is the market where you are currently active?
AD REM: Not in the least due to EU regulations, the automotive recycling market in Europe is already at a very advanced stage. At Galloo, today, 98,5% of every car is recycled. Many efforts are done in Europe to also increase the recycling rates for electronic waste and other categories, but there is still some work ahead. The main problem is the illegal export of waste to less developed nations, where it is often manually taken apart, burned, or landfilled, causing a massive loss of primary resources and major environmental concerns.
In many emerging economies, proper disposal of ELV’s and WEEE is a huge challenge. The infrastructure is simply not there. They do not have the volumes or investment capabilities to erect shredder plants and the subsequent post-shredder residue recycling installations. Increasing regulations and investments in these areas, as well as raising the general standard of living, could improve the situation in the future.
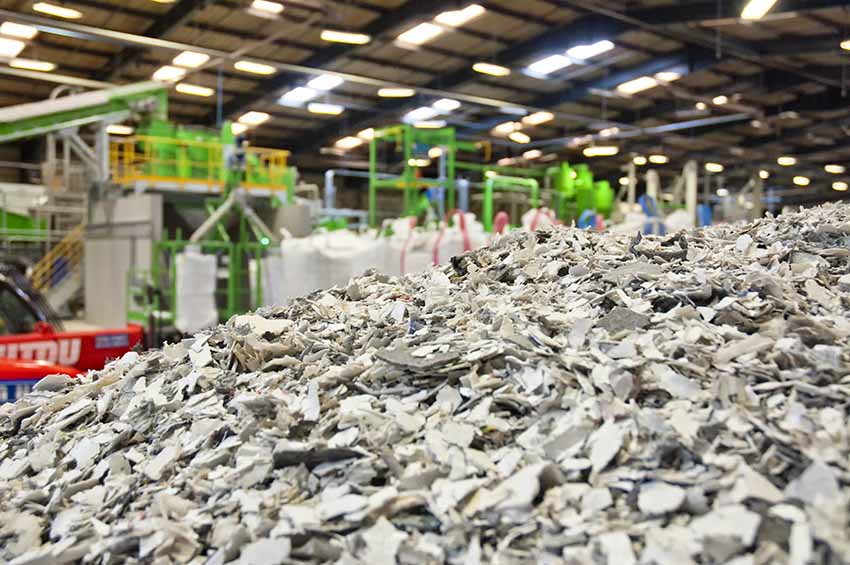
E.E: What can you tell us about market trends?
AD REM: A few years ago, China banned all import of mixed plastic waste. In 2021, the global trade of plastic waste will come to a further stop because of a convention most countries in the world have agreed with (the „Basel convention”). This means that many countries will have to adapt and invest in domestic plastic recycling equipment. It is expected this will cause a significant disruption in the global recycling industries. Ad Rem believes these developments will be mainly positive, both from an economic and ecologic perspective. Countries and companies will be forced to invest in the necessary technology to manage their own waste, instead of simply sending it overseas, where it was previously landfilled or incinerated.
E.E: What are the most innovative products marketed?
AD REM: All of Ad Rem’s projects are custom made according to the specific needs of the material to be treated. In this regard, each new project can be seen as innovative. In 2021 specifically, Ad Rem will build Japan’s largest plastic recycling facility to date. Part of the plant is a new and secret design to separate the light plastics PE from PP according to the method that was developed in-house at Galloo.
For a project in Greece to separate metals from automotive shredder waste, Ad Rem will introduce a new and more efficient washing system. This is an important development, as it will bring down the investment cost for such a system while still upkeeping the performance, which is required to avoid pollution of the density liquid in the process.
Ad Rem is also developing its own equipment to dry plastic material, and various components to further clean up the plastic waste fractions, making them suitable for re-extrusion.
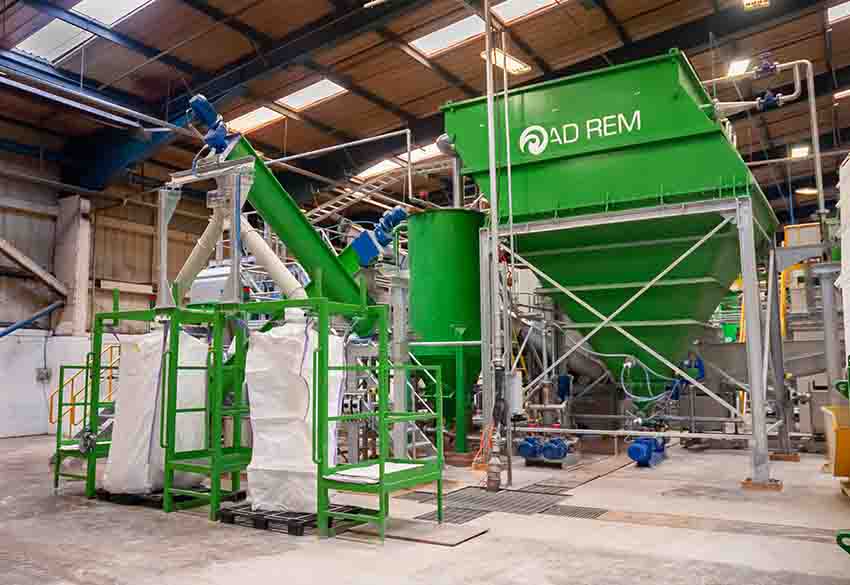
E.E: What estimations do you have for 2021?
AD REM: Despite the situation with COVID19 and the subsequent global recession, Ad Rem’s order book is quite full. With the changing market trends, especially for plastic recycling, it is only expected to get busier. Ad Rem projects a significant growth for 2021 and beyond, both in terms of revenue as in number of employees and projects.