GG Tech designs and manufactures parts, devices, prototypes and machines. The company specializes in geometrically and technologically difficult parts and machines mainly for the automotive, chemical, food and machine industries. Established in 2003, it constantly increases its market potential. Initially, as a small service company based mainly on small orders and the work of the owners themselves, it constantly expands its structure.
Currently, GG TECH has approx. 50 highly qualified employees and a modern, well-equipped machine park. A stable market position, constant investments and the highest quality make the company a brand itself. The year 2017 was the beginning of the diversification of the company’s activity by the acquisition of one of the steel hardening plants in Lodz and creating a capital group focused on the same industry.
Easy Engineering: What are the main areas of activity of the company?
GG TECH: Over the last years, GG Tech has gained enormous experience in the design and manufacturing of measurement instruments, handles, jigs and small to medium-sized tools, which lead to the creation of its own R&D department. Its work resulted in the development of many design and construction solutions as well as its own patents and finally the development of the APMS (Automotive Professional Measurement System) instrument line. The result of the investment is the implementation of large-size special measuring instruments for production, dedicated for the automotive industry, as well as precise processing of large dimensions from other industries. Also, we manufacture format parts of bottling lines (screws, stars, guide tables, capping heads etc.) and provide services related to a precise 5-axis machining of large and small parts with high accuracies.
E.E: What’s the news for 2021 about new products?
GG TECH: As a part of the investment, the construction of a new production hall with all the necessary infrastructure and the purchase of new CNC machines and software was made. The milestone of the entire implementation was the recent launch of a 6-axis milling center with a machining area of 3200x6000x1200 mm and a volumetric positioning accuracy below 0.05mm in the full working range for all axes simultaneously. The tool paths are created using one of the best CAM software on the market and a post-processor dedicated to this particular machine. To control deviations in shape and position the existing measurement laboratory was expanded with a purchase of a coordinate measuring machine with a simultaneous 5-axis REVO measuring head and a work area of 1500x3000x1200 mm.
Video of measurements of the body of the measurement fixture:
E.E: What are the ranges of products?
GG TECH: We don’t develop a single product ourselves and mostly focus on the services. Our product ranges depend on the customer needs. As a tool shop we manufacture tailored solutions for our customers. From parts to machines and production lines. We also provide engineering, design, measurement, machining and hardening services. To sum up, the range of GG Tech products is very wide, from simple details to very complex, precise and technologically difficult to machine parts as well as entire machine assemblies. We accept both individual and large-series orders. Our product range includes solutions for the food, pharmaceutical, energy, automotive, chemical and paper industries. Each order is a challenge in which we engage in 100%.
Main ranges of our production are:
Machine parts
The manufacturing industry is the main recipient for our products. We make cheaper replacements, improve existing parts and restore damaged elements. We supply various types of workshops, technical warehouses and production facilities with spare parts. All products manufactured by us are assigned unique system codes, which are related to electronically secured technical and manufacturing documentation. At request, we provide measurement protocols for the manufactured goods, which certifies the quality of manufacturing. We maintain our own warehouse stocks for regular customers in order to better secure their production. We invite you to cooperation.
Format parts for bottling plants
Several years of experience in servicing the food and chemical industries has allowed us to create a professional department that fully specializes in servicing the bottling machinery. Starting from repairs and renovations ending with the improvement of production efficiency and the implementation of new products. At the same time, we have created one of our leading products – format part kits. We provide comprehensive implementations for new packaging, such as bottles, cans, corks, dispensers, etc. for any brands of machines. Our format parts work in most Polish factories, and in the last few years we can be found more and more often on the markets of Western Europe.
Helixes
Machine helixes – most often they are a part of the equipment of lines transporting packages. In the production cycle, they most often provide the separation of grouped packages fed to the bottling machines. With the help of helixes, various types of tasks are carried out, such as: rotating, separating, grouping, tilting, mixing and others. They are also used to give the products the desired speed and acceleration. Variable geometry of recesses or variable pitch are not limiting us, both in terms of design and technology. In Poland, GG Tech probably has the highest specialization in their manufacturing, both in terms of knowledge, experience and machine park equipment. Until today we have manufactured and sold over 1000 pieces of various types of helixes.
Machines and devices
As a company profiled in mechanics, apart from the standard manufacturing program of individual machine parts, we dynamically develop the department of machines and devices design. We design and manufacture specialized, unique structures in compliance with the applicable safety and quality regulations. If necessary, we equip the devices with advanced automation systems at the level of advancement tailored accordingly to individual customer requirements. We issue CE certificates for all completed projects and provide production implementation. The previous implementations of machines and devices manufactured by us relate to such industries as: chemical, food, confectionery and automotive.
Turners
The frequent need to rotate the packaging during the production process contributed to the creation of a specific product at GG Tech – the turner. It is mostly used in industrial washing, drying and printing machines and must be characterized by an appropriately designed shape course necessary to maintain the efficiency of the process. Our turning machines are individually designed products, according to the customer’s requirements, often made with the use of 5-axis CNC machines. They are made of materials with a low friction coefficient, both plastic and polished steel, ensuring long and reliable operation.
Gears
A part of GG Tech company is a fully equipped tool room. Our machine park allows the production of most gears and chain wheels. We reverse engineer, design and manufacture gears and chain wheels, the purpose of which is to supplement the standard offer of the market of finished goods. The large machining ranges of our machines and their versatility allow us to meet the most diverse customer requirements. To maintain the increased durability of our products, we use additional heat treatment techniques, such as surface hardening and nitrating, and for plastic wheels, we provide advice on the selection of the appropriate material.

Welded structures
In order to supplement our production capabilities and provide customers with a comprehensive supply of spare parts, we have created a welding department. Welded structures are made using MIG/MAG and MMA techniques. We weld various steels as well as materials such as aluminium, titanium and selected plastics. We have the possibility of finishing the welded products by: sandblasting, satin finishing, rotary-finish and powder coating.
Gravitational and vacuum molds
The GG Tech company has many years of experience in the design and production of vacuum molds, used as interchangeable elements of thermoforming and gravity machines used in the casting technique with the use of epoxy resins. Vacuum molds are typical industrial tools, characterized by high wear resistance, while gravity molds are tools for the production of short series of parts, the design of which must ensure adequate venting of the cast models. Considering the large number of projects and molds produced so far, they naturally became a separate product in our company.
Shafts for cookies
We make shafts for the production of cookies, both in the form of molds and dies. We carry out orders for any patterns provided by the client and we offer our own. We cut the shapes of cookies on monolithic shafts, rings and in the form of individual molds. The material that is used for this type of parts is mainly plastic approved for contact with food (POM) and brass with an outer layer of Teflon.
Measurement gauges and instruments
GG Tech manufactures test and measuring instruments to verify the dimensional quality of mass-produced parts. Devices of this type allow you to easily check the deviations of the geometry of any part against the set criteria. They can be equipped with dial indicators facilitating the reading of the deviation value or with tolerance fields on the basis of which the controller qualifies the position of a given dimension in the required deviation field. Gauges and measuring instruments speed up control, eliminate the need to have universal measuring tools, the use of which is impossible when measuring shapes and points on curved surfaces. The ease of handling and qualifying parts with the instrument eliminates the need to maintain a qualified metrology staff.
Mounting brackets
We produce various types of manufacturing brackets, assembly and fixing devices. They are used in welding, machining and mass production of elements that undergo many technological processes. Clamps of this type allow to unambiguously determine the position of the part with the required repeatability and fix it to a specific task. We design these tools on the basis of the guidelines provided by the client, while providing advice based on many years of experience in the design of devices for many industries. For the production we use a variety of materials that must guarantee secure fixing without exposing the part to damage (e.g. scratches on aesthetic surfaces).

E.E: At what stage is the market where you are currently active?
GG TECH: Due to the COVID-19 the market slowdown is very visible. We noticed a drop in orders and we have a spare capacity (what was rare in previous years).
E.E: What can you tell us about market trends?
GG TECH: Automotive industry is moving in the direction of electro mobility. This is why the design of motor vehicles are going to change. We are already observing our customers preparing for the new products in the form of the electric drives. In addition, the automotive industry strives to improve and automate measurement processes, which we respond to by adjusting our instruments and tests.
E.E: What are the most innovative products marketed?
GG TECH: Speaking about market innovations these are robotic measuring cells. Unfortunately, their huge price does not allow for implementation in all areas where measuring instruments and gauges are used today.
Speaking about innovations being researched by us, we have to mention the motorcycle and it’s engine we developed. We are pleased to present you a study motorcycle, which was created by GG Tech. The design was made by the JJS Design studio by J. Jacek Synakiewicz and was manufactured by us mainly due to its aesthetic value and innovative solutions. We were able to implement such a demanding project thanks to the technologically advanced machine park and the experience gained during the implementation of complex projects. The motorcycle was selected to take part in the exhibition “Design in Poland – Transition to Modernity”, organized in Geneva by the Patent Office of the Republic of Poland. The motorcycle was nominated for the exhibition at last minute. We had only one month to build its first stage, visible in the photos. Only thanks to the latest CAD/CAM/CNC design techniques, our efficiency and passion, all work was completed on time. As it is an exhibition model, aesthetics, precision and quality of workmanship were our priority. We believe that only products made at the highest level can promote Polish design and technical thought in Europe. The completed study motorcycle is our contribution to further work on the joint project JJS Design – GG Tech.
The engine is the most complicated part of our motorcycle. It is a great design and technological challenge. The innovative concept of J. Jacek Synakiewicz gives rise to several variants of the piston itself. We have successfully built, commissioned and briefly tested three different two-stroke engines. The first was the 125 cc engine with the use of the spatial piston. This engine is a “quarter” of the JJ2S X4 500 from a motorcycle. A very interesting solution of the piston is the so-called jet piston where is a potential to use the kinetic energy of exhaust gases in a way that has not been seen before in the design of internal combustion engines. This solution also brings an unconventional approach to the design of the exhaust resonator, which can generate a return pressure wave not to boost the engine as in classic two-stroke but to re-affect the piston – specifically the upper walls of the pre-compression chamber flange. Perfect cooling, simple design and, above all, the freedom of crank systems are the features that determined the construction of the model engine according to the JJS Design project. Successful tests of the single-cylinder 6.5 cc engine whet the appetite for building a V-twin engine, which was rare in the previous two-stroke engine designs. Mainly due to the problem of location and separation of the prestressing chambers. Our solution is simple, compact and free of the above-mentioned problems, not only in the V configuration, but in all other. For this reason, the current stage of development is a great base for modelling internal combustion engines and is a good basis for testing larger units.
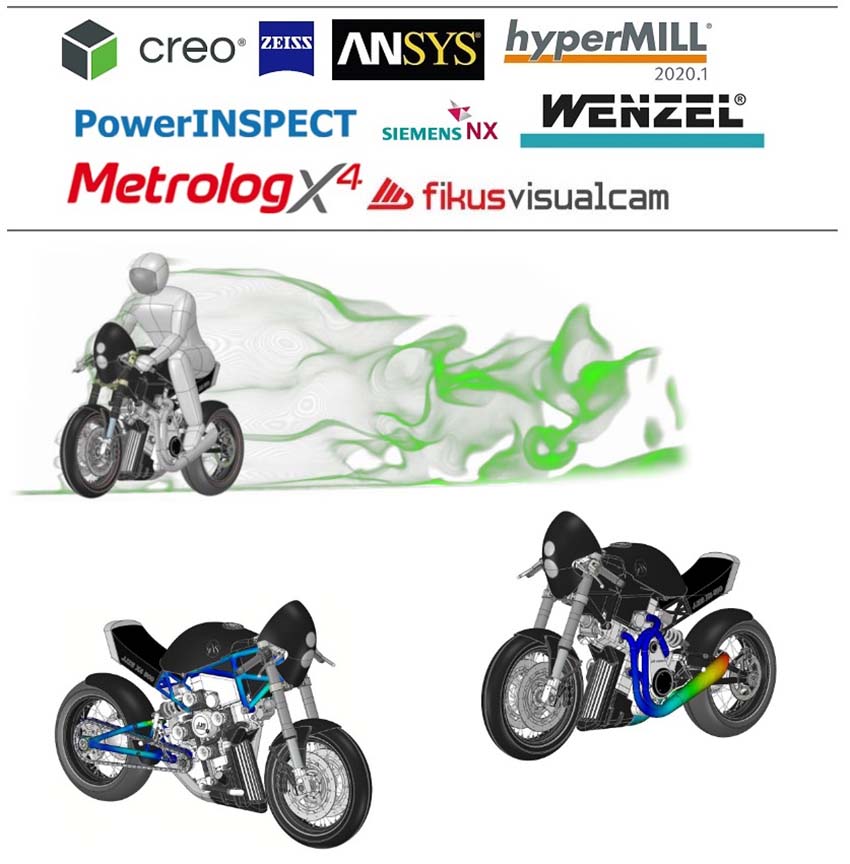
E.E: What estimations do you have for 2021?
GG TECH: Hopefully the pandemic will end and the market situation will improve. In the meantime we are working in-house on improving of the so-called continuous cutting technology on milling machines. In the current state of development of this technology, it can be applied to appropriate machine tools for a wide spectrum of surface types. The method has a great potential in surface finishing and many non-technological elements in the milling process. We are looking for partners for the development of this surface treatment method, mainly in terms of programming support in CAM systems and the design of the machine tools themselves.
The continuous cutting method had proven to be very efficient in keeping the cutting speed at least at a minimum level of Vc. By the nature of the method, this speed is equal to the feed. Therefore, it requires the use of machine tools with high operating speeds of controlled axes (over several thousand mm / min). Making a sample using the continuous cutting method takes 60% less time than the classic method, while maintaining better roughness parameters. It should be noted that this time may be several times faster when confronting the samples with the classical method of similar Ra, because at maximum spindle revolutions the only way to improve the roughness is to reduce the feed, which extends the process. The surfaces made for the purpose of the study were relatively small (about 100mm long). Due to the dynamics of the machine tool, machining times will be significantly reduced when making longer surfaces and the time will be longer for shorter ones.
The continuous cutting method, compared to the classic method, gives much better roughness values along the cutting line and comparable values perpendicular to the cutting direction. However, it should be noted, that the sample made with the classical method was milled with a tool with almost twice the radius. Accuracies are on a very comparable level with the advantage for the classical method (differences on the order of 1-2 micrometers). The accuracy of the continuous cut method deteriorates as the machining area is moved away from the rotary axes. This is due to the action of the distance from the tool contact point to the rotary axis as the angular position, velocity, and acceleration error multiplier. It manifests itself mainly by deterioration of the surface waviness. Speed and acceleration errors are greatest and can be minimized on a specific machine by using lower feed rates. They could also be reduced by using better drives and axis measuring systems, but this is a task for machine tool builders and goes beyond the capabilities of technologists and programmers. Errors resulting from the position of the angular axes cannot be minimized by the technologist and programmer because they result from the construction of the machine tool. However, when comparing the continuous cutting machining with the classical machining in a smooth four / five axis, the 2 micron shape deterioration encountered will be the same.
The use of the continuous cutting method on milling machines with a swivel-rotary head instead of the cradle, or a rotary table plus a tilting head, will give greater opportunities to control shape errors due to the constant distance of the rotary axes from the tool edge. This configuration of the machine tool kinematics guarantees constant values of the obtained shape tolerances on any large work piece (throughout the entire machining range of a given machine tool).
The continuous cutting method is used mainly in finishing (milling from 2.5 to 6 axes) of surfaces that allow the introduction of a path for acceleration and deceleration of the tool, or if the surface parameters on a given specific part will allow start and end of cutting from 0 mm/min. Thus, open surfaces (not limited by vertical walls) can be processed without major problems. Surfaces with vertical walls can be processed using a special path trajectory strategy or special tools. The current possibilities of CNC programming with the use of computer assist systems (CAM) are very large. However, they could be successfully developed mainly for the use of standard turning tools, boring bars or special tools in milling machining strategies and the generation of these strategies, tool inputs and outputs in the aspect of maintaining a minimum cutting speed Vc. Current CAM systems in milling strategies do not support at all the smooth use of the sixth axis in the machine spindle and such support would be crucial due to the above-described problems.
The method can be used in shaping low-tech internal corners due to the possible use of blades with minimal radii of high stiffness (e.g. 0.05 mm or less).
It is possible to use any turning and milling inserts, which gives great opportunities to match the appropriate tool to the surface being processed. The use of ready-made handles and holders as well as the construction of self-made tools extends the spectrum of possible shapes.
Machine tool – the main factor affecting the durability of the spindle is its zero rotation speed during machining. The spindle rotates only in positioning or at very low speed when machining with a smooth sixth axis. The disadvantage of the method due to the durability of the machine is its dynamic operation, which, however, results in a shorter processing time of a given part.
More information on the website: www.ggtech.com.pl