Conveyor belts play a crucial role in the large-scale transportation of materials on site. More often than not, the materials they convey and their working environments place extremely tough demands on them. Consequently, rubber conveyor belts are a complex and costly component. Despite this, there is a surprising lack of knowledge about how they are made and how they are engineered to cope with the toughest of conditions. Belts for different applications may have alternate production methods but here is a general overview of the core process.
It’s all about the rubber
In the majority of cases, it is the quality of the rubber outer covers that will have the greatest influence on the performance and operational lifetime of a conveyor belt. Some belts need to be able to resist the ravages of heavy, sharp, abrasive materials while others have to cope with either high material temperatures, oils and other potentially aggressive chemicals or fire. Very often, the rubber needs to handle a combination of these factors. The rubber for each belt therefore needs to be made using a very specific recipe.
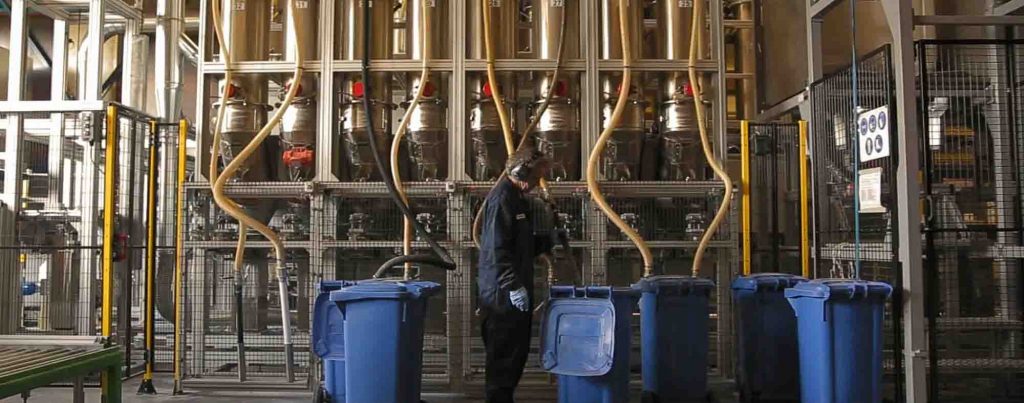
It is becoming increasingly common for manufacturers to outsource the manufacturing of their rubber. Although it helps to reduce the cost, the downsides of outsourcing are considerable. Apart from making quality control and consistency of performance virtually impossible, outsourcing makes it equally impossible to ensure compliance with European safety and environmental regulations. In Dunlop, we believe that the only way to truly control the quality of the end product is to carry out every step of the production process in-house including, of course, the manufacturing of our own rubber compounds. The vast majority of rubber used to make conveyor belts is synthetic, the most common being Styrene Butadiene Rubber (SBR). This is because synthetic rubber is far more adaptable than natural rubber and can be more precisely engineered to cope with the many combinations of operational demands.
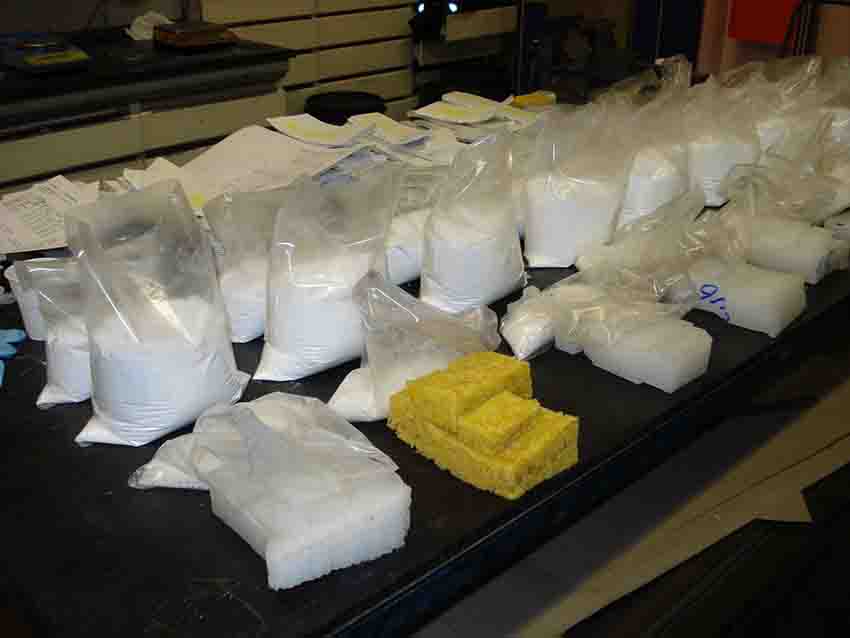
Each rubber compound consists of a complex ‘cocktail’ involving a huge range of different chemical components, polymers and other essential ingredients. This includes the UV stabilizers, anti-ozonates and anti-oxidants needed to create a resistance to premature ageing of the rubber caused by exposure to ozone and ultra violet light, which every rubber compound should have.
Mixing – Making the rubber compound
The process starts by the hand selection of the raw materials according to a computerised formula specific to the required specification of rubber. The various ingredients are carefully weighed and measured out along with oils and carbon black, which is one of the most essential polymers used in any black rubber compound. These are added automatically to form the base mixture. The batch of mixed rubber compound is then heated and mixed coarsely. After a calculated time, the mixture is dropped onto a rolling mill and then further kneaded until a soft, pliable consistency is achieved.
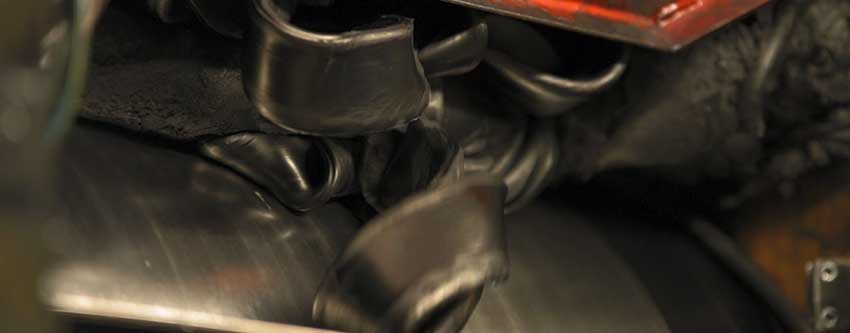
When complete, the rubber is hung like ‘drapes’ to cool down. A soap-like solution is applied to prevent the surfaces from sticking to one another. In Dunlop, each batch of rubber is labelled and a sample is sent to the laboratory for testing. This is a crucial stage in the quality control process because every batch has to be tested and approved before it can be released for further processing. This helps to ensure a consistent quality so that each specification of rubber performs exactly as it is designed to do.
Safe to handle?
At this point, I think it worth briefly mentioning an important aspect of safety. To make some rubber compounds it is unavoidable that chemicals that may be extremely dangerous in their own right have to be used. Fortunately, strong regulations are in place to protect humans and the environment in the form of REACH (Registration, Evaluation and Authorisation of Chemical substances) regulation EC 1907/2006.

These regulations stipulate that all European manufacturers are legally obliged to comply with the regulations relating to chemicals, preparations and substances used to create finished products. This includes registering the use of any “substance of very high concern” (SVHC) listed within the regulations with European Chemical Agency headquarters in Helsinki. Sadly, many European manufacturers have chosen to ignore these legal requirements, either completely or at least partially because of the impact on production costs. Of even more concern are those manufacturers located outside of EU member states and the UK because they are not subject to EU regulation concerning the use of hazardous chemicals or the use of Persistent Organic Pollutants (POPs). Safe to say that all the rubber we make and use in Dunlop is fully REACH compliant.
The calendering process
The next stage is the calendaring process. It is at this point that the belt begins to take on its durable form as layers of inner fabric (for multi-ply belts) or steel cords in the case of steelcord belts, are mated with the raw unvulcanised material. The rubber is introduced from what is called ‘the nip’ where it is spread as a film onto the rolling mill. The fabric plies (Polyester warp and Polyamide weft (EP) fabrics are the most commonly used) are then fed through the nip, where the rubber is compressed directly onto it.
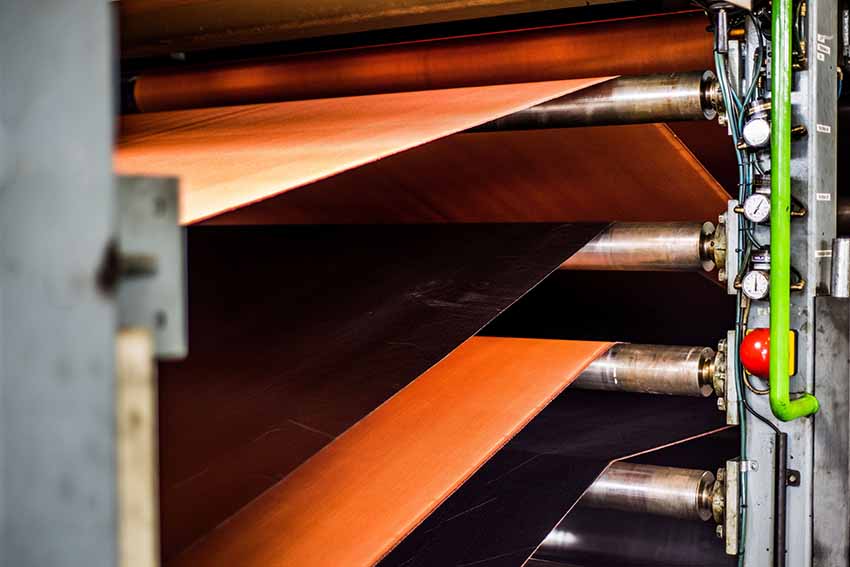
Some fabrics are calendared with one or two sides of rubber, allowing the additional strengthening layers to be added. The strength of the level of adhesion (bond) between the various layers of plies and between the plies and the covers is extremely important and is measured according to the ISO 252 test method. This literally involves pulling the layers apart and measuring the force required in Newtons per millimetre. If the adhesion levels are too high then this can be very problematic when creating a splice joint to make the belt ‘endless’. On the other hand, if the adhesion is insufficient then the layers of the belt can become separated over time. This phenomenon is known as ‘delamination’.
The layering process can happen several times depending on the number of plies required by the belt specification and the thickness of the outer covers of the belt. Once the specified grade thickness is achieved the calendared belt moves forward onto the stationary vulcanisation presses.
Vulcanization
Vulcanization is the chemical process in which the belt is pulled under tension into a press. The rubber compound is typically heated with sulphur; accelerator and activator at a temperature of between 140–160°C and pressures up to 20 bar are applied. Pressure is exerted on the surfaces of the press in contact with the outer covers of the belt using hydraulic rams. Both the temperature of the press plates and the level of pressure need to be extremely accurate and uniform throughout the entire area of the press surfaces otherwise imperfections and inconsistencies can occur.
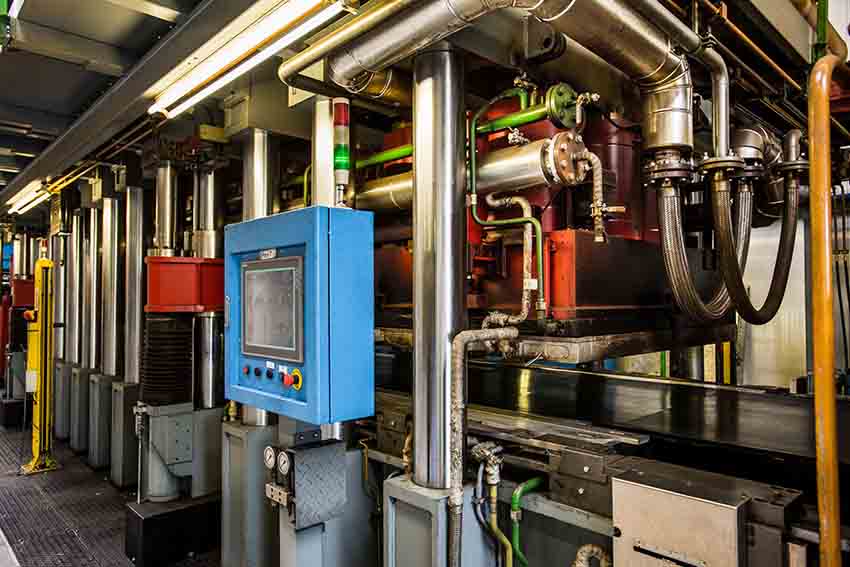
The actual scientific process involves the formation of cross-links between long rubber molecules in order to achieve improved elasticity, resilience, tensile strength, viscosity and hardness. It is therefore a crucial part of the production process. The duration of the vulcanisation process depends on the thickness of the belt and the type of rubber. For example, heat resistant rubber requires a longer vulcanisation time compared to straightforward abrasion resistant rubber. Although highly automated, the vulcanization process stills needs to be closely monitored by experienced personnel.
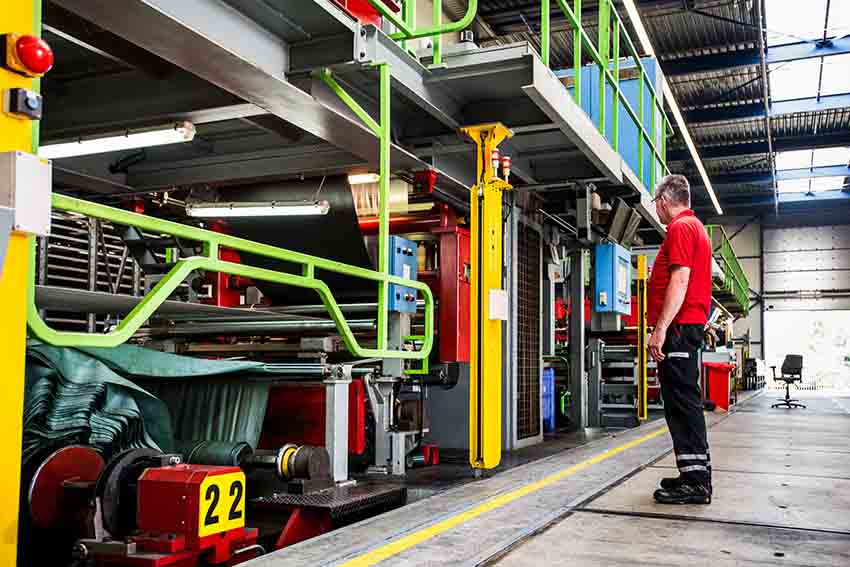
Final checking
The manufactured belt finally moves onto quality control where every metre is thoroughly inspected before being approved for transportation to the shipping and storage areas. But even at this stage, final quality control procedures are in place because random samples of completed belt are subjected to further arduous testing in the Dunlop laboratory.
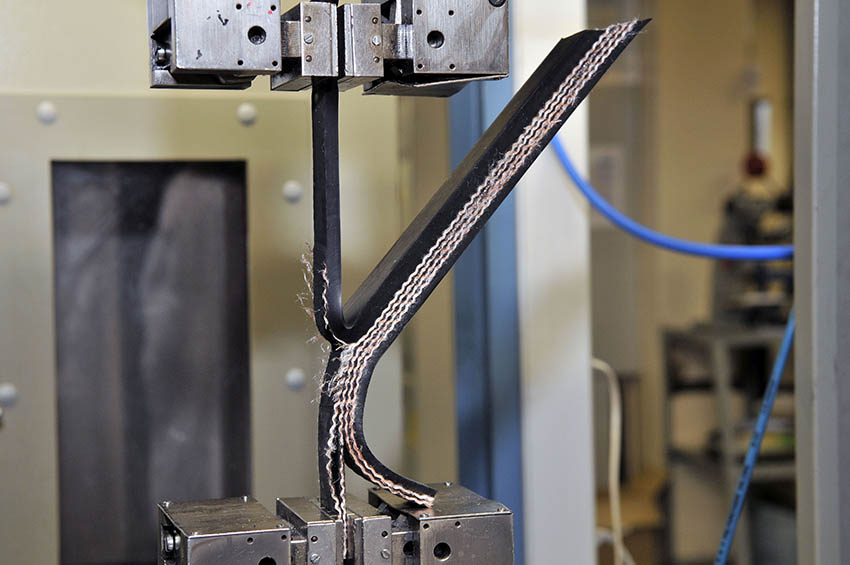
Not every conveyor belt is created equal
Although the basic production process involved in the manufacture of conveyor belts is ostensibly the same one used by all manufacturers, the fact remains that there are huge variations in the quality, performance and longevity of the end product between one manufacturer and another. Such differences are particularly magnified when comparing belting made in Europe and imported belt from Southeast Asia. All the evidence points to high quality European made belts being able to provide up to four or five times longer operational life. There is also growing anecdotal evidence where working lifespans increase from a matter of months to four or five years.

There can be no denying that the quality standards applied during the production process have an extremely significant influence. However, any production process is only as good as the raw materials that are used within that process. Raw materials constitute up to 70% of the ultimate cost of a belt. Low grade, unregulated raw materials cost appreciably less than their higher quality, regulated counterparts, which is the biggest single reason why some manufacturers are able to offer prices price that can easily be 50% less than their competitors.
No matter what price you pay, it is how long your conveyor belts last before they need to be replaced that actually dictates how much they cost. The reduction in expenditure over time and increases in productivity achieved by investing in well-made, premier quality conveyor belts will compensate for the higher buying price many times over. As the old saying goes, “Price is what you pay but cost is what you spend”.
Les Williams