Automation in maintenance management is a logical step on the way to Industry 4.0. Timly software supports this.
Swiss start-up Timly develops smart maintenance software
Automation in maintenance management is a logical step on the way to Industry 4.0. The demands on maintenance management software are enormous. In practice, production lines consist of a heterogeneous landscape of machines, IT components and tools.
If production is spread across several locations, as is the case with DAX-listed companies of the size of Bayer or Siemens, then the development of suitable maintenance software that is able to record all assets and manage upcoming maintenance appointments is a real challenge.
The Swiss start-up Timly has taken on this mammoth task. Within a very short time, the young, innovative team around the founders Fitim Mehmeti and Philip Baumann developed into one of the market leaders.
The scalable cloud solution is increasingly becoming a standard application in the field of maintenance software, as evidenced by the names on the growing list of satisfied users. In addition to the chemical companies Bayer and BASF, these include Siemens, Philips and Panasonic, for example.
CMMS – that’s what maintenance management is all about
The acronym CMMS stands for Computerised Maintenance Management System. It refers to the computer-controlled optimisation of maintenance and repair processes. The process of maintenance is standardised in DIN 31051, where the more common term maintenance is defined as a sub-area of maintenance. The other sub-elements are inspection, necessary repairs and the improvement of systems.
The CMMS not only combines the sub-areas of maintenance. It is about recording all relevant information for each asset. This includes operating instructions, maintenance instructions and documentation of previous maintenance measures. A maintenance planning software must therefore be far more than a computer-based schedule management system. It represents the central tool for information management around asset management.
Smart maintenance tool – industry has special requirements
If machines or parts of them are not available, this has interactions with other work areas in industrial production that can lead to lasting disruptions in the production process. This results in the requirement to use all reasonable preventive measures to maintain the functionality of work equipment. Another requirement is usually that maintenance measures must be designed in such a way that they disrupt normal work processes as little as possible.
Timly’s asset and maintenance management software creates the conditions for recording assets of all kinds with all the necessary parameters. Logical associations can be created in the form of so-called containers, for example of rooms, production sections or units of a machine.
On the one hand, objects can be managed in a fine-granular way, which, for example, contain all the necessary information and have their own smart appointment calendar. On the other hand, information can be filtered in this way for entire work areas.
The coordination of appointments is easier to handle with a global maintenance calendar. Events stored in it are actively managed. In this way, they can be assigned defined actions. This can be the notification of the responsible person by e-mail, but also the initiation of a maintenance order with external service providers.
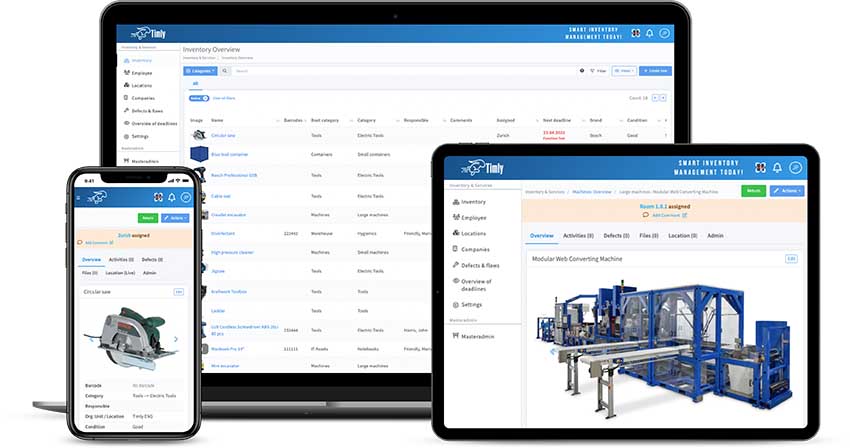
Always have maintenance and deadlines in view: with the intuitive Timly software.
Maintenance software market leader: Timly
Timly’s maintenance management software is implemented as a cloud service. The software-as-a-service (SaaS) principle provides several advantages in maintenance. The central data storage on the cloud server administered by Timly can be accessed with any internet-enabled end device. The company’s IT infrastructure does not need to be adapted.
The web app optimised for smartphones and tablets can be used to call up a device profile. For simplification, it is possible to mark assets or workspaces with QR codes. This means that scanning the QR code in the app is sufficient to gain access to all the necessary documentation for a machine. Maintenance and inspection records can be filled out digitally in this way and stored directly in the profile of the work equipment.
Initiated repair processes can be tracked in the maintenance software.
Maintenance planner free of charge: full version offers added value in practice
Timly’s SaaS concept makes it possible to use the software in the existing IT infrastructure. Even existing smartphones and tablets of employees can be used safely to operate Timly, as the web app does not permanently store any data on the end device.
The servers used are set up in compliance with DSGVO, encryption and user management ensure data security and data protection. Since the actual computing power is only needed on the cloud server,Timly’s inventory management software is scalable as desired. Compared to local and possibly free open source solutions, this has the advantage that in principle there is no administration effort – which in turn ties up own employees and costs working time.
In addition, a commercial solution like Timly offers professional support. If maintenance management software is used for an interface function such as maintenance planning, prolonged outages or unresolved software errors are otherwise quickly a serious problem.
Using Excel as a maintenance planner – not a solution for industry
While software such as the spreadsheet programme Excel may be suitable for an initial inventory of assets, the permanent updating of necessary parameters quickly leads to borderline areas. Poorly implemented multi-user capability, lack of usability for mobile devices and the cumbersome integration of files such as PDFs or image files are problems that frequently arise in practice when Excel is to be used for maintenance management.
Database-based maintenance software has a clear advantage here. User views are generated dynamically, which keeps them clear. Data records can be linked and filtered as desired. New functions are always working with the existing data stock.
For example, Timly offers the linking of its maintenance software with IoT sensors. GPS trackers show locations, an automated fill level check for operating materials, which is carried out by distance measurement, can be stored with intelligent notification functions.
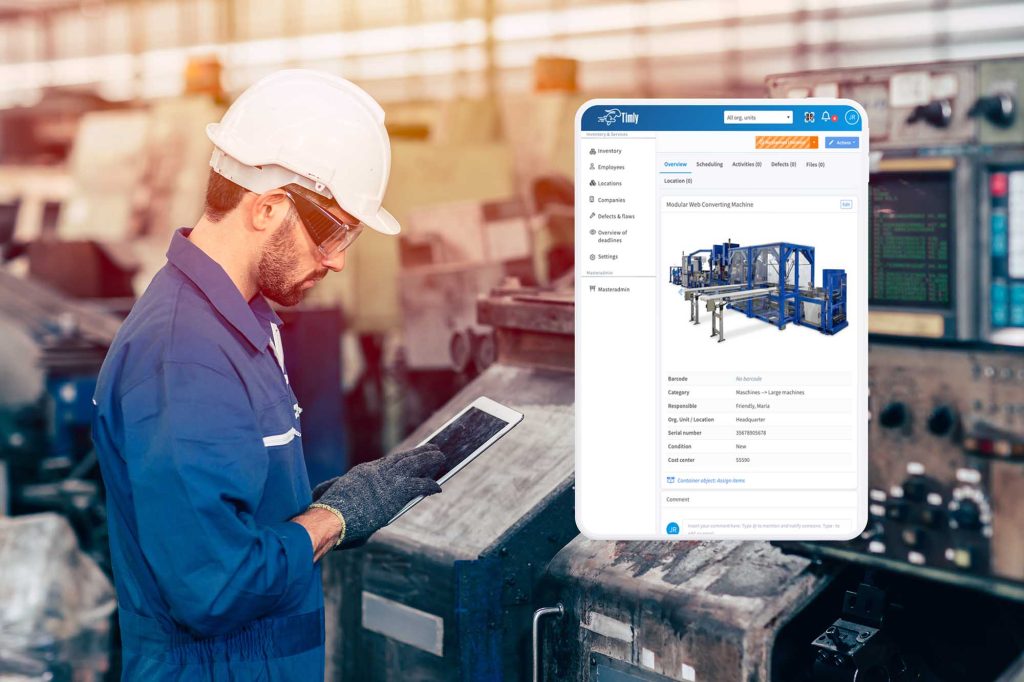
Software selection: Gather experience through own tests
Before software for maintenance management and planning can be used in a company, it is necessary to record the complete inventory once. Although the developers of Timly support the import of existing data from different file formats, a later switch to another product is time-consuming.
For this reason, maintenance software should be tested extensively in one’s own working environment before it is introduced. For this purpose, those responsible for Timly Inventory Management offer a free test phase.
Maintenance management software: costs vs. working time savings
The use of commercial software must pay off for those responsible in companies. CMMS “accompanies” work equipment for the entire duration of its productive use. A structured maintenance concept ensures the longevity of machines and tools. The reduction of downtime saves money in the end.
The less working time that has to be spent on administrative activities, the more efficient company processes become. The holistic overview of plants, machines and also parts of them, facilitates the assessment of the economic efficiency of assets used. Therefore, a calculation should speak for the use of a maintenance app in most cases.