Stevia Automation is an engineering company in the field of industrial automation. They have many years of experience in designing, commissioning and servicing of production process control systems in many places around the world. The company’s strengths: an experienced team of engineers and a modern design office equipped with professional test stands of their software, including CAD environment – Emulate3D (virtual commissioning).
Interview with Paweł Wróbel, Managing Director at Stevia Automation.
Easy Engineering: A brief description of a project / projects.
Paweł Wróbel: This year, together with PZM Technology – our partner, we have completed the project of designing, installing and commissioning an automated sorter project for one of the delivery companies located in Southern Poland. The automated sorter was located inside a warehouse with a main goal of segregating parcels directed to different locations. Our mechanics partner in this project, PZM Technology company is a Polish company which was responsible for designing and installing the sorter with infeed lines, while we have delivered the software part together with control cabinets and electrical installation.
E.E: What were the needs of the client?
P.W: Our client was the delivery company handling courier delivery packages packed usually in carton boxes, but also polybags, envelopes or trays. The client was shipping the parcels to different locations, and had a wish to sort the orders as per location in a faster and more efficient way. Manual sorting of the parcels would be too tiring for the employees and related with a high risk of a human error, causing the package to be sent to a wrong location. The process of sorting itself includes repeatable, monotonous tasks, as the goods flow is constant. Our client’s main goal was to sort parcels using a barcode-reading scanning system. The system is capable of identifying a package by scanning the barcode placed on it, and after communicating with the WMS system, it can send the product to the appropriate location based on the information received from the higher-level system.
E.E: Why did the client choose your products / solutions?
P.W: In my opinion the most important reason why our solution was chosen, was experienced personnel and a wide variety of services we could offer for our client. Our engineers were able to analyze the client’s needs and adjust the concept version of the project to them. The technical consulting aspect is very important as from the very beginning we can gain the position of the expert in our field and through listening to the client we can gain more experience about the common needs visible on the market. As a company, we can provide the complete software and carry out the commissioning, as well as control cabinets prefabrication and supervision of the electrical installation. We are also able to prepare an EPLAN design of the project, and virtual commissioning, through which the client can see an actual digital twin of the system.
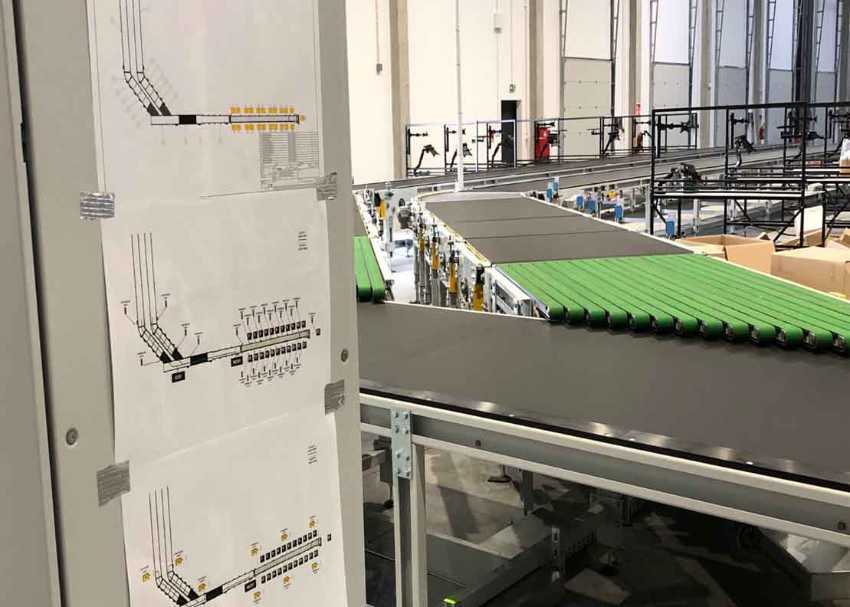
E.E: What products / solutions were used?
P.W: Providing that automatic sorting system we integrated high-throughput sorter, scanning tunnel and conveyor infeed lines. The sorter was very universal when it came to the packaging types, whether it handled carton boxes, poly bags or envelopes. While implementing an automated sorter, we have used a scanning tunnel equipped with multiple scanning cameras. With a very fast speed of the goods moving, the camera reads a barcode on each parcel, with the label located on every side of the package.
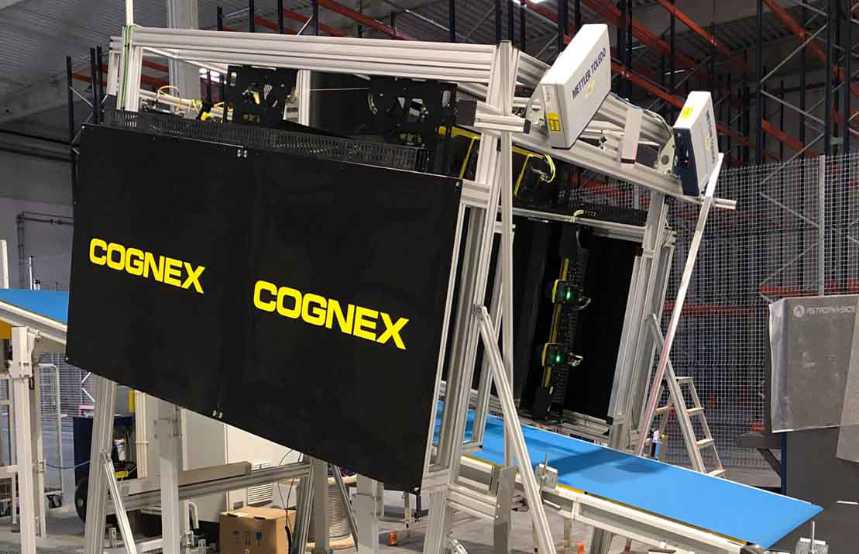
E.E: Please describe how the project was implemented?
P.W: This project, as well as many other ones, had four main phases: preparatory phase, design phase, implementation phase, and a technical maintenance phase. During the first phase we define the requirements of the system, and we prepare the FDS (Functional Design Specification) document, which describes the detailed assumptions of the whole system. We select the right hardware and software and we make the hardware specification, project schedule and quotation.
Next, we prepare the complete mechanical and electrical documentation of the project in the design phase. We create source code and hardware configuration. We test the software using the Emulate 3D program, and we prefabricate control cabinets.
In the implementation phase we install hardware and implement the software, then we carry out on site tests. In this phase we also supervise the start of the system’s work and we can provide the technical training for the machine operators. During the technical maintenance phase, we offer warranty services, remote technical support and regular overviews. This pattern of implementing such projects has been working for us for many years and allowed us to always complete projects on time and in an efficient way.
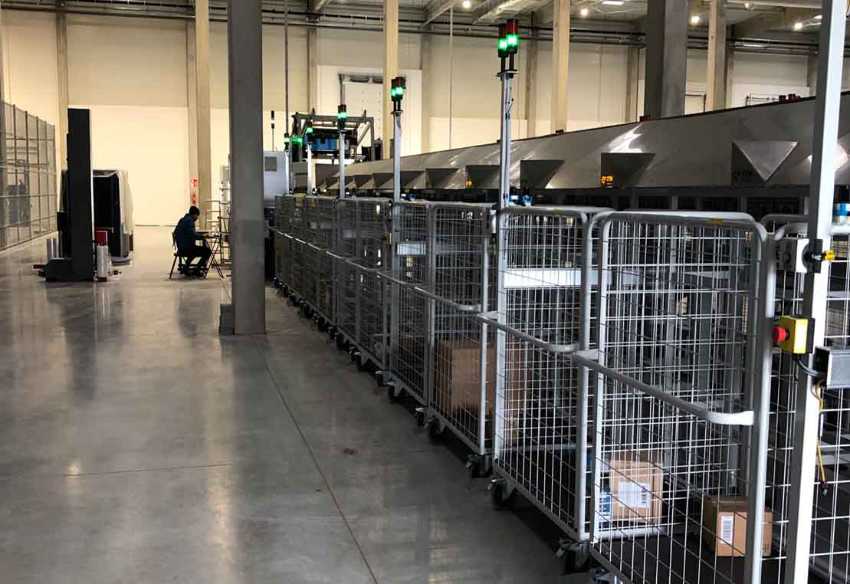
E.E: Were there any products with special characteristics used?
P.W: Looking at the completed project, the most outstanding element is a high throughput sorter with the ability to handle different types of packages, a wide range of dimensions and weights. Also, an interesting solution is a scanning tunnel which allows to read the barcodes on every side of the moving package. The scanning tunnel is equipped with cameras that can take a picture of every parcel and measure their dimensions.
E.E: How did your products / solutions improve productivity for the client?
P.W: The solution of an automated sorter improved productivity of the client because of the speed increase of the process, and replacing repeatable, monotonous employees’ work with way more precise machines. Sorter is designed to handle product flow at a capacity of up to 5000 products per hour. It can handle cartons, polybags and envelopes with different dimensions, from 100x150x10mm up to 800x800x800mm, and weight from 0.01kg up to 30 kg. Additionally, the system equipped with AI scanning cameras can take a picture and automatically measure the dimensions. The image and dimensions of the parcel can be available immediately in the IT system and the data can be visible for every department of the company. The operators of the system have to be trained for operating the sorter, however they can avoid manual scanning of each parcel which is very time consuming and very little developmental work.
E.E: How important was the project / projects for the client?
P.W: We were able to identify and familiarize ourselves with our client’s problems and create the solution. The client – a delivery company, was looking for shortening shipping times, and higher percentage of accurate shipments – right goods to the right receiver. Short delivery time and precision of each delivery is the key to the client’s success, because it makes their customers satisfied with the service and generates good opinion in the market, so that people can trust our client with their orders.
E.E: What was the client feedback after implementation?
P.W: The client received full support at the first stage of the system’s work. The sorter was well tested and the employees were provided with the training. Our engineers keep in touch with the client constantly during the first period after commissioning. That generated good feedback from the client, once they know they can count on us in any problematic situation.
E.E: How did the solutions provided improve efficiency for the client?
P.W: The solution implemented provided an efficient way of parcel sorting, so that they can be delivered to each location faster. Having all the parcels sorted on time and being able to increase capacity of the product flow and throughput of the warehouse is the main reason why we can certainly say our solution drives efficiency to our client. Operational costs of the warehouse can be also lower though investing in automated sorters.
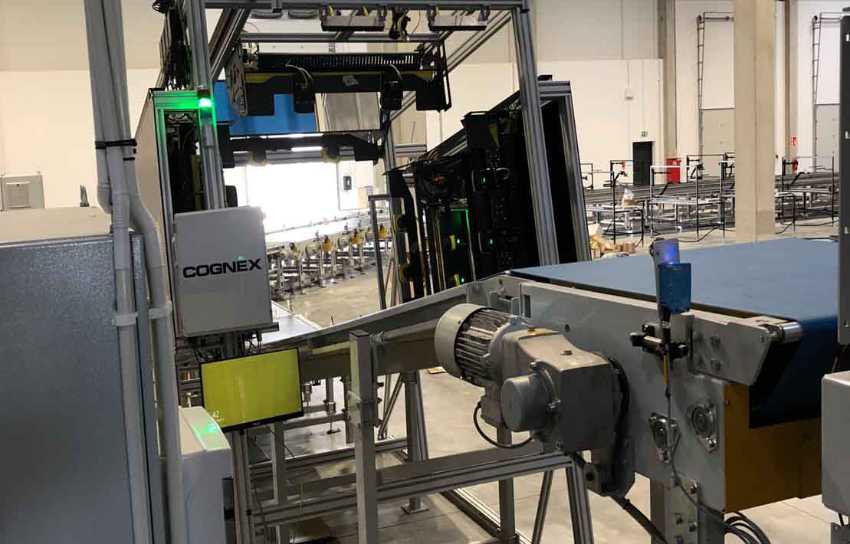
E.E: What are your forecasts for the second half of 2024?
P.W: The second half of 2024 already is very exciting to us. We are starting some of the new partnerships that will hopefully allow us to take part in many exciting projects, focused on implementing automated solutions like sorters, AGVs, scanning workstations all over Poland and beyond. We would like to show the world our experienced personnel and develop to always be up to date with the rapidly changing +market.
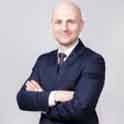
Paweł Wróbel
Managing Director
Tel: +48 571 371 087
Email: pwrobel@stevia-automation.pl
www.stevia-automation.com

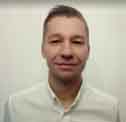
Witold Marciniec
Technical Director
Tel: +48 607 772 921
Email: w.marciniec@p-zm.com
http://www.p-zm.com
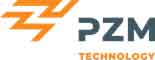