Innovative Collaboration Aims to Revolutionize Thick Section Welding in Shipbuilding
Fincantieri S.p.A., a global leader in high-value ship construction, in collaboration with Castellini Officine Meccaniche S.p.A. leader in production of welding systems, has announced the results of an extensive study utilizing Civan Lasers’ 28kW Dynamic Beam Laser (DBL). The findings of this groundbreaking investigation reveal the tremendous potential of DBL technology to revolutionize welding processes for thick steel sections.
Remarkable Early Results of the Collaboration:
- 40% Increase in Welding Speed: The introduction of DBL technology has drastically accelerated the welding process, allowing Fincantieri to complete projects more efficiently.
- Reduction of Distortion and Heat-Affected Zone (HAZ): Pure laser welding transfers significantly less heat into the workpiece, minimizing distortion and substantially reducing the size of the Heat-Affected Zone, which leads to better mechanical properties.
- 100% Increase in Weldable Thickness: DBLs can weld steel sections over twice as thick as those handled by current methods, expanding possibilities for ship design and construction.
- 60% Energy Reduction: DBL technology offers significant energy savings, reducing costs and supporting Fincantieri’s sustainability objectives.
- 90% Reduction in Filler Material Usage: The need for costly filler materials has been nearly eliminated, drastically reducing production costs.
- Minimized Use of Protective Gases: The requirement for protective gases, a major cost factor in traditional welding, has been reduced to a minimum.
This research exemplifies how Civan’s Dynamic Beam Lasers can be seamlessly integrated into Fincantieri’s production processes, setting a new standard for welding thick steel sections and making shipbuilding faster, more efficient, and environmentally sustainable.
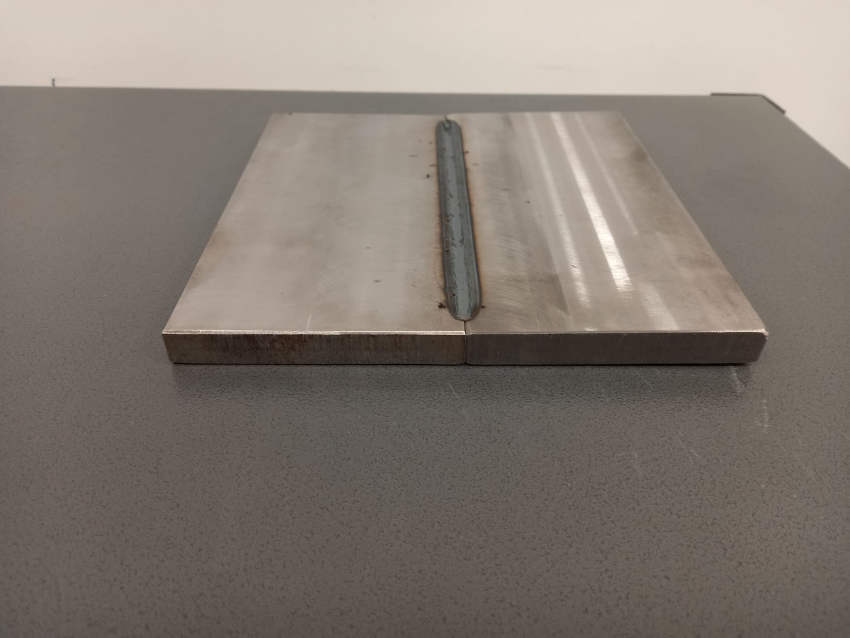
Dynamic Beam Lasers: A Breakthrough in Welding Technology for Thick Sections
Dynamic Beam Laser (DBL) technology is revolutionizing the field of welding, offering solutions to some of the most challenging welding problems and unlocking new opportunities for industries. One of the most promising applications of DBL technology is in the welding of thick sections, where traditional methods fall short. Currently, the most advanced approach for thick section welding in shipyards is hybrid welding, which combines laser and MIG/MAG technologies. However, even this method faces significant limitations.
Dynamic Beam Lasers vs. Hybrid Welding: A Game-Changer for Thick Section Welding
While hybrid welding processes have provided improvements over traditional arc welding, they still come with a range of challenges. These include high heat input, which can cause material distortion, reliance on consumables such as filler rods and protective gases, and the need for complex joint preparation through beveling.
Key Advantages of Dynamic Beam Lasers Over Hybrid Welding:
Minimal Heat Input, Reduced Distortion, and Better Mechanical Properties:
DBL technology introduces far less heat into the welding process compared to hybrid methods, resulting in significantly reduced distortion. This minimizes the need for large fixturing and mitigates the risk of misalignment, simplifying the process. Additionally, the smaller Heat-Affected Zone (HAZ) ensures superior mechanical properties in the welded material, enhancing the overall quality of the weld.
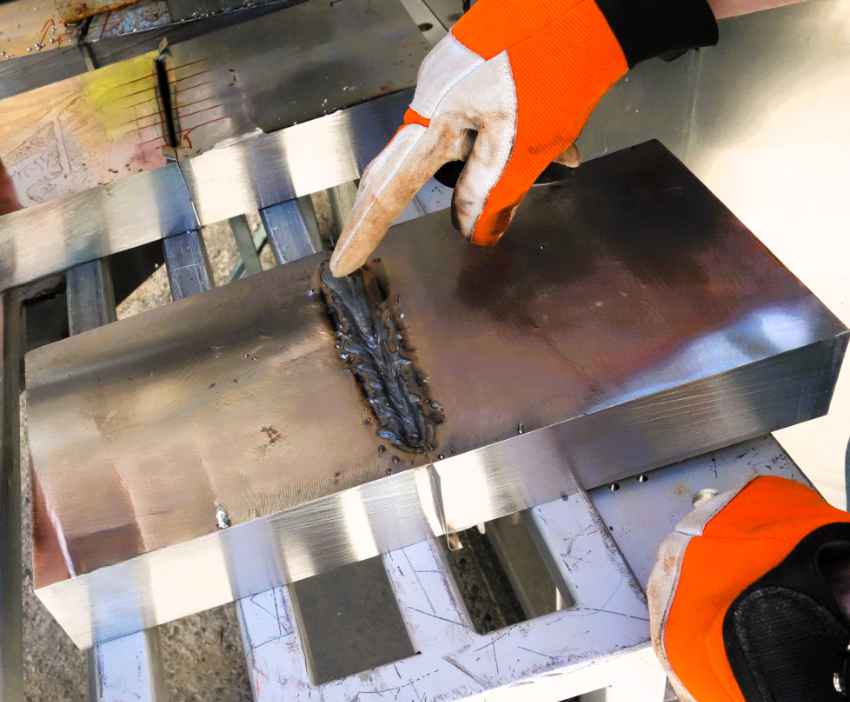
Higher Penetration Depth in a Single Pass:
DBLs offer greater penetration depth, allowing thick materials to be welded in a single pass. In hybrid welding, a single-pass hybrid weld typically needs to be followed by multiple MIG or MAG passes to achieve the desired thickness. With DBL technology its possible to reach up to 30mm in a single pass, making it an ideal solution for welding thick steel plates, particularly in the shipbuilding industry.
No Pre-Heating Required, Faster Process, and Lower Power Consumption:
DBL technology reduces the need for pre-heating, which is often necessary in hybrid welding to ensure proper hardness when welding thick sections. By reducing this step, DBL technology speeds up the process and reduces energy consumption, making it both cost-effective and energy-efficient.