Lagupres was founded in 2004 with the aim of providing basic industrial cleaning services in Tarragona and Barcelona (Spain), two cities with large business environments. The innovative spirit of the team made the company grow and expand their scope of action to the entire peninsula, adding possibilities to their portfolio of services.
Currently, Lagupres has a staff of more than 100 workers. Lagupres is one of the leaders in the Iberian Peninsula, and they are open to work all over the world, mainly in Europe, North Africa and South America.
Given the good work and the success of their actions, since 2018, the company has formed a synergy and they are twinned with the German company Lobbe, a world leader in robotization and industrial services.
Interview with Rafael Feria, Commercial Director at Grupo Lagupres.
Easy Engineering: What are the main areas of activity of the company?
Rafael Feria: Lagupres offers services to any market related to industrial activity: Petrochemical, food, energy, automotive, pharmaceutical, naval, paper, metallurgical and iron and steel industries, as well as work contracted by the public administration.
Each industry requires specific services. We try to offer the best solutions for each of the needs of any of these industrial environments, always related to the industrial cleaning and maintenance of spaces, equipment, or the products themselves in pre-operational objectives.
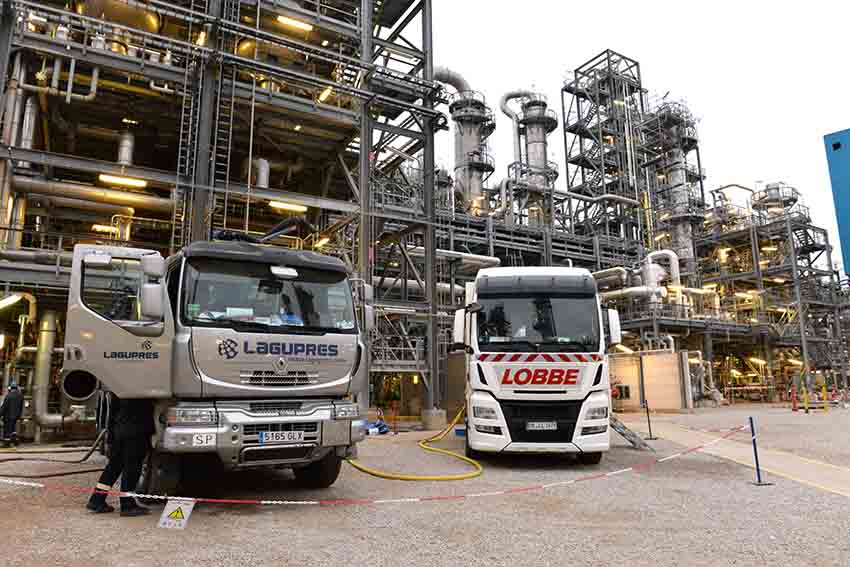
E.E: What’s the news about new products?
R.F: The last service we have added to our possibilities is chemical cleaning by applying solvents in vapor phase. These cleanings are intended for tanks and pipes, heat exchangers, process units, etc.
Its main advantages are:
- Its excellent degreasing capacity.
- We do not need the installation of scaffolding at the work site.
- As it is a dry cleaning, we avoid corrosion processes due to use of liquids
- We avoid the generation of huge quantities of waste.
- We do not need operators inside the equipment in the case of tanks and reservoirs.
On the other hand, for the catalyst loading and extraction activity, we have incorporated the new generation of Edelhoff Life Support Systems (LSS) into our equipment. These systems significantly improve the protection of our employees, the work environment and the traceability of the workflow.
The entire operations process can be digitally monitored and recorded. The data obtained is stored in an external storage system, constantly updated and available for analysis. All our equipment is CE certified and guarantees the perfect functioning of the panic helmets with the breathing air console.
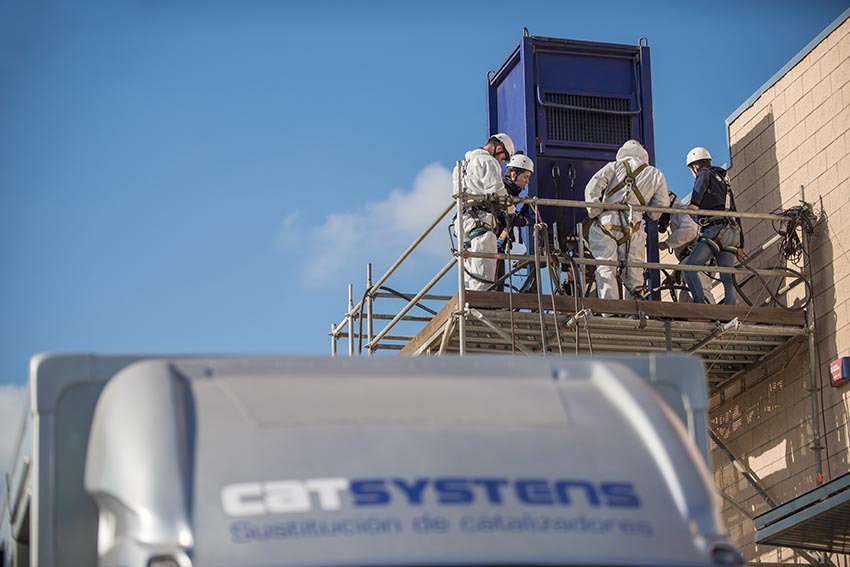
E.E: What are the ranges of products?
R.F: Our main activity is the industrial cleaning and maintenance service. This activity can be divided into 4 large groups: basic industrial cleaning with pressurized water, specialized robotic cleaning and ultra-pressure equipment, chemical cleaning and the loading and extraction of catalysts in an inert atmosphere.
Regardless of the classification, we always offer our customers the ideal cleaning service for each type of industry.
On Basic industrial cleaning, our main services are hydromechanical cleaning, cleaning of urban areas, sewage and wastewater treatment plants and cryogenic cleaning with CO2 pellets.
In terms of specialized robotic services, we can perform ultrahigh pressure cleaning (UHP) or high energy cleaning (HE). We also offer hydro cutting of metals or concrete in explosive areas or hydro blasting of road markings. On the other hand, robotized cleaning of exchangers, tanks, reactors, and columns and pickling and sanitizing of surfaces. Finally, we have the means and equipment to carry out ATEX work in the zero zone.
Within chemical cleaning, we can carry out degreasing, pickling and passivation, oil washing and steam cleaning.
Chemical cleaning consists of carrying out cleaning processes through the recirculation of chemical solutions, with the aim of achieving the optimum pre-operational state of the equipment.
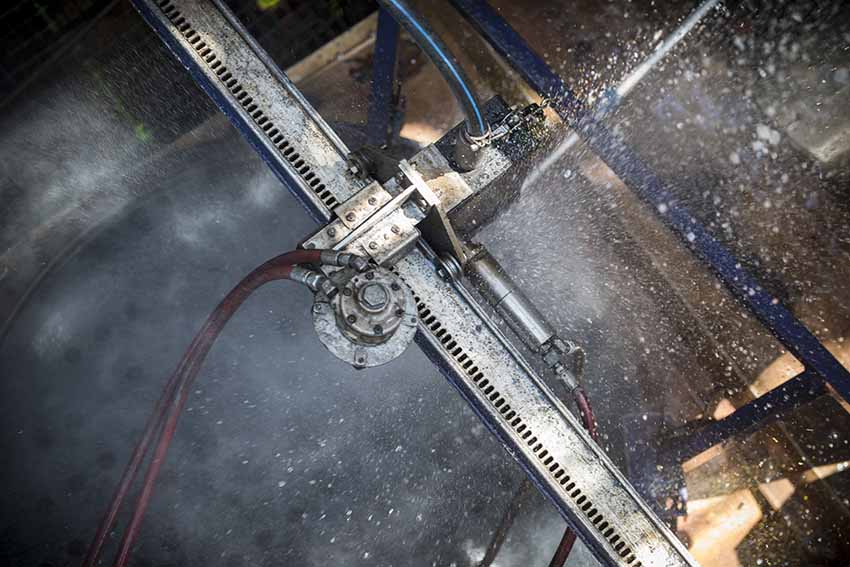
Chemical cleaning has a wide range of advantages over mechanical or hydro-mechanical cleaning procedures. The main situations where we recommend their use are:
- when the disassembly of accessories of the equipment to be cleaned is complex or impossible.
- in long pipes or pipes with many elbows.
- in equipment with apparently inaccessible internal parts.
- in chemical product storage tanks.
The extraction and loading of catalysts, especially in an inert atmosphere, is the main service we perform outside the Spanish territory. The complexity of this service, our ability to carry out the work in complete safety and our structure to reduce execution times, are the main reasons why foreign clients prefer to count on us despite the distance. With this same technique we can vacuum dry and in any environment, all kinds of dusty products
E.E: At what stage is the market where you are currently active?
R.F: Our business is run in a very mature market.
Depending on the size and sector of our customers and their degree of demand, there is a clear advance towards robotization and automation of work processes for the safety of people and the performance of cleaning services.
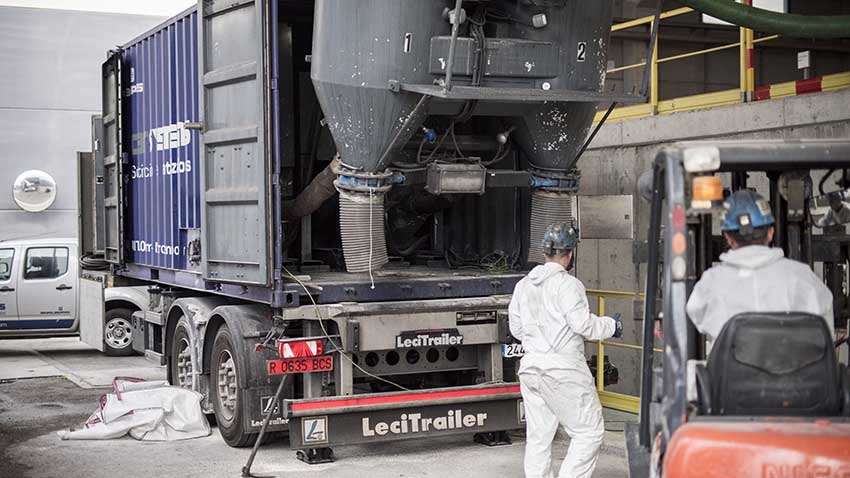
E.E: What can you tell us about market trends?
R.F: The most important trend in our sector is the robotization of processes, with the main objective of reducing safety risks to zero during the execution of work.
With robotization, we eliminate risks such as: working in the front line of fire and the fatigue factor of workers.
In addition, with our 4.0 robots we are able to work in a more constant and uniform way, which leads to greater productivity and quality in the cleaning work finish.
In three words, safety, quality and efficiency.
E.E: What are the most innovative products marketed?
R.F: Currently, our most innovative service is the extraction and loading of catalysts in an inert environment.
We have the most modern equipment and that is why we are starting to work worldwide.
At Lagupres, we have developed and approved our own training courses for work in an inert environment.
This has made us pioneers for having the ideal specialist technicians in these processes
Our work is carried out in two phases. For the unloading of the catalyst, we use suction unloading, using gravity from the bottom. The product is stored in an intermediate silo and then stored in containers.
Once the catalyst has been unloaded, we use the LSS to neutralize and clean the equipment to be loaded.
The loading of the reactors is carried out by means of hoppers and sleeves, minimizing shocks and impacts that may deteriorate the state of the catalysts. We offer two different loading techniques: dense loading or shock loading.
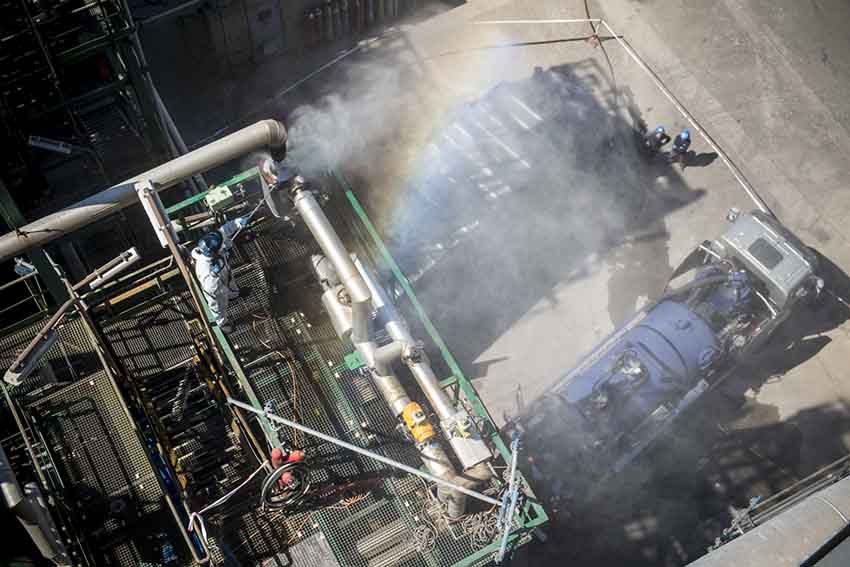
E.E: What estimations do you have for the rest of 2022?
R.F: Currently, with a major global energy crisis, all refineries are producing at record highs.
As the fuel production plants are at maximum production, in the short term it will be necessary to make very rapid interventions, and then, in the short to medium term, when this bubble starts to fall, it will be necessary to carry out very exhaustive maintenance of the installations, which means that we foresee a considerable increase in our ordinary activity.