WASP- World’s Advanced Saving Project is a company born in 2012 in Massa Lombarda (Ravenna- Italy) that designs, produces and sells 3D printers Made in Italy all over the world.
The wide range of WASP 3D printers has been developed to answer human needs: food, housing, health, energy, work, art and culture. Inspired by the Potter Wasp, which builds its own nest with material recovered from the surrounding environment, WASP was born with the aim of developing large-scale 3D printers, to build houses with natural materials and available on the territory. The main company target is to provide effective benefits to humans through technological innovation and research.
In 2012 WASP presented its first printer, the Power WASP, but soon after the company characterized its range with the Delta line of small and large dimensions up to the generation of the Delta WASP Industrial line WASP 3MT, WASP 4070, and WASP 2040.
The Delta WASP Clay line is the market leader thanks also to the experience gained in the architectural field. The new 3D printers Clay optimize the LDM system by 3D printing fluid-dense materials and industrial clays continuously and in large dimensions. In 2021, WASP has presented more technological advancement in the large 3D printers of the Industrial line and Clay line that meet the market demands for the extrusion of bio-polymers, super-technopolymers, recycled materials, pellets, natural material and raw earth, and industrial clay.
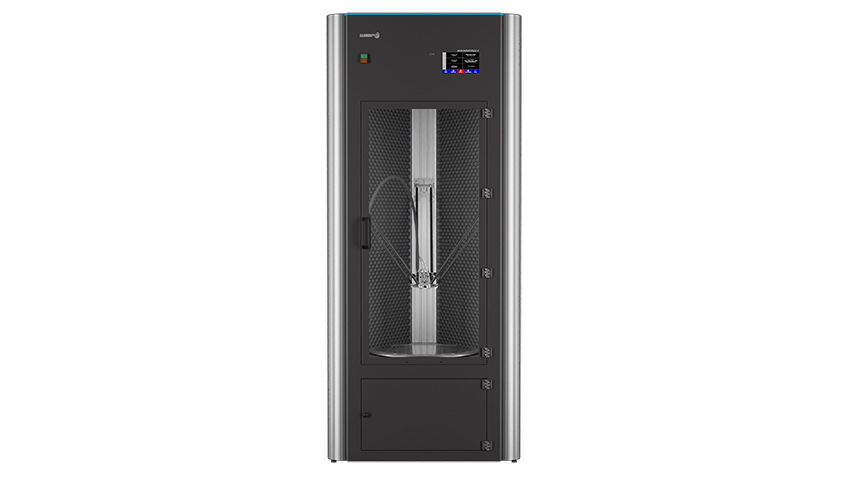
Easy Engineering: What are the main areas of activity of the company?
WASP: WASP designs, produces and sells 3D printers Made in Italy all over the world.
E.E: What are the most innovative products marketed?
WASP: WASP’s approach to 3D printing has always been multidisciplinary. Materials, print size, precision, speed and safety are at the heart of WASP technology. Today WASP leads the way for the future of large-scale printing of a wide range of materials, from technopolymers to raw earth. The new INDUSTRIAL line: two jewels of large dimensions 3MT HDP (HD pellet) and 4070 HDP (HD pellet). These 3D printers have been designed for 3D print with pellets and recycled plastic polymers in granules, in a fast, precise and cost-effective way.
The technological innovations are linked precisely to the HDP extruder that directly prints the granules reducing costs and times and to the feeding of the material which is a pneumatic continuous system, transported in an intelligent way and controlled by a capacitive sensor. In addition, the patent pending Firecap system generates a localized hot chamber up to 250 ° directly on the printing area without overheating the mechanics, allowing optimal printingand layer adhesion. The VAC (Vacuum Active Control) system, a vacuum printing plate, which allows the plate to be replaced in a few seconds, ensures the total absence of micro-movements during printing even at high temperatures. Three more jewels of additive technology can be found in this stand, the 4070TX (PEEK) designed to print technopolymers such as PEEK in large sizes, which, in addition to the Firecap, mounts another patent for Inline drying of the filament;the 4070 FX (Flex Extruder) which prints soft materials up to 50 shore A and the 4070 ZX (Zen Extruder) which prints industrial materials such as PA Carbon.
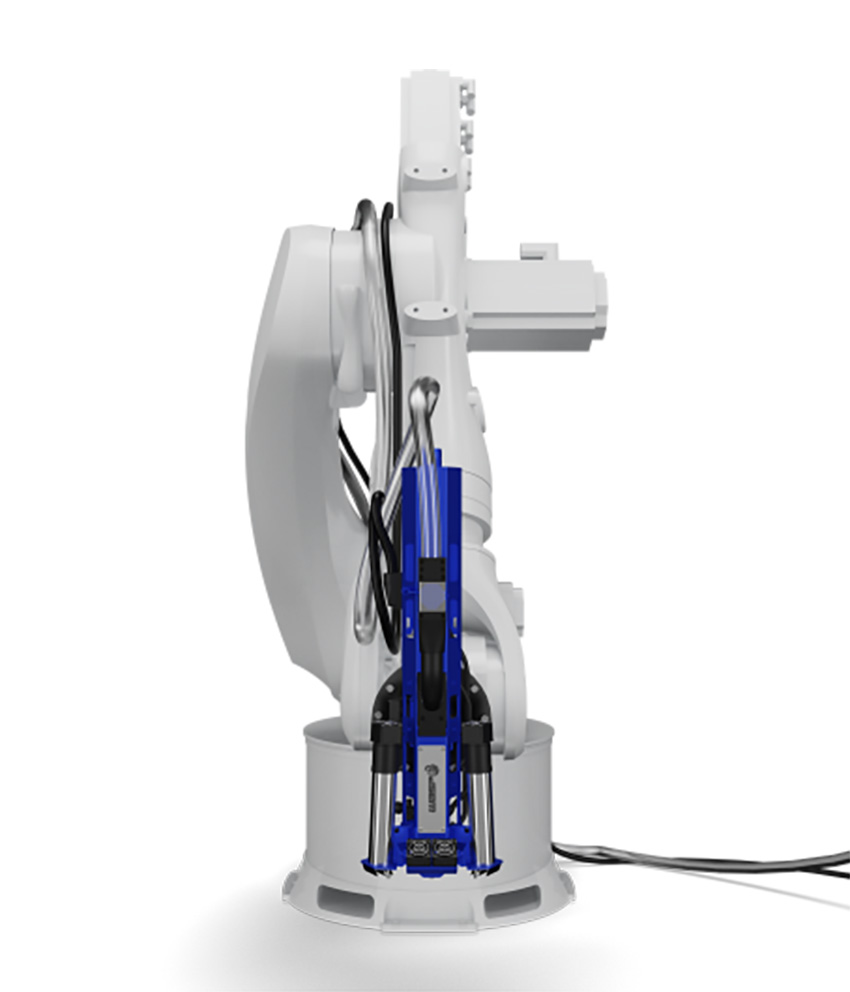
The LDM technology and the new CLAY line: a new 3D printer WASP 40100 INDUSTRIAL CLAY called “the collaborative 3D printer”, extrudes industrial clay and prints prototypes for the automotive industry, which can be finished by hand and reprinted countless times if necessary. A paradigm shift in the modelling prototyping process applicable to many other industrial fields. The new WASP 40100 CLAY CONTINUOUS FEEDING machine is another patent designed by WASP to print clay in large format thanks to a continuous material feeding system equipped with a 10l. tank. An attraction for Universities and Research Centers is certainly the CRANE WASP, a building printer that built the first internationally renowned housing modules in raw earth and natural materials, called GAIA, TECLA and the recent Dior concept stores in Dubai.
Lovers of robotic arms will be satisfied with the two WASP solutions, ROBOTIC ARMS 3D PRINTING for fluid-dense materials, such as concrete and plastic granules.
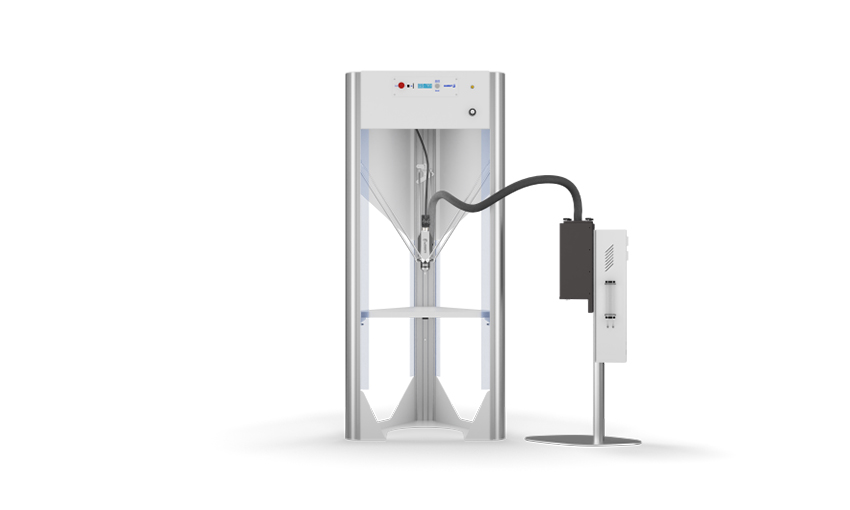
E.E: What estimations do you have for 2022?
WASP: The pandemic has accelerated trends that were already strongly underway: automation, digitization, while also introducing more urgency toward some other ones—such as supply chain resiliency, on-demand short batch production, re-localization—that were also in the works. Our innovations are declined on materials and we have designed and produced large 3D printers s on specific materials. We believe in large dimensions and in the future of materials. We are confident of the considerable development of this Additive Manufacturing market all over the world.