Ecopneus scpa is the non-profit company for the tracking, collection, processing and final destination of end-of-life tyres (ELTs) created by the major tyre manufacturers operating in Italy (Bridgestone, Continental, Goodyear Dunlop, Marangoni, Michelin and Pirelli). In the course of time many other companies have joined our network. Under Art. 228 of Legislative Decree 152/2006, tyre manufacturers and importers are indeed obliged to ensure the management of a quantity of ELTs equal in weight to that which is placed on the replacement market in the preceding calendar year, based on the Extended Producer Responsibility – an organizational model adopted by the majority of the European Countries. Our goal is to manage every year an average of 200,000 tons of End of Life Tyres in Italy.
Interview with Federico Dossena, General Manager of Ecopneus.
Easy Engineering: What are the main areas of activity of the company?
Federico Dossena: When a tyre is no longer sufficiently safe or efficient to be reused, even if retreaded, it is termed an “end-of-life tyre” – that is, waste – and must be collected and recovered in specific plants. The rubber the tyre is made of is, indeed, a mix of very high-quality polymers with exceptional chemical-physical characteristics, which remain unaltered even in the recycled rubber obtained from it.
ELTs may be channelled towards one of two different processes: recycling, whence new materials such as rubber, steel and textile fibres are obtained, or recovered as energy in ad hoc plants, mainly cement factories. Indeed, ELTs have the same calorific power as coal, but with much lower climate-changing emissions.
For material recycling, ELTs are sent to specific plants. By the means of mechanical shredding at room temperature these plants reduce ELTs in smaller and smaller pieces, until the separation of the three tyre components, rubber, steel and textile fibre, is achieved. Together with the management activities of collection, transportation, treatment and recovery of ELTs, we are also strongly committed to promote the applications for recycled rubber, as well as initiatives of information and awareness raising for the creation of a “recycling culture”.

E.E: What are the ranges of products?
F.D: Recycled rubber is used to create innovative eco-sustainable products in a wide range of sectors. From the products for the building industry, such as acoustic insulation and anti-vibration elements, to sport, with playgrounds, football pitches, and multi-purpose sports flooring. There is also the sector of roads and infrastructures where, next to silent and long-lasting “modified” asphalts, we can find cycle lanes, street furniture and items for road safety. Animal wellbeing, design, objects and new compounds made by combining recycled rubber and thermoplastic materials complete the range of products available.
E.E: At what stage is the market where you are currently active?
F.D: In Italy, the environmental consciousness is constantly growing, however our goal is to increase even more the demand for products made with recycled rubber, which represents the only sustainable closure of the end of life tyres “cycle”.
Many steps forward have been made in the last years, even so the road is still long. We are constantly working with our supply chain, with the industry and also with Research Centre to create a breeding ground for an increase of recycled rubber applications and products. Institutions must be involved and support this process with regulations aimed to encourage and increase the use of recycled materials.
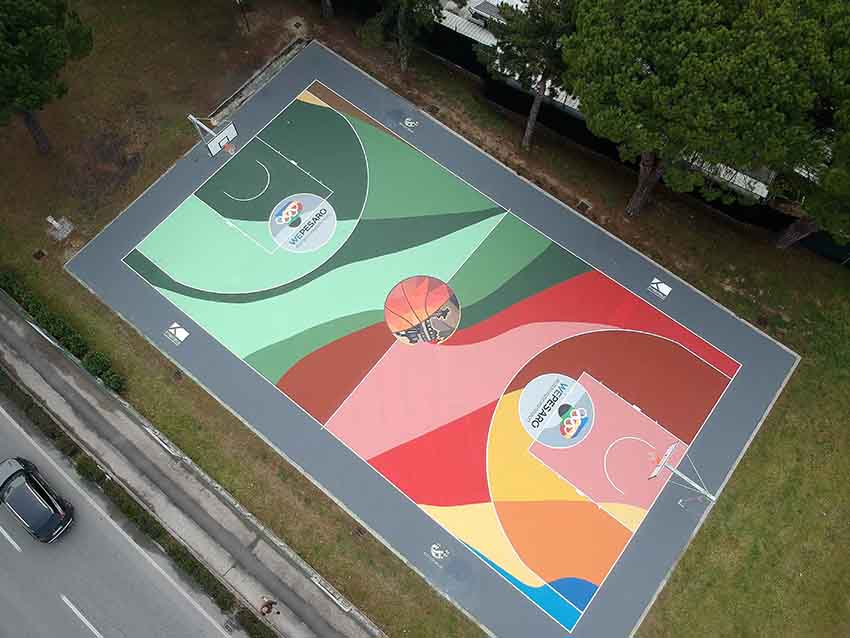
E.E: What can you tell us about market trends?
F.D: The sportive sector is one of the most strong and dynamic; today it absorbs about 30% of the recycled rubber from the Ecopneus’ system. We’re observing an increase in padel playground, a sport that is experiencing an enormous growth in our Country, and we expect that 2022 confirm this trend. Modified asphalt is another recycled rubber application which is growing constantly, but not as much as it might be: to date we have about 670km in Italy paved with modified bitumen compared to more than 800,000 km of conventional asphalt. It’s a pity if we think about the real advantage it can bring to our road and our health: by adding rubber powder to asphalt bitumen, it is possible to obtain a road surface with better mechanical performances than a conventional one. Moreover, these mixes can reduce the noise generated by the passing of vehicles. It is not a secondary aspect, considering that 1/5 of the EU population is exposed to excessive noise levels and, according to the World’s Health Organisation, noise pollution causes over 10,000 premature deaths every year in Europe. This technology was developed in the USA at the beginning of the 1960s and it has gradually spread all over the world. In Italy, it has been tested for over 15 years.
E.E: What are the most innovative products marketed?
F.D: In February we inaugurated an innovative basketball court in the city of Pesaro, in the Marche Region, which is made with over 3.200 kg of recycled rubber. In basketball, it is necessary to be able to rely on floorings that faithfully recreate the feeling of the return of energy upon jumping. They must also be able to guarantee shock absorption without being excessively “elastic”, as this aspect would affect the athletes’ weariness, thus compromising their performance.
The system installed in the Pesaro playground also meets the requirements of the FIBA (International Basketball Federation) and in the future it will be subjected to homologation to be able to host official international competitions as well. The field was created with an innovative mat in recycled rubber with an innovative “honeycomb” shape produced by the company Progeplast, then installed by the specialized company Waterproofing which finally applied the surface resins and the game lines.
The project has been carried out thanks to the collaboration of Giacomo “Gek” Galanda, ex-captain of the Italian National Basketball team and currently advisor with the Italian Basketball Federation. Thanks to his experience as a professional athlete at the highest levels for many years, Galanda personally tested several sports surfaces in recycled rubber and the court in Pesaro is the synthesis of the best characteristics and performances of each one of them.
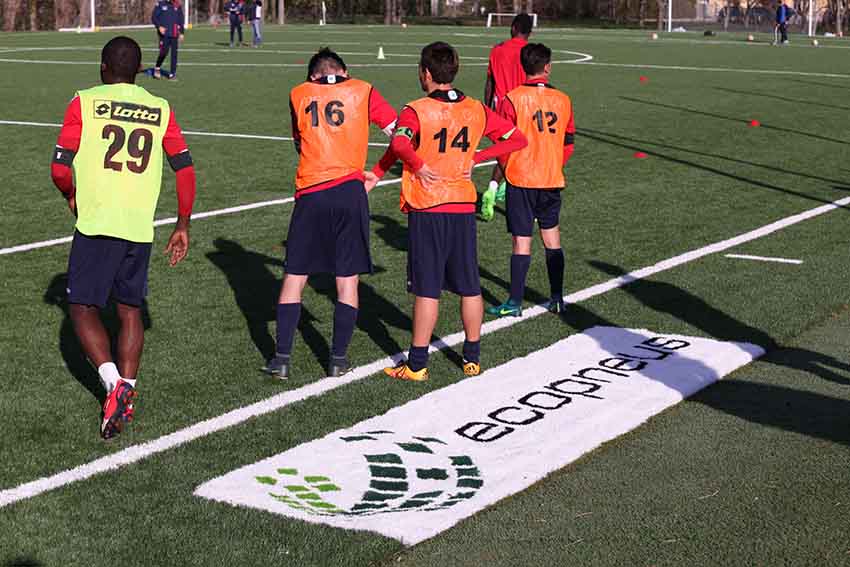
E.E: What estimations do you have for 2022?
F.D: I’m sure that 2022 will be a great year. On one hand, we are confident not only to reach but to go beyond our legal target of ELTs collection, avoiding any environmental risks and assuring a continuous and capillary collection service to the over 26.000 tyre fitters reached all over Italy. On the other hand, we hope to see a constantly growing of the applications and products made by recycled rubber, focusing on modified asphalt and basketball playground, two applications with a great potential for expansion.