A development project that has been underway for a long time at Kolzer has given the desired results and even something more.
This Italian company, engaged for 70 years in the production of PVD machines for vacuum metallization and sputtering, has allocated special resources, skills and extensive experimentation to the development of a new and effective industrial solution that has long been part of its business objectives. We are talking about the enhancement of the mechanical and chemical characteristics that can be reached with our PVD Sputtering machines, the result: the birth of PVD 2.0 Sputtering.
THE FUNDAMENTALS OF PVD SPUTTERING TECHNOLOGY
Sputtering is a deposition method that belongs to the category of physical vapor deposition (PVD) methods.
The PVD technique has long been established and widely used to apply a thin coating on an object with the aim, among others, of enhancing its tribological properties and improving its aesthetic appearance.
The PVD process, which operates in a high vacuum environment in the presence of argon (or another inert gas), involves the atomization of the material from a solid source, called “target”, and its subsequent deposition on the substrate, forming a coating that grows atom by atom.
In the “sputtering” process, a magnetron is placed close to the target. The magnetic field that is created causes the electrons to spiral along the magnetic flux lines near the target instead of being attracted to the substrate. The advantage of this system is that the plasma remains confined to an area close to the target, without causing damage to the thin film being formed. Additionally, electrons travel a greater distance, increasing the likelihood of further ionizing argon atoms. This tends to generate a stable plasma with a high ion density. A greater number of ions means more atoms expelled from the target, with a consequent increase in the efficiency of the sputtering process. The faster ejection rate, and therefore the higher deposition rate, minimizes the formation of impurities in the thin film, and the greater distance between the plasma and the substrate minimizes the damage caused by stray electrons and argon ions.
PVD Sputtering is the most flexible, current, reliable and environmentally friendly method to deposit a thin metal film, giving the product aesthetic and mechanical performance.
The process is carried out under vacuum to deposit metals and alloys with high efficiency on any type of substrate and to ensure uniformity as well as functionality.
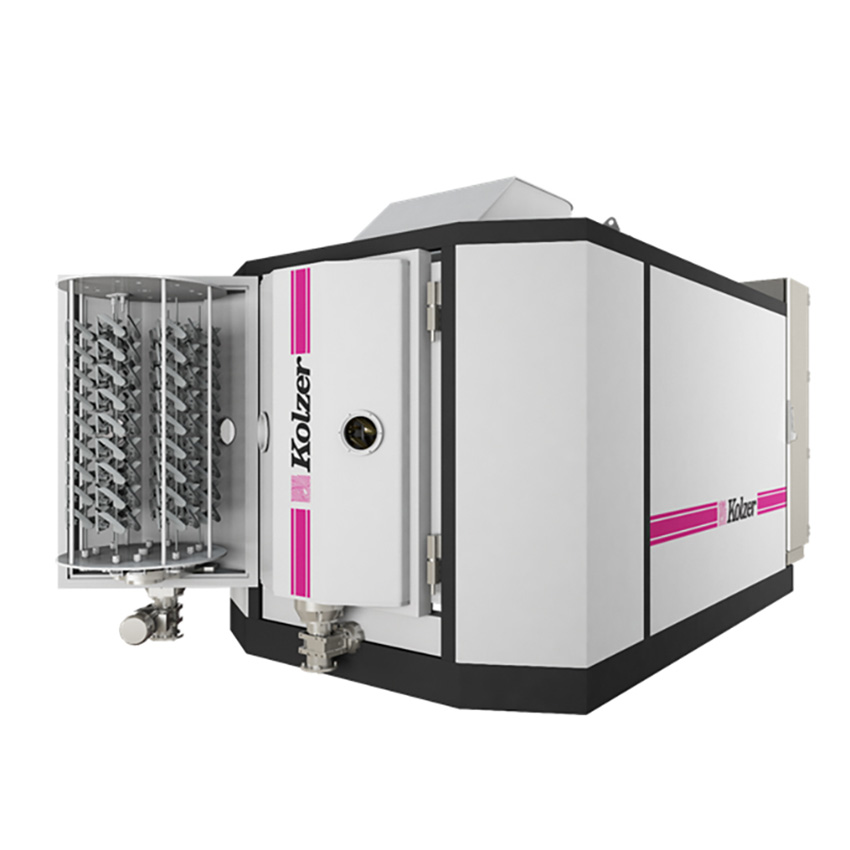
The machine MK 34 PVD 2.0
The range of achievable colors is very wide, as are the variants of gloss.
Coatings are inexpensive are obtained at room temperature. The cycles are repeatable, so after the initial setup there are no production waste problems.
The machines are compact, easy to run and manage.
With the new generation PVD 2.0 process all these strengths are maintained.
HOW THE NEW PVD 2.0 COATING IS OBTAINED
The PVD 2.0 process uses long magnetic pulses (up to 3.0 msec) with power of the order of hundreds of KW on the cathode. This gives the atoms high energies so as to project them onto the surface layers of the substrate, depositing dense, adherent coatings, free of surface defects and very hard (> 30 GPa) and with an increase in Young’s modulus (> 368 GPa).
The new Kolzer machine PVD 2.0 mod MK 34” brings together all the performance characteristics to classify it as the innovative and optimal solution for many metal components.
On which substrates
Virtually all metals can be coated with the PVD 2.0 technique: aluminum, brass, carbon steel, stainless steel, zamak, etc.
The possibility of a wide range of colors on stainless steel components is particularly interesting.
Quali sono i vantaggi del nuovo processo
A new chapter is truly opening: the PVD 2.0 coatings obtainable with the innovative Kolzer MK 34 system are morphologically dense and free from defects.

The control of the microstructure guarantees perfect adhesion to surfaces. The result is a compact and extremely smooth coating at the atomic level, resulting in new performance frontiers in the mechanical and chemical fields, with a consequent improvement in resistance to corrosion, chemical agents, hardness, mechanical and tribological properties, etc.
Kolzer positions this recent PVD 2.0 proposal at the highest performance levels of classic PVD machines and also capable of surpassing those of arc PVD.
In some cases Kolzer has also experimented with overcoming the traditional sequence of treatments, reducing and simplifying the phases, thus allowing a further significant contribution to the cost-effectiveness of the process.
In other cases, the anodic oxidation / PVD 2.0 integration has allowed the achievement of previously unthinkable performances.
Surely this renewed and enhanced technology is able to offer companies prepared and aware of their objectives, even more revolutionary results and significant functional and aesthetic satisfactions.
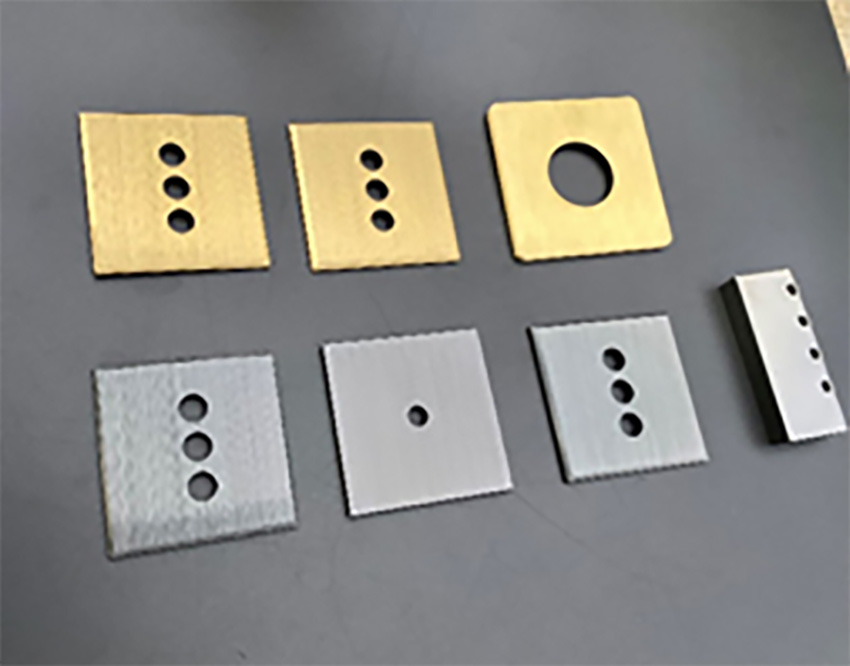
Finished parts with aluminum substrate
Process integration
This is a very important point: PVD 2.0 can be particularly integrated with existing galvanic chrome plating And anodizing processes, even improving their performance. So the actors who can interpret and maximize the new potential offered by the machines are practically the same. Naturally, the novelty also concerns the end users integrated internally with traditional galvanic systems.
Examples of coatings | |
Application | Coating |
Corrosion resistance | CrN / NbN |
Resistance to oxidation | CrAlYN / CrN, Ti-Al-Si-N, Cr-Al-Si-N |
Optical systems | Ag, TiO2, ZnO, InSnO, ZrO2, CuInGaSe |
MAX phases | TiSiC |
Microelectronics | Cu, Ti, TiN, Ta, TaN |
Hard coatings | Carbon nitride CNx, Ti – C |
Hydrophobic surfaces | HfO2 |
The range of colors
Next to the relevant “performance” strengths, the palette of colors is very broad, capable of satisfying the ever-increasing demand for new chromatic variations. More and more often, in fact, companies choose to distinguish with innovative and special colors, “high range” products that require high visibility, as well as simple components, with the aim of updating the aesthetic impact of their products.
What are the sectors of use
Faced with this very important innovation, it is not easy to delineate and circumscribe its areas of use. First of all, let’s think of mechanics in general where each reality will be able to evaluate and interpret the extent of this novelty according to its own productive experience and personal strategic plans. Among the references in evidence, we have: high fashion accessories, taps, handles, components for hydraulics and pneumatics, automotive components, tools, hardware accessories, etc.
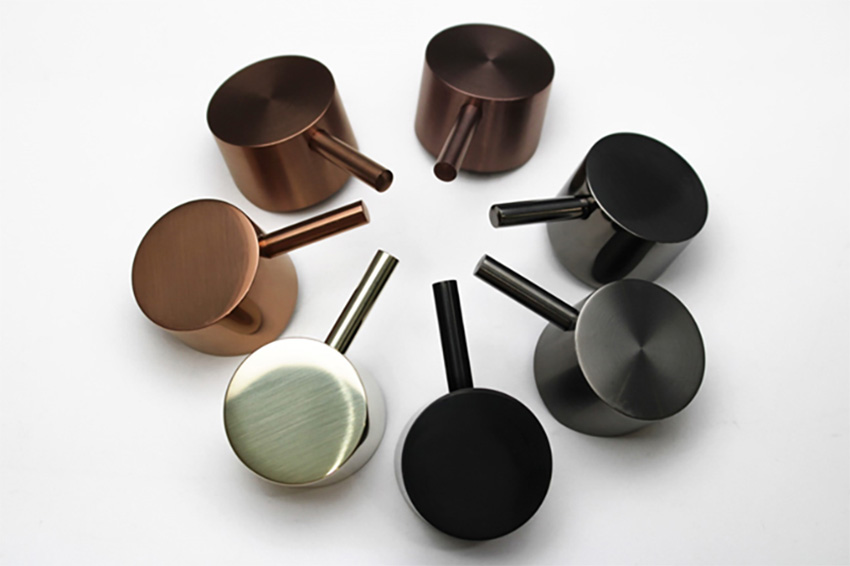
Launched in 1952 by Guido D’Esposito in a small laboratory in Milan, Kolzer produced machines mainly dedicated to the metallization of aesthetic details in plastic (Christmas decorations, perfume caps, reflectors, etc.).
Born as an artisan company, it was soon promoted to industry thanks to the tenacity and foresight of its founder.
The same qualities that we find today in the second generation D’Esposito which, with the addition of a visionary instinct, make Antonio and Davide two modern entrepreneurs with an eye to the future beyond the predictable.
Hence the desire today, at the current headquarters in Cologno Monzese, to operate a significant expansion by adding 3,000 square meters dedicated not only to the production of machines but also to the impulse of the laboratory. The new pole includes a PVD investigation and competence center set up with five TEST machines for various types of PVD coatings as well as equipment to complement the coating diagnosis and process.
For about 20 years Antonio and Davide have been carrying on the culture of PVD machines born 70 years ago, innovating, experimenting and patenting processes that have rightfully positioned them among the leading exponents in the world of PVD plasma.
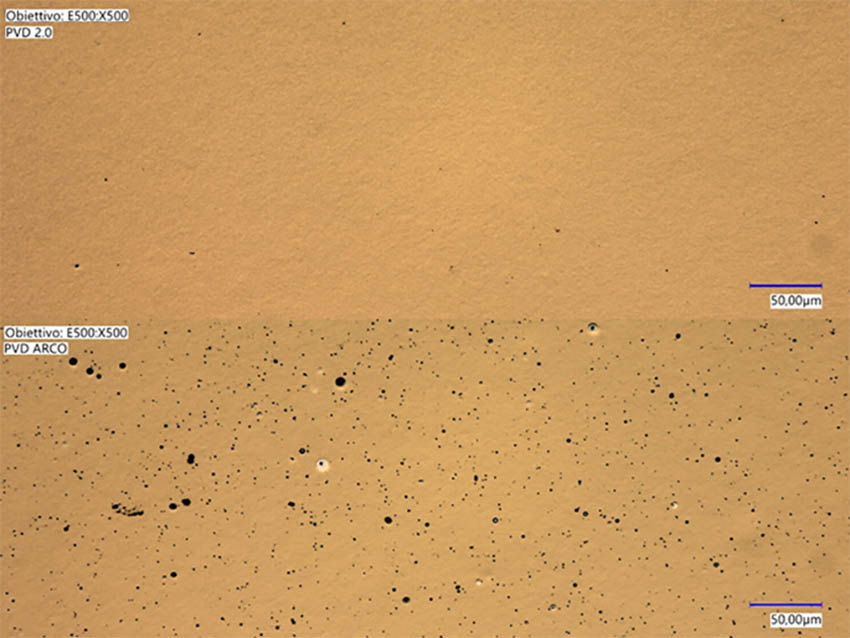
Today Kolzer represents the best Italian plant engineering answer to PVD technology as an industrial application competence. It produces and supplies vacuum treatment plants, i.e. in conditions of low atmospheric pressure, where the density of the gaseous particles is reduced and the environment in which the processes take place (treatment chambers) becomes uncontaminated.
It offers considerable concentration and strategic vision on solutions capable of allowing customers a considerable technical / technological leap and “get out of the fray”.
The many years of experience with over 1300 machines sold and installed allows it to have a wide and complete overview of surface treatments in various fields of application.
Kolzer offers qualified Engineering for the supply of machines, from the “Compact production station” for small and medium-sized companies, up to in-line processes for high volumes or large items.
Sputtering PVD 2.0 is the most recent example of the innovative effort of this company which has been able to position the world of metal surface finishes at the highest performance levels, confirming at the same time all its aesthetic qualities.