Forward AM is the brand of BASF 3D Printing Solutions GmbH which provides 3D printing materials and solutions along the entire additive manufacturing value chain. From consultancy and development through customized design to digital simulation and prototype printing to completion with finishing and exhaustive component testing, the team provides customers with exactly what they need. No matter the material required for a specific project, Forward AM offers the world’s largest selection of 3D printing materials and service solutions.
Interview with Martin Back, Managing Director, BASF 3D Printing Solutions GmbH.
Easy Engineering: What are the main areas of activity of the company?
Martin Back: We at BASF Forward AM invest in research and development, as well as in business development of the industrial and functional application of 3D printing. Together with our numerous specialist industry partners, new materials, integrated system solutions and cutting-edge services are developed continually. We also have BASF R&D laboratories located in Ludwigshafen (Germany), Lyon (France), Shanghai (China), and Wyandotte (US).
Our expansive Material Portfolio includes:
Ultrasint® Powders for Powder Bed Fusion (PBF). Our Forward AM Ultrasint® powders set new standards in 3D printing using polymer powders that enable a variety of possibilities for advanced applications, from functional prototyping through to end-use serial production parts. These materials fulfill the highest quality standards and are designed for ease of use on most common printing equipment. We also offer expert technical support and the full spectrum of services from design and simulation through to post-treatment of printed parts.
Ultrafuse® Filaments for Fused Filament Fabrication (FFF) – Our Fused Filament Fabrication (FFF) provides an extensive range of materials offering a variety of beneficial material properties such as ease of print, dimensional stability, durability, and flexibility. Whether its standard filaments, filaments for high temperatures and engineering or filaments for temporary support material, the product range Ultrafuse® offers applications for both Bowden and direct-driven extrusion systems.
Ultracur3D® Photopolymers – Our Ultracur3D® reactive urethane photopolymers deliver class-leading performance and consistency to meet specific application needs, while also accelerating design iterations and cutting development costs. Based on BASF’s decades of experience in polyurethane research and production, the Forward AM range of advanced photopolymer resins and solutions delivers long-term UV stability and structural performance far superior to conventional photopolymers.
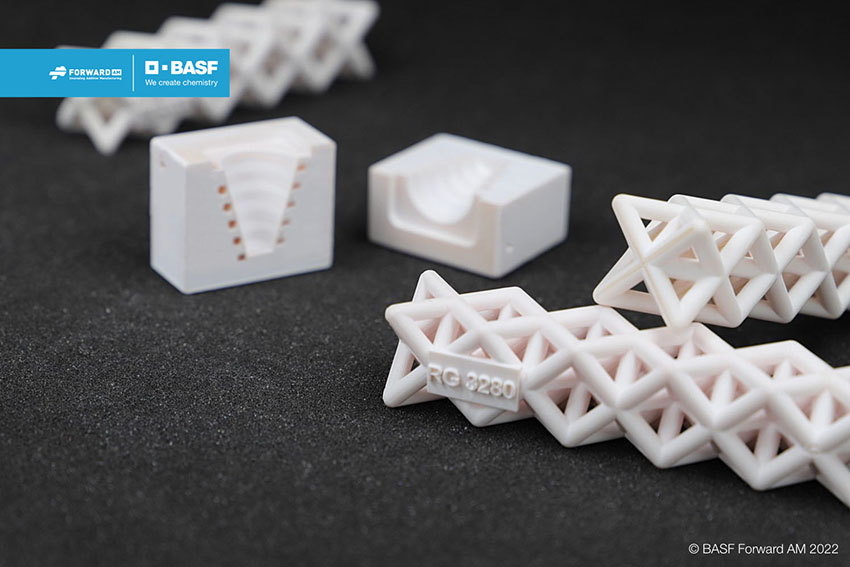
E.E: What’s the news about new products?
M.B: At Formnext 2022, we were excited to launch three new materials and continue to expand our Portfolio with additions to our powders and photopolymers. They are:
Our Ultrasint® AP26 was launched in partnership with Cipres and is a zero-waste material with affordable cost and high detail resolution enabling high volume applications. With a 100% reusability rate and the lowest cost per kg in the PBF portfolio the new PBT is therefore an ally for sustainability that offers the sharpest detail quality while assuring the lowest cost.
Ultrasint® PP 1400 Black, launched in partnership with RPM, finally brings an easy to process PP material to the market. The low density, high reusability rate, and end part recyclability delivers what others can’t, the ability to create a sustainable end part from a high-quality isotropic material.
Our Ultracur3D® RG 3280 offers superior stiffness and temperature performance while being low-viscous, easy to use and fast printing, with material qualities including excellent stability of suspension which results in limited settling in the vat.
E.E: What are the ranges of products?
M.B: The Forward AM team strives to design durable materials and complete solutions for the industrial-scale manufacturing of end products for a variety of industries such as automotive and aerospace, consumer goods as well as in the medical and dental sectors. And many of our potential customers are companies that intend to use 3D printing for industrial production.
E.E: At what stage is the market where you are currently active?
M.B: The industrial 3D printing market is expected to reach a value of $107.7 billion by 2031 according to the recent study released by Allied Market Research. This represents a Compound Annual Growth Rate (CAGR) of 21.9%. This large-scale projected growth is influenced by two main issues: the demand for customized products to gain a competitive advantage and the rapid adoption of 3D printing materials. Industry experts also point out that there are some obstacles to overcome in order to see a wider adoption of 3D printing. These can include the increased costs associated with production line or manufacturing changes and potential need for skilled professionals to work the technology. At Forward AM, we are committed to working with our customers as a partner to ensure that as the 3D printing market grows and changes we can and will continue to provide innovative materials and processes to support their Additive Manufacturing goals.
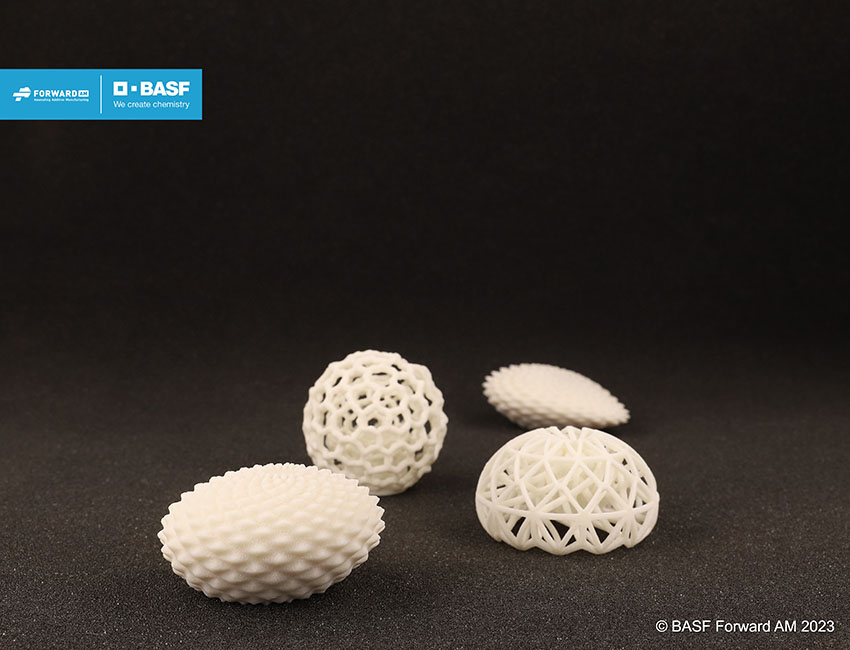
E.E: What can you tell us about market trends?
M.B: In looking at the State of 3D Printing for 2022, we can see that Additive manufacturing confirms its position as a genuine manufacturing solution used for Research, Education, and R&D for end-use purposes. We can also see that most use additive manufacturing when they need less than 1 000 parts. This technology offers considerable advantages in developing projects that create few parts. “Power Users” are a particular segment of Additive Manufacturing users who have more experience with the technology and are more mature in their use of this technology, which tends to lean more toward end-use/functional parts at 69%, R&D at 66%, and tooling at 49%.
Part optimization is also a growing focus for 3D printing users. One fourth of users use additive manufacturing to accelerate their product development process, which aligns with the strong use of additive manufacturing for proof of concepts and prototypes. Regarding the choice of 3D printing materials for their projects, users are looking for accuracy, specific technical properties, and a cost-effective option. More sustainable materials are also important for 81% of 3D printing users.
E.E: What are the most innovative products marketed?
M.B: Ultrasim® 3D Lattice Design works to optimize parts to their fullest capacity. 3D-printed lattices are repeated patterns comprised of a network of cells, beams, and nodes. These 3D-printed micro-architectures unlock entirely new designs that are considered impossible to produce with traditional manufacturing methods. This pioneering design and production process utilizes only one material with a whole range of different mechanical properties by finetuning the combination of lattice characteristics leading to higher comfort, better rebound, increased aeration, and reduced weight. Lattice characteristics include lattice type, cell size, beam diameter and aspect ratio. From these basic parameters, millions of options can be easily created.
With all the different types of lattice options to choose from, it can easily become overwhelming. Because not all lattices make sense to use for any given application, BASF Forward AM has developed a lattice library to understand the different mechanical performances of different lattice types. We offer three different Ultrasim® 3D Lattice Test Pads – Footwear, Seating, Protection – with all being compatible with our Ultrasim® 3D Lattice Engine. This newly launched service goes even a step further and combines BASF lattice know-how with Hyperganics´s Algorithmic Engineering into one easy-to-use software. It allows for the generation of lattice designs by the user in an instant. The team at Forward AM has worked to incorporate the know-how into the touch and feel versions with our Ultrasim® 3D Lattice Test Pads provide our customers the ability to physically experience the wide range of properties lattices we can achieve.
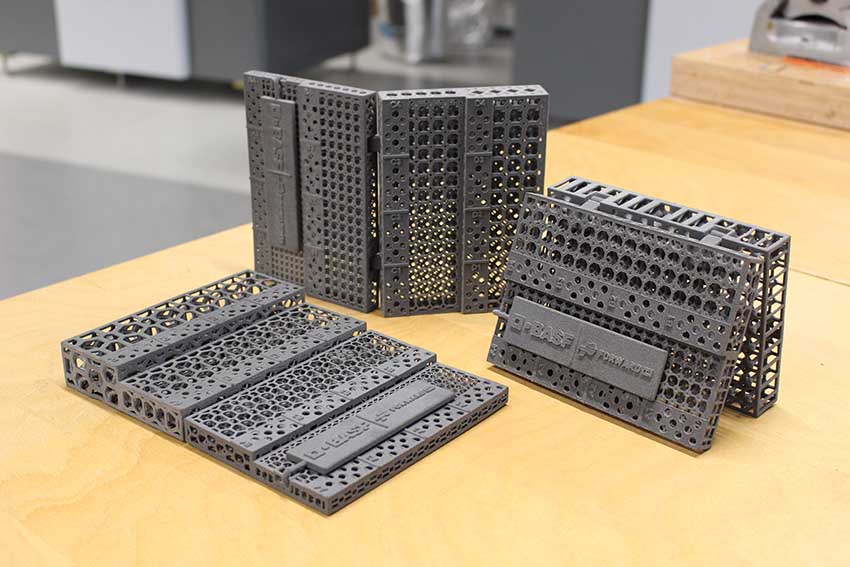
E.E: What estimations do you have for the rest of 2022?
M.B: I’m excited to lead the efforts of the whole Forward AM team to build a strong strategy and process foundation for our continued success. In this new decade, we want to further build Forward AM as the industry leader and remain an innovative partner for our customers. As a team, we remain motivated and driven to provide our customers with high-quality materials and services to help them achieve the best possible 3D printing application to meet their needs and sustainably grow their business.