In modern industry, automated processes and efficient material transport are of central importance for increasing productivity and optimizing production processes. Transfer systems such as Montech AG’s LTE and LT40 play a crucial role in this process, enabling smooth and precise transfer of workpieces and goods between different workstations.
The Swiss technology company Montech AG specializes in the industrialization and standardization of state-of-the-art, unusual belt conveyors, transfer systems, and innovative aluminum framing systems. Its advanced LTE and LT40 transfer systems are characterized by their great precision, flexibility, and energy efficiency.
The LTE Transfer System
The LTE transfer system is an innovative single-belt system for workpiece conveying in industrial manufacturing processes. With a speed of 7.7 to 19 m/min, it automates the transport of materials between different workstations.
The workpieces are securely fastened to standardized workpiece carriers, which are available in four sizes and in an anti-static version. This ensures reliable and precise movement of workpieces throughout the entire production process. The maximum payload is 5.3 kg. It is therefore suitable for the transport of small and medium-sized products.
The workpiece carriers are deflected using fixed and movable 90° curves and fixed 180° curves. Movable curves can have a drive or not. With the help of bypass belts, it is also possible to create offline stations. Here, too, the flow of workpiece carriers is controlled with moving curves.
The most common applications are for automation, assembly, and logistics.
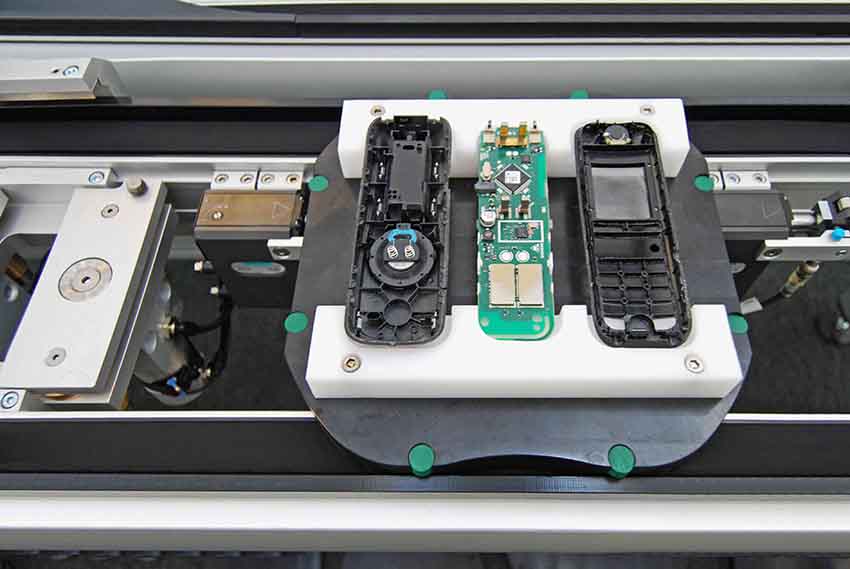
The LT40 Transfer System
The LT40 transfer system is a double toothed belt system that transports workpiece carriers at speeds of up to 20 m/min. There are three sizes to ensure optimal configuration for different applications. The workpiece carriers are available in six sizes and in an anti-static version and can be equipped with RFID for identification at any time. The maximum payload is 16.8 kg.
These belt conveyors are fitted with the desired components and assembled according to customer requirements, which enables smooth integration into existing production lines. The workpiece carriers are deflected by transverse deflectors, 90° deflection, 180° deflection, or turnout. The damped pneumatic separator/stopper enables workpiece carriers to be stopped, separated, and slowed down. The components can be adjusted easily and infinitely thanks to the dovetail guide.
For processing on the workpiece carrier, there are various options, including an integrated indexing device, a positioning device with 1000 N support force, and a mounting device for up to 60 kN vertical load. The transfer system can also be extended to include a lifting/rotating unit or lift depending on customers’ needs.
The LT40 transfer system ensures precise material transport with efficient drives and meets high energy efficiency and precision requirements. The motors are optimized for efficiency and exceed the minimum requirements of the EU efficiency class IE2. Even in comparison to the highest efficiency class IE5, the drives for Montech’s belt conveyors are up to 10% more efficient. This helps you reduce energy costs substantially.
Differences between the LTE and LT40
The LTE and LT40 transfer systems are both versatile and they address a wide range of needs and requirements. They differ in three main points:
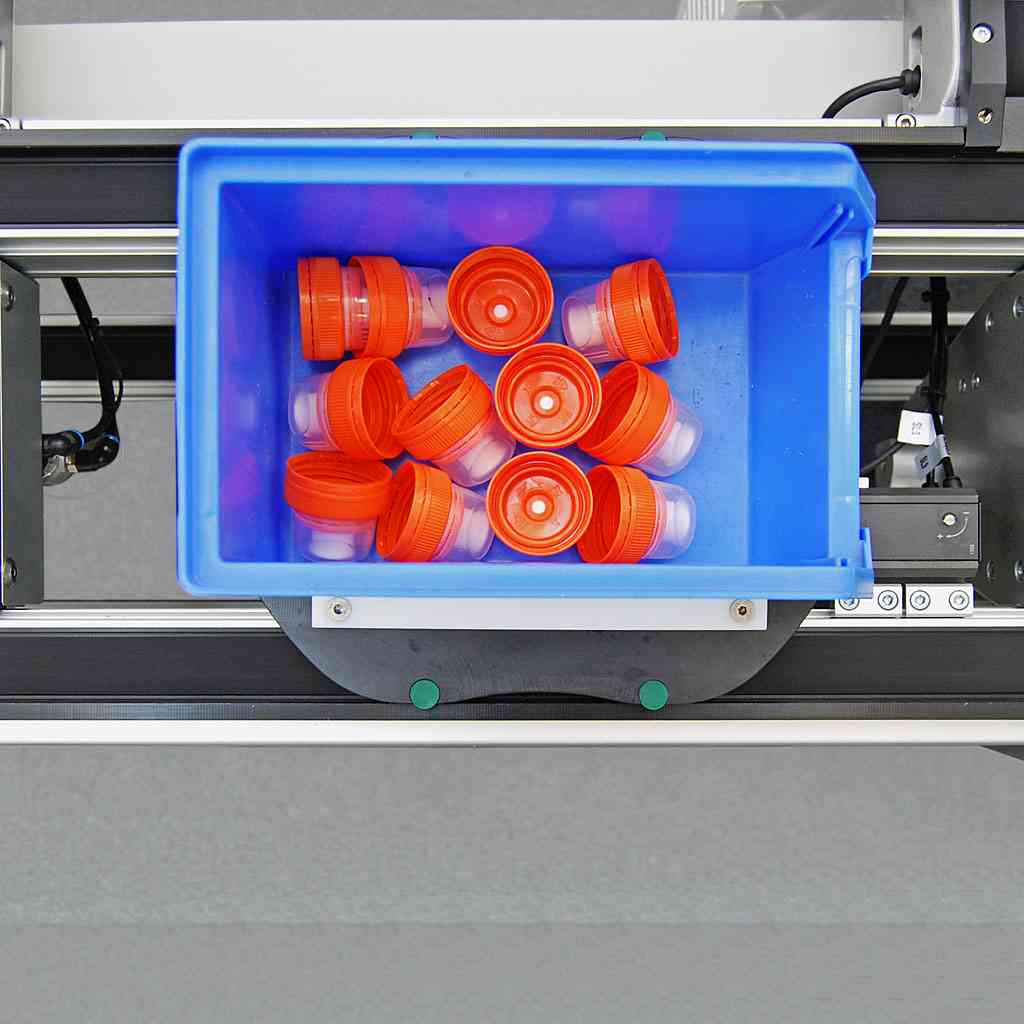
Size of the workpiece carrier: The LTE transfer system is suitable for small workpiece carriers from 80 x 80 mm to 225 x 225 mm. The LT40 transfer system is available for workpiece carriers from 200 x 200 mm to 320 x 480 mm.
Ability to work from below: The LT40 transfer system is a double toothed belt system and is therefore ideal for working from below. The LTE does not offer this option.
Load capacity: The LT40 can carry more weight than the LTE. Its workpiece carriers allow a payload of up to 16.8 kg. The LTE workpiece carriers carry a maximum of 5.3 kg.
Innovative, efficient, and flexible
The LTE and LT40 transfer systems both offer advanced solutions for precise and smooth material transport in various industries. Thanks to their great efficiency, flexibility, and energy efficiency, they make a significant contribution to optimizing production processes and increasing productivity. Companies use these transfer systems as a reliable basis for improving automation processes and meeting the requirements of modern industry.