As engineers increasingly look towards edge intelligence to provide gateway functionality, a system component is surprisingly often overlooked: the HMI device. This can be the case, for example, in the context of the provision of an industrial rack or box PC to provide intelligence at various edge-points within a system architecture. Similarly, within geographically diverse architectures, intelligent cellular routers are deployed to facilitate edge computing. These cellular routers are capable of hosting software for applications such as protocol translation or AI inference. In many of these implementations, the architecture will also include some requirement for visualization, either at local machine level, for site/production line overview or to monitor an entire system operation.
HMI devices are often viewed as local endpoints for data being sourced or created within other devices. Yet, this misses an important opportunity to simplify overall system design by instead using the HMI device as an intelligent edge gateway in its own right.
HMI Software in Automation
HMI software, whether supplied as an integral part of a display panel, or as a separate software application for installation on a panel or industrial PC, is a fundamental component of automation architectures, providing information to engineers and operators, and allowing them to interact with the underlying processes and devices.
Even in today’s ever more connected world, there are still cases where process plant operators either cannot, or do not want to connect to external systems and devices. A typical example would be where an older or more basic PLC style device is used within a machine or process line. It is still necessary for operators and engineers to interact with the system, but the underlying PLCs do not support wide area cloud connectivity.
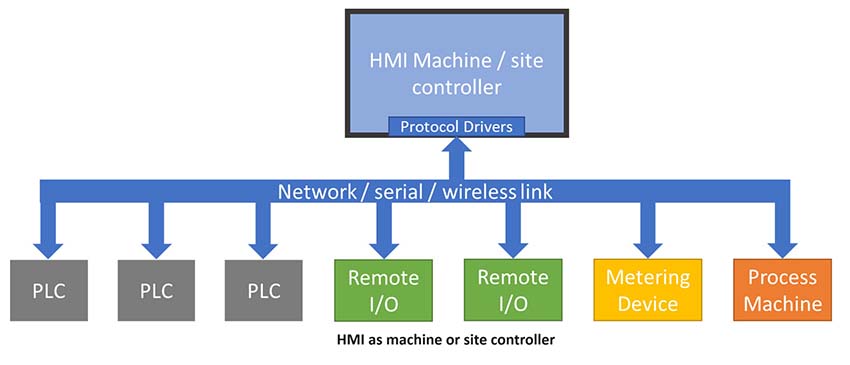
In these cases, an HMI of appropriate size and capability can be used as a standalone controller, providing an interface which ranges from simple mimic panels and virtual pushbutton control of a single machine, up to a sophisticated visualization, historian and alarm package for an entire production line or distributed process, offering a mix of pushbutton and recipe-based control options. The HMI effectively becomes a single screen, self-contained SCADA system, providing a cost-effective option for users where a multi-screen setup is not required.
The Graphical Endpoint
In this use case, the HMI panel is considered as a visualization package for an industrial PC or similar which provides the edge intelligence for the machine, line, or process.
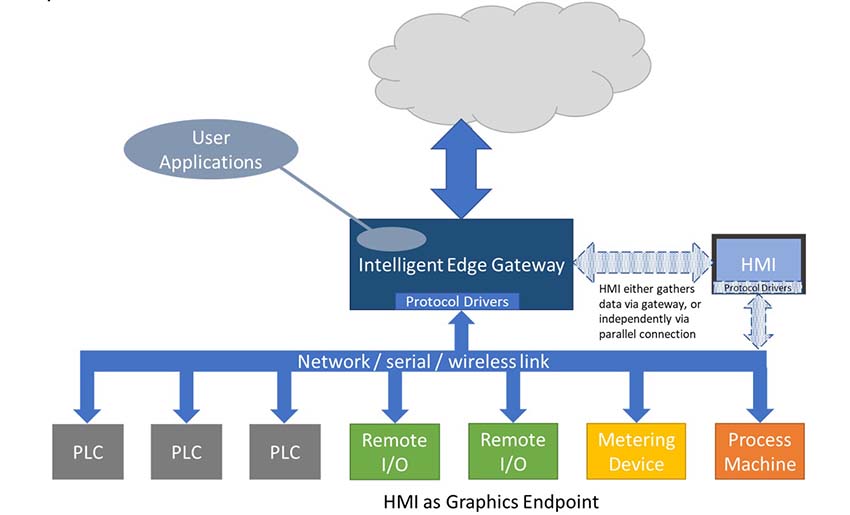
Here, an edge device provides the site intelligence, typically acting as a gateway, providing data enrichment, aggregation and filtration leading to actionable insights which are subsequently communicated upwards to the enterprise. It may also host user applications designed to manipulate the local data in order to layer control and management strategies on top of the devices connected to it.
In such cases, the HMI may simply be a touchscreen display which is driven by visualization software running on the edge device, but more typically will provide functionality very similar to that in the case of a standalone controller. Indeed, in many cases, the HMI operates independently of the edge device, interfacing directly to the underlying process to recover its base data.
The HMI as a Gateway
The concept of using an HMI device as a system gateway makes a lot of sense. Architecturally, the gateway is a point at which data converges from lower order devices, and this is obviously also true of any HMI deployment point.
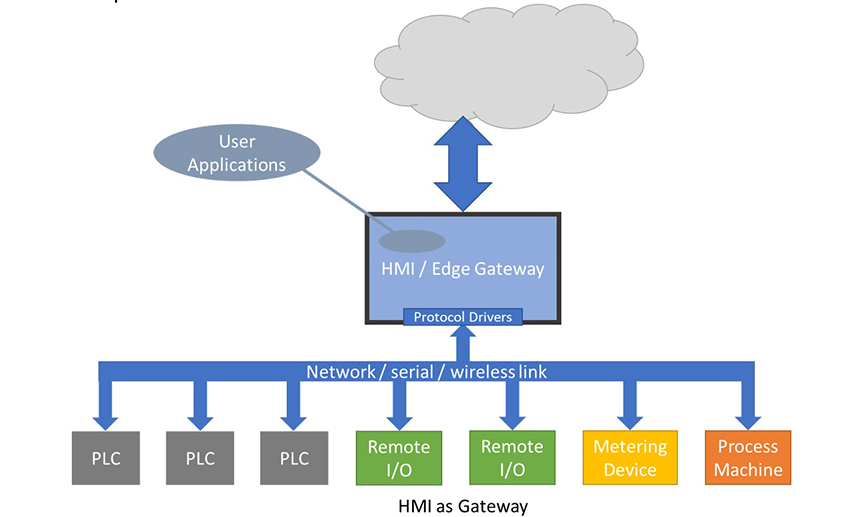
By providing mechanisms through which user applications can be deployed on the HMI hardware and interface to the data in the HMI, users are able to leverage the device protocol and data recovery capabilities of the HMI system, potentially saving man weeks of development effort, and concentrate their application efforts around their paradigm expertise and industry experience.
Furthermore, using HMI software means that interfacing upwards to the enterprise using IT protocols such as MQTT, SQL and ODBC or via direct connectivity to cloud services such as AWS or Azure can be achieved. And this interfacing involves simple, no-code configuration – potentially saving significant development effort for users.
Sourcing Hardware and Software Together
Of course, there are a number of suppliers who provide HMI hardware, and a further set of suppliers who provide SCADA software, so why buy both from a single vendor? The answer is because there are a number of advantages to this approach.
Every vendor that companies purchase from carries a hidden cost. Terms and conditions need to be agreed, quality needs to be audited, orders need to be expedited and so on. Sourcing both hardware and software from a single vendor eliminates the costs associated with a second vendor.
Sourcing hardware and software from a single vendor ensures that the software will run properly. This is obviously important at the time of initial purchase, but is even more important once equipment is deployed in the field. It is a reality of the modern world that software gets patched for all sorts of reasons. Bug fixes, security updates or simply ongoing development all raise the possibility of introducing an incompatibility with the underlying, deployed hardware. When only a single vendor is involved, these incompatibilities are much less likely to occur.
Scalability
Often, users have a variety of HMI applications, varying both in complexity of the data processing and visualization requirements, and also the underlying panel size and environmental characteristics. Independent software vendors typically have a minimum platform requirement which will preclude deployment on the simpler, small panels typically used for single machine control, whilst suppliers of simple machine operator panels rarely offer the comprehensive functionality required for higher order SCADA type operations. This means that engineers need to learn to operate and maintain multiple software packages, again incurring a hidden cost for the operator.
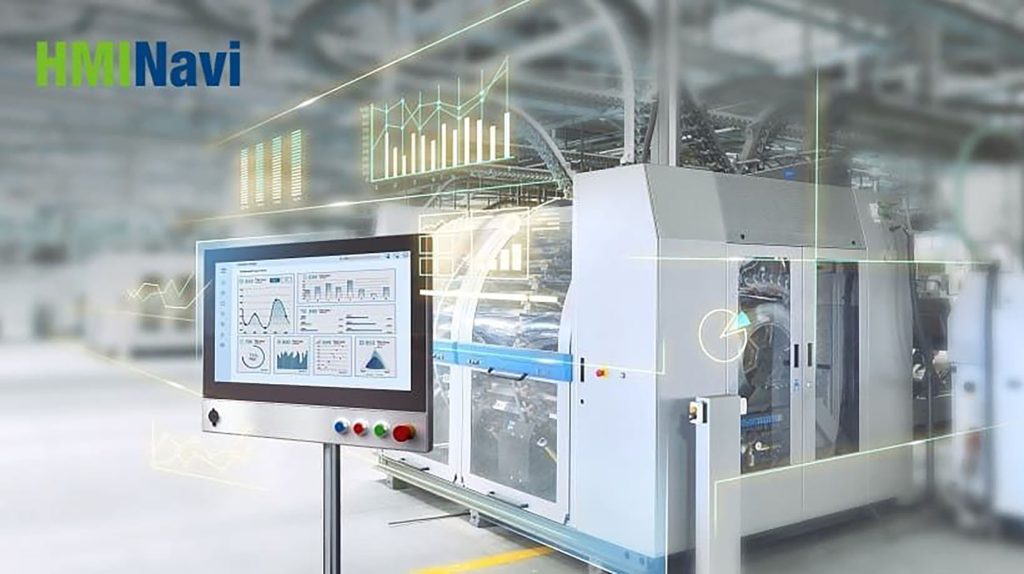
HMINavi by Advantech
Extensive involvement in client engagements will often revolve around using edge intelligence to provide gateway, complemented by sophisticated software and intelligent communications hardware offerings. It’s the case at Advantech.
The company’s HMINavi is a highly functional SCADA package optimized for deployment within a single screen HMI environment, which has particular relevance to OT engineers looking for a way to visualize PLC data and to integrate it within IT cloud environments and MES systems. It is available across a wide range of data panels, panel PCs and industrial PCs, encompassing both general purpose and specialist application hardware platforms.
This enables users to deploy a consistent environment across a wide range of applications, significantly reducing the hidden costs involved where different display packages are used at different points. It inherits a constantly evolving list of protocol drivers/device maps for over 500 common devices such as PLCs, allowing easy integration into virtually any process automation environment, together with uplink protocols enabling it’s use as a protocol gateway, translating and passing data between otherwise incompatible peer systems, or interfacing between the OT and IT environments through simple point and click configuration.
A comprehensive set of dynamic graphics primitives enable data rich and intuitive operator interfaces to be built and deployed, whilst real time trend displays are also supported to provide visualization of emerging behavior. Output operations are well catered for via a range of bi-direction graphic primitives, together with recipe blocks, scheduling, scripting and macro execution. A full alarm package provides operators with proactive notification of out of bounds conditions via a variety of optional methods, together with the ability to go back and analyze the events leading up to the alarm condition via a data historian capable of exporting data in a number of formats.
This combination of classic HMI functionality, coupled to flexible uplink capabilities and the ability to coexist and share data with other applications running on the same physical HMI hardware make HMINavi a compelling proposition for users implementing any of the architectures mentioned earlier. HMINavi enables the operator panel to become the central hub for all functionality, leading to lower complexity, cost and risk associated with the site deployment. Further, the high levels of functionality provided by the no-code configuration environment can save significant amounts of development time and cost when creating a system.
https://www.advantech.com/en-eu
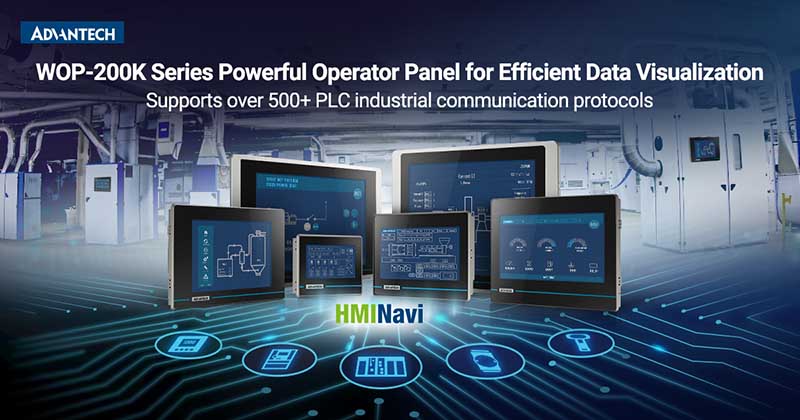