Corrosion protection is hugely important for several reasons. Most importantly, corrosion protection can save lives. Damaged equipment can cause accidents in production. Corrosion can weaken structures and equipment, which leads to failures and accidents. For example, corroded bridges could collapse, and corroded pipes could leak dangerous substances. Proper corrosion protection helps to ensure that these structures and equipment remain safe. It can be very expensive to repair or replace corroded materials. Taking steps to prevent corrosion enables us to achieve significant savings. Corrosion can also lead to environmental problems. Corroded pipes for instance can leak pollutants into the soil or water. Proper corrosion protection can help to protect the environment without toxic substances. For this reason, it is important to carefully select environmentally safe corrosion protection methods such as VpCI (Vapour Phase Corrosion Inhibitor Technology)
Patented Vapor phase Corrosion Inhibitors are technology that simplifies corrosion protection and is ideal for keeping enclosed void spaces (e.g., packages, equipment internals, or structural metal cavities) free from corrosion. The VpCI® molecules diffuse from areas of high concentration to low concentration reaching all areas of the enclosure. VpCI’s are effective at protecting multi-metals in electrical, static, rotating, and civil equipment and structures. This technology is designed to save time, money and offer more thorough, reliable, and easier-to-use protection than a variety of other metals preservation strategies. VpCI inhibitors are generally safe to handle and non toxic. Most products are recyclable or water-based and have a lower environmental impact than many harsher chemicals. With environmental pollution at an alarming high, green technologies like those utilizing the circular economy model are becoming essential for production process, including corrosion inhibitor manufacturing. In today’s world where environmental awareness is more important than ever, manufacturers are adapting and embracing sustainable practices for the benefit of consumers and our planet. A huge shift has been made from the linear to the circular economy.
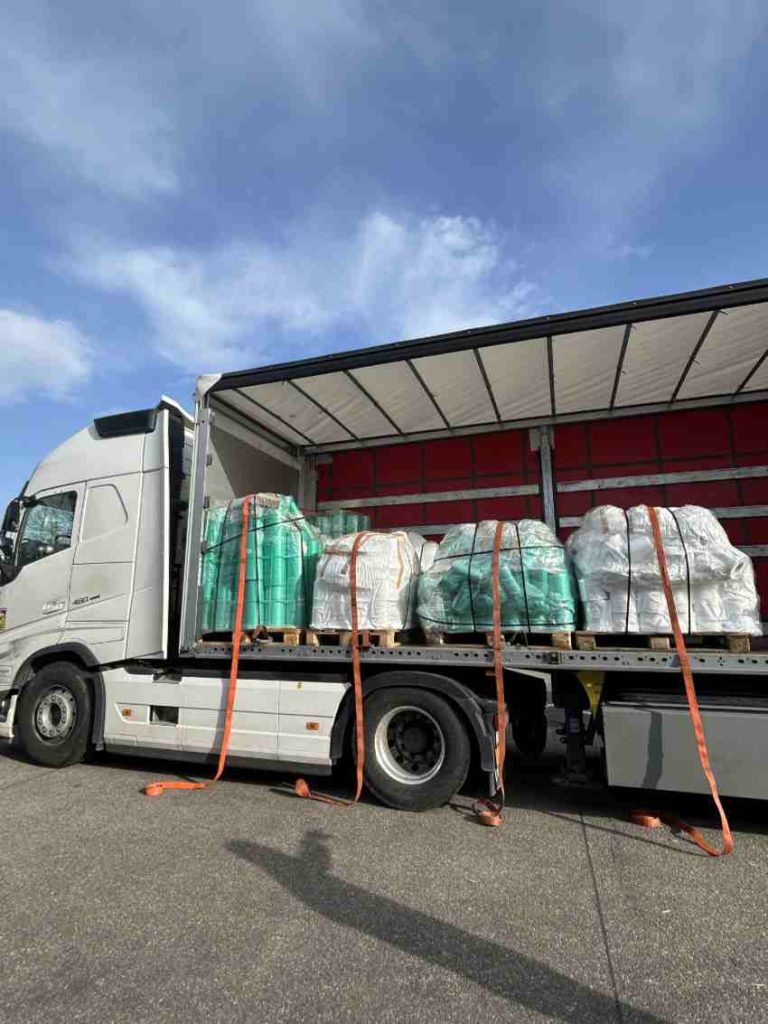
Circular Economy Challenges
Talking about the circular economy is much easier than making it happen. According to the UN, 46% of plastic waste ends up in landfills, 22% ends up as litter, and less than 9% actually ends up recycled. Why is it so hard to capture and reuse this plastic waste? Among the challenges are collecting material after it has been sent around the world and finding a consistent supply of recycled content within strict cleanliness and quality requirements. These issues can make it difficult for manufacturers to turn used packaging into anything more than cheap garbage bags. In areas such as the automotive industry, corrosion of transported parts can lead to expensive waste.
Overcoming Recycling Barriers
We should not let these barriers stop us from pursuing and implementing a circular economy in the VCI films market. European green corrosion protection manufacturer, EcoCortec, located in Croatia introduced VpCI®-126 PCR film that protects assets from corrosion in early 2023. This version of Vapor phase Corrosion Inhibiting film contains 30% post-consumer recycled content (PCR) sourced from a recycled raw material supplier that follows strict quality standards. Eco-conscious customers intentionally order this film to achieve a better environmental footprint. The plant closed another plastic recycling loop with the first delivery of plastic waste from its customer from Waldorf, Germany to Beli Manastir, Croatia. This signals the start of a new recycling partnership between two companies to recover plastic scrap and incorporate it back into quality finished goods.
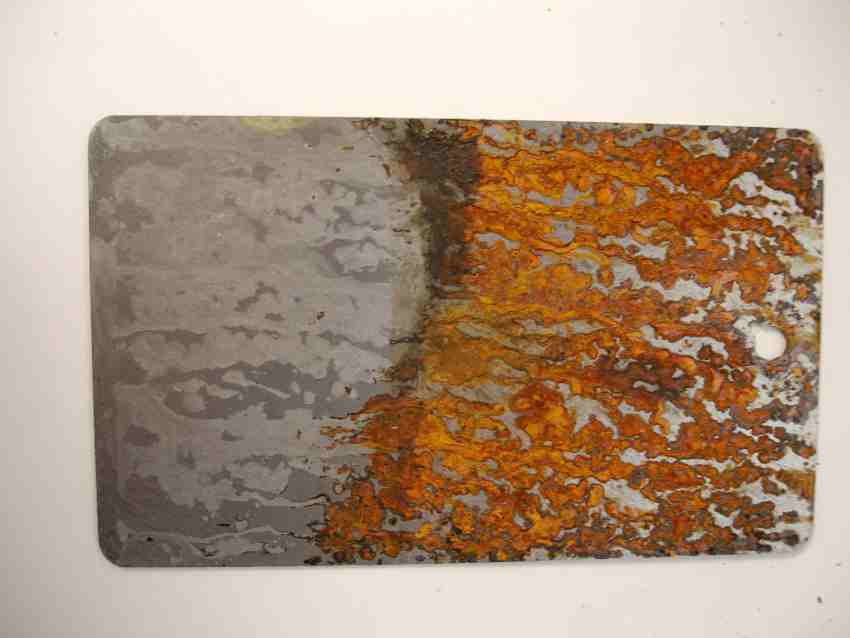
Onsite Reprocessing Facility
Croatian facility is able to go above and beyond simply producing film with PCR content, thanks to its onsite recycling facility, where both post-consumer and post-industrial scrap are reprocessed. German partner naturally ends up with much of the latter as it creates 3D bags from both VpCI®-126 PCR film and regular plastic film for their export packaging kits. Scrap builds up quickly, and in March 2024, Jakob Schober entered into an agreement with EcoCortec® to ship clean plastic scrap to the Beli Manastir plant for reprocessing. After further inspection the scrap was re-granulated using state-of-the-art reprocessing equipment and tested in the lab before being used in VpCI® Film production. EcoCortec® does the same with used packaging from a local construction company minimizing waste and expanding the use of PCR in finished goods beyond VpCI®-126 PCR film alone. The same truck that brought VpCI®-126 PCR to Schober was loaded with VpCI®-126 PCR scrap for transport to EcoCortec® 1,000 km away, resulting in additional fuel savings for a better carbon footprint as well as a circular economy.
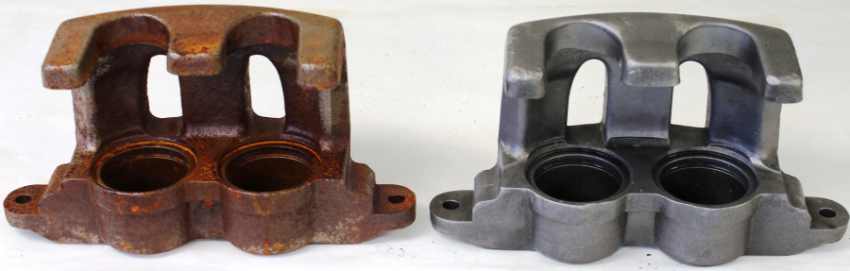
Pursuing Recycling Goals
The company is on the lookout for more recycling partners who will help them increase their volume of high quality recycled content in all VpCI® Films by sending their clean post-consumer plastic waste for recycling. This will create new channels for Croatian plant and local businesses to fulfill European and international goals such as increasing the amount of high-quality closed loop recycling, making products that can be recycled in their original markets, and reaching 30% recycled content in plastics packaging by 2030.
The initiative comes at a time when Europeans and the world are increasingly looking for ways to be more sustainable. It is a powerful example of helping to make the “circular economy” a reality at the level of a direct customer-manufacturer relationship.