Andoria Foundry supplies a wide range of top quality iron castings. Many years of experience in the production of diesel engines gives them the opportunity to make high-precision castings for various industries. The company has specialized staff with extensive experience. Additionally, Andoria has a very well-developed machine park in the field of mechanical processing and technical capabilities in the thermo-chemical treatment department.
Interview with Agnieszka Zuber- Trade Specialist, Roman Serwin- Chief Foundry Process Engineer & Paulina Bałys-Giereś- Quality Manager at Andoria Foundry.
A brief description of the company and its activities.
Agnieszka Zuber: For nearly 80 years, Andoria Foundry has stood out as a renowned producer of grey and ductile iron castings. We offer a comprehensive range of services, from machining to assembly, ensuring our customers receive top-tier service.
Our infrastructure includes 32 CNC machining centres, heat treatment, a paint shop and an automated grinding facility, enabling us to handle complex projects under one roof.
We prioritize long-term business relationships, believing them to be the foundation of stable business growth. Our commitment to quality has earned us the trust of a wide range of component industries.
In collaboration with our customers and their engineers, we continuously refine our processes and technologies to meet the evolving market demands.
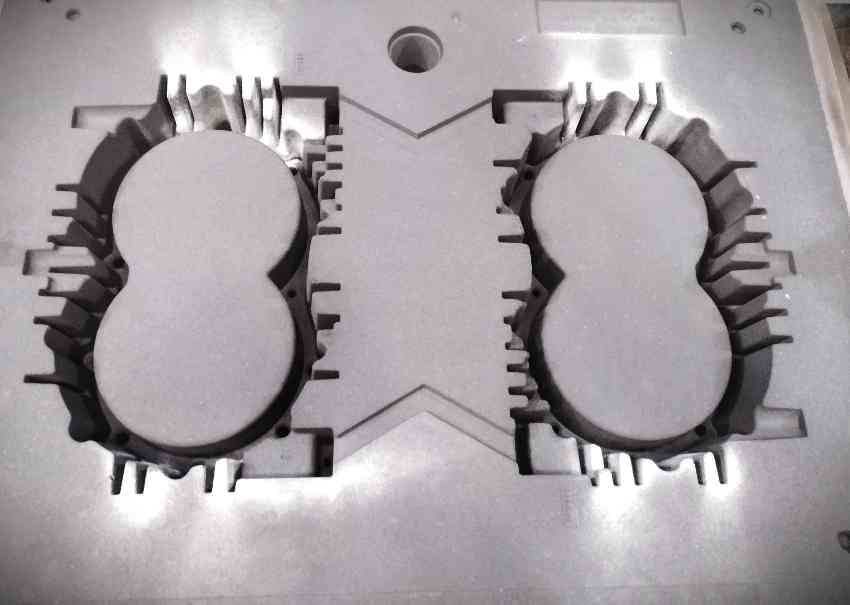
What are the main areas of activity of the company?
Agnieszka Zuber: Andoria is committed to ongoing evolution and actively pursuing new customer acquisition opportunities in diverse markets. However, our casting production is primarily concentrated in four main sectors.
Our lift and escalator high-quality mechanical components are essential for the reliability and durability of transport equipment.
Castings used extensively in agricultural machinery are valued for their hardness and ability to operate in harsh environments.
We also specialise in the production of precision elements for internal combustion engines and transmissions. Our castings are also widely used in the manufacture of pumps and valves, which require high pressure and corrosion resistance.
These four sectors form the foundation of our business and drive our growth. Thanks to our advanced technologies and years of experience, Andoria is able to meet the requirements of various industries with products of the highest quality and precision.
What’s the news about new products/services?
Agnieszka Zuber: It is of great importance to us to expand our product range. If the products created by our customers weigh between 5 and 250 kg and fit into our flasks, we are ready to take on the challenge. Andoria specialises in particularly complex castings with full machining, which makes us a unique partner in the industry.
We are currently focusing our efforts on strengthening our presence in the rail market. To this end, we are in the process of implementing rail certification, which will allow us to extend product range supplied to the rail transport sector. At the same time, we are exploring the market for industrial robots and forklift components, which opens up new opportunities for expansion.
What more we are particularly excited about is the development of products dedicated to the maritime industry. This spring, we were obtained the esteemed LR Marine & Offshore Approvals from Lloyd’s Register, which attests to our commitment to excellence and compliance with international standards.
What are the ranges of products/services?
Roman Serwin: Our company is a foundry specialising in the production of small-batch castings with complex shapes. We produce several hundred to several thousand pieces per year, with each component receiving our full attention.
Our extensive experience includes the production of components for internal combustion engines, such as casing, heads, flywheels and pump housings, as well as components for gearboxes.
Our product range also includes responsible drive parts for lifting. The automatic moulding line, with flask size of 1050x800x320/320, enables us to produce castings weighing between 20 and 180 kg in both grey and ductile cast iron.
From the outset, we ensure that each casting meets the required specifications and have a compact structure in each section. Our carefully designed technology and has of exothermic and natural feeders enable us to provide our customers with products of the highest quality.
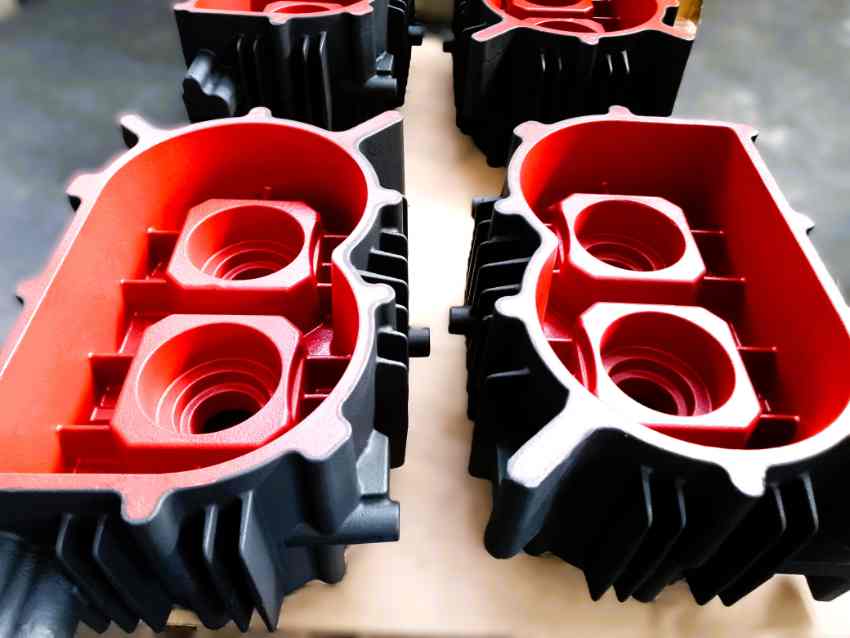
What is the state of the market where you are currently active?
Agnieszka Zuber: The foundry industry is characterised by a dynamic and challenging market environment. The last two years have presented significant challenges, with a notable decline in market performance observed also at the 25th International Fair of Technologies for Foundry METAL in Kielce in September of this year, which we attended.
This year’s event was rated by participants and exhibitors as one of the least successful in recent years.
However, as the crisis affects selected industries at different times, our strategy of diversifying production and not limiting ourselves to one industry allows us to maintain our position in the market. Consequently, we are better equipped to navigate challenges and capitalise on emerging market opportunities that will drive future growth.
What can you tell us about market trends?
Paulina Bałys-Giereś: The latest forecasts indicate a clear upward trend in infrastructure investment, resulting in increased spending on construction and rail projects. These are areas of interest for our company.
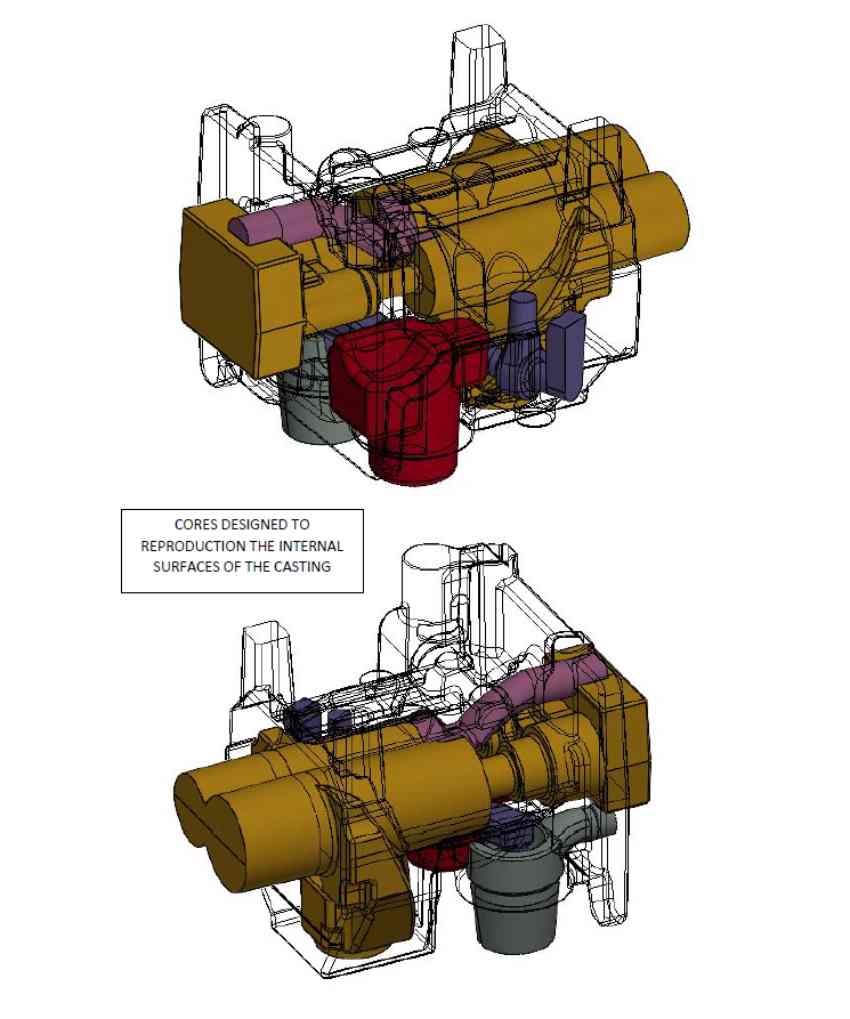
Andoria is following also to the trend, in line with its commitment to environmental protection, as evidenced by its ISO 14001:2015-certified environmental management system. This will allow us to adapt easily to the increasing sustainability restrictions in the future.
Both of these factors give us hope that the next year will be stable and peaceful. The latest forecasts indicate that a full return to normality in in the broad sense casting business is anticipated in 2026.
What are the most innovative products/services marketed?
Agnieszka Zuber: As previously stated in this article, Andoria is a leading producer of tricky iron castings. The company employs 3D core printing technology, which enables the fast and precise creation of complex shapes that were previously unattainable through conventional techniques.
The advanced core process allows us to significantly reduce labour intensity on the moulding line by assembling cores ready for pouring. Painting, gluing and assembly are conducted at the earlier stage of technology process. We are able to accurately reproduce the internal shapes of the castings with maintaining the required wall thicknesses.
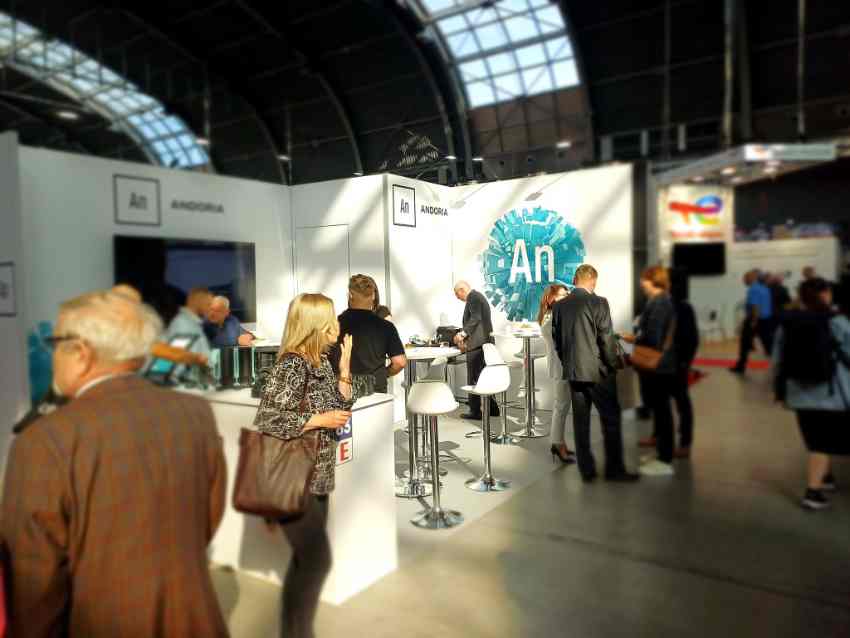
One of the key benefits of this approach is the elimination of the need for tooling, which allows for swift and cost-effective corrections to the shape by simple modification in the CAD program. This eliminates the need for costly tooling intervention.
The innovative processes guarantee the highest precision, durability and surface smoothness in our castings. Thanks to this cutting-edge technology Andoria is able to realise the most demanding projects and deliver products of the highest quality and complexity to our customers.
What estimations do you have for the rest of 2024?
Agnieszka Zuber: As the year 2024 draws to a close, we are aiming to conclude the year with the best possible result. This will allow us to start 2025 in a positive position, ready to face the challenges ahead.