Worldia, founded 2000 in China, is a leading manufacturer of high-quality, superhard cutting tools, components and materials (PCD, CVDD, MCD, PCBN) with 5 manufacturing locations and more than 1100 employees worldwide, thereof 10% in research and development, holding over 250 patents. Since 2019, the company is listed on Chinese stock market as one of the first 25 high-tech companies. Innovation, a focus on technology, highest quality standards and consistent customer orientation have enabled Worldia to grow steadily and invest in new product areas and locations. Worldia Europe as first foreign subsidiary serves the European market and offers application technology support and on-site warehousing since 2022.
Interview with Michael Grimm, Chief Strategy Officer of Worldia Group.
Easy Engineering: Price: tell us something about the costs from a ROI perspective?
Michael Grimm: Similar as when buying other products, also for cutting tools many buyers look at the purchase price as leading criterion for their decision. However, this can be misleading and even cause much higher ongoing cost if following criteria are not being considered at the same time:
- Tool life per cutting edge
- Number of indexes or re-grinds per cutting edge
- Regrinding/ recoating cost, if any
This all directly impacts the purchasing budget of tools and as a rule of thumb only makes up around 3% of total manufacturing cost.
In addition, tools have strong influence on other cost that do not fall within tooling purchasing budget. Such cost include:
- Tool setup cost
- Tool change time
- Coolant cost
- Time to remove chips from machine
- Machining time/ number of machines required for the operation/ number of operators needed/ ROI of machine purchases.
These costs have a much bigger impact on overall manufacturing cost, but are often not considered when taking purchasing decisions as they might not be part of the buyer’s KPIs.
So even for cutting tools, the old saying often applies: “Who buys cheap buys twice”.
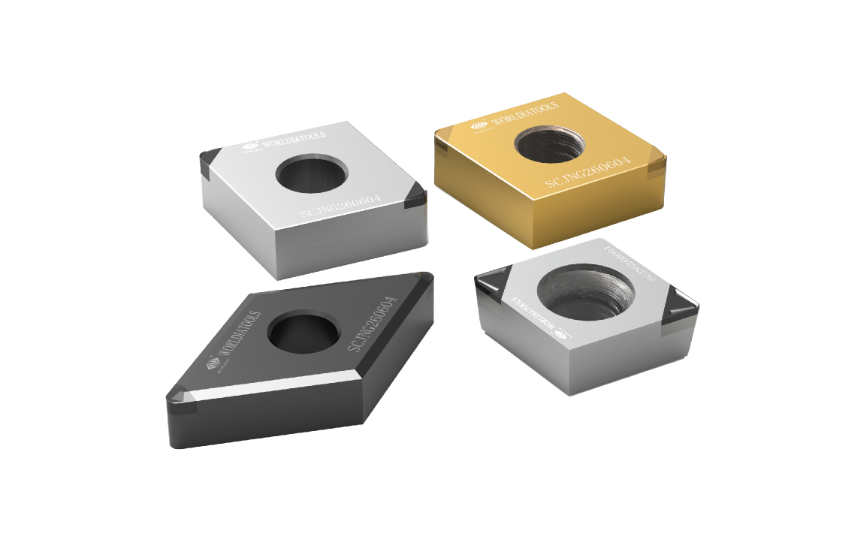
E.E: What about the costs for maintenance / future upgrades etc.
M.G: Maintenance cost of cutting tools include
- Regrinding of HSS, carbide, ceramics, PCD and PCBN tools
- Retipping (de-brazing of worn and brazing of new PCD and PCBN cutting egdes)
- Recoating of HSS and carbide tools
- Maintenance of indexable cutter bodies (regular check, exchange of screws and other spare parts, repair as needed)
Especially the last topic is very critical to the accuracy and lifetime of these tools. Well-maintained cutter bodies often can last decades in mass production, whereas e.g. tools with worn-out screws or insert pockets do not only lead to higher insert consumption, but in worst case can also damage or destroy expensive workpieces.
E.E: Quality: tell us something about the quality behind your products / solutions.
M.G: WORLDIA tools are known for their superior quality that stands out from many other China suppliers. “World-leading quality made in China” is one of our 7 “mantras”. WORLDIA tools run successfully in leading global companies, meeting their highest quality standards.
WORLDIA is certified according to ISO 9001 and related standards and has really introduced quality as part of it’s culture that is being lived by every employee every day.
E.E: Characteristics: what important features should clients search and what features do your products / solutions offer?
M.G: When it comes specifically to superhard tools, the core of WORLDIA’s portfolio, I think there are 2 main directions in product selection:
- Availability of high-quality products for universal use. Easy choice, fast delivery.
With our MANANOVA portfolio of stock-keeping ISO PCD and PCBN inserts, we have an immediate first solution for 60-70% of all related application cases which is very important e.g. to the competitiveness of job shops and Tier 1-2 suppliers. Thanks to our simplified product selection guide, usually no on-site application support is necessary. Products are being shipped from German warehouse latest 1 workday after order entry.
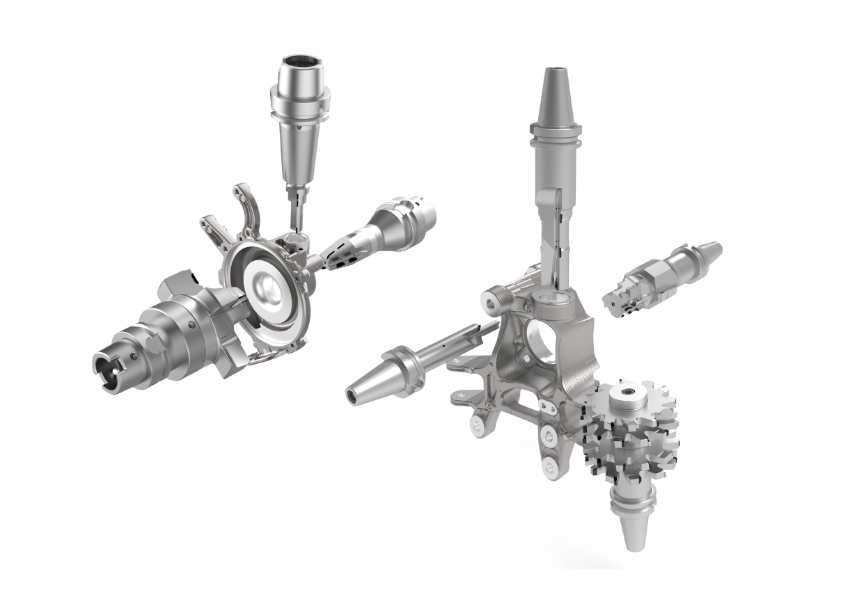
- Capability to design and manufacture tools exactly to the customer’s needs.
This starts with the detailed analysis of the component to be manufactured, the machine, the clamping and the intended process and requires an open communication between customer and supplier to achieve the best result. For this, support by application experts in the region is key. Meanwhile, WORLDIA has a strong application team in Europe, supported by a network of technically trained distributors.
Functionality: tell us something about ease of use, integration with other solutions or other innovative features of your products / solutions?
Ease of use is a topic that has direct impact on quality but also on cost. Take our PCD monoblock tools as an example: Often different functions such as milling, countersinking and reaming are integrated into 1 tool. This combination saves tool changes on one hand, and on the other hand does not even require time-consuming tool setup. These tools come “out of the box, ready to perform”. Other tools, like our indexable BE-series PCD face milling cutters include fine-adjustment capability which, however, is only being used when really needed, e.g. for finish milling applications. If an axial runout of 20 µm is sufficient for an application, the same standard cutter can also be used as fixed-pocket cutter without any adjustment. This feature helps our customers to minimize inventory of cutter bodies.
Another feature that operators really like is the light-weight design of our milling cutters. A 250 mm diameter cutter doesn’t weight more than 6,5 kg.
By shifting from (wet) grinding to (dry) hard turning with PCBN inserts, customers can save significant cost e.g. for coolant and grinding waste disposal. Lasered chipbreakers ensure that chips don’t disturb the machining process.
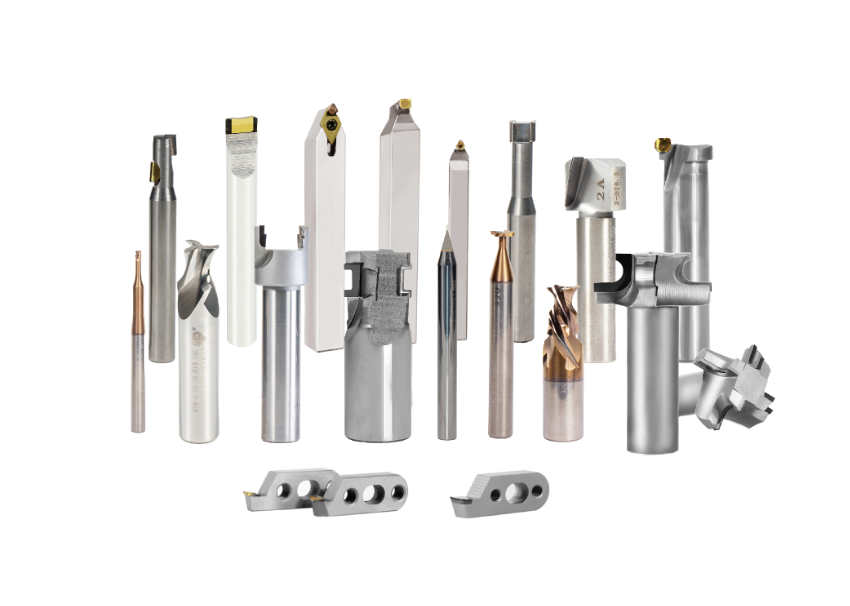
E.E: Comparison: what key features do your products / solutions have compared to others on the market?
M.G: Some unique features have already been mentioned before. Other examples are our PCD micro drills that start already from 0,1 mm diameter and our PCD helical end mills with “twisted” PCD cutting edges. Due to WORLDIA’s capability to manufacture its own PCD and CVDD materials, we are often more competitive versus companies that have to buy these materials.
Again, these are only a very few examples. To learn more, please check our website or visit us at AMB Stuttgart 10.-14.09.24 in hall 1, booth Z130.
E.E: Feedback: what was the feedback from clients about your products / solutions?
M.G: Well, first I came to know WORLDIA was approx. 10 years ago. In all these years, feedback from clients has always been very positive, especially on quality, but also on price-performance ratio.
E.E: What purchasing advice do you have for clients in your fields of activity?
M.G: As I replied to your first question, I would consider it short-sighted only to look at the price of the individual cutting tool. Important is the “total cost of ownership” respectively the tooling cost per manufactured component. Furthermore, I have seen biggest benefits for customers resulting from stable and trustful customer/ supplier partnerships with joint development projects etc.