The case study on a large building and construction materials company, with operations in Australia, the US and Asia, sought to strengthen their current respiratory protection program by introducing Powered Air Purifying Respirators (PAPRs) while staying on budget. Personal respiratory protection against small dust particles, or toxic fumes that are non-visible and odorless, is one of the biggest occupational health and safety challenge faced by industrial companies in their quest to ensure the everyday and long-term health of the employees.
Easy Engineering: What were the needs of the client?
CLEANSPACE: The company’s hard rock quarries had many workers who regularly confronted hot conditions and dust hazards during daily shifts. Staff were issued with negative pressure masks and disposable respirators in the production and maintenance phases.
Many employees working over long periods were required to carry a range of equipment and personal protection equipment (PPE) during high exertion activity. There was a natural desire to seek relief from cumbersome or uncomfortable face masks by removing or constantly adjusting the face masks despite knowing the risks.
The disposable respirators also relied heavily on the wearer correctly fitting the mask. Subsequent reports from quarry workers said the face masks were tight and uncomfortable and contributed to safety glasses fogging up, another cause for workers to remove their face masks.
The company was concerned employees weren’t replacing the disposables and filters as often as they should when the filters became dirty. In other instances, masks were being disposed of before they are required – this has significantly added to the cost of the site’s PPE program.
E.E: Why did the client choose your products / solutions?
CLEANSPACE: CleanSpace respirators increased compliance by increasing comfort and ease of use. CleanSpace also reduced overall wastage and cost by being reusable and alerting staff to when a filter needed replacing.
The company conducted an extensive review of available respiratory protection solutions in the industry. Following discussions with leading safety suppliers, the company found clear advantages with CleanSpace positive pressure PAPRs, designed and engineered in Australia. While they provide all the protection of a PAPR, they are free from belts, battery packs and hoses making them more comfortable over long periods. Compared to disposable masks, CleanSpace respirators offer superior protection, are reusable with economic advantages, as the annual cost of replacing disposables stacks up.
The company expressed interests in the three CleanSpace respirators: CleanSpace EX is intrinsically safe, is suitable in potentially explosive environments such as mining; CleanSpace ULTRA is IP rated 66, water tolerant, perfect for stonemasons carrying out wet-cutting; and CleanSpace2 is the most versatile, suitable for various industrial applications where water tolerance or intrinsic safety is not required.

E.E: What products / solutions were used?
CLEANSPACE: CleanSpace2 was selected to roll out the trial program at the company’s hard rock quarries. The innovative, award-winning design and breath responsive CleanSpace2 were well received and gave employees great comfort and confidence against airborne particulate and gas contamination that has never before experienced in the workplace.
“Although small, the respirator has an intelligent software system that delivers clean, fresh air and is breath-responsive. The system adjusts the mask pressure and airflow to match that needed by the wearer, regardless of how hard they are working. It’s a remarkably comfortable mask.” – Dr Alex Birrell, CEO, CleanSpace Technology.
E.E: Please describe how was the project implemented?
CLEANSPACE: Selected employees took part in the trial program and agreed on how easy it is to use the CleanSpace2. The powered respirator was used daily up to 8 hours shift over 5-days working week. Employees to note the ease of functionality, the level of protection and comfort in their work environment. The users have expressed a preference for wearing CleanSpace2 over the traditional disposable dust masks that had been in use on-site for many years.
The employees said the unit was more comfortable to wear, easy to use and simple to maintain. For the management team, this meant it simpler to implement the choice of CleanSpace2 respirators in line with the site’s mandatory PPE requirements.
E.E: Were there any products with special characteristics used?
CLEANSPACE: CleanSpace2 is a positive pressure respirator, which meant the silicone masks did not need to be tightly fitted against the face negating the need for regular fit testing. The site evaluation, supported by PortaCount data, clearly demonstrated the high protection factor of the PAPR vs APR. The company also noted the filter blockage detection system that alerts the wearer to replace the filter when the system detects a heavy particulate load, ensured employees maintaining an efficient level of filtering while eliminating costs associated with unnecessary filter changes.
E.E: How did your products / solutions improve productivity for the client?
CLEANSPACE: The trial highlighted additional benefits from using CleanSpace2, such as eliminating the issue of fogged-up safety glasses. Employees also reported less heat stress and can perform daily tasks with greater ease from fresh airflow across their mouth, nose and face. Since the initial trial, the company’s other Australian sites have witnessed similar improvements in safety, productivity and costs. And with the support of a safety solution provider, Protector Alsafe, they are now looking to implement CleanSpace2 powered respirators at many of its quarry sites as a replacement for disposable respirators.
E.E: How important was the project / projects for the client?
CLEANSPACE: From an environmental perspective, the company felt proud to be reducing its waste footprint with reusable units. The company favored another benefit of the CleanSpace2 powered unit, without the silicone masks, which utilize by employees at different shifts. Thanks to a closed-circuit design, the exhaled air will not travel into the powered section of the respirator unit. Every employee has their individual correctly fitted silicone half-face mask, thus preventing the potential for the transfer of pathogens between staff.
E.E: What was the client feedback after implementation?
“We were pleasantly surprised when we compared the costs of CleanSpace2 against the ongoing costs of disposables. There was a significant reduction in our long-term costs on respirators when we switched to CleanSpace2. Every employee at our trial site now has their kit including the battery charger, filter pack and mask,” – The company’s Health and Safety Officer.
E.E: How did the solutions provided improve efficiency for the client?
CLEANSPACE: Ensuring employee cooperation and compliance was a key concern for the company when using disposable and reusable half masks. The associated cost, not only in the turnover in disposable masks and filters but also the financial impacts of employee morale and productivity, and absenteeism were also a concern. The company sought a cost-effective way to increase employee respiratory protection compliance & CleanSpace2 powered respirator has achieved positive outcomes.
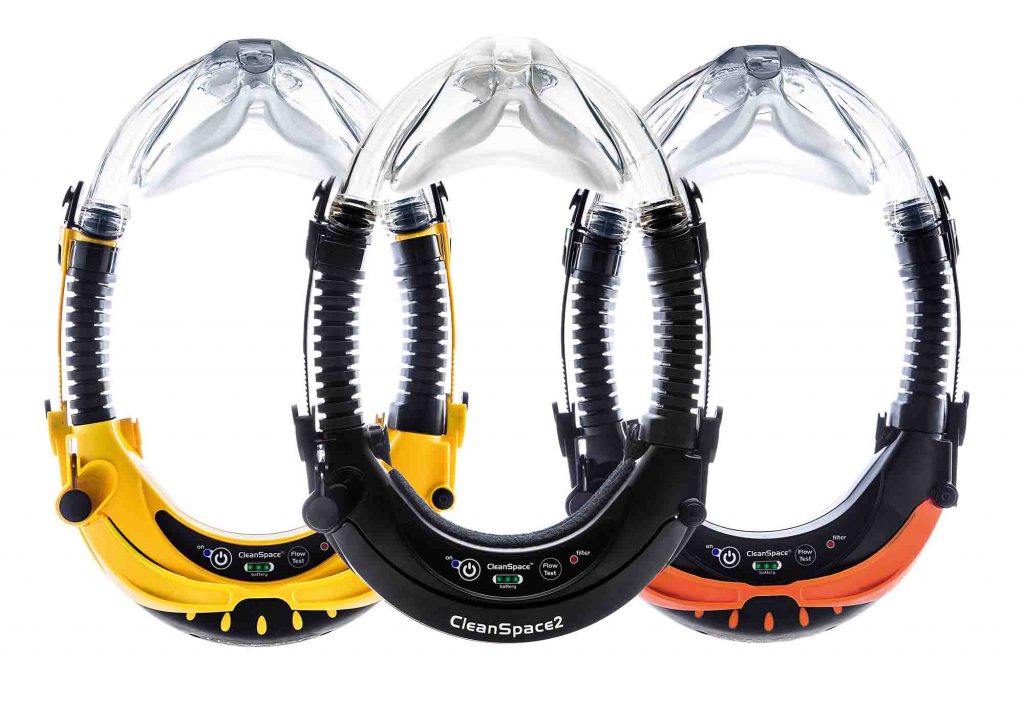
E.E: Did the current situation made your company implement differently than usual?
CLEANSPACE: CleanSpace respirators enable thousands of industrial companies to implement work safely in comfort and with minimal intrusion to workflow. A wide range of blue-chip companies and governments have entrusted CleanSpace respirators in managing occupation health & safety.
CleanSpace Technology supports ongoing learning, product training, fit-testing and instructions on maintenance and care with attentive customer support.
Contact the team for more information or request a demo.
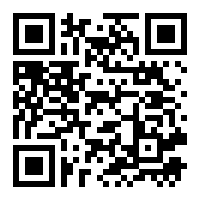
Address: Unit 5, 39 Herbert St, St. Leonards NSW AUSTRALIA TEL: +61 2 8436 4000
Email: sales@cleanspacetechnology.com Website: www.cleanspacetechnology.com