Contec is a climate tech company based in Poland that specialises in processing end-of-life tires. Through a patented pyrolysis process, Contec transforms ELTs into circular rubber and plastic raw materials that deliver low-carbon-footprint products for the manufacturing industry: recovered Carbon Black, recovered Tire Pyrolysis Oil, and recovered Steel.
They’re the only company in the world that uses a molten salt mix as the heat transfer medium. Contec proprietary molten technology creates the conditions for a safer, more efficient, and economical method of production designed with repeatable quality in mind.
Since 2017, the company has contributed to decarbonising the manufacturing industry, focused on providing a sustainable replacement for virgin Carbon Black and petrochemical raw materials.
Interview with Przemyslaw Rakoczy, Business Development Director at Contec S.A.
Easy Engineering: What are the main areas of activity of the company?
Przemyslaw Rakoczy: Contec S.A. is focused on ELT recycling, research and development of rCB applications, and the development of industry production standards.
E.E: What’s the news about new products/services?
P.R: In 2023, Contec secured a PLN 72 million (EUR 15 million) funding round from VINCI, Blachy Pruszyński, Warsaw Equity Group, and Mariusz Machcinski. This funding marked Poland’s largest round in the Climate Tech sector in 2023. The capital injection is earmarked for expanding Contec’s Szczecin plant, enabling the company to triple its production capacity and process 33,000 tonnes of waste tires annually.
Contec has expanded a plant in Poland—and we’re counting down the days for its expansion—and is now one of the few European companies that offer full circular products and solutions for the rubber industry regarding ELT recycling, producing industrial volumes of the highest quality of rCB.
In 2023, we registered our proprietary technology, Molten®. The technology creates the conditions for a safer, more efficient, and economical production method, designed with repeatable quality in mind. The salt mix, Molten®, brings unparalleled energy input control into the reactors, allowing complete control over process parameters. Contec is the only company worldwide using molten salts as a heat transfer medium.
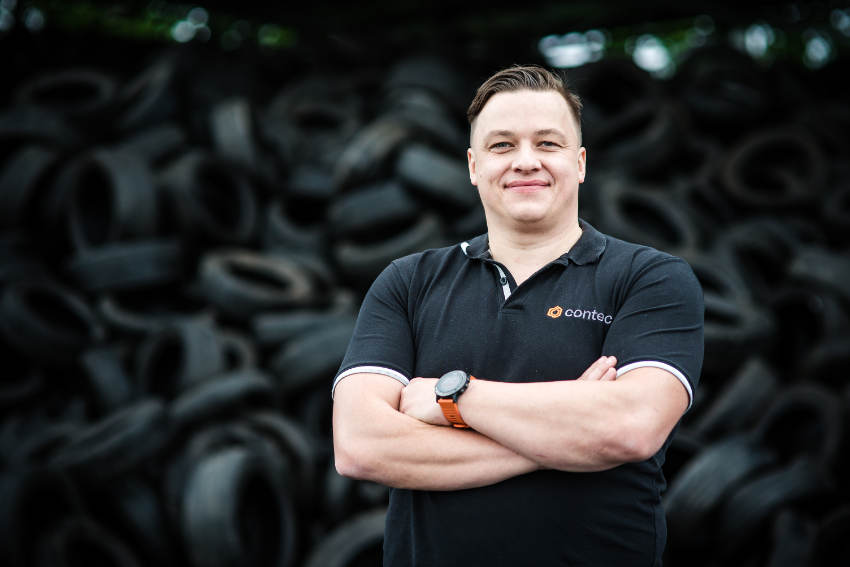
E.E: What are the ranges of products/services?
P.R: Contec S.A. provides circular rubber and plastic solutions that deliver low-carbon-footprint products by recovering Carbon Black, oil, and steel from waste tires: ConBlack® (recovered Carbon Black), ConPyro® (recovered Tire Pyrolysis Oil), and ConWire® (Recovered Steel).
E.E: What is the state of the market where you are currently active?
P.R: Tire and rubber industries are quickly seeing recovered Carbon Black as a viable solution to reduce the overall carbon footprint of their end products. However, scaling these circular solutions across the tire, rubber, and plastic industries remains the main challenge. The industry needs additional financial backing and a rapid scale-up in constructing additional pyrolysis plants to meet current and future market demands. Additionally, the industry could benefit from the development of rCB standards, both in Europe and worldwide.
E.E: What can you tell us about recovered Carbon Black market trends?
P.R: The global rCB industry is still mostly working on financing the scale-up and the construction of industrial plants. As the pressure to ecarbonize products increases, more companies are investing their research and development efforts into finding new applications for rCB. rCB producers need to breathe new application cases into the plastics and automotive industries.
Pyrolysis plants require serious investments in capital expenditures (CapEx) and are challenging to operate, so they must successfully meet all environmental and safety standards.
It needs to be easier for tire and rubber manufacturers to start using recovered Carbon Black (rCB). At Contec, we achieve this by focusing on technological developments to meet the most demanding market requirements—this is our starting point. We also ensure quality and consistency throughout the entire supply chain. Lastly, we price rCB competitively. Sustainable products don’t need to have a premium, contrary to current trends. In fact, that premium often serves as an entry barrier for manufacturers. Maybe we can price it higher once we have more demand, but that’s not a priority right now.
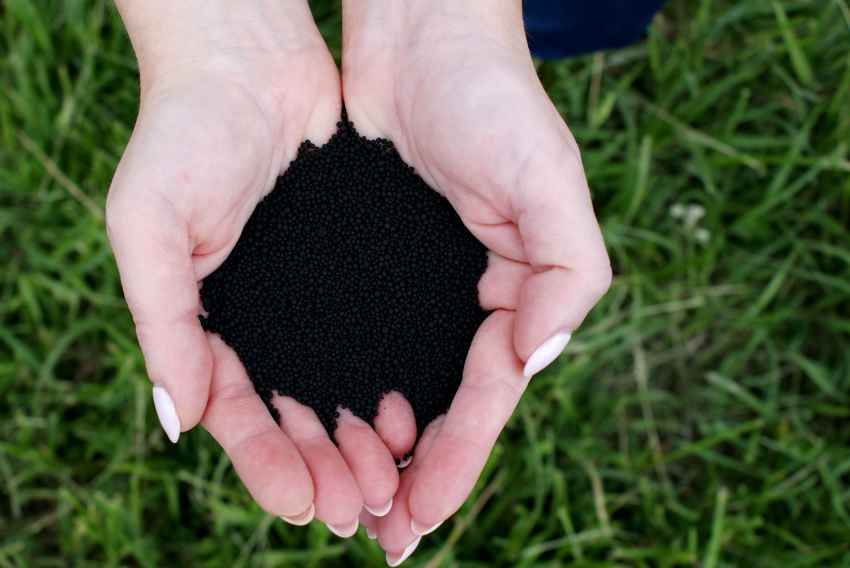
E.E: What are the most innovative products/services marketed?
P.R: Our registered technology, Molten®, results from our passion for innovation and commitment to research and development. This exclusive mix of molten salts is used as the heat transfer medium in our pyrolysis process, enabling the tire industry to source cleaner and more sustainable products.
Our technology is different because it’s a continuous process based on molten salt as a heat transfer medium. The liquid mixture works up to 560 degrees Celsius, allowing complete control over how much energy is put into the reactor. It ensures control over the temperature and reaction parameters, which is impossible under standard technologies such as open flame or fuel gases.
Numerous benefits can be listed, but the most important is the control over rubber treatment. Every rubber particle passing through the reactor is treated equally because it receives the same energy. This is brought about by setting the exact temperature that is required.
Secondly, the flow of molten salt heats the reactor uniformly. The entire length of the reactor has almost the same temperature. The difference between the inlet and outlet is barely 5 degrees Celsius, which brings control and stability to the process. Hence, we can offer quality and stability in our products.
E.E: What estimations do you have for 2024?
P.R: After securing a 15 million EUR investment in 2023, we’re expanding Contec’s Szczecin plant, enabling the company to triple its production capacity and process 33,000 tonnes of waste tires annually. Currently, we’re carefully selecting new plant locations across Europe, working closely with esteemed worldwide architecture and engineering consultancy firms, and studying other regions for plant locations that would provide global coverage for our most strategic customers. After all, scaling up is a trend across the industry and is needed to match the demand for rCB that we’ve seen.