In the rapidly evolving manufacturing sector, the ability to leverage data for enhancing productivity, reducing waste, and bolstering competitiveness is paramount. smartFAB, with its AI-powered industrial analytics solution, assisted a multinational auto components manufacturer to address several critical challenges affecting the efficiency of a painting line.
Project overview and client requirements
The client’s painting line serves as a pivotal point for multiple assembly lines that produce a variety of components. This line is considered a bottleneck for the entire factory. Despite its automation, the line requires operator intervention at several workstations, such as in the loading, unloading, and painting. Operators predominantly relied on their experience to determine the optimal sequence for loading products onto the line, which often led to unplanned line stoppages and waste. The primary objectives of the manufacturer were therefore to identify the root cause of unplanned stoppages and optimize product scheduling to enhance efficiency and minimize material waste, as well as equip operators with a tool to explore various scenarios and understand the impact of changes on production and waste.
Why smartFAB?
The client chose smartFAB for its holistic approach to data analytics and its capability to provide a multifaceted solution that could solve simultaneously different production problems. smartFAB’s solution offers real-time insights, caters to the needs of both engineers and operators with diverse skills, and facilitates data-driven decision-making.
Predominant features include:
- Integration of data silos
smartFAB connects data from MES and ERPs systems as well as from IoT sources, automating data science workflows to simplify data access and analysis without the need for a specialized in-house team.
- Creation of a digital twin
The solution creates a digital twin of the production line, enabling real-time monitoring and optimization of machine and plant performance, identification of issues, and provision of timely solutions.
- Human-in-the-Loop AI
Through the HitL approach, smartFAB incorporates domain knowledge into the solution, combining AI with operator intuition and expertise to achieve optimal results.
- Contextualized insights
The solution translates data into contextualized and comprehensible stories and practical recommendations, aiding informed decision-making at all organizational levels.
- Impact-based insight classification
smartFAB categorizes insights based on their impact on production, allowing decision-makers to prioritize and address the most significant issues to improve efficiency and quality.
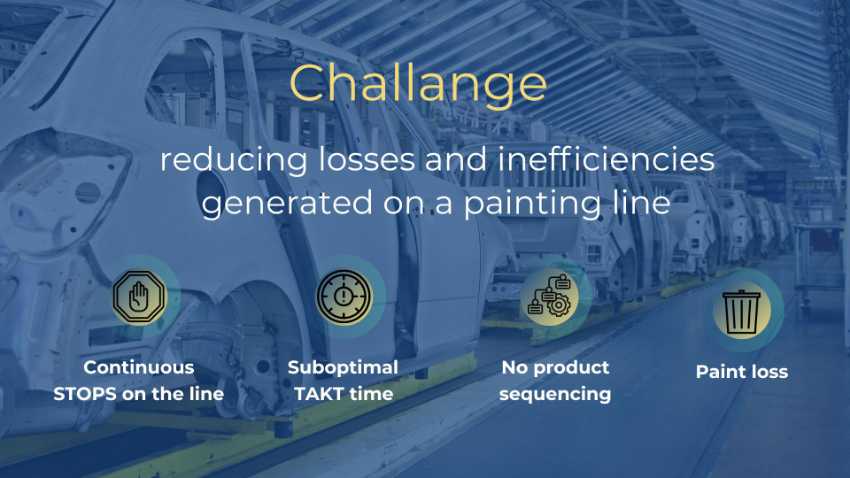
Solution Implemented
smartFAB initially recommended the implementation of its digital lean module to identify and monitor sources of variability and inefficiencies in production. Alerts were set up to detect deviations and anomalous behavior on the line A root cause analysis was conducted to understand the reasons behind these deviations, pinpointing inefficiencies and bottlenecks, such as problematic operations at specific workstations or delays caused by particular product types. This real-time monitoring was crucial for the immediate identification of issues, guiding operators on when to take action and which problems to prioritize.
The second phase involved deploying an optimization module that provided actionable recommendations, such as optimal part sequencing based on a specific or multiple objectives, such as throughput, cycle time, worker productivity and/or color changes.
The final phase introduced a “What if?” module, enabling operators to experiment with product sequencing and immediately understand the potential impact of each change on KPIs such as throughput and material loss. This tool empowered operators to make informed decisions based on data-driven insights, enhancing their flexibility and strategic planning capabilities in response to variations in demand.
Impact
The implementation of smartFAB’s solution had a deep impact on the client’s manufacturing operations, facilitating a transition from an experience-reliant production model to a data-driven one. The solution’s real-time insights and predictive analytics capabilities were transformative, allowing proactive rather than reactive adjustments. Notable achievements included a 10% increase in OEE and throughput, a 15% improvement in worker productivity, and a 20% reduction in color changes, and subsequent reduction in paint, solvent and water consumption.
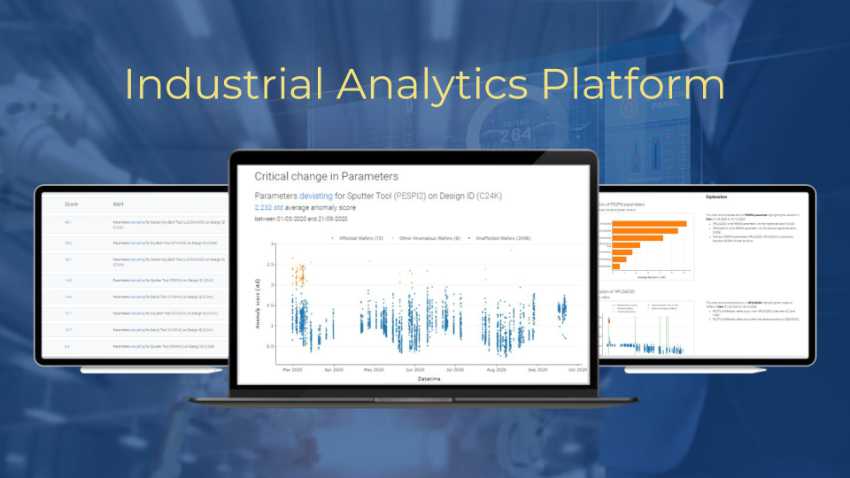
Future outlook
smartFAB continues to innovate, with plans to introduce new modules targeting energy cost savings and the estimation of the residual life of critical components in the manufacturing process. This will further enhance the portfolio of solutions available to manufacturers. In particular, the modular nature of smartFAB’s solution is a key factor in resolving existing challenges and setting the stage for continuous improvements in efficiency and productivity as data maturity and understanding of production frameworks and challenges evolve within the manufacturing sector.