Freshape is a Swiss GreenTech company developing next-generation technologies that fuse performance with sustainability. The company’s work spans materials science, solar-powered systems, and integrated digital technologies, each designed to reduce environmental impact while meeting the real-world demands of engineering, manufacturing, and industrial design. With R&D facilities, manufacturing and offices in Switzerland and China, Freshape’s goal is to provide disruptive technologies to industries and consumers, enabling a more sustainable future.
Interview with Matthias Henchoz, International Marketing Lead at Freshape SA.
What are the main areas of activity of the company?
Matthias Henchoz: We focus on three primary innovation tracks:
- Hi Materials – Advanced material development, including bio-based, recyclable alternatives to synthetic composites like carbon and glass fibers.
- Sun Appliances – Practical, user-ready solutions for solar energy usage, food production, and water access.
- Roles Agent – Natural interaction technologies aiming to create more intelligent, natural digital experiences that adapt to context and user roles.
What’s the news about new products/services?
M.H: Our latest and most significant innovation is HiWood, the world’s first wood fiber paper reinforcement. It combines high-performance mechanical properties with bio-based sustainability, targeting industries that traditionally rely on energy-intensive materials like carbon, glass, or metal. It was just awarded the SAMPE China Innovation Award, underscoring its readiness for industrial application. Since its launch at JEC World 2025, we have received interest and orders from a wide variety of industries, from sports equipment and light mobility to automotive, marine and aerospace. We are excited to further develop our material for these diverse product applications.
What are the ranges of products/services?
M.H: Each HiWood format is designed to easily integrate into conventional composite manufacturing processes without major tooling changes.
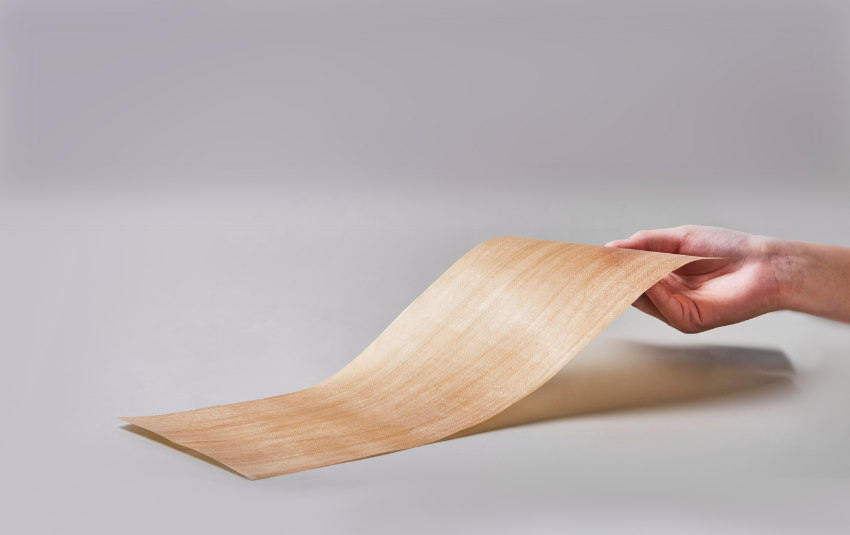
The current HiWood product family includes:
- HiWood Fiber Paper (UD) – A dry continuous unidirectional wood fiber paper with excellent mechanical properties, rivalling conventional materials like glass fiber reinforcements.
- HiWood Epoxy Prepreg – Epoxy-impregnated versions suitable for vacuum bagging, autoclave, and compression moulding.
- HiWood PA Prepreg – A thermoplastic (polyamide) version for thermoforming and stamping, with recyclability and reprocessing ability.
What is the state of the market where you are currently active?
M.H: The composite materials industry is at a pivot point. Engineering teams are under pressure to decarbonize without compromising structural integrity or scalability. Natural fiber composites have historically fallen short in stiffness, water resistance, performance or durability. HiWood was designed to address those exact limitations, offering true structural performance, industrial scalability, and compatibility with multiple processing routes.
What can you tell us about market trends?
M.H: We see a strong movement toward:
- Bio-based replacements for traditional synthetic reinforcements, even in interior structures and aesthetic components.
- Low-temperature, low-pressure processing to reduce energy input and capital expenditure.
- Circular material systems that integrate recyclability and safe end-of-life strategies directly into product design.
OEMs are actively retooling material strategies in line with upcoming regulations and cost pressure. Using natural materials in their new product designs is a strategy that is being adopted across all industries we are working with.

What are the most innovative products/services marketed?
M.H: HiWood is our flagship innovation: a continuous UD fiber composite reinforcement made from engineered wood fiber paper. With tensile strengths of 450 MPa and a modulus of ~45 GPa at just 1.3 g/cm³, HiWood provides a superior specific modulus and lightweight performance than many conventional materials like steel, aluminium or glass fiber, but in a fully bio-based, recyclable format.
It enables simplified layups, cleaner trimming, and efficient forming, with a beautiful natural wood aesthetic. Unlike woven fabrics, the unidirectional paper format improves fiber alignment and mechanical predictability.
What estimations do you have for the second half of 2025?
M.H: We expect strong expansion in HiWood’s industrial evaluation pipeline. Industry leaders have entered sampling and prototype testing phases with us, so this second half of 2025 will be pivotal for our joint R&D efforts. As we expand into new markets this year, we anticipate many new partnerships in the months ahead.
On the manufacturing side, we just opened a new factory in Shanghai, and we are in the process of scaling prepreg production and parts prototyping capacity to meet demand. This will ensure we can expand our technical collaboration network to support application-specific integration. Growth will be driven by increasing regulatory requirements, combined with the need for commercially viable, performance-grade alternatives to energy-intensive unsustainable materials.