Users choose Senzoro in order to find out which components in their factory do not function properly. When components are not working properly, this often leads to excessive energy consumption or an unplanned equipment breakdown and thus to a production standstill. To prevent this, they have developed the simplest and cheapest solution using ultrasound and artificial intelligence (AI).
Interview with Markus Loinig, CEO of Senzoro.
E.E: Give us some examples of projects in which your products / solutions were used?
M.L: The application areas are manifold; our solution has been used for a wide range of projects.
One example is the monitoring of CNC spindles. CNC spindles cause quality problems at the end of their service life, and finding the cause is not possible with reasonable effort due to the many machining steps. For this reason, CNC spindles are replaced either too early or too late in daily practice. Spindles with high wear that are replaced too late cause excessive costs because there is no repair compensation. With our solution, CNC spindles can be measured quarterly, monitored by means of a health indicator per spindle and replaced in a data-driven manner. “Normally” damaged spindles can still achieve a revision revenue of about 8,000 €.
Another example is the detection of cavitation in the pump area: Occurring cavitation is one of the main reasons for increased wear in turbines and pumps of all kinds. When steam bubbles arise in a liquid at certain points in the system, this is called cavitation. The steam bubbles occur when the static pressure in a system, the temperature and the steam pressure do not match. Physical processes cause these steam bubbles to burst again and, like micro-explosions, attack and destroy the surfaces of rotating blades in pumps and turbines. This “bursting” of the bubbles emits acoustic emissions in the ultrasonic range, whereby cavitation monitoring can be realised by means of ultrasonic sensors. The whole case study can be viewed on our homepage (https://en.senzoro.ai/post/case-study-detection-of-cavitation).
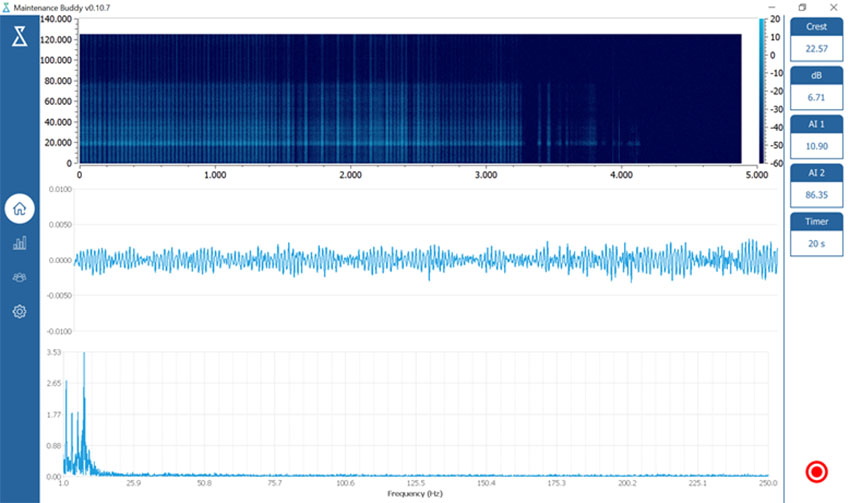
E.E: What products / solutions were used in these projects?
M.L: We use BeepMeep®, the world’s most intelligent mobile ultrasonic measurement system. BeepMeep® consists of an industrial tablet and acoustic sensors (ultrasonic) which adhere magnetically to components. One measurement takes about 30 seconds, after which the data is sent to the AI. The evaluation of the data takes place completely automatised.
A brief insight into how the system works, provides this 40-second video:
E.E: What special characteristics do your products / solutions have compared to others?
M.L: The special about our solution is that we evaluate everything fully automatized with AI. Using the example of roller bearings, the AI has been trained on the basis of 40,000 measurements. And it does not end there: the AI is self-learning, becoming even more accurate with each measurement. Another big advantage is that there are no investment costs because it is a mobile measuring device. And not to forget: our technology works from day 1.
E.E: How did your products / solutions improve productivity / efficiency for the users?
M.L: Our solution improves productivity and efficiency by predicting failures, thus reducing unplanned downtimes. Users also benefit from lower spare parts costs because fewer parts are replaced and because they are replaced more accurately. The service life of components is utilized for longer. Last but not least, energy costs are saved because non-functioning components such as steam valves and poorly lubricated bearings are detected. This is crucial considering that even a small leak can result in up to 30 % of the energy used being lost. Poorly lubricated bearings also belong in this category, because they generate friction, and friction in turn leads to higher energy demand and thus higher energy costs. And not only that: lubrication problems are often the cause of plant downtimes. 80 percent of premature rolling bearing failures alone can be traced back to this. It is a cycle and our users benefit in many ways.
Detailed field reports, case studies and background information you can find in the blog section on our homepage: https://en.senzoro.ai/blog-de.
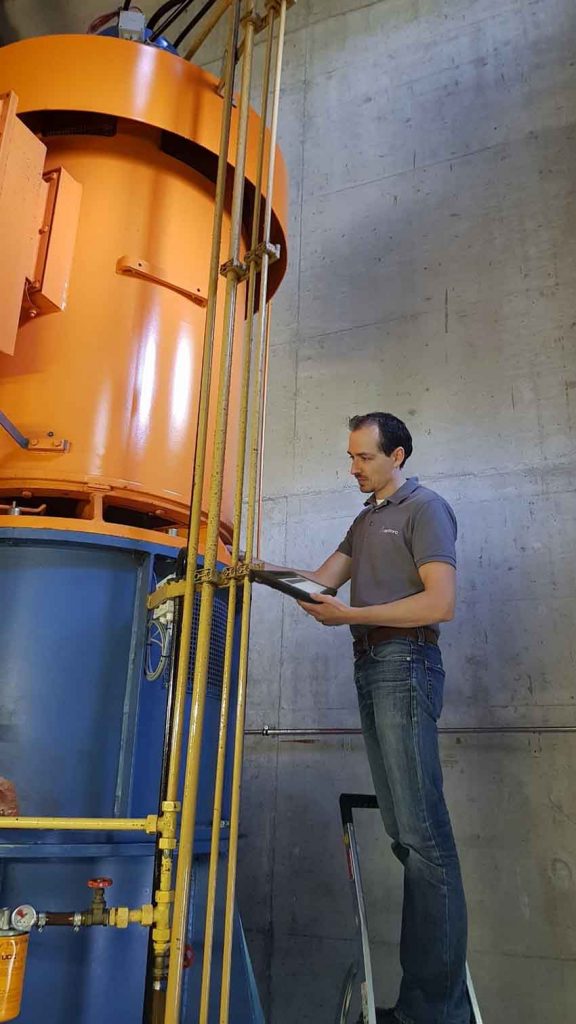
E.E: What was the feedback from users?
M.L: Users appreciate our technology as very simple, very precise and immediately applicable.
A customer from the paper industry always had the problem that his slow-turning bearings failed unplanned. With Senzoro, he has finally found a way to monitor slow-turning bearings and replace them in time.
Another customer in the wood industry had previously used vibration measurement. Due to the weight of the logs and the constant load changes, this did not work and he switched to our technology. He is happy that he has finally found a solution that works.
E.E: How do users work better with your products / solutions?
M.L: Our solution offers a number of advantages: First of all, it can calculate the remaining service life for certain components such as roller bearings. Replacements can be planned and breakdowns prevented, which in turn has a favorable effect on the cost structure in terms of personnel, spare parts and inventory costs. In addition, there are no investment costs because it is a mobile measuring device. The advantage of using AI is that training takes only 5 minutes and the technology is ready to use from the first second, no specific data has to be recorded at the user’s premises.
E.E: Which are the most successful products / solutions in your lineup?
M.L: Due to its high flexibility, which we have described in more detail above, BeepMeep® is very popular. The range of applications is wide, from monitoring components such as roller bearings, gearboxes and steam valves to cavitation monitoring and optimizing lubrication. More details on the product itself are listed on our homepage (https://en.senzoro.ai/beepmeep).
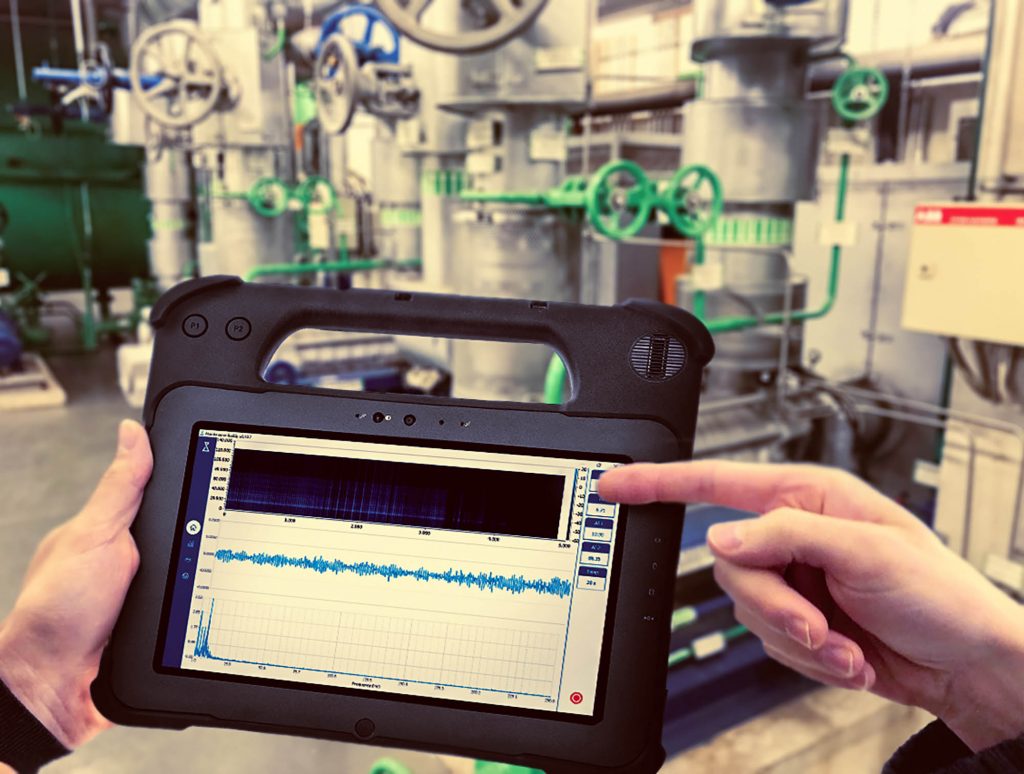
E.E: How important is sustainability in your field?
M.L: Sustainability is an extremely important topic in maintenance. We contribute to achieving the climate goals by reducing wear parts: using components longer saves resources and CO₂. We also reduce energy costs by optimizing lubrication and detecting defective components such as non-functioning steam valves.
This way, we make a contribution to more sustainable manufacturing.
E.E: What are your forecasts for the rest of 2022?
M.L: Energy costs are currently higher than ever. The topic of utilizing existing resources and detecting potential energy savings is therefore more important than ever before. We are fully booked and currently conquering new markets with system partners.
For more information or questions please feel free to visit our website www.senzoro.com or contact us at info@senzoro.com.