3D Lab was established in 2007, and its expertise in additive manufacturing technologies, particularly 3D printing and the creation of new materials, dates back more than 15 years. The company partnered with well-known 3D printer manufacturers such as 3D Systems, Coherent, and 2OneLab, and invested in R&D to overcome obstacles to AM technology development.
Interview with Jakub Rozpendowski, CEO of 3D Lab.
How was 2024 for your business, a short summary?
Jakub Rozpendowski: 2024 was a pivotal year for us at ATO, marked by relentless work in research and development. Despite the challenging condition of the additive manufacturing (AM) market, we treated this time as an opportunity for innovation and growth. Our efforts culminated in the successful creation of the ATO Suite – a complete, integrated ecosystem for metal powder production from start to finish.
Today, we are proud to offer a fully comprehensive solution: from preprocessing technologies and core powder production units to advanced post-processing methods. On top of that, we have developed several critical accessories that address real needs within the industry.
While many slowed down in response to market challenges, we doubled down on development – and the results speak for themselves. We expanded our ATO ultrasonic metal atomization technology and devices portfolio, delivering a suite of solutions for atomizing, sieving, casting, and cleaning both feedstock and atomizer components.
The interest we’re seeing from our customers is a testament to the fact that the market values both technological excellence and strategic foresight.
Additionally, we achieved significant milestones, including the approval of new patents for ATO Technology in USA and China, further solidifying our position as a global leader in metal powder production solutions.
As we move into 2025, we’re well-positioned to drive further innovation and set new standards in AM powder production.
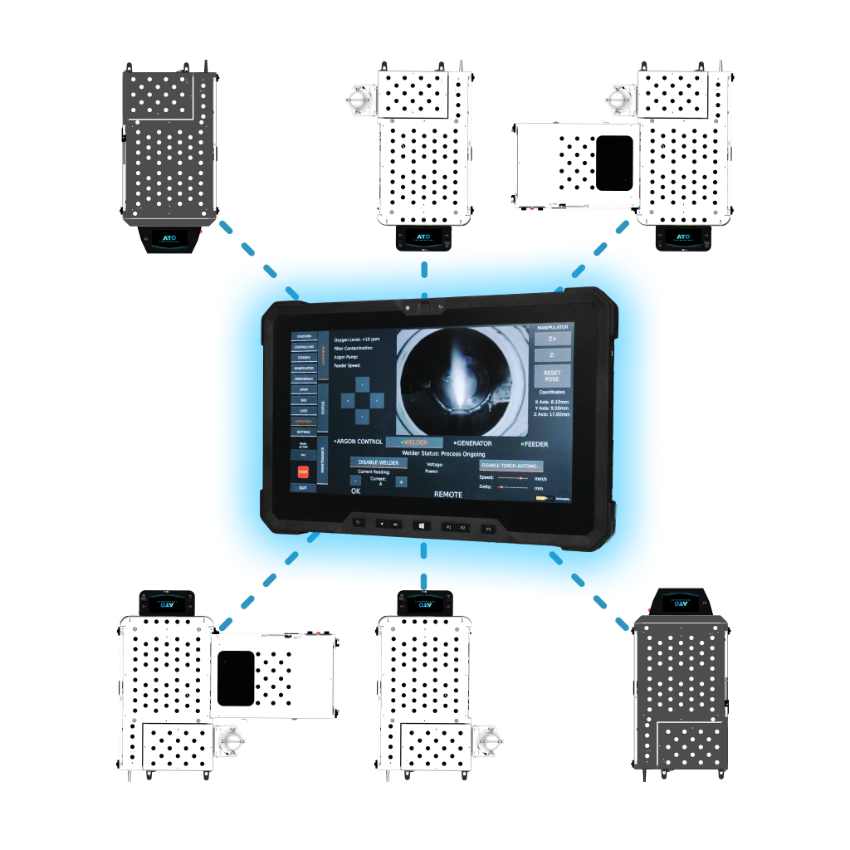
What products/services did you launch this year?
J.R: ATO Wipe: Ultrasonic cleaning solution for metal feedstock, including wires and rods, used in atomization. This system ensures the highest-quality produced metal powder by removing impurities and achieving exceptional chemical purity. It features both manual and automatic modes for cleaning and rewinding specific wire lengths or weights.
ATO Remote Control: A tablet-based system for remote management of the ATO series of atomizers, enabling live process monitoring, real-time adjustments, and the management of multiple atomizers simultaneously. This scalability allows operators to monitor multiple atomizers, freeing up time for other tasks and optimizing overall production efficiency.
ATO Revolver Rod Feeder: An automated system for feeding up to 10 rods (1200mm total) in a gas-protected environment, ensuring consistent feedstock quality. Seamlessly integrated with the rods size produced by the ATO Cast vacuum casting furnace, it streamlines the workflow from casting to atomization.
How did the market change, compared to previous years?
J.R: In my opinion, ingenuity and responding to current market needs are paramount; companies implementing smarter solutions are succeeding. The future of 3D printing (AM) belongs to those introducing smarter, not just larger, innovations. The AM industry is focusing on real material development needs. Companies increasingly pay attention to sustainable development and ecological use of materials.
The market has become more competitive, with companies emphasizing material innovation to maintain an edge. Rising material costs have also spurred interest in reusing manufacturing scrap to produce high-quality powders, reducing waste and operating costs. This shift highlights the growing importance of circular economy principles and efficient operations.
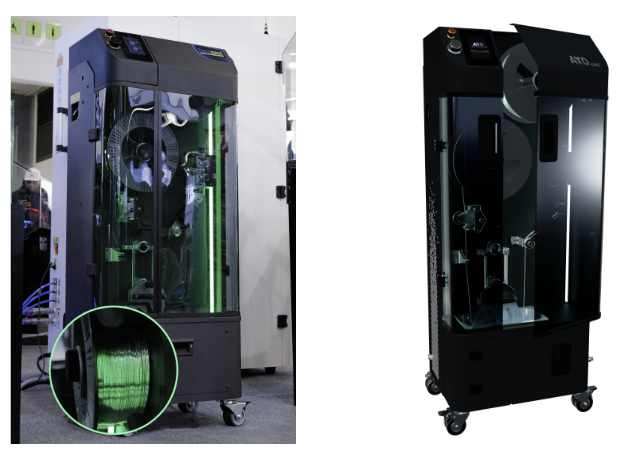
What are the new challenges in your field of activity?
J.R: Key challenges include reducing material waste and meeting diverse material requirements while ensuring consistent powder quality for critical industries such as aerospace and healthcare.
How did you overcome these challenges in this more competitive environment?
We introduced the ATO Suite, a comprehensive set of modular equipment that allows customers to control the entire metal powder production process. This enables a zero-waste workflow that produces high-quality spherical powders with customizable properties. The modularity and flexibility of the suite ensures that customers can adapt and scale their setups as their needs evolve.
Tell us about product innovation and how will it impact the future?
J.R: Product innovation is at the heart of our mission, driving solutions that enable customers to take complete control of their metal powder production processes. Our modular systems are designed to meet different needs, from small-scale development to full-scale production. With the ability to process any feedstock and achieve precise powder characteristics, such as tailored particle size distributions, users can tailor their production for specific technologies and applications. In addition, the no-minimum batch capability of our atomizers supports both experimental research and efficient prototyping, enabling rapid progress in the development of new alloys. For large-scale production, our innovations ensure seamless integration, streamlined workflows and efficient operations to help customers meet evolving market demands. By also incorporating material recovery capabilities, we enable users to recycle production waste into metal powders, optimizing resource use for more sustainable Additive Manufacturing practices.
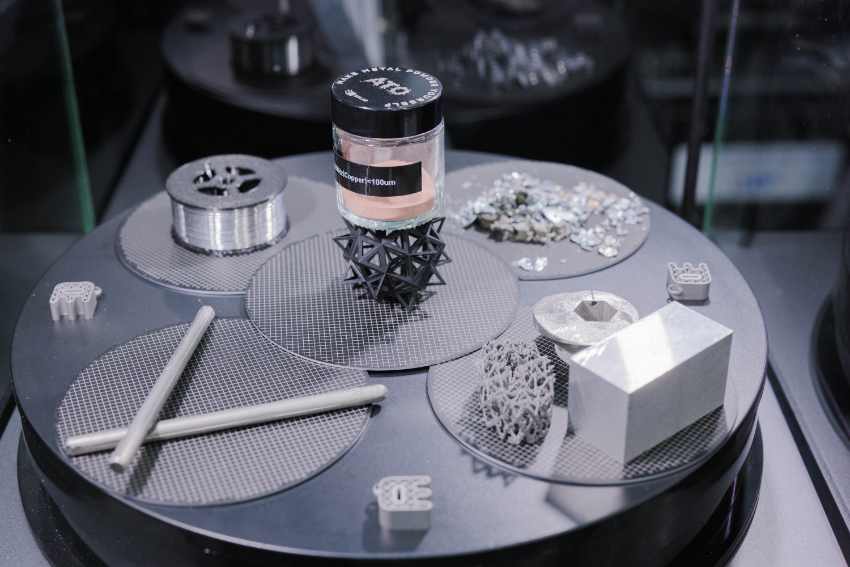
How will product innovation help the customers?
J.R: Our innovations provide customers with the essential tools to produce high-quality metal powders tailored to their specific needs, whether for research, prototyping or mass production. Customers can optimize powders for their unique applications by controlling particle size and material properties. For research and development, this flexibility accelerates the exploration of alloys and materials. In production environments, features such as ATO Remote Control and modular atomizer systems allow users to manage multiple units simultaneously and efficiently scale up to meet mass production requirements. These capabilities streamline workflow, reduce material waste, and ensure operational flexibility, helping customers improve performance, maintain competitiveness, and achieve exceptional results in industries such as aerospace, healthcare, and manufacturing.
What are the industry trends in the markets you are currently active?
J.R: The industry is increasingly focused on efficient material recovery and scalable solutions to address rising costs and reduce waste. Modular and scalable solutions are gaining traction, enabling companies to be self-sufficient in powder production and remain agile in response to market demands. In addition, materials innovation is taking center stage, with novel metal powders playing a critical role in advancing applications across industries. These innovations not only enable greater customization in additive manufacturing, but also improve the performance and capabilities of end products. As companies look for ways to differentiate themselves, the ability to produce specialized powders for unique applications is becoming a defining trend.
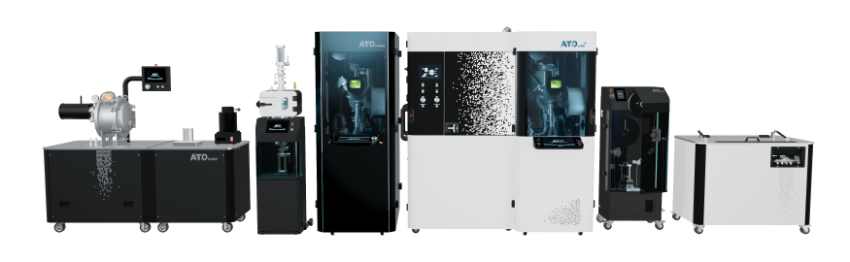
What do you think the trends will be next year?
J.R: Building on the current momentum, we expect to see an increased emphasis on modular, scalable production workflows and in-house manufacturing capabilities. Demand for efficient material recovery and reuse will continue to grow as companies strive to optimize resources and reduce costs. Material innovation will remain a top priority as companies focus on developing unique powders tailored to their specific applications, driving advancements in Additive Manufacturing. In addition, the need for solutions that enable rapid prototyping and small-batch production will become more critical, especially as companies work to shorten product development cycles and improve time-to-market. The growing competitive environment will push businesses to adopt flexible, turn-key systems that can adapt to changing market needs.
What is the outlook for 2025?
J.R: The future of AM belongs to those who innovate smarter, not just bigger. And I repeat once again that AM industry is clearly focused on real needs for materials development.
We will improve the current ATO Suite with new capabilities and functions. You can also expect a new device that is already under R&D – but I hope we will talk more about this in next year’s interview.
We are committed to delivering adaptable systems that meet evolving needs, helping our customers shape the future of Additive Manufacturing.