ALTERO was born from the merger of a team with more than 20 years’ experience in the plastic recycling sector and the company Aranow Packaging Machinery who has been manufacturing machinery for vertical packaging on a global scale for more than 18 years.
For over two decades the team has built their professional career being the technical support in Spain for the leading brands in the sector, installing and repairing different types of machinery for thermoplastic recycling. This has allowed ALTERO to learn a lot about the equipment and machinery used to pelletize plastic waste and we detected some opportunities and some clear weaknesses on the market.
ALTERO now offers comprehensive solutions to recycle plastics consisting of high-performance extruders and complete pelletizing lines combined with the latest technology for remote assistance to guarantee their machines’ optimum performance and drastically reduce maintenance costs. ALTERO’s mission is to offer maximum profitability and efficiency in the plastic recycling industry.
The company’s range of products covers many different applications for post-consumption and post-industrial waste while their unique and personalized designs offer a combination of high-quality components from top European brands and the latest technology in the field.
Interview with Marc Costa, Head of Sales at Altero Recycling Machinery.
Easy Engineering: What are the main areas of activity of the company?
Marc Costa: ALTERO specializes in manufacturing complete pelletizing lines specifically designed for plastic recycling applications.
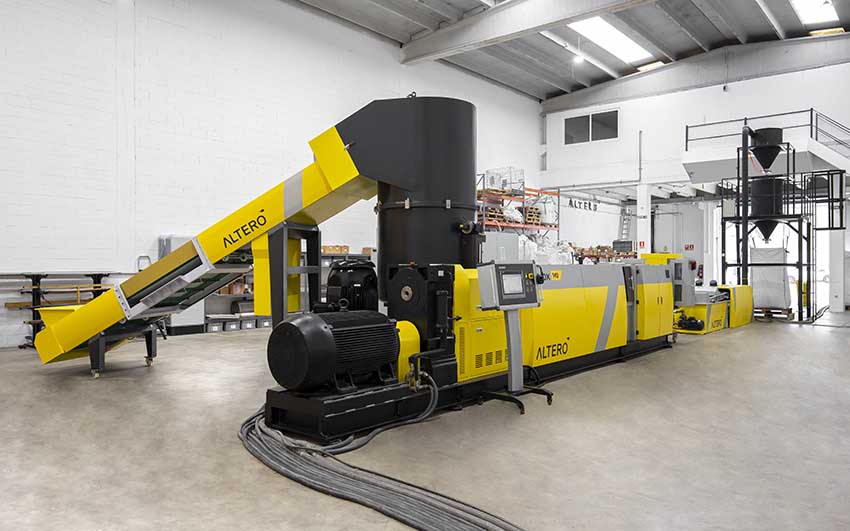
We focus on two different segments:
On one hand, we work with plastic recyclers who specialize in the processing of post-consumer plastic waste making it into reusable pellets. This process involves various steps that must be in perfect coordination and our equipment sits at the end of this value chain and ensures the highest quality possible for the recycled pellets to meet the quality standards the industry demands.
On the other hand, we help plastic transformers close the loop on their own installations. Our dedicated range of equipment excels in pelletizing plastic waste obtained from self-produced plastic scrap. The scrap can be from injection machinery, edge trims from film, sheet manufacturers, etc. With this equipment and our technical support, we help our customers with their circular economy challenges which can improve their profitability.
Finally, we offer consulting services for thermoplastic mechanical recycling to ensure our customers obtain the most appropriate solutions to each project
E.E: What’s the news about new products?
M.C: We are currently developing and improving our IN-LINE machinery, designed to pelletize plastic waste coming directly from blow film machinery. Our equipment is installed in-line with the customer’s equipment with the idea of recovering 100% of the edge trims and roll scraps.
We are adapting the same idea to help process rigid materials from injection molding so we can recover 100% of the scrap on the same line with minimum impact on the layout. As always, we are very focused on energy efficiency, so we try to make the ROI of the equipment as quick as possible.
We are improving the designs for our DUPLO equipment to extract volatiles and we have begun a collaboration with technological centres to implement new solutions on the deodorization of HDPE and other polyolefins.
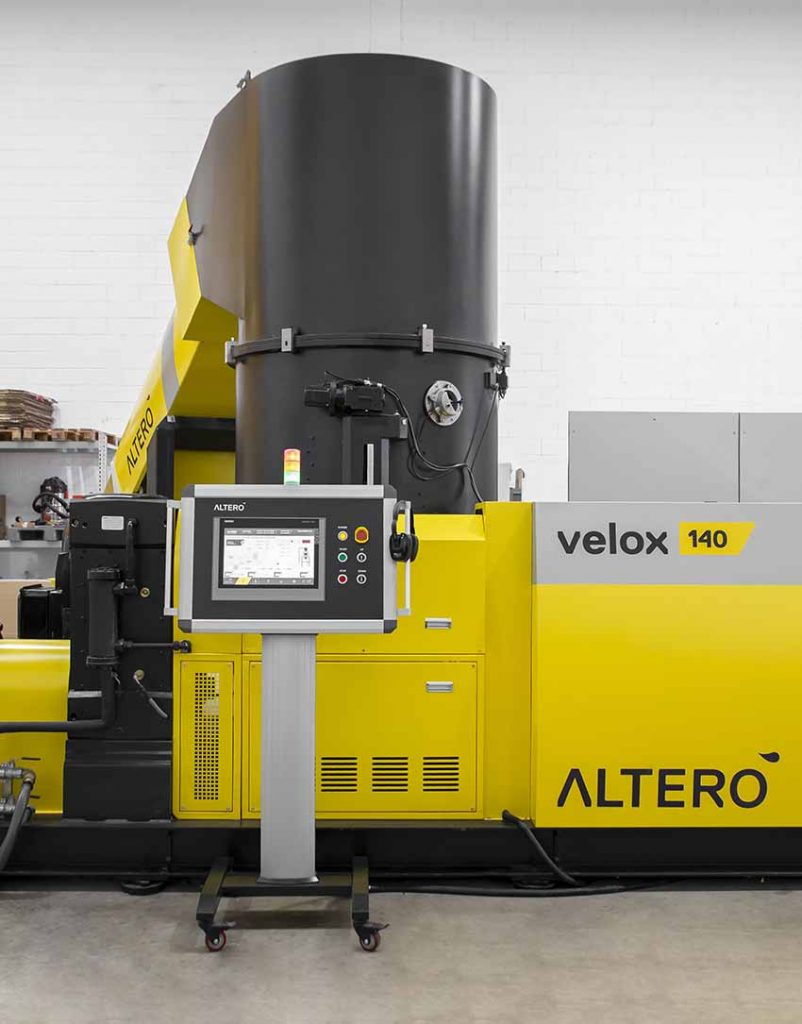
E.E: What are the ranges of products?
M.C: We have four product families, each with the aim to bring solutions to a huge range of customers in the plastic industry.
For post-industrial waste, our OPTIMA machinery is designed to be as efficient as possible on non-contaminated low humidity scrap. This family of product has a simpler design, shorter screws to reduce material degradation and a minimalist approach for energy efficiency and minimal material degradation.
The VELOX and DUPLO families are ideal for post-consumer recyclers.
The VELOX family has the most common design for post-consumer plastic recycling. It incorporates a single-screw extruder made of the best bimetallic steel on the market as well as a double-stage degassing unit, different filter configurations depending on the material and the project, and different cutting systems depending on the viscosity of the material, the customer requirements, and the output of the line.
The DUPLO family is our “cascade” configuration where we integrate a filter system between two single-screw extruders. This configuration is especially adequate to recycle material with high-ink content and/or high content of additives or contaminants that become volatiles during the extrusion process. With this approach, we can extract up to 7 times more gases from the melt.
The last product family is our AQUA range, which has been designed to process PET and PA. Highly hygroscopic materials require special designs and element configurations to ensure minimal intrinsic viscosity loss, as well as to preserve the virgin qualities of the materials. We are currently working on specific designs to help textile manufacturers on their recycling challenges as we have been receiving a lot of interest from Nylon and Polyester industry in regard to the textile recovery process.
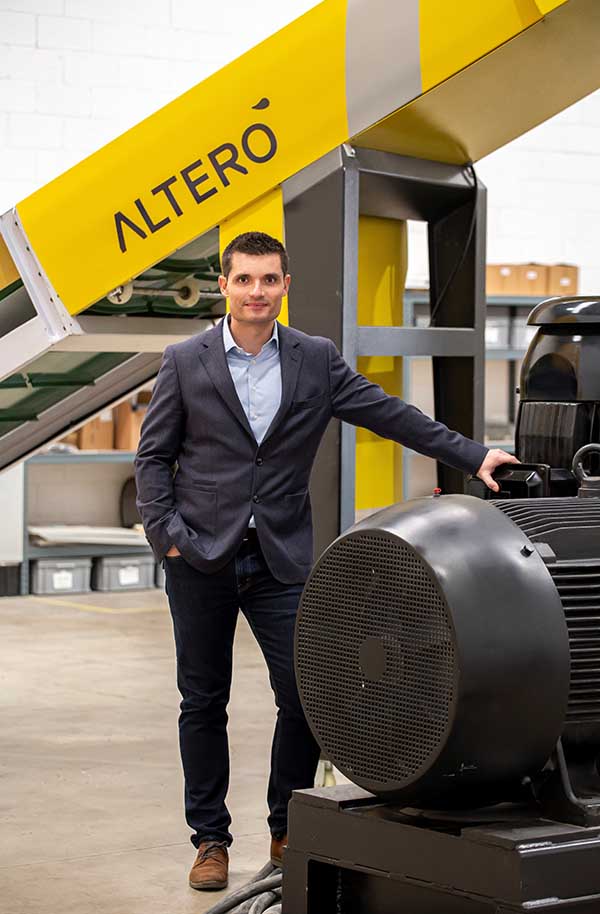
E.E: At what stage is the market where you are currently active?
M.C: The plastic recycling market is growing fast, but its maturity and its infrastructure greatly depends on the geographic region. Europe is the most mature market and is clearly pushing new legislation to increase recycling and circular economy in the coming years. The European market is also under a lot of pressure to grow and improve which is benefiting companies such as ours, who are invested in offering the most energy-efficient machinery to help companies recycle more, better, and at a reduced cost.
In other regions, the maturity varies but we can observe clear signs of growth, sometimes due to legislation and public incentives but mostly due to social pressure. We have also observed a tendency toward high-efficient machinery now the energy cost is so important for the viability of most recycling projects.
E.E: What can you tell us about market trends?
M.C: There is a growing interest in circular economy processes as well as on the revalorization of plastic waste coming from both public and private sector.
As I previously mentioned, In Europe, there is a clear move toward circular economy which increases the demand for recycled materials. Therefore, most companies are looking to increase their recycling efficiency and capacity to keep
up with the new legislation. With that in mind, we can observe improvements in the quantity and quality of recycled plastics such as PE, PP, and PET.
We have also noticed a growing interest in food-grade recycled polyolefins. As the technologies advance, the packaging industry needs to incorporate more and more recycled material and the demand for food-grade polyolefins is growing fast.
We are also seeing a move toward the upcycling in general, with plenty of companies looking into adding value during the recycling process to obtain more technical and high-value materials.
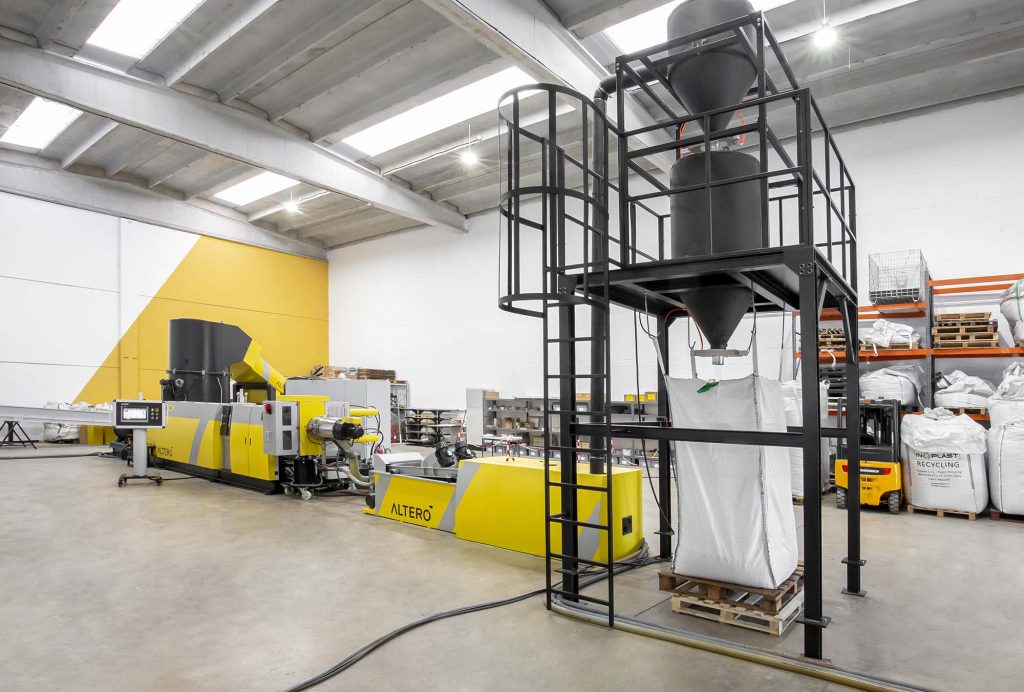
E.E: What are the most innovative products marketed?
M.C: I think the most innovative part of our equipment is the energy transfer technology. We have always aimed to offer energy efficient machinery, with that in mind, we are constantly working and improving our Smart Energy Transfer system where we transfer energy from different areas of the machine to where it is needed in order to save on electrical and mechanical energy. To achieve that we require constant monitoring and a special design on some key areas of the machine to ensure we can transfer the energy safely and efficiently.
We are very proud to collaborate with technological canters in Spain and Switzerland, where we are developing some R+D projects that will soon be ready to market.
E.E: What estimations do you have for 2022?
M.C: We are very happy with what we’ve achieved in 2022 so far. We have closed very important deals, participated in PRSE and PLASTPOL and the interest and response of the markets have been very positive. We have signed with TH plastic to represent our company in the UK recently and we are currently preparing our attendance to the K-Show next October. This event will help us to reinforce our position internationally and with that we are looking forward to new projects.
For the second part of 2022, we will continue to establish ourselves in key markets in Europe and abroad and build relationships with partners to create references in these markets.
In short, we are very optimistic about the future.