Element Six, part the De Beers Group, was founded in 1946 and has developed into a global leader in synthetic diamond and supermaterials manufacturing. As a business, te company harnesses the unique properties of tungsten carbide and synthetic diamond to deliver supermaterials that improve the efficiency, performance and reliability of industrial tools and technology.
Their expertise lies in the ability to engineer and manufacture materials that help customers do things better, faster and for longer, be that a polycrystalline diamond (PCD) tool for machining aeroplanes, or a tungsten carbide insert that better prevents wear in tunnelling operations.
Interview with Markus Bening, Global Sales Director, Mining, Road & Wear Products at Element Six.
Easy Engineering: What are the main areas of activity of the company?
Markus Bening: Element Six’s material expertise, which has been developed over more than 75 years, is utilized in a wide range of industries and operations worldwide.
As mentioned previously, our diamond and CBN powders, PCD and polycrystalline cubic boron nitride (PCBN) solutions offer new levels of precision and efficiency for automotive and aerospace manufacturing, where new technologies and materials are demanding new cutting solutions. We collaborate with toolmakers and manufacturers to create solutions that support smarter and more efficient manufacturing.
Moreover, our world-leading, high quality chemical vapor deposition (CVD) diamond has applications in electronics, as diamond heat spreaders enable device designers to run higher power levels without increasing junction-operating temperature. Within optical applications, CVD diamond can also enhance power scaling and durability, while also supporting the sanitization of wastewater and accelerating some of the most ground-breaking quantum applications for sensing and healthcare.
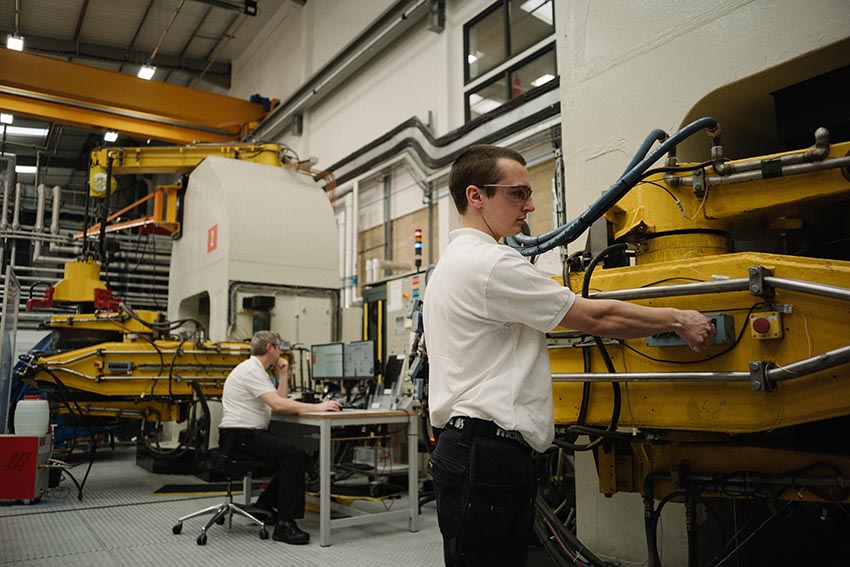
Additionally, Element Six provides an extensive portfolio of high-quality synthetic diamond solutions, supporting the semiconductor and electronics manufacturing value chains at every stage, from “front end” wafer fabrication, “back end” assembly, packaging and testing, to final electronic device production.
The area of our business which I am responsible for includes our tungsten carbide and synthetic diamond solutions, providing for industries such as mining, road milling, construction, as well as agriculture and forestry. We utilize our materials to develop versatile product ranges capable of withstanding tough environments and the specific challenges that these operations present.
E.E: What’s the news about new products?
M.B: This year, Element Six launched the HD™ Series, a new range of heavy-duty tools specially designed to provide superior performance, extended tool life and improved reliability for milling and reclaiming operations.
The products combine a large body and washer disc with Element Six’s premium MasterGrade™ carbide. The tools’ larger body has by design more steel, which leads to extended tool life and increased wear resistance, improving performance in highly abrasive conditions where the steel body typically wears quickly.
The HD™ Series gives operators a choice of four new MasterGrade™ bits, enabling them to select the tool that best meets the need of their application, achieving superior performance while reducing overall tool costs.
In addition, we have recently introduced a new, state-of-the-art, fully automated line for manufacturing road milling bits, such as the products in the HD™ Series. The multi-million-dollar investment has expanded our capacity- enabling us to service customers more efficiently thanks to faster production speeds at our Burghaun facility in Germany.
In line with this, we have made our control steps more integrated -to further improve product quality and create greater flexibility thanks to the ability to address the manufacture of our entire road milling range. In essence, the line has automated the production of our carbide tools.
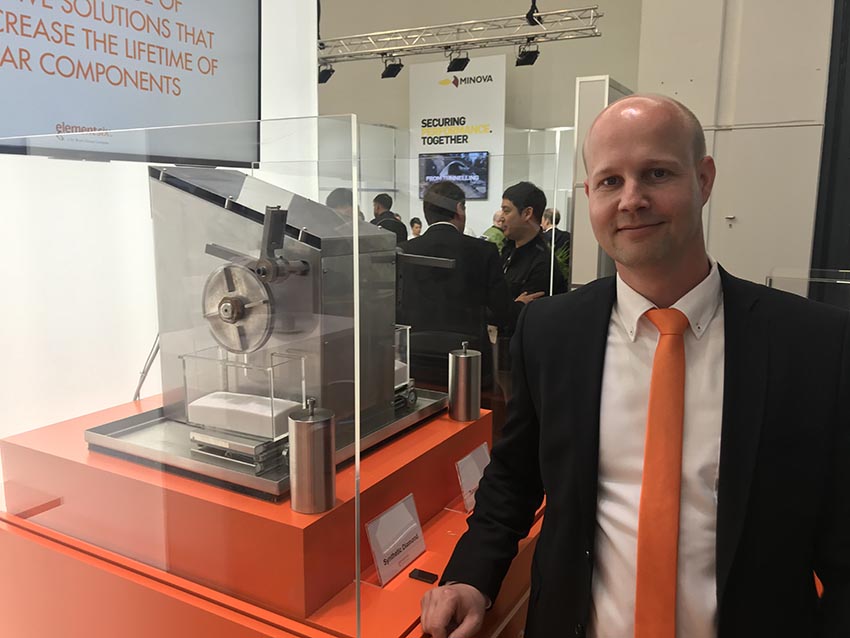
E.E: What are the ranges of products?
M.B: Element Six has been supplying the road milling and mining industries for decades, with its tools being used in a wide range of applications, each presenting its own, unique challenges.
To overcome these challenges, the MasterGrade™ range uses our proprietary ‘nanotechnology’ to enhance the cobalt binder matrix and optimize wear without impacting the bit’s toughness. For road milling, MasterGrade™ M-Series road bits use this nanotechnology to provide greater wear resistance and fracture toughness. The result is a versatile, economical road bit with up to 50% greater life expectancy compared with standard bits. In addition, the MasterGrade™ technology is also available for our mining bit range, specially designed for conditions that require longer tool lifetime.
Element Six also offers a complete range of tungsten carbide products in the form of ready-to-press powders, bespoke products and industrial wear parts, -such as- valve and bearing parts for the oil and gas industry as well as metal forming applications.
E.E: At what stage is the market where you are currently active?
M.B: Innovation has always been at the heart of what we do. That’s why, across all areas of our business, we work with a range of organizations, from universities and start-up businesses to mature and established suppliers. It’s this commitment to research and development, and the breadth of coverage across industries, that allows us to take advantage of the latest in scientific innovation and technology and adapt them for our customers’ gain.
E.E: What can you tell us about market trends?
M.B: Our tungsten carbide products operate in a range of sectors, from construction to road milling, as well as mining and oil drilling. What is common among those markets, alongside almost every other, is that there is constant demand for better, longer lasting parts.
Efficiency truly is the name of the game when it comes to toolmaking. A bit with a longer lifetime means fewer changeouts, reduced downtime and, when combined with our synthetic diamond or tungsten carbide materials, better overall performance.
All of our customers are facing growing pressures, from increasing costs to staffing issues that are likely to be sustained. Element Six products are able to deliver one piece of the jigsaw to help lower their overall costs and improve production.
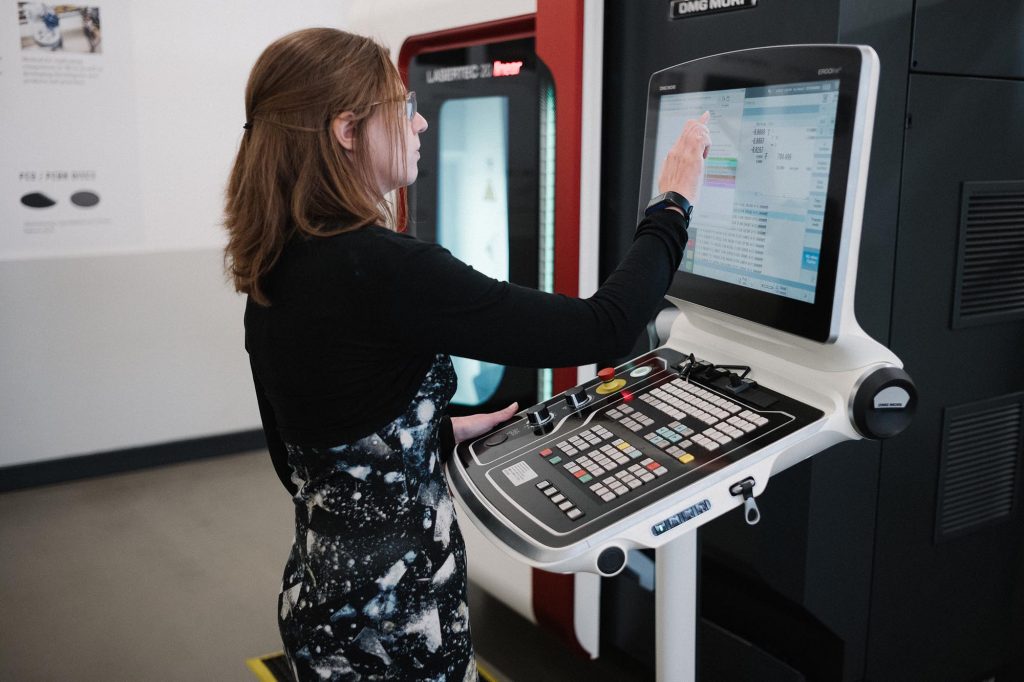
E.E: What are the most innovative products marketed?
M.B: Within the carbide section of our business, the MasterGrade™ product range is still, without doubt, one of our most innovative, although new R&D projects are progressing with leading OEMs for the relevant sectors, focussing on synthetic diamond-based solutions for the mining and construction industries.
E.E: What estimations do you have for 2022/23?
M.B: Owing to worldwide rising energy costs and the urgent and growing need to reduce carbon emissions, the need for efficiency and durability within the sectors I have mentioned previously will continue to be front of mind. While these pressures continue to affect industry, Element Six tools can support businesses to improve their operational efficiency and performance.