Liqtra GmbH is based in Hamburg, Germany and was founded in 2019. With a team of currently 13 people, the company builds Material Extrusion 3D printing technology for polymers.
Interview with Joscha Krieglsteiner, Co-Founder of Liqtra GmbH.
Easy Engineering: What are the main areas of activity of the company?
Joscha Krieglsteiner: We build 3D printers and the software to operate them. Our proprietary technology consists of printer hardware plus in-house software solutions along the whole process chain: web applications, process planning and firmware.
E.E: What’s the news about new products?
J.K: We recently launched the LIQTRA™ FX-7 Pro at Formnext 2022. It is the first multi-nozzle 3D printer on the market. It processes polymer filaments into technical parts much quicker than any other Material Extrusion printer and without compromise on geometrical details or part strength. Cutting the process time by -75 percent is particularly helpful to serve ad-hoc printing demands as seen in repairs, medical aids or manufacturing aids. Customers in med tech for example can provide patients with individual medical aids in the shortest time frame. What formerly took a few days to print, can now be done overnight with the LIQTRA™ FX-7 Pro.
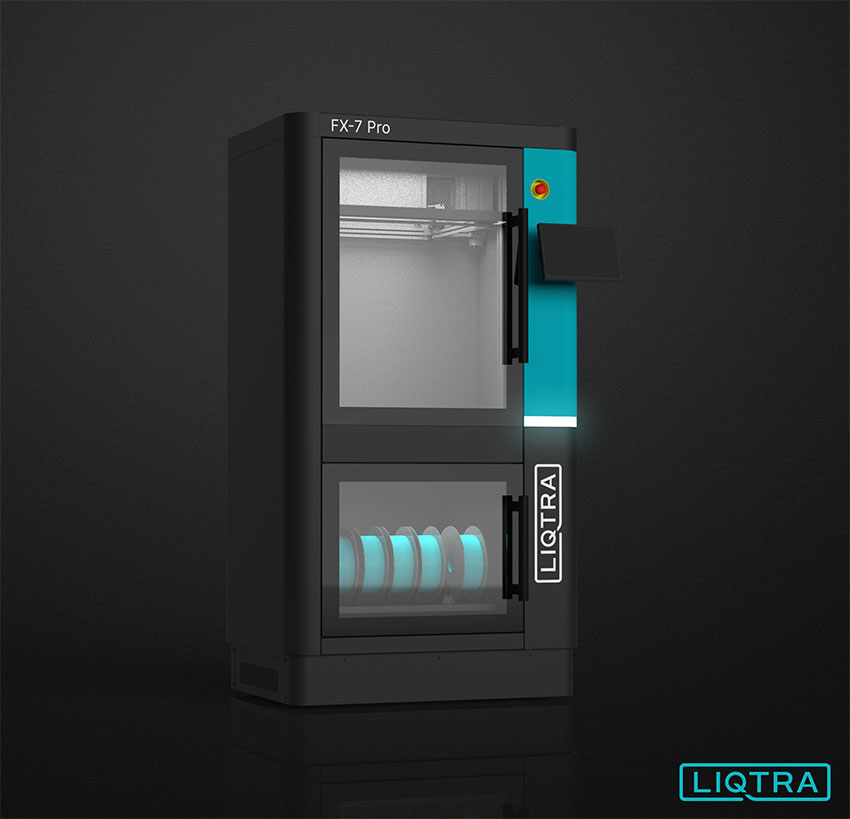
E.E: What are the ranges of products?
J.K: We provide different Material Extrusion 3D printers. Apart from filament printers, we are going to offer a pellet-based printer line, which is currently under development. As an addition, we offer design and printing services.
E.E: At what stage is the market where you are currently active?
J.K: The 3D printing market has been growing rapidly in the last years and all forecasts see it keeping this trend. For our field of industrial polymer printing systems, forecasts see the market tripling in the course of the next four years.
E.E: What can you tell us about market trends?
J.K: A lot of activity can be observed in the process chain before the actual printing process. With the goal of making 3D printing applicable more easily software solutions help the users to identify the right parts to 3D print, to design parts with respect to their printing process or to tune the process parameters.
On our side, we designed our technology for easy usage right from the start. We use artificial intelligence and numerical optimization to keep the complexity away from the user and make the technology also usable for non-experts.
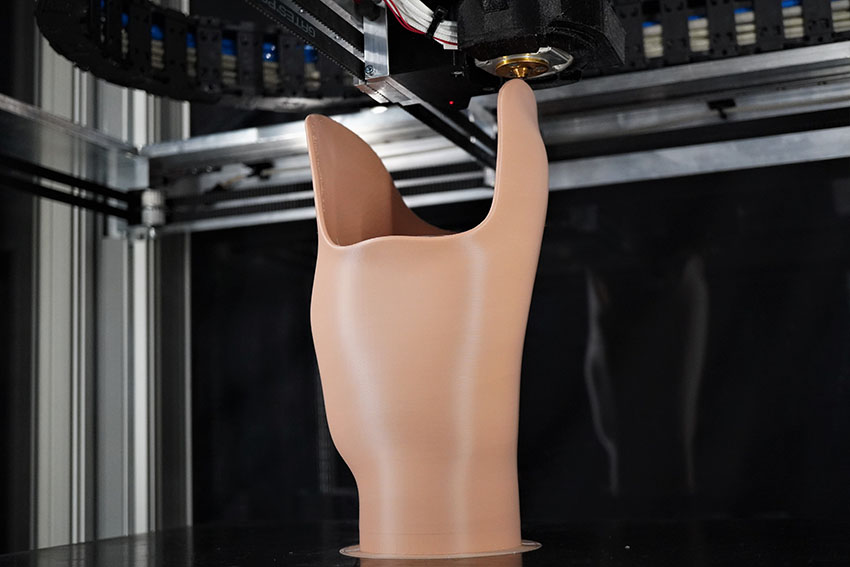
E.E: What are the most innovative products marketed?
J.K: Our multi-nozzle technology is a major progress in material extrusion 3D printing. Using multiple nozzles in one print head simultaneously instead of just a single one solves a number of problems at the same time:
- Productivity is boosted by +300 percent, an urgently needed cut to the former long process times of 3D printing
- Part strength in build direction experiences an increase by +37 percent, which neutralizes a well-known weak spot of 3D printing
- Multi-material printing opens the door for new functional integrations and sustainable solutions in part design.
E.E: What estimations do you have for the rest of 2022?
J.K: For the few days left of 2022 we are going to be busy following up on the contacts we made at Formnext 2022. Particularly the end-of-year offers announced at the trade fair give us a lot of traffic at the end of the year.