Lithoz is the world market and technology leader for 3D printers, materials and solutions for the industrial production of high-performance ceramics. Based in Vienna, Austria, Lithoz aims to establish ceramic 3D printing as a reliable manufacturing technology for industrial production. Since its founding in 2011, the company has developed a wide range of 3D printers, ceramic materials and training programs in use worldwide, including in Asia, Australia and Brazil, while the founding of a subsidiary in America has allowed Lithoz to better connect with customers and strengthen the company’s global presence.
Easy Engineering: What are the main areas of activity of the company?
LITHOZ: Lithoz specializes in creating 3D printing solutions and materials for ceramic manufacturing, covering applications in fields ranging from aerospace, medicine and industries requiring highly durable, complex components. Their CeraFab printer range covers the entire production workflow, with the CeraFab System printers being specifically designed for the manufacture of first parts all the way up to serial production. Lithoz has also added more specialist machines to their 3D printer line, including 2020’s launch of the CeraFab Multi 2M30.
A breakthrough in the 3D printing world, this printer is able to combine ceramics, metals and polymers not only in varying layers of a component, but also within a single layer. Such material combinations open the door to completely new applications in various fields as component properties can be greatly improved – they have already seen success using the CeraFab Multi with the printing of the strongest alumina ever achieved.
Finally, in a world becoming ever more digital, Lithoz has ensured that its machines are suited for the future of manufacturing by all being Industry 4.0 and IIoT ready, offering innovators an entirely digital warehouse of easily customizable and accessible CAD designs. The entire AM method is modelled after digital independence, making this manufacturing technique perfect for independence and stability in today’s industry.
E.E: What’s the news for 2021 about new products?
LITHOZ: Lithoz has already had a very exciting 2021 with the launch of the CeraFab Lab L30, their shop-floor friendly 3D printer. The first of its kind in their range, this machine is suited for those new to the ceramic market, as well as for those looking to expand their 3D printing capabilities. It has been specifically designed for fine-tuning component designs with its rapid and economical production of first parts, allowing for rapid entry into the 3D printing market across diverse fields. This 3D printer enables the development and use of own materials, while the near-limitless design freedom offered by the LCM process opens the door to new markets and applications to drive your product innovation further than ever before.
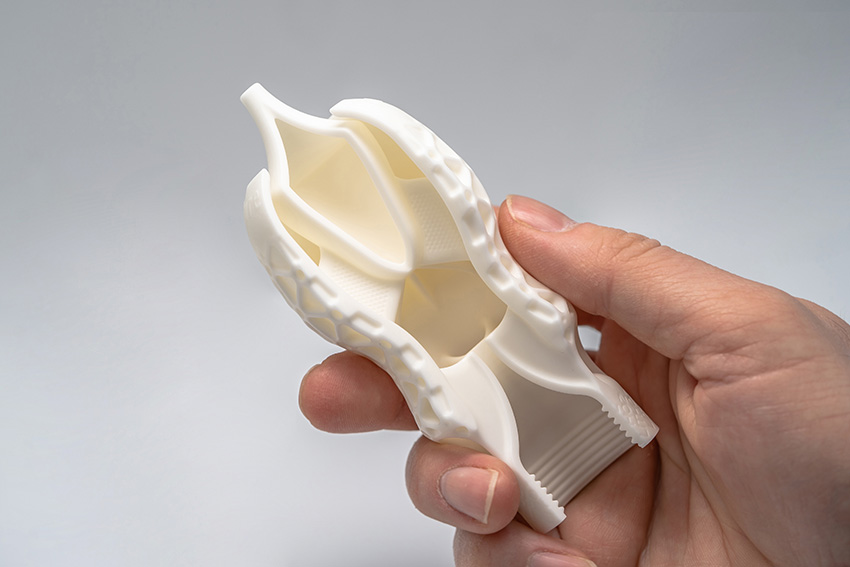
E.E: What are the ranges of products?
LITHOZ: Lithoz offers innovators a range of 3D printers and ceramic materials for a broad variety of applications. Their machines have been specifically designed to cover the entire production workflow from first part to large-scale production. Using the CeraFab Lab L30 allows companies to develop and fine-tune their products before using the CeraFab System (S25, S65 and S230) to print the component in larger volumes.
Lithoz also has a wide range of ceramic materials on offer for the industry, including aluminas, zirconias, zirconia toughened aluminas, silica-based as well as silicon nitride. In addition, medical-grade, bioresorbable materials are available which can be used for bone replacements and implants. Advanced software solutions are also on offering. The CeraFab Control software is a powerful database-driven software platform to promote complete traceability, intelligent data analysis of production related data and greater efficiency in manufacturing.
E.E: At what stage is the market where you are currently active?
LITHOZ: In a world that is becoming ever more digital, ceramic 3D printing is fast growing into an established production technique. The fact that 25% of Lithoz customers have invested in multiple additive manufacturing systems highlights the success they have had with this technology. They believe AM to be a growing manufacturing market – and they are not the only ones. A recent SmarTech Analysis study has shown that the additive manufacturing industry is expected to grow over the next decade to become a $4.8 billion market by 2030, with the area of technical applications representing the most significant sector for driving market growth to over $3 billion. The adoption of ceramic AM is expected to rapidly increase, with the main inflection point being in 2025 as major ceramic AM technologies come to maturity and benefit from having enough of a presence in the market to support the serial production of final components.
E.E: What can you tell us about market trends?
LITHOZ: Additive manufacturing is becoming more and more widespread in the manufacturing world thanks to the advantages it offers innovators. The nature of the process through the utilization of digital CAD files means AM is IioT and Industry 4.0 ready, bringing companies closer to a Factory of the Future set-up. The CeraFab System has also been specifically designed for scalability, where manufacturers can utilize multiple machines to enter into mass production. Finally, multi-material 3D printing is a growing area of interest due to the new applications being unlocked with this innovative technology. Lithoz’s CeraFab Multi 2M30 allows innovators to take advantage of these new industrial applications by developing stronger and more durable ceramic materials for high-performance components.
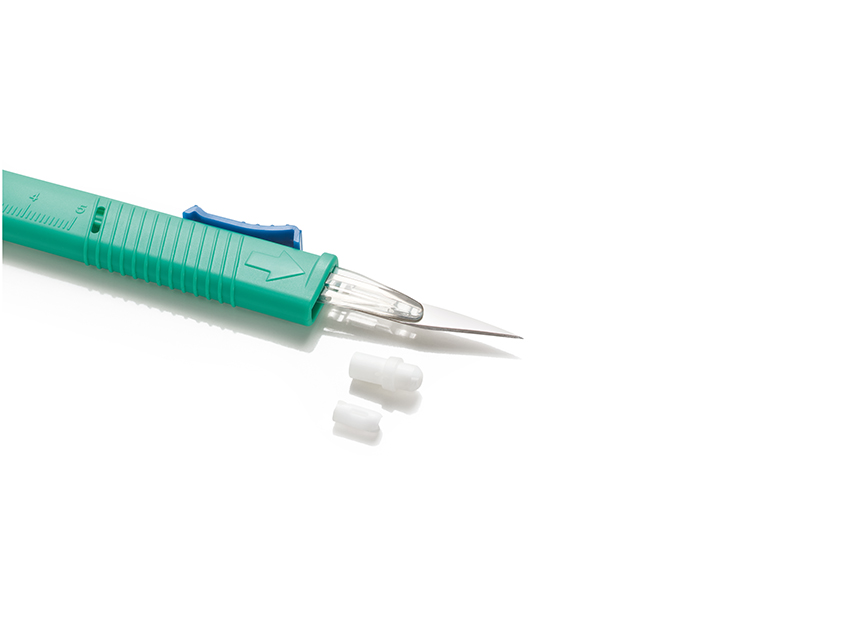
E.E: What are the most innovative products marketed?
LITHOZ: Lithoz aims to provide companies with powerful 3D printing technology and materials and, in this way, enable their partners to truly bring innovation to the market. By facilitating the rapid and sustainable production of high-quality ceramic parts, Lithoz customers are able to break into entirely new markets and experiment with new applications. The ease with which this process allows for mass customization means that manufacturers can be as specific or broad with design changes as they wish, giving them far greater levels of design freedom than is achievable using conventional manufacturing techniques.
The addition of multi-material 3D printing to this arsenal of manufacturing tools only allows for even greater innovation by companies, and Lithoz are looking forward to see the future designs and applications that their flexible 3D printing solutions have enabled.
E.E: What estimations do you have for 2021?
LITHOZ: As the market recovers from the COVID-19 pandemic, there will be new applications springing up and innovative products released. Since Lithoz’s founding 10 years ago, their partners have grown in skill and are now using Lithoz technology to its full potential. We predict that companies will start showing the results of being ahead of the game when it comes to additive manufacturing through promoting new products only manufacturable using this technique.
More and more companies are gaining serial production capabilities thanks to CeraFab System printers which will allow for a greater launch of new designs and thus facilitate rapid entry into new industries, enabling market growth across fields. Finally, as the technology becomes more well-known, the range of applications is broadening – new players in various fields are entering the ceramic AM market, finding new applications in the process and innovating past traditional ceramic companies. This puts them at a great advantage, allowing them to explore new design ideas and functionalities unachievable using conventional forming techniques.
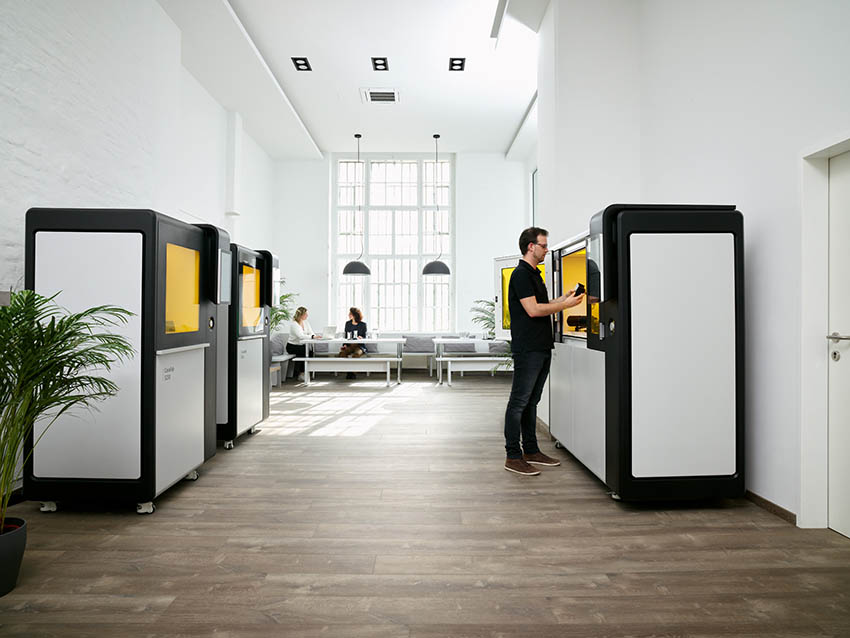
Additive manufacturing gives businesses a secure supply chain in a way other production methods simply cannot. This independence has made AM invaluable for many companies during the pandemic, as they could be self-reliant in times of economic and manufacturing uncertainty. The entire AM method is modelled after digital independence – once a customer has a digital file of the part, components can be produced and edits made to reach certain parameters and files can be saved and accessed anywhere in the world. Where there is a 3D printer, this part can now be produced. The use of digital files opens up an entire digital warehouse for the customer, making it easy to gain new connections and innovate with others in their field.
Ceramic 3D printing is very well suited to today’s and tomorrow’s manufacturing, no matter what field a company is based in, and the market will grow rapidly as more businesses implement AM as a serial production method to find new innovative applications and enjoy the advantages of digitalization and a stable supply chain.