Founded as a specialist in gear cutting for watchmaking and instrumentation, MICROINGRANAGGI has evolved quickly over the years to encompass several market sectors. Step by step, project by project.
MICROINGRANAGGI has been imagining, designing and engineering precision mechanical and electromechanical micro components since 1973.
Today, the company is able to offer customers a know-how covering a variety of sectors: automation, robotics, packaging, domotic, but also medical applications, shipbuilding, textile, automotive/racing, Aerospace and Defence.
Interview with Marco Garavaglia – Marketing & Sales at MICROINGRANAGGI.
Easy Engineering: What are the main areas of activity of the company?
Marco Garavaglia: Our mission is to provide our customers with the best micromechanics solution from a wide range of products including precision kinematics, industrial components, planetary and cascade gearmotors, electrical linear actuators, gears, worm screws, pulleys etc.
The factory, a 3.000 sqm plant located near Milan, is equipped with more than twenty CNC machines for tuning and gear hobbing, an assembly department assisted by specialists, a controlled temperature metrology room for dimensional precision measurements as well as three automatic warehouses.
We support our clients also with external services, working closely with trusted partners for grinding, heat treatments and similar activities.
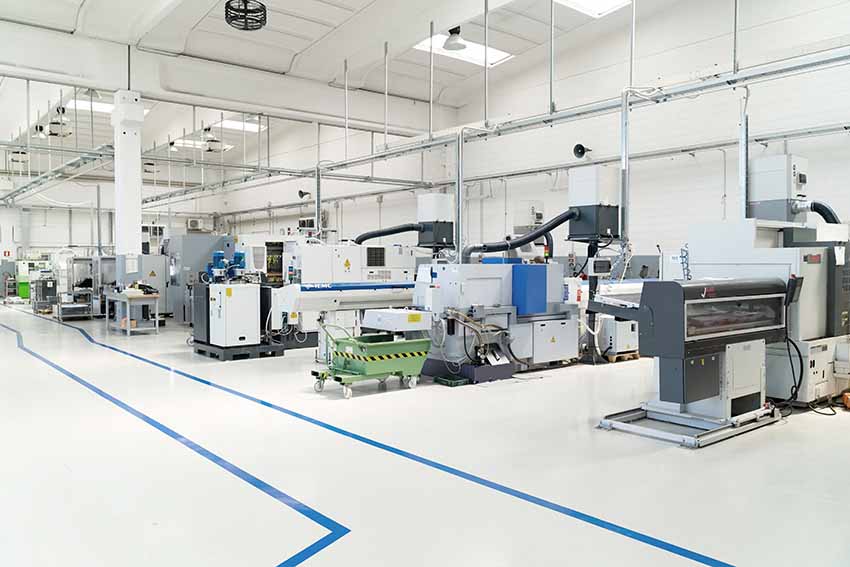
E.E: What’s the news about new products?
M.G: We have always worked as subcontractors, therefore without having a standard list of our products. In the last 10 years, however, thanks to the creation of an internal R&D office, we have begun to develop some standard products. Today we have several families of gearmotors and actuators, from Ø22mm to Ø45mm, and with different motor coupling possibilities.
In particular, last year we introduced our re-styled Ø28 gear motor, improved in quality and performances, and the brand new Ø22 linear actuator.
In 2022, we are planning a re-styling of our main Ø45 gear motor, together with another couple of projects that we can’t talk about yet.
E.E: What are the ranges of products?
M.G: As mentioned before, our standard products are gear motors and linear actuators, covering the diameter range 22-45mm.
However, our main volumes are based on custom products, both assembled parts as well as single components.
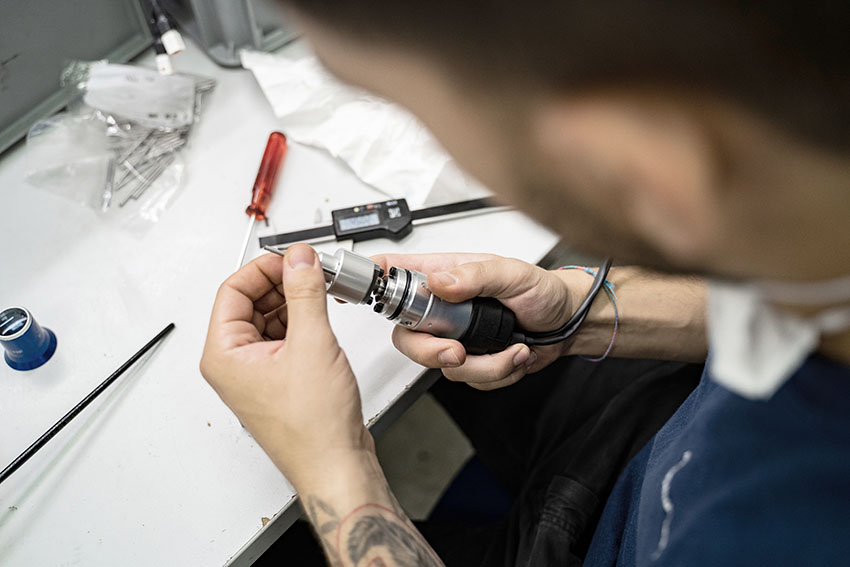
We offer:
- Custom gearboxes and motor gearboxes
- Gear hobbing of straight and helical spur gears – Module 0.2/2.5 – Ø4-120mm
- Milling bevel gears with straight teeth – Module 0.2/1 – Ø4-40mm
- Timing pulley – Pitch 10 max Ø8-120mm
- Milling worms and worm gears – Module 0.2/2.5 – Ø4-50mm. Lmax. 200mm
- Manual and semiautomatic assembly and testing
- Mechanical design with Creo PTC and DTS software for gear design
- Three-dimensional measurements with Zeiss Contura and report gears with check machines up to Ø250mm
E.E: At what stage is the market where you are currently active?
M.G: After 2020, our forecasts for the future were actually quite optimistic. Now that 2021 has gone, we can say that our optimistic view has been confirmed. The recovery after pandemic is continuing very well, and we reached a +20% in sales, in line with the Italian averages from the sector.
However, we can’t affirm to be completely satisfied.
Even if we worked a lot, receiving many orders, we had to make a huge effort to manage and fulfill everything, because of several reasons.
First of all, together with the orders also the extra requests (eg.early deliveries) grew proportionally, creating a situation of constant emergency and urgency that turned into fractioned orders, loss in marginality, loss in time, etc…
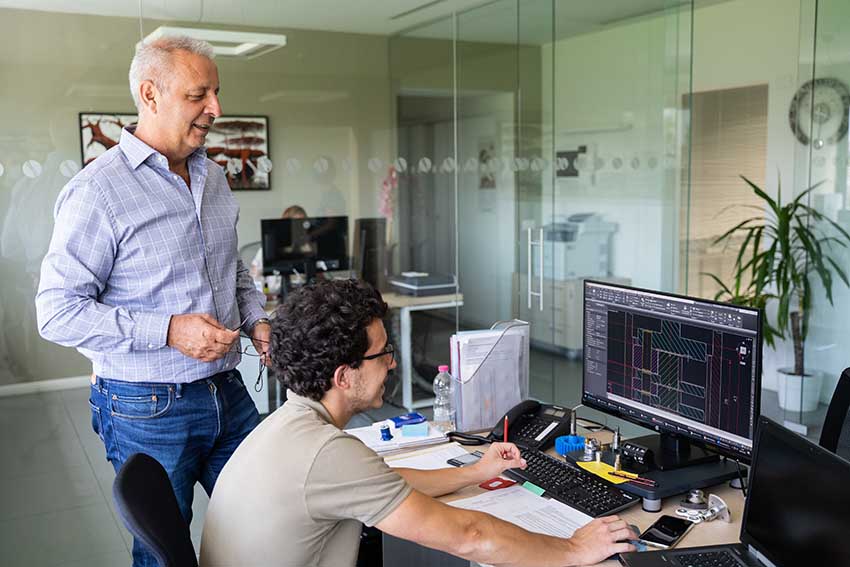
Then, it continues to persist the lack of raw materials necessary for some production batches. The difficulty in finding raw materials can be devastating, especially for the assembled parts. You could have a gear motor ready and assembled, but maybe still not able to deliver it to the customer because of a not available screw.
In conclusion, I would say that the market is recovering surprisingly well from the pandemic lockdown of 2020, but it’s still crucial to overcome the actual issues with raw materials and energy prices.
E.E: What are the most innovative products marketed?
M.G: We have recently worked on a very stimulating project together with the Italian Institute of Technology, the Hannes hand. This prosthetic and robotic hand is controlled by the contraction of the residual muscle by surface sensors that capture the electrical signal coming from the brain. This signal – after being cleaned and amplified – is transmitted to a motor card which then gives the input to the motor for the finger’s movement. The gearmotor we developed is connected to the hand motor, and it controls a series of cables that pass through all the fingers and which allow the hand to move in a precise way, articulated, automatically adapting to the grasped object and with a gripping force up to five times higher compared to other prosthetic hands on the market.
The project also gained multiple tech prizes, and it’s now available on the market at a price even ten times lower compared to other similar prothesis.
And this is the perfect example of a 360° collaboration with a customer: from the idea and the initial study, to the development of the design, the creation of prototypes, and the final industrialization.
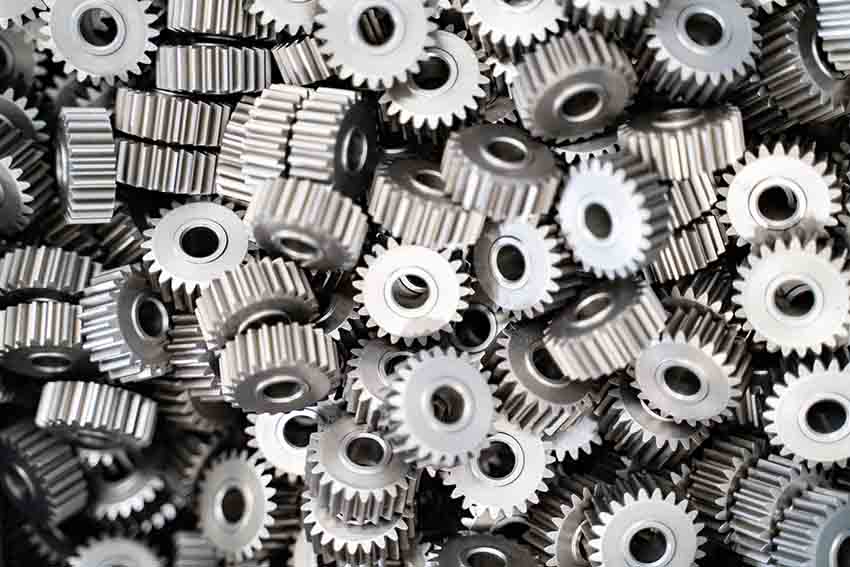
E.E: What can you tell us about market trends and what estimations do you have for 2022?
M.G: Domotics has been our top and most growing market in the recent years, and in 2021 it confirmed its position even more. For next year we are expecting a similar trend, and we see the medical, aerospace and packaging industries that will follow just behind. Within the newest sectors, we definitely see an important growth in the e-mobility market, especially for e-bikes, where we gained different customers in just a couple of years.
In general for 2022, we expect the market to keep growing, following the trend from last year. Unfortunately, the lack of raw materials and the energetic instability make it not possible to predict what will really happen in the coming months, but as already mentioned, it’s crucial for the industry to get over this situation.
On top of it, we’ll keep investing to modernize and increase our production capacity. In 2021, we presented a 2 years investment plan consisting in almost €2M, the biggest in our history, and including 4 CNC for tuning and gear hobbing, a new washing center and a third Modula warehouse.