Peerless Plastics & Coatings is an award winning manufacturer and applicator of enhanced Protective Hard Coatings (including Anti-Microbial, Anti-Fog, Anti-Glare, Anti-Static, Anti-Graffiti, Frost & Formable coatings) for plastic substrates and printed/painted surfaces, designed to protect, upgrade and enhance the longevity of the substrate, based in Thetford, Norfolk, UK. They offer flexible, bespoke, protective hard coating solutions for plastic(s) to all customers the world over, serving a large variety of industries. Offering a complete chain solution, all in-house, from design, research & development, supply, and full production processes. The company prides themselves in the ability to tailor their processes to individual company and market requirements, and have done for over 30 years, proudly adhering to their ISO 9001:2015 and ISO 14001:2015 accreditations.
Peerless Plastics & Coatings continually develop their range of Protective Hard Coatings for plastic substrates which are widely regarded as some of the most high performing and reliable coatings in Europe.
The company aims to promote the message that Protective Hard Coatings offer long term durability and superior surface performance to plastics through improved chemical and abrasion resistance, significantly extending the original substrates useful life, meaning less waste and reducing the carbon footprint of projects, helping to aid sustainability.
Interview with Mark Scott, Marketing Manager & Peter Llewellyn-Stamp, Managing Director at Peerless Plastics & Coatings.
Easy Engineering: What are the main areas of activity of the company?
Mark Scott & Peter Llewellyn-Stamp: Our main activity is applying Protective Hard Coatings to plastic substrates. Our Thetford facility incorporates fully automated coating line technology for materials up to 3050mm x 2050mm as standard (and over-sized sheets on request), with mass volume hard coating of small parts, mouldings & extrusions for many industries & applications, all applied in clean-room conditions. In addition to the Peerless specialist Protective Hard Coatings and finishes, we also supply and distribute a wide range of plastic sheets to our customers all over the world, working in a large variety of industries. These plastic sheets can be used either in conjunction with our Protective Hard Coatings or as a base material. We also provide Injection Moulding, Large Format Digital & Screen-printing capabilities, a high-precision Plastics Machining Department & Spray Painting facilities, meaning that we can have more control over quality, shorter lead times and help to reduce costs associated with having different companies perform the processes that we offer in-house all under one roof.
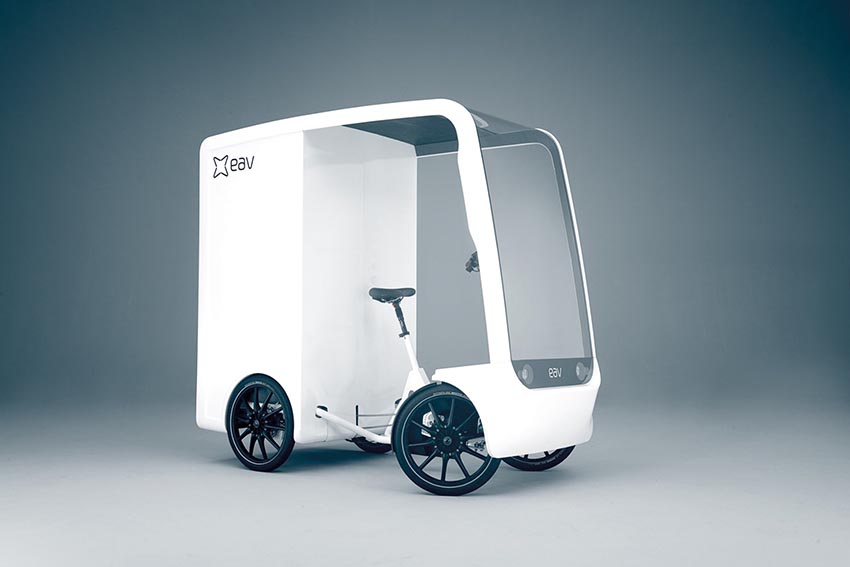
Materials that we coat, supply and work with:
- Polycarbonate
- PMMA – Cast and Extruded
- PETG
- PET
- ABS
- Digitally and Screen-printed surfaces
- Painted surfaces plus many more.
Some of the industries we service:
- Automotive
- Aerospace
- Rail
- Construction and Glazing
- Retail and Point Of Sale
- Electronics
- Highways and Traffic
- Sound and Noise Barriers
- Canopies and Walkways
- Medical and Healthcare
- Polycarbonate and PMMA sheet manufacturers
E.E: What’s the news about new products?
M.S & P.L.S: We have launched our own range of Hard Coated Polycarbonate, under the name PolyGuard™. The pre-coated sheet has been designed to give chemical and abrasion resistance to Polycarbonate and grant anti-graffiti protection, amongst other benefits. Spray coated with a UV-cured, silica-modified coating, PolyGuard™ offers a high quality, sustainable, flat plastic sheet in a wide range of thicknesses and sizes. Whilst nothing is ever truly a ‘scratch resistant plastic’ – PolyGuard™ is the closest you will find in a Polycarbonate (PC). Glass-like in appearance, the material maintains the high impact strength of PC but combines improved weather-ability with chemical and scratch resistance (as well as additional extra benefits) to the original plastic.
We are constantly evolving our Protective Hard Coatings to improve their performance, add additional benefits and create new, bespoke protective hard coatings.
Upcoming product developments include an NIR blocking coating to be incorporated within the PolyGuard™ range.
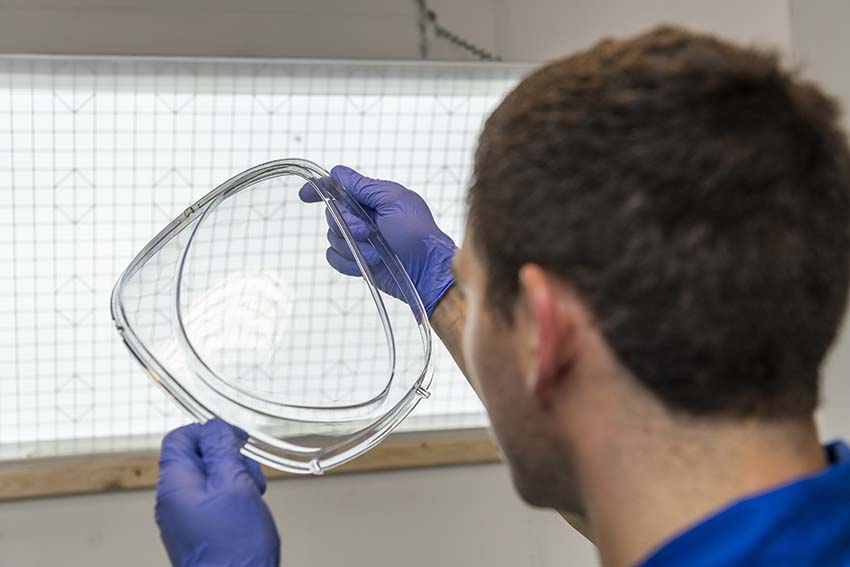
E.E: What are the ranges of products?
M.S & P.L.S: We provide a range of products (to complement our extensive services listed above):
The PeeraGuard™ Range:
- Clear
- Anti-Fog
- Optical
- Anti-Glare
- Anti-Static
- Frost
- Formable
- Exterior
The MicroGuard™ Anti-Microbial Range:
- Clear
- Anti-Glare/Satin
- Anti-Fog
Premium Exterior grade hard coatings:
As well as our range of protective hard coatings, we also offer:
- Conductive Coatings that shield electronic equipment.
E.E: At what stage is the market where you are currently active?
M.S & P.L.S: We are seeing a rise in enquiries from EV manufacturers as they endeavor to decrease weight and therefore increase the range of their vehicles. Our hard-coated plastics sheets offer several options for the automotive/EV market as we have gained ECE R43 Type Approval for automotive glazing options. This accreditation, along with our extensive range of substrates and hard coatings, makes us the ideal partner in the automotive industry for various glazing options, as well as assault screens and partitions, etc. in buses and commercial vehicles.
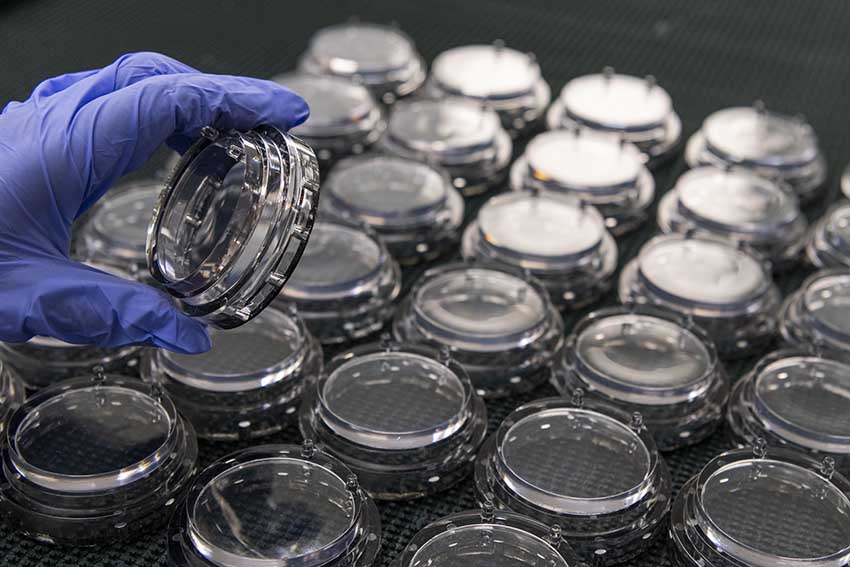
E.E: What can you tell us about market trends?
M.S & P.L.S: Sustainability and efficiency are the constant protagonists in today’s market with more customers being aware of their impact on the environment and the greater social responsibilities involved. As well as lowering our own carbon footprint and making ourselves as agile and sustainable as possible, we are actively trying to promote the fact that protective Hard Coatings do the same to regular, uncoated plastic sheets, due to them lasting longer, as well as offering the additional benefits listed earlier in this interview.
E.E: What are the most innovative products marketed?
M.S & P.L.S: As Covid gripped the globe, Peerless were well placed to offer long term hygienic surface solutions through our existing MicroGuard™ range of protective hard coatings. However, due to specific demand from the public services, in particular the UK Police force, development and test work commenced in mid-2020 to expand the MicroGuard™ coating range to include an Anti-Fog coating which could be heat formed.
With extensive development works in conjunction with project partners, Peerless were able to develop MicroGuard™Anti-Fog, a coating which offers excellent long-term Anti-Fog/Anti-Mist performance together with Anti-Viral properties. This coating has been marketed for medical applications together with the production of a unique public order helmet visor solution which achieved UK Home Office approval.
The development, expansion and marketing of the MicroGuard™ range saw Peerless successfully win the 2021 Plastic Industry Innovation Award.
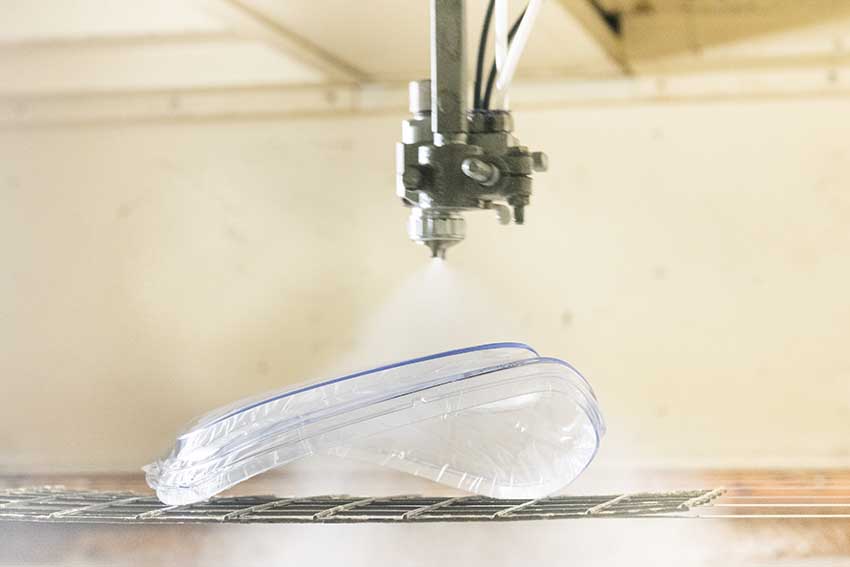
E.E: What estimations do you have for 2023?
M.S & P.L.S: We believe that 2023 will remain challenging, with the cost of production rising and continued disruption in global supply chains.
Peerless will continue to expand it’s unique offering into new markets within Europe and beyond. With our sustainable plastic and single source solution capabilities, we are well placed to be a cost effective, engineering driven, low carbon foot-print, project partner.
We expect to see growth in EV markets, together with sustainability, as many companies seek to achieve Net Zero status.
PEERLESS PLASTICS & COATINGS LTD.
16 – 20 Howlett Way Thetford,
Norfolk, IP24 1HZ
United Kingdom
Tel.: 01842 750 333
Email: sales@peerless-coatings.co.uk
Website: www.peerless-coatings.co.uk