Resino is an expert in reactive inks for flexographic, gravure and inkjet printing. The ink company delivers a wide range of high-quality inks, in particular water-based, solvent-based and UV curing inks, for special requirements.
Resino’s mother plant is in Denmark covering EMEA, and the company has warehousing facilities in USA and Malaysia to cover the areas of respectively North and Central America and Asia Pacific.
Interview with Niels Nielsen, V.P. Commercial Director at Resino.
Easy Engineering: What are the main areas of activity of the company?
Niels Nielsen: We are very engaged in the market of inks exposed to direct food contact. We offer inks that are suitable for direct and in-direct food contact and can be used for informative and/or decorative purposes.
We also deliver printing ink for non-woven diapers and other hygiene products. We offer both solvent-based and water-based 1k and 2k inks. Printing on hygiene materials is a delicate process, where it is necessary to balance physical performance and regulatory demands.
We are proud of our global leading position in inks for meat casings, and we enable our customers to perform high quality fine print decoration on all types of meat casings. We offer 2k water-based and solvent-based systems, plus UV curing inks. Our inks for meat casings have great adhesion, low migration risk as well as boiling and sterilization resistance.
Resino operates in markets with strict regulations and thus, regulatory compliance is key to us. It is especially the inks for products exposed to direct food contact and meat casings that are influenced by high regulatory standards. To assure credibility of our information, we work with third party institutes which validate the data to always ensure that regulatory standards are met.
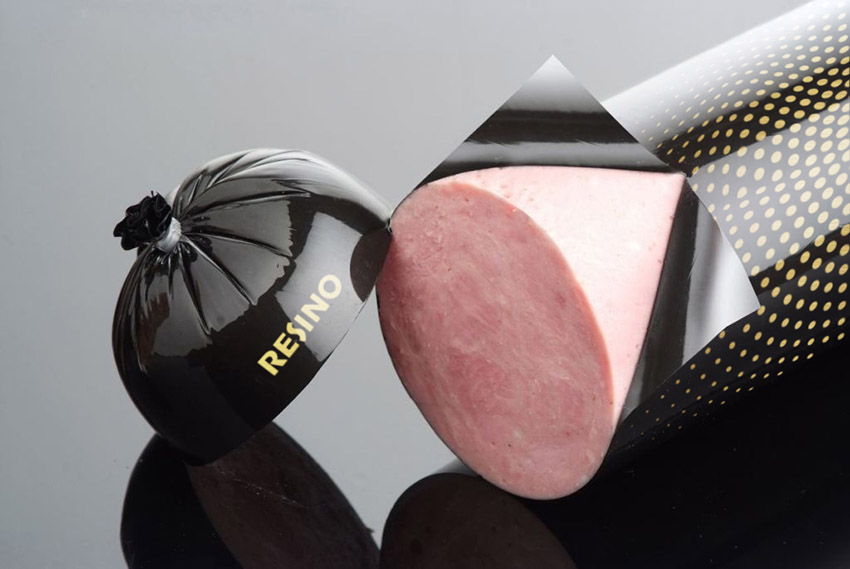
E.E: What’s the news about new products?
N.N: A new legislation has come into force within the EU, which bans the use of plastic for disposable tableware (European Union’s Single-Use Plastics Directive). Resino has worked in close cooperation with customers to find a solution and we have developed varnishes, based on acrylic binders as well as natural materials, which can replace the plastic coating. The varnishes of natural materials present an important milestone within Resino as they are also compostable.
With the increased focus on reducing plastic consumption, there is also a great need in the market to reduce or eliminate plastic-coated food packaging, and many companies desire to switch from plastic to paper and board. However, plastic has protective functions, which does not appear in paper and board packaging. Therefore, we support our customers in finding an alternative barrier to take on this protective function.
E.E: What are the ranges of products?
N.N: High quality inks and coatings that are always regulatory compliant.
We deliver water-based, solvent-based of UV curing ink systems for complex print requirements.
E.E: At what stage is the market where you are currently active?
N.N: Ink technology is heading towards inkjet printing. This development has environmental benefits which will be further explained in the below question.
E.E: What can you tell us about market trends?
N.N: Sustainability and the environment are issues that we must integrate this in our product development which includes focusing on water-based inks. Therefore, we are currently working on replacing 2k ink systems by 1k water-based ink systems both for flexographic printing and inkjet printing.
In relation to the environmental issues, ink technology is also heading towards inkjet printing and thus, this is a focus point of our product development. Inkjet printing results in low circulation which contributes to less waste and makes it a more sustainable solution.
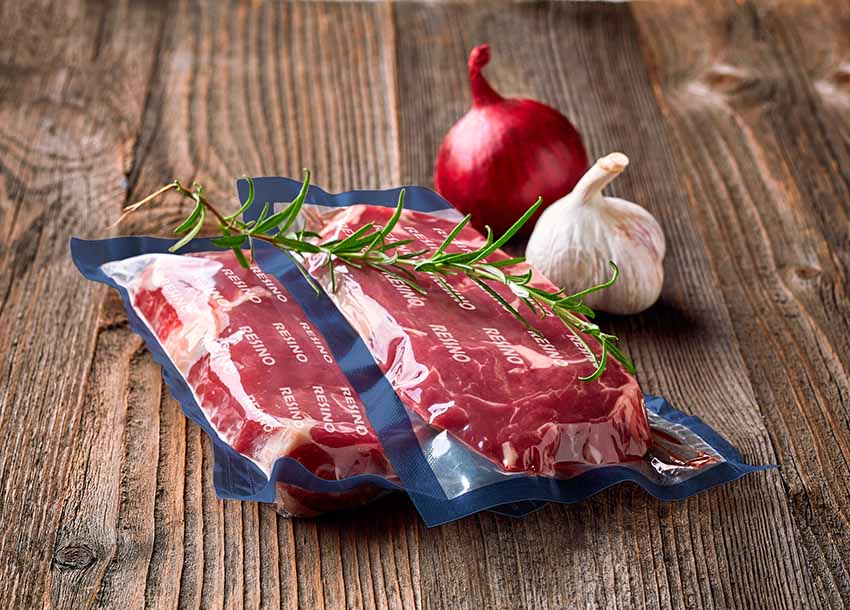
E.E: What are the most innovative products marketed?
N.N: We use a technology for our UV inks that differs from traditional UV curing inks. RESUCAT® inks are based on cationic UV curing technology. The advantages for cationic UV curing are continued curing after exposure to UV light, excellent adhesion on difficult substrates, low shrinkage, high flexibility and high heat & chemical resistances.
We use the same specialized technologies to develop inkjet variants of UV and water-based inks that fit into these sophisticated markets. This allows us to offer inks for inkjet printing to provide the opportunity for personalized printing and small circulation designs.
The varnishes developed in relation to the EU Directive are also highly innovative since they support the conversion from plastic to paper and board products.
As mentioned, the varnishes of natural materials are compostable which make them very innovative. In this way, you avoid the issues regarding waste that is not biodegradable.
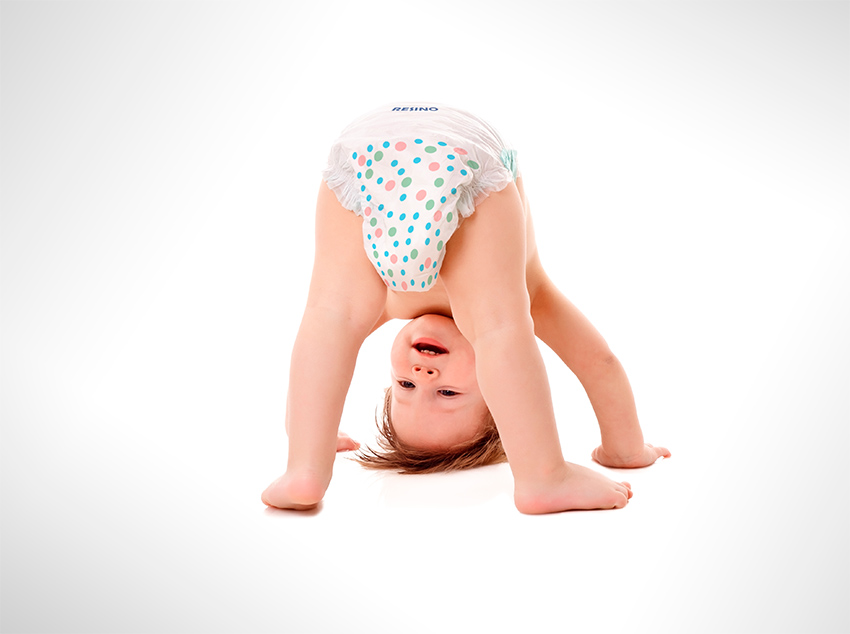
E.E: What estimations do you have for 2022?
N.N: Food safety and regulatory compliances are forever tightening, and we expect this to continue. It is important for us to stay at the forefront of this and these issues will remain a high priority in our development work.
Sustainability is also an issue we must continuously consider in our product developments, both in the form of renewable resources and biodegradability. Furthermore, Resino is active in a “Circular monoplast” project to improve recyclability of plastics.