With over 40 years of designing and producing reflow solder systems in Santa Barbara, California, Sikama International’s reflow solder systems have been providing reliable and trusted performance to electronics manufacturers worldwide. Their unique thermal technologies, close customer support, and unmatched quality offer significant benefits to customers.
Sikama is proud to design, develop and manufacture products at their headquarters, which allows them rapid innovation cycles, and offers hands-on product customization and on-site customer evaluation and product testing. The company continues to grow and develop new technologies to keep pace with the ever-evolving electronics industry.
Interview with Jeffrey Blair, Director Of Sales And Business Development at Sikama International.
Easy Engineering: Which are the most innovative products / services and what special features do they have?
Jeffrey Blair: We’re very excited to announce the availability of our EA UP1200, the first of its kind truly fluxless reflow oven utilizing electron attachment technology developed in conjunction with AirProducts. This product provides significant benefits by offering safe and highly effective oxide removal without the use of formic acid or flux. We believe this product will be transformational to the advanced packaging industry.
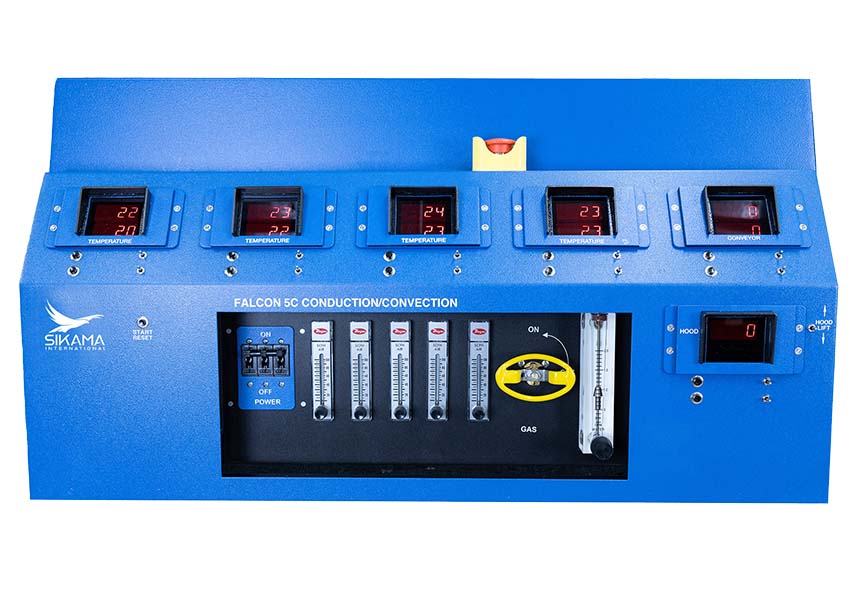
E.E: How important are these features for the users in their work?
J.B: Our products stand out by offering conductive plus convective heating which allows extremely efficient thermal transport, high throughput, and an industry-leading small footprint. Our transport systems provide low vibration and friction-free part handling, as well as high versatility to meet any profile and part geometry.
E.E: How important is innovation in your field?
J.B: The electronics industry is advancing quickly, so keeping pace with innovative solutions is paramount for success. Sikama continues to meet the needs of our customers with updates to existing equipment as well as developing new machines to meet our customer’s needs. The fluxless EA UP1200 oven is a great example of this.
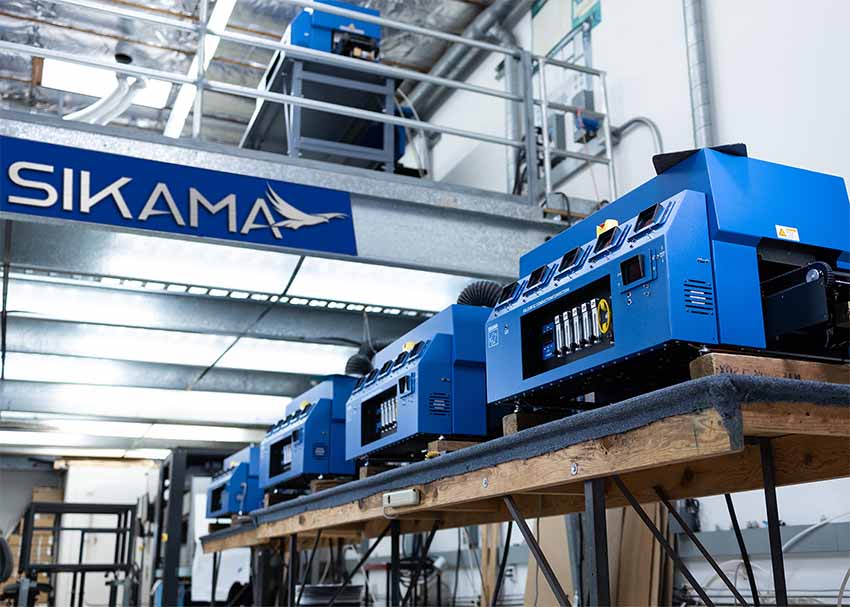
E.E: How do your products / solutions impact cost effectiveness for the users?
J.B: The cost per square foot of manufacturing space is at a premium, as is the cost of energy and gas. With our small footprint and efficiency metrics, we provide extremely cost-effective solutions for our customers. In addition, our equipment is built to last, with most of our equipment running successfully for decades.
E.E: What kind of work do users who use these products / services do?
J.B: We support a very broad range of customers who are manufacturing electronics equipment. From upstream wafer manufacturing to downstream component assembly, and from fully automated production lines to small R&D facilities, we can offer a solution.

E.E: How do your products increase profitability for users?
Our cost of ownership models consistently lead the market due to low energy and gas utilization, high throughput, and minimal maintenance due to the product quality and service life of the product. We also offer close customer support, with engineers only a phone call or email away, and on-site training and services available to all our customers.
E.E: How do your products / services differ from other types on the market?
J.B: Sikama is the only reflow oven manufacturer that utilizes both conductive and convective heating methods, something that’s not available in a belt furnace, and offers industry-leading thermal transport. This significantly increases our performance advantage and energy/gas usage. This also allows very small footprints since components are allowed to “dwell” in each zone for a specified period, dramatically decreasing floor space requirements.
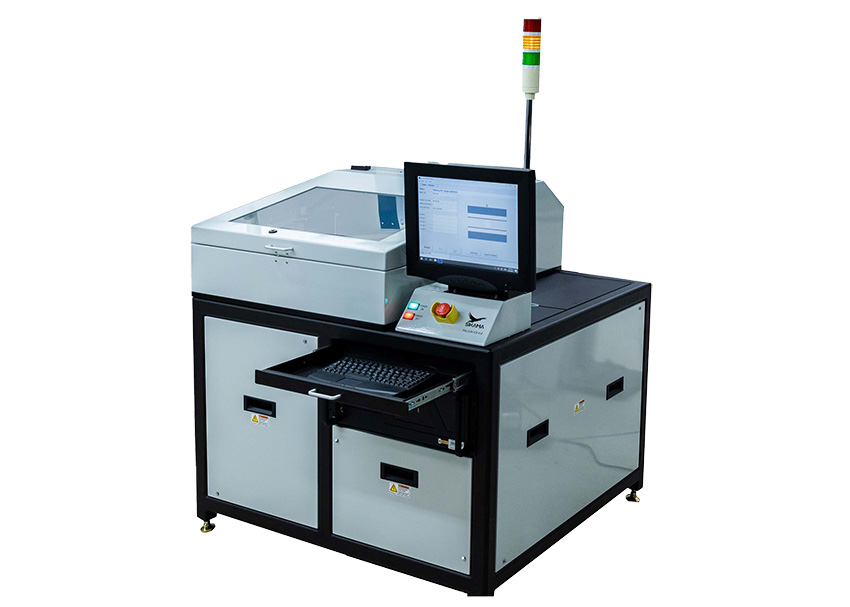
E.E: How do your products help solve users’ problems?
J.B: Customers who purchase a reflow solder system are looking for something that is built to last, requires minimal overhead, offers high performance and versatility, and ensures repeatable results. Sikama checks all these boxes with a track record of 40 years to prove it.
E.E: What products / solutions are you going to launch in the future?
J.B: Sikama continues to build out its product roadmap which will include the additional ability to better handle JEDEC trays, more fluxless reflow options utilizing Electron Attachment technology developed in conjunction with AirProducts, and even more options for customer support with increased in-field support. We are also partnering with automation companies to offer turn-key solutions.