Rubber represents the biggest single influence on the performance and longevity of a conveyor belt. It also represents some 70% of the mass and up to 50% or more of the cost of making a belt. Consequently, in these times of ever-increasing price competition, led and dominated by manufacturers in Southeast Asia, primarily China, rubber is also the biggest opportunity for savings. Cost-cutting practices include the use of unregulated, low-grade raw materials, the use of bulking agents such as chalk, increasingly larger proportions of recycled scrap rubber of highly questionable origin and the substitution of essential polymers such as carbon black with low-grade versions created by burning scrap vehicle tyres. Another method is reduced quantities and often the total omission of key ingredients such as the antioxidants that all good quality rubber needs to resist the premature degradation caused by exposure to ozone and ultraviolet light.
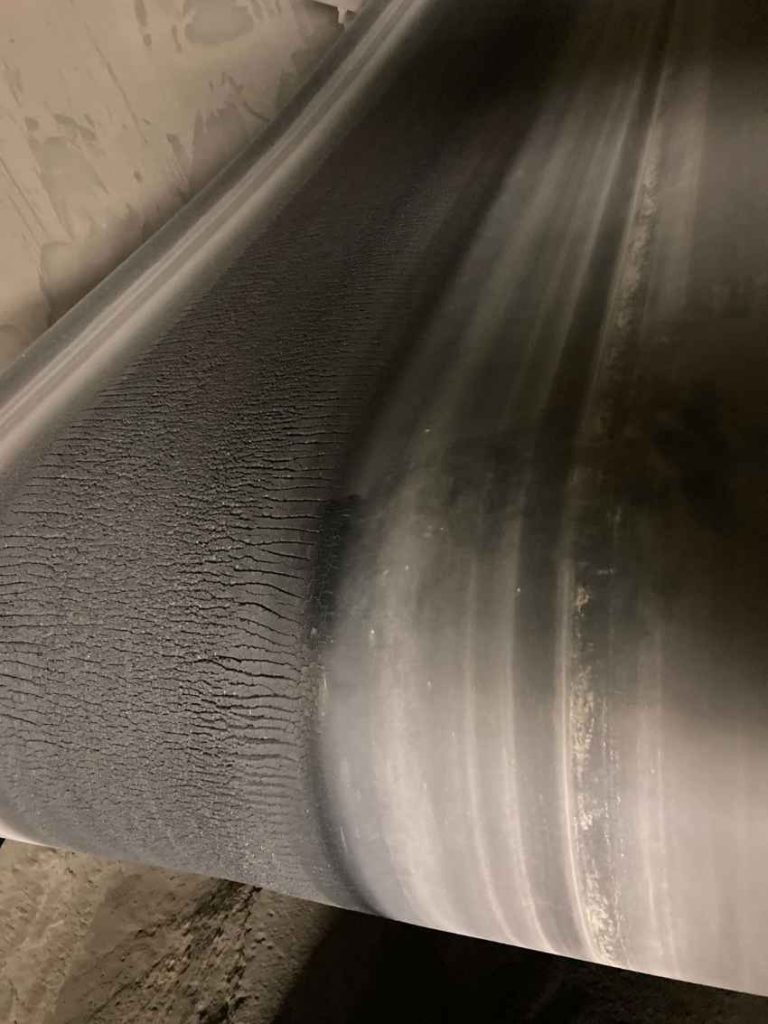
Omitting key ingredients to reduce costs causes life-limiting damage to the rubber
Such practices allow unscrupulous manufacturers to massively undercut the prices of the few remaining manufacturers at the quality end of the market, such as Fenner Dunlop in The Netherlands. Despite such pressures, Fenner not only refuses to change direction, they are more committed than ever to further widen the quality and value gap.
A complex process
Because of its adaptability, most conveyor belt rubber is synthetic or only contains a relatively small amount of natural rubber. The creation of rubber compounds (rubber compounding) is the process where a range of ‘specific task’ chemicals, reinforcements, antioxidants and anti-degradants are mixed with rubber polymers according to the specific recipe for the required rubber type.. The most common polymers used in conveyor belts are Styrene- Butadiene rubber (SBR) and Nitrile rubber (NBR).
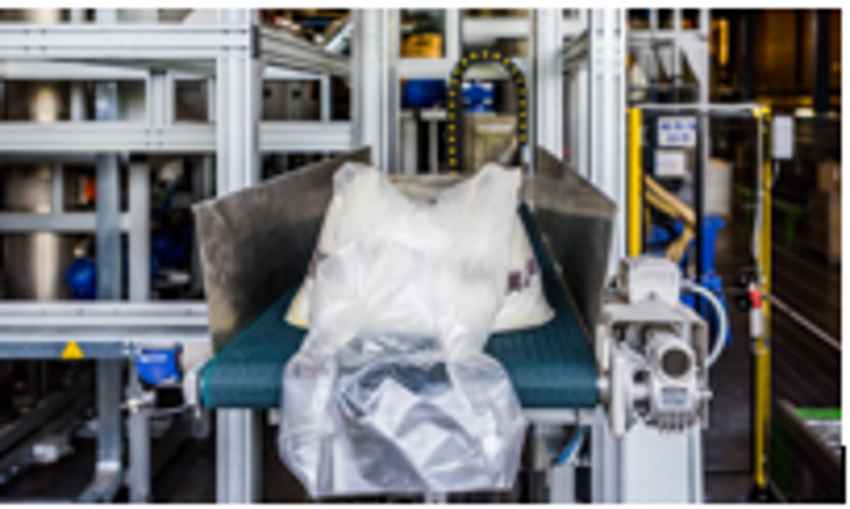
Precise measurements of each ingredient in polymer-based bags are mixed
Homemade
Fenner Dunlop are fiercely proud of the fact that they are the only remaining European belt manufacturer that continues to make all of its own products using its own production facilities. This includes the rubber, which even fewer of their competitors now make themselves due to a growing trend to outsource the manufacturing of their rubber compounds, mostly to Southeast Asia, rather than produce them in-house.
The advantage of outsourcing is that rubber compound manufacturers minimize production costs by mass-producing rubber compounds in extremely large quantities. The downsides, however, outweigh the advantages Firstly, outsourcing makes it almost impossible to apply the quality control disciplines needed to ensure the consistency of properties between batches of rubber produced at different times. Another downside is that some compounds have a ‘best before’ shelf life, so they need to be vulcanized before some important characteristics start to diminish.
Safe to handle, safe for the environment
Fenner Dunlop are certainly committed to their policy of making everything themselves. So much so that they have recently invested some €2.4 million in new machinery in their mixing department. Installation is complete and has entered the testing phase. They have also purchased an additional mill that will be installed at a later stage. The primary reasons why such investment was needed revolves around three key factors – Quality, safety and the environment. “Firstly, they needed greater control over the processing of the more difficult materials that they are now having to use. This is a result of the need to find alternatives to materials that they can no longer source from previous suppliers, for example due to the Russia – Ukraine conflict. It is, of course, essential that these alternatives have the same or even higher quality properties than we have used before”.
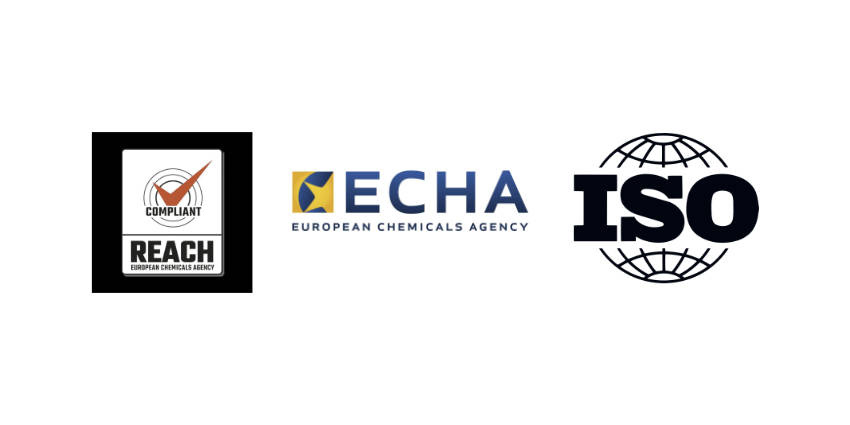
Also, a result of compliance with REACH (Registration, Evaluation and Authorisation of Chemical substances) regulation EC 1907/2006 and EU Regulation No. 2019/1021 concerning the use of persistent organic pollutants (POP’s), they need to find alternative processing solutions for the substitute chemicals that replace those that become banned or have usage limitations placed upon them. Last but not least, there is the highly important question of safety. New ISO standards relating to operational safety of machinery are being introduced and although currently still in the draft stage, when they are implemented, their new mixing machines will instantly be compliant.
Conclusion
There can be no argument that the quality of the rubber has the biggest part to play in terms of performance, longevity and human and environmental safety. At the same time, it provides the greatest temptation for manufacturers to sacrifice those qualities in order to create as big a price advantage as possible. Fenner Dunlop clearly has no intention of making such sacrifices, even in the face of such fierce competition from Asia. By surviving the onslaught, they are at least providing the end-user market with a choice. Long may that continue.