Maxphotonics is one of the first batch fiber laser manufacturers and national high-tech enterprises that have independent intellectual property rights and vertical integration in 2 core technologies of fiber lasers and optical components in China, and has now developed into an internationally renowned laser manufacturer integrating R&D, production and sales of fiber lasers and core optical components.
Interview with Markus Geck, Sales Manager at Maxphotonics GmbH.
What are the most common cost-related challenges your customers face, and how do your products/solutions help them cut expenses?
Markus Geck: One of the main challenges our customers face is balancing high-quality production with cost-efficiency, especially in industries with rising material and energy costs. Our fiber laser solutions, such as the CW (Continuous Wave) and pulsed lasers, are designed to reduce energy consumption, minimize rework due to precision issues, and integrate easily into automated environments. This translates into lower operational costs, higher process stability, and fewer production downtimes.
Can you share a specific example of how your products/solutions have improved efficiency for a client?
M.G: In the battery manufacturing industry, our collaboration with one of China’s leading EV battery producers led to the integration of our annular beam laser solution. This technology minimizes spatter, pores, and hot cracking by independently controlling the inner and outer laser beams – one for preheating, the other for welding. It has increased process stability and raised the production yield to over 99%.
Additionally, our film laser cleaning equipment replaced a previously manual PET film removal step, reducing processing time from 1–2 minutes to just 10 seconds – boosting efficiency by over 90% while lowering material waste and eliminating the need for chemical solvents.
How does your technology minimize waste and optimize resource usage?
M.G: Maxphotonics lasers offer high beam quality and precision, which means material is processed with minimal heat-affected zones. This reduces deformation, scrap rates, and the need for post-processing. Our laser cleaning systems also eliminate the use of chemical solvents, contributing to cleaner and more sustainable production processes. By cutting down waste, our customers save not only on materials but also on disposal and environmental compliance costs.
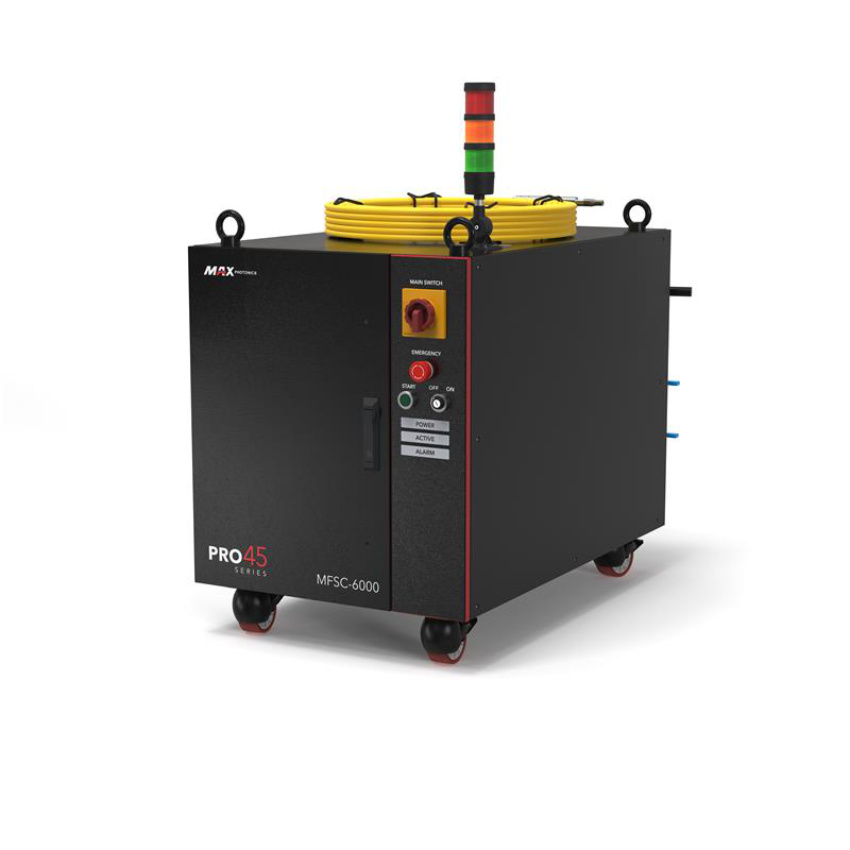
What key features of your products/solutions contribute the most to cost savings for businesses?
M.G: High wall-plug efficiency: Maxphotonics fiber lasers reach WPE levels of up to 48%, converting nearly half of the electrical input directly into usable laser output—dramatically reducing energy costs.
Stable, low-maintenance design: Thanks to sealed optics and air-cooled systems, our lasers require less frequent maintenance and are highly resistant to environmental contamination, minimizing downtime and service costs.
Application-optimized laser configurations: Tailored beam shaping and power control, such as in our annular beam solution, reduce defects and rework—improving yield and reducing scrap by over 99% in real-world applications.
Compact, modular integration: Our systems are designed for easy integration into existing production lines. Smaller footprints reduce infrastructure and space costs, while plug-and-play functionality speeds up deployment.
Are there any hidden or overlooked costs that your products/solutions help eliminate?
M.G: Yes. Poor-quality welds can lead to costly rework, scrap, and warranty claims — often underestimated in total production costs. Our high-stability lasers, such as those with annular beam technology, help minimize these risks by reducing spatter, porosity, and cracking. In addition, our systems are designed for seamless integration into automated production lines via bus communication, cutting down on manual handling and related labor costs. Planned AI-supported process monitoring will further help avoid downtime and material waste by enabling real-time adjustments.
How do you ensure that your products/solutions provide long-term value?
M.G: All Maxphotonics products are developed with durability and long-term operational stability in mind. We use high-quality components, offer long service life, and support customers with a global service network and continuous software updates. Through R&D and field feedback, we also adapt and improve our systems to meet evolving industry standards and customer needs. Additionally, to further ensure long-term value, our products feature up to 20% power redundancy and PL-D technology. Our highly automated production processes and the traceability of test and quality datasets guarantee consistent quality and reliability.
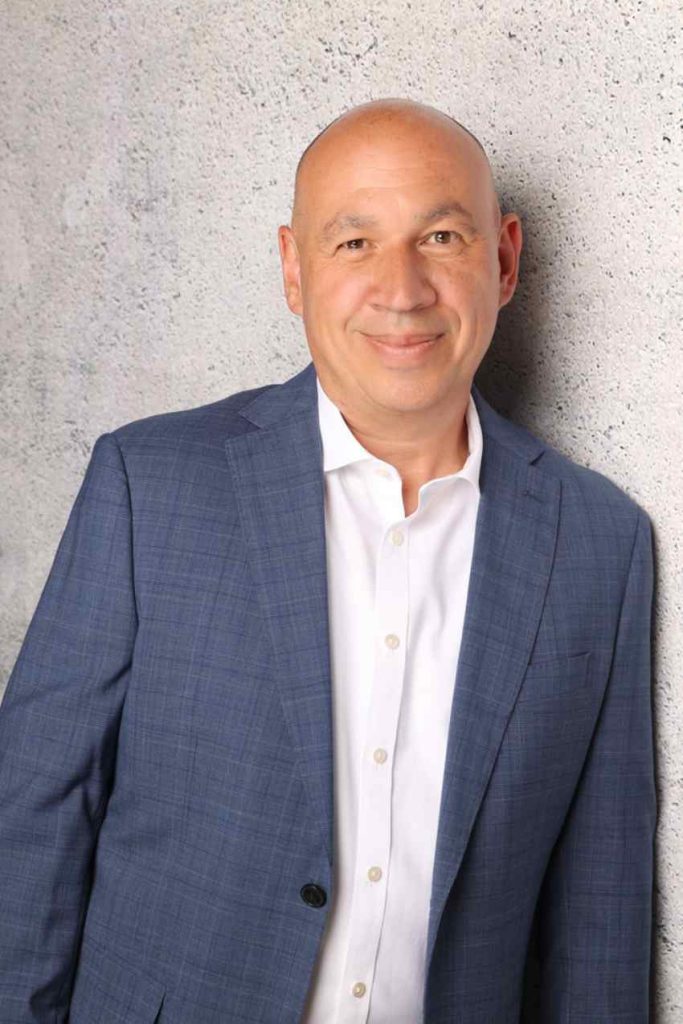
What role does automation play in helping businesses reduce expenses when using your products/solutions?
M.G: Automation plays a crucial role in maximizing the cost-efficiency of Maxphotonics laser solutions. Our systems are designed for seamless integration into robotic cells and automated production lines, supported by standardized bus communication and versatile control interfaces.
As already mentioned, in our collaboration with a leading Chinese battery manufacturer, automated laser cleaning systems replaced manual film removal processes, reducing processing time from 1–2 minutes to just 10 seconds – a 90% increase in efficiency. Across all applications, automation minimizes human error, reduces labor costs, and increases consistency. Our R&D teams are now working on AI-powered monitoring and real-time parameter correction to further reduce downtime, material waste, and quality-related rework.
How do your products/solutions compare with competitors in terms of cost-effectiveness and return on investment (ROI)?
M.G: Our fiber laser sources offer a compelling balance of cost-effectiveness and return on investment (ROI) compared to those of major competitors.
Long-Term Operational Savings: Our products are engineered for efficiency and durability, reducing downtime, consumable use, and the total cost of ownership.
Tailored Support Leads to Reduced Risk: Our proactive customer support ensures quicker integration and fewer production disruptions, which directly impacts ROI.
What advice would you give to businesses looking to maximize efficiency while keeping operational costs low?
M.G: Start by evaluating the full process chain and identifying steps where precision, repeatability, and cycle time matter most. Invest in technology that not only solves today’s challenges but scales with your production needs. Consider automation readiness, energy efficiency, and service support. Partnering with a solution provider like Maxphotonics ensures you get more than a product – you get a path to sustainable productivity.