For over 50 years, Ness has been planning process heat systems for use on all continents in Remshalden near Stuttgart in Germany. Founded in 1964 by Eduard Ness as an engineering company for heat process technology, the company has developed into a well-known complete provider of thermal engineering equipment for many different applications. Ness is among the first to promote heat transfer technology for industrial heat processes.
Can you describe your company’s approach to driving innovation in product development?
At NESS Wärmetechnik GmbH, our approach to innovation is rooted in a deep understanding of our customers’ needs and a constant drive to improve efficiency, safety, and sustainability. We combine decades of experience with cutting-edge technology to develop solutions that not only address current challenges but also anticipate future market demands. Our team continuously explores new methods, integrates the latest technological advancements, and optimizes our processes to deliver high-quality products.
What recent products or solutions have you introduced, and how are they shaping the industry?
Our latest innovation, the NESS Nitrogen Generator NG2000, is a prime example of our forward-thinking approach. This advanced nitrogen generator uses membrane technology to efficiently separate nitrogen from air, achieving a purity level of up to 99.5%. The system provides a continuous and fully automated nitrogen supply, eliminating the need for labor-intensive and costly cylinder replacements. This significantly reduces operating costs and enhances safety for our customers.
What technologies or trends are influencing your latest innovations, and how do they benefit your customers?
Our NG2000 leverages membrane technology for efficient gas separation, which is both energy-efficient and environmentally friendly. The growing trend towards automation and real-time monitoring also plays a key role in our innovations. The NG2000 is equipped with a continuous self-diagnosis system that ensures timely and reliable fault detection, minimizes downtime, and boosts productivity.
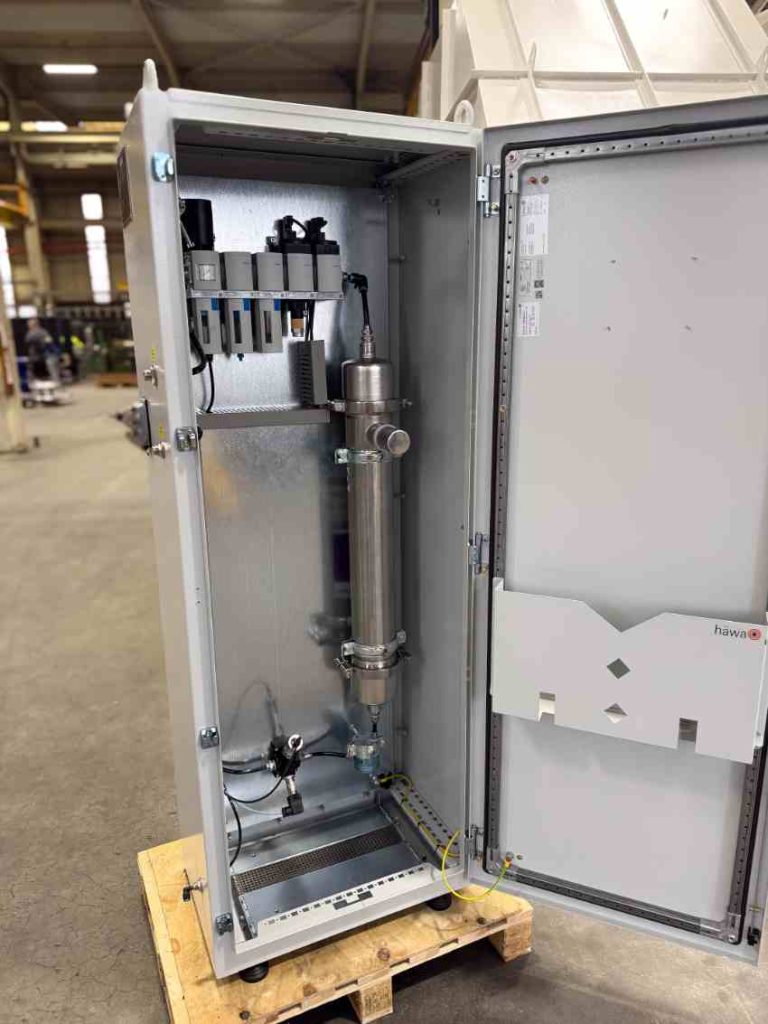
How do you ensure your innovations meet both current market needs and long-term industry evolution?
We maintain constant dialogue with our customers to gain a clear understanding of their challenges and requirements. At NESS, we believe innovation must be both purpose-driven and future-proof. We achieve this through regular market analysis, investment in research and development, and a collaborative approach in which feedback loops guide our product improvements. With modular designs and adaptable technologies—such as the NG2000’s ability to integrate into existing systems—we ensure our solutions remain relevant as the industry evolves.
What challenges did you face while developing your latest products, and how did you overcome them?
One of the biggest challenges was ensuring the high nitrogen purity level of up to 99.5% while maintaining cost-efficiency and reliability. A particularly difficult aspect was finding a precise residual oxygen sensor that not only measures with extreme accuracy but is also durable and resistant to material fatigue. Through targeted testing, continuous improvements, and selecting the right measurement technology, we were able to successfully overcome this hurdle.
How do your latest products differentiate you from competitors in the market?
The NESS Nitrogen Generator NG2000 stands out through its cost-saving efficiency, minimal maintenance requirements, and fully automated operation. Unlike conventional nitrogen supply methods that rely on external gas cylinders, the NG2000 offers seamless, continuous nitrogen generation—dramatically reducing logistical and operational costs.
Can you share any feedback or success stories from customers who have adopted your new innovations?
One of our customers experienced a sudden breakdown in their nitrogen supply, which was previously managed by two separate generators. With our NG2000, we were able to step in quickly—and since then, the required nitrogen has been reliably generated by just one device.
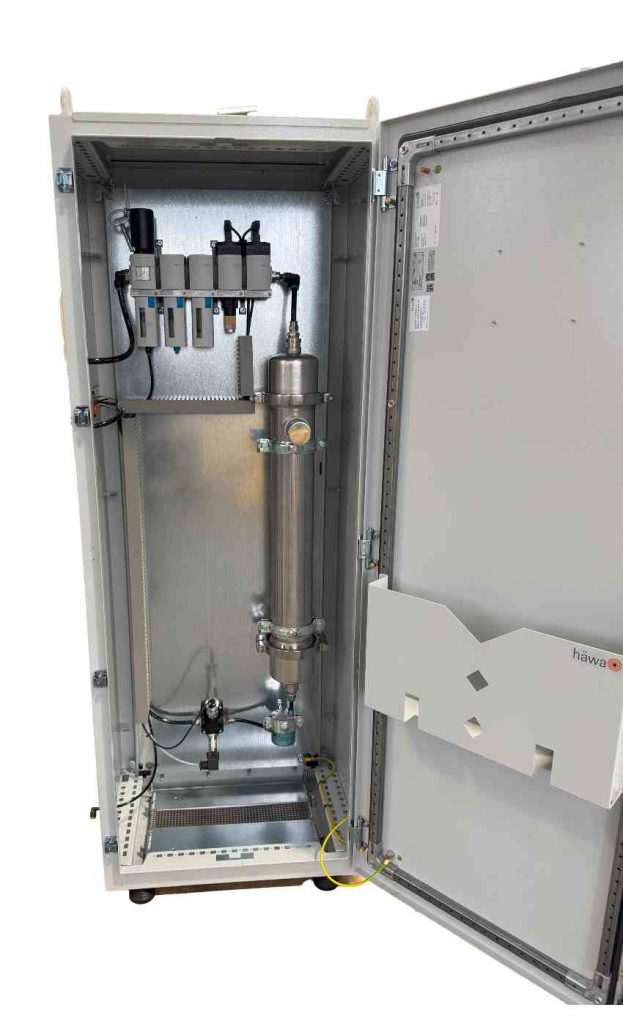
How is sustainability integrated into your product development strategy?
We develop our products closely aligned with the market and tailored to the needs of our customers. Meeting technical requirements is our top priority. However, the way we achieve this always includes careful material selection and consideration of energy efficiency during operation. For every product, we strive to minimize the environmental footprint without compromising technical specifications. In the case of the NG2000, the primary focus was on reliability and independence from external nitrogen suppliers. Additionally, producing nitrogen on-site eliminates the need for transporting heavy gas cylinders over long distances, contributing to a more sustainable operation.
What emerging trends or technologies do you think will drive the next wave of innovation in your industry?
The future of our industry will be increasingly shaped by automation, intelligent monitoring systems, and sustainability. At NESS, we are particularly excited about further developing the potential of our automated diagnostic systems and advancing our membrane technologies to offer even more efficient, reliable, and eco-friendly solutions.